.035 4043 spool
180 Lincoln mig
1/8" aluminum flat bar stock
I've cut 2x2 coupons to assemble in a cube for practice. Mostly my problem is that it is coming out slowly globular. The recommended settings (which I never go by) aren't even close, but since I'm trying a new trick I started there. I was getting balls of ally. Played with it until I got what looks slightly cold, but forms a bead. It's cold because it is still dropping in large globular. I've tried many settings, but my best effort is below. I know when it is too hot, it starts melting through. I've been able to turn the wire speed up to stop the globular and it starts sounding like a machine gun, but the wire speed is too high at that point.
I bought a second argon tank (1st is for my tig) just to do ally, so I intend to get it right. I wasn't doing any better with the spool gun so I went to the mig and tossed the gun. It works just as well.
General welding questions that dont fit in TIG, MIG, Stick, or Certification etc.
from what i understand of it, your running way to cold.
crank it up. you need to be in spray transfer.
odds are you where melting through because your travel speed was to slow.
so crank the heat up and crank the travel speed up.
your doing well for thin diameter 4043 to run through a mig gun.
your machine is probably bare minimum or even undersized especially for that thickness material.
crank it up. you need to be in spray transfer.
odds are you where melting through because your travel speed was to slow.
so crank the heat up and crank the travel speed up.
your doing well for thin diameter 4043 to run through a mig gun.
your machine is probably bare minimum or even undersized especially for that thickness material.
tweak it until it breaks
- MinnesotaDave
-
Weldmonger
-
Posts:
-
Joined:Sun Oct 27, 2013 10:57 pm
-
Location:Big Lake/Monticello MN, U.S.A.
If in globular your wire speed is already too fast for the voltage.
You need more voltage or less wire speed to get to spray transfer.
Aluminum is not short circuit welding.
Here is a very short video to show what it sounds like in spray.
https://m.youtube.com/watch?v=IHkbh0oKv_g
You need more voltage or less wire speed to get to spray transfer.
Aluminum is not short circuit welding.
Here is a very short video to show what it sounds like in spray.
https://m.youtube.com/watch?v=IHkbh0oKv_g
Dave J.
Beware of false knowledge; it is more dangerous than ignorance. ~George Bernard Shaw~
Syncro 350
Invertec v250-s
Thermal Arc 161 and 300
MM210
Dialarc
Tried being normal once, didn't take....I think it was a Tuesday.
Beware of false knowledge; it is more dangerous than ignorance. ~George Bernard Shaw~
Syncro 350
Invertec v250-s
Thermal Arc 161 and 300
MM210
Dialarc
Tried being normal once, didn't take....I think it was a Tuesday.
What's weird is lincoln says use setting A for voltage. This machine is a lot hotter than you think, but it isn't THAT hot. I've been using B and trying to find a nice medium. If i go above B or go too fast on wire speed it makes a crater down the bead no matter how fast i move. Even halfway up on voltage (C) it melts through instantly. I think people underestimate the 180 because the 125, 140, etc are weak 110s. I bought this machine 2x because i couldn't find anything as hot out there. I tried esab, miller, and several others. After wasting thousands trying to find the right 220 mig i came back to the 180 and bought a brand new one 2 weeks ago.
The issue I'm having now is that i am either dropping globs or blowing the bead out down the middle.
I've been able to land a few beads, seen below with my cold starts as i was padding.
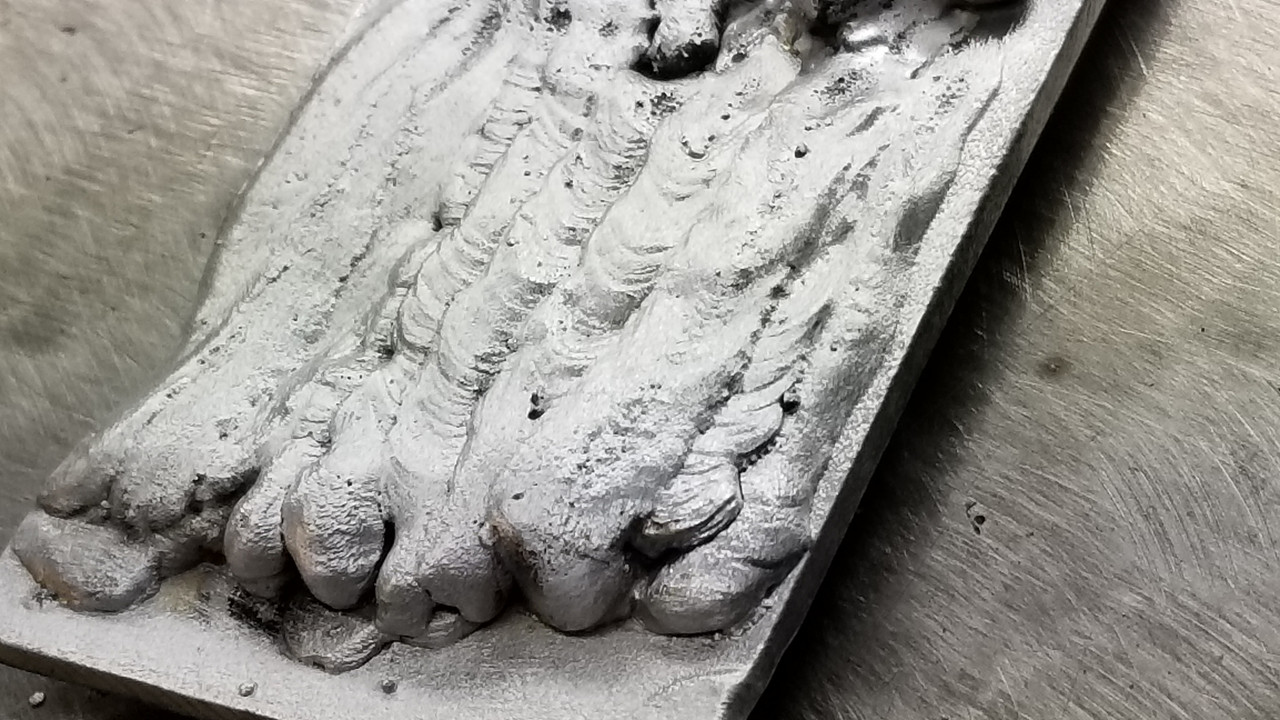
This is hugely annoying to me knowing what i can do with steel. Totally different beast.
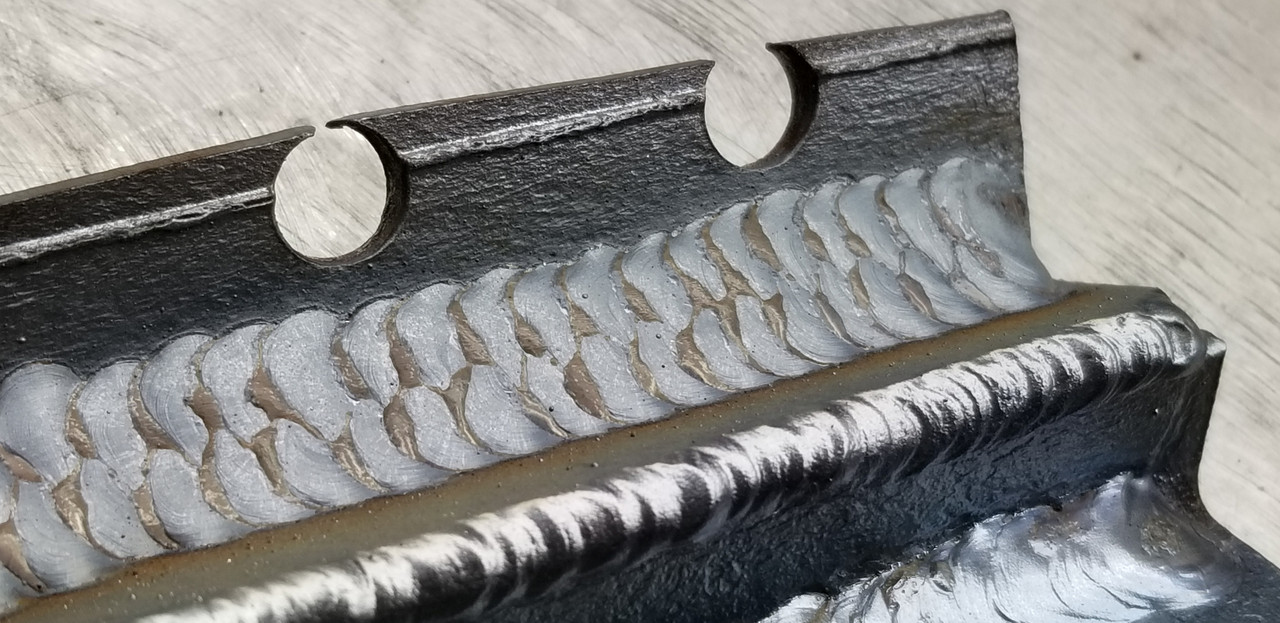
So i cut those bead pads above and as it turns out, it's solid. It won't win any instagram awards, but it did fuse. (i welded on both sides of the ally at different times)

The issue I'm having now is that i am either dropping globs or blowing the bead out down the middle.
I've been able to land a few beads, seen below with my cold starts as i was padding.
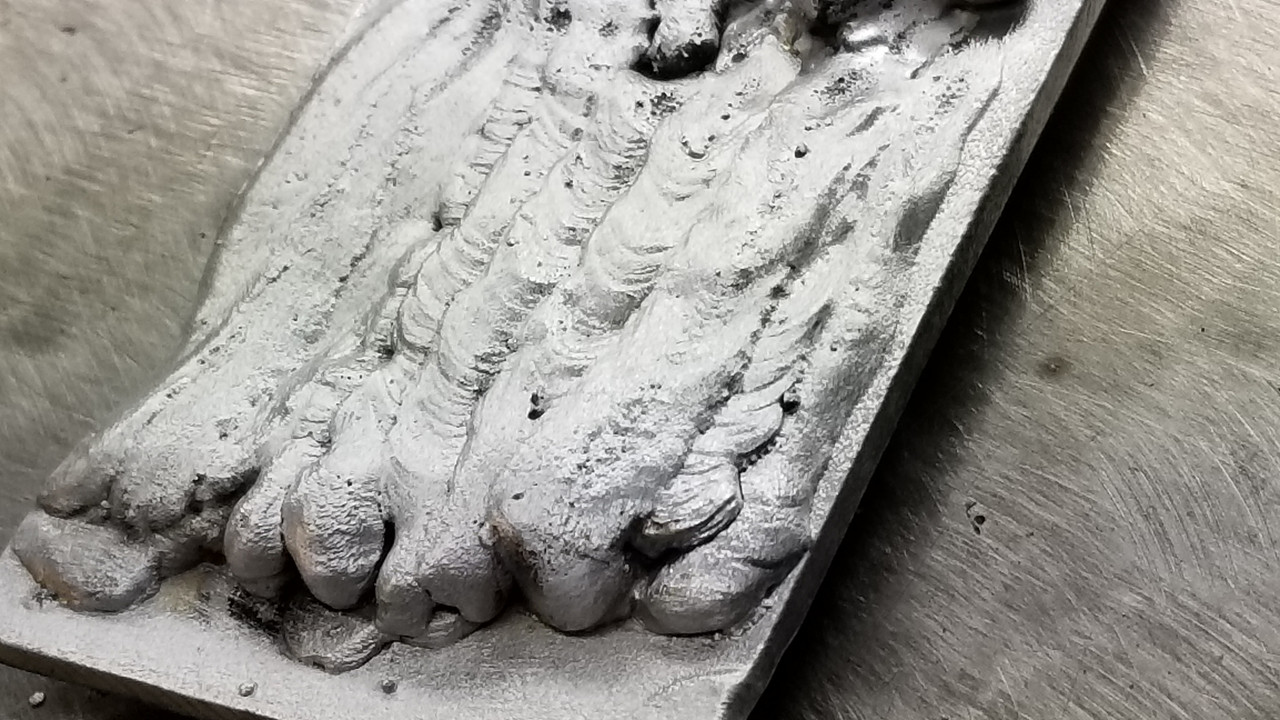
This is hugely annoying to me knowing what i can do with steel. Totally different beast.
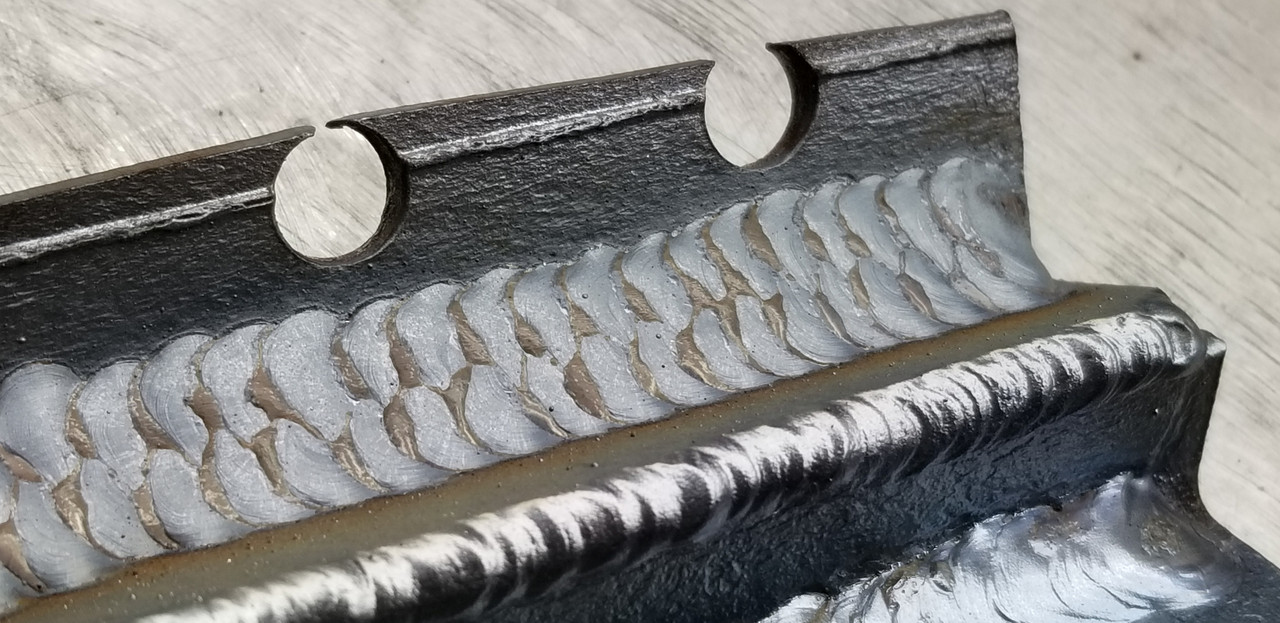
So i cut those bead pads above and as it turns out, it's solid. It won't win any instagram awards, but it did fuse. (i welded on both sides of the ally at different times)

1957 Lincoln Idealarc 300, Miller 211 v1 mig, Lincoln 3350, CK Worldwide CK17FV, 9FV
in my very limited experience with spray transfer, when you wind it up and you get that machine gun noise, then your still to low.One1 wrote: I've been able to turn the wire speed up to stop the globular and it starts sounding like a machine gun, but the wire speed is too high at that point.
you need to go up through that noise. you will notice it straight away when you hit spray transfer because it goes quiet.
use a longer stick out than steel.
tweak it until it breaks
Never said this with a straight face, but it ain't me, it's the material. Since I'm globbing i have to turn up the wire speed, but when I do I burn too hot and leave a ridge. Only choice is to turn the voltage down and I can't. I'm on A, first setting. So to prove it i put the two pieces i cut back together since it had a pad of beads and was nice and thick. With the wire speed up it did great. This 1/8 in material just can't handle the mig on A which is 21.5 volts. Needs to be lower around 20 volts. I ran several beads over the old pad and none were messed up cause the material could handle it at that thickness. This 1/8 had me losing faith. Damn i knew i couldn't be that bad at it. After that i ran several beads in the thick spot and all was well.
- 20180714_195943.jpg (49.3 KiB) Viewed 2891 times
1957 Lincoln Idealarc 300, Miller 211 v1 mig, Lincoln 3350, CK Worldwide CK17FV, 9FV
I did quite a bit project with a spool gun same specs as yours, 0.35 4043 on 1/8 alu. But I had big pieces, 2.5 inch wide c channel that I’d bent out of 1/8 thick alu sheets, 4 foot lengths. I had to go really fast to not burn through, a 2.5 inch weld took maybe 3-4 seconds. Turning it down let to very ugly tall thin welds. I didn’t like it at all I like to go slower and let the puddle do it’s thang!
I noticed on the chart on my welder the thinnest recommended alu for 0.35 is 5/16 and up to 1/2 not sure if that is for a spool gun tho. But I imagine the settings are similar for spool gun vs not.
I noticed on the chart on my welder the thinnest recommended alu for 0.35 is 5/16 and up to 1/2 not sure if that is for a spool gun tho. But I imagine the settings are similar for spool gun vs not.
If you divide by 2 it is.Demented wrote:Isn't A more like 10V, not 22V?
Only the lincoln C (any model) drops below 19v
1957 Lincoln Idealarc 300, Miller 211 v1 mig, Lincoln 3350, CK Worldwide CK17FV, 9FV
Spool gun doesn't change the settings it merely feeds the wire. Machine does the work regardless. The miller guns are too long to feed ally, they birdnest, but lincolns are short enough to do it no problem. I tried it with and without the spool, no change.JayWal wrote:I did quite a bit project with a spool gun same specs as yours, 0.35 4043 on 1/8 alu. But I had big pieces, 2.5 inch wide c channel that I’d bent out of 1/8 thick alu sheets, 4 foot lengths. I had to go really fast to not burn through, a 2.5 inch weld took maybe 3-4 seconds. Turning it down let to very ugly tall thin welds. I didn’t like it at all I like to go slower and let the puddle do it’s thang!
I noticed on the chart on my welder the thinnest recommended alu for 0.35 is 5/16 and up to 1/2 not sure if that is for a spool gun tho. But I imagine the settings are similar for spool gun vs not.
I couldn't figure out at first why I was having such issue running a bead. I'm no pro and have plenty to learn, but for what I do with steel I'm more than seasoned at mig. I knew the ally was a different beast, but I should have been able to run a bead. What I didn't count on was how quick it liquifies and how little surface tension it has. I learned a lot this go round. Barely scratched the surface though. Ally is not near as easy as steel is. All the cleaning, speed, etc is something I'm looking forward to getting down pat.
1957 Lincoln Idealarc 300, Miller 211 v1 mig, Lincoln 3350, CK Worldwide CK17FV, 9FV
I’ve got a Miller spoolgun and it works perfectly, even on 0.030 4043 wire. Not sure why you’ve struggled so much with them birds nesting ally. Typically it occurs when your speed is too high for the voltage. With ally and spoolguns, a push angle works much, much better.One1 wrote: Spool gun doesn't change the settings it merely feeds the wire. Machine does the work regardless. The miller guns are too long to feed ally, they birdnest, but lincolns are short enough to do it no problem. I tried it with and without the spool, no change.
Correct, I didn't say spool gun. Aside of some choppy feeding with cheaper spool guns, all of them feed ally pretty well.
1957 Lincoln Idealarc 300, Miller 211 v1 mig, Lincoln 3350, CK Worldwide CK17FV, 9FV
Huh? Isn't this your post? Isn't the entire thread about ally MIG via a spoolgun?One1 wrote:Correct, I didn't say spool gun. Aside of some choppy feeding with cheaper spool guns, all of them feed ally pretty well.
I accept that you meant MIG ally with a MIG box and not via a spool gun, but the words were yours.
Miller makes a 350P shop box for ally MIG, industrial level. Works like a Swiss watch. $6k worth of Swiss watch. Standard MIG liners and rollers for steel do not work well for ally wire for several reasons.One1 wrote: Spool gun doesn't change the settings it merely feeds the wire. Machine does the work regardless. The miller guns are too long to feed ally, they birdnest, but lincolns are short enough to do it no problem. I tried it with and without the spool, no change.
I guess I've been looking at the wrong machines then. You have the 180HD? I checked the chart on one of them at the store earlier today. 1/8" aluminum should be on setting E, not A, for the voltage.One1 wrote:If you divide by 2 it is.Demented wrote:Isn't A more like 10V, not 22V?
Only the lincoln C (any model) drops below 19v
"Your welds should sound like bacon. If your welds smell like bacon, you're on fire." - Uncle Bumblefuck (AvE)
NO. Everyone else read the thread and comprehended.cj737 wrote:Huh? Isn't this your post? Isn't the entire thread about ally MIG via a spoolgun?One1 wrote:Correct, I didn't say spool gun. Aside of some choppy feeding with cheaper spool guns, all of them feed ally pretty well.
I accept that you meant MIG ally with a MIG box and not via a spool gun, but the words were yours.
Last edited by One1 on Mon Jul 16, 2018 1:46 am, edited 1 time in total.
1957 Lincoln Idealarc 300, Miller 211 v1 mig, Lincoln 3350, CK Worldwide CK17FV, 9FV
It's A (but also can be B), the 1/4" is E, but only on the 180C. You seem to be looking at the C or Dual, where the setting is E. The only Lincoln 180 that drops as low as you state is the 180C or 180 DUAL. That's what they made them for is to be able to adjust constantly under very low voltage for thin sheetmetal. It's actually the only relevant difference in output. Both do the same voltage top end.Demented wrote:I guess I've been looking at the wrong machines then. You have the 180HD? I checked the chart on one of them at the store earlier today. 1/8" aluminum should be on setting E, not A, for the voltage.One1 wrote:If you divide by 2 it is.Demented wrote:Isn't A more like 10V, not 22V?
Only the lincoln C (any model) drops below 19v
Here is the 180 C
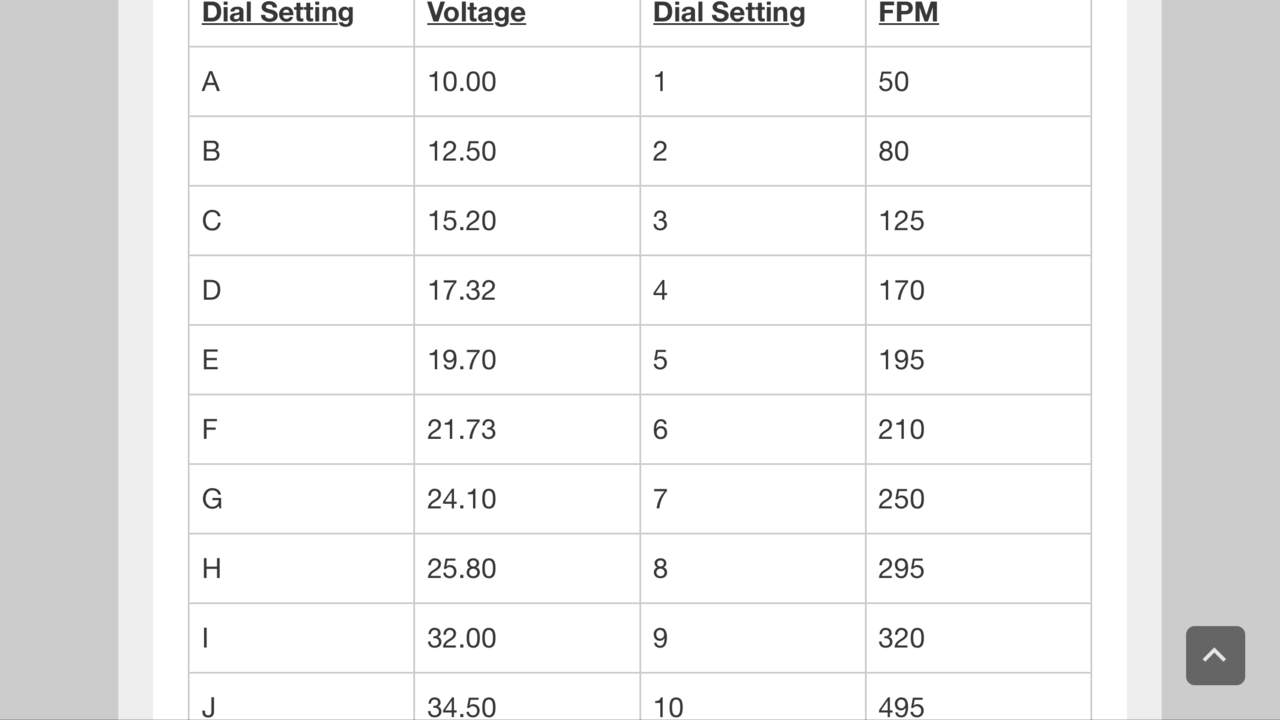
Here's the 180T
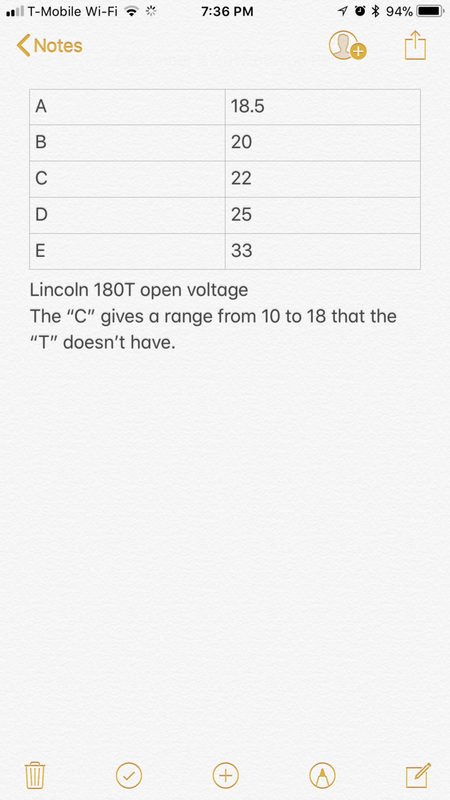
Here's the inside of the 180, as you can see it doesn't even mention E. My welder is 2 weeks old, fresh from the store. Also, my ally measurement which is 1/8" (12ga) for recommended setting B using Lincolns wire, but the Vulcan wire doesn't seem as good and barely handles A,

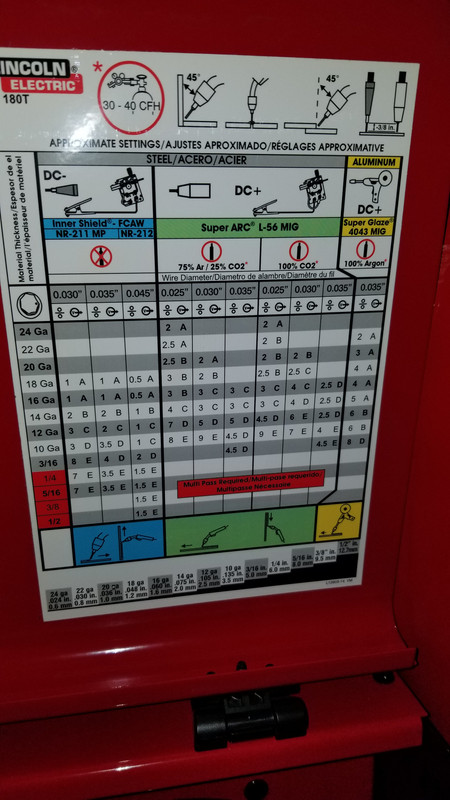
1957 Lincoln Idealarc 300, Miller 211 v1 mig, Lincoln 3350, CK Worldwide CK17FV, 9FV
I was checking 180 T/HD models. That chart is a bit different than what I've been seeing. Either way, checked the machines at work here too and for .035 wire with .125 aluminum, they're all suggesting 20-22v.
"Your welds should sound like bacon. If your welds smell like bacon, you're on fire." - Uncle Bumblefuck (AvE)
Yeah B is the usual recommended setting for the lincoln superglaze (20v). The chart is different for the 140, and probably says E for it.
1957 Lincoln Idealarc 300, Miller 211 v1 mig, Lincoln 3350, CK Worldwide CK17FV, 9FV
Return to “Welding Forum General Shop Talk”
Jump to
- Introductions & How to Use the Forum
- ↳ Welcome!
- ↳ Member Introductions
- ↳ How to Use the Forum
- ↳ Moderator Applications
- Welding Discussion
- ↳ Metal Cutting
- ↳ Tig Welding - Tig Welding Aluminum - Tig Welding Techniques - Aluminum Tig Welding
- ↳ Mig and Flux Core - gas metal arc welding & flux cored arc welding
- ↳ Stick Welding/Arc Welding - Shielded Metal Arc Welding
- ↳ Welding Forum General Shop Talk
- ↳ Welding Certification - Stick/Arc Welding, Tig Welding, Mig Welding Certification tests - Welding Tests of all kinds
- ↳ Welding Projects - Welding project Ideas - Welding project plans
- ↳ Product Reviews
- ↳ Fuel Gas Heating
- Welding Tips & Tricks
- ↳ Video Discussion
- ↳ Wish List
- Announcements & Feedback
- ↳ Forum News
- ↳ Suggestions, Feedback and Support
- Welding Marketplace
- ↳ Welding Jobs - Industrial Welding Jobs - Pipe Welding Jobs - Tig Welding Jobs
- ↳ Classifieds - Buy, Sell, Trade Used Welding Equipment
- Welding Resources
- ↳ Tradeshows, Seminars and Events
- ↳ The Welding Library
- ↳ Education Opportunities