This is the only welding specific forum I belong to as well. I started on the Miller site years ago under a different handle that I don't recall. I think I made it to two or three posts before losing interest. Seems it had that ever present inclusion of forum troll hierarchy that so many forums do these days. I was relieved to find a less 'hawked' forum in that regard. That, and the owner is obviously interested in the trade at the user end. I think that helps to set the atmosphere for the like minded not out to find conflict. I too spent a bit of time in the archives. This seems more true to form in the real world sense. I certainly don't feel more or less qualified than anyone here at any rate.
I know that some of the older guys can relate to this having come up through the ranks. Where as your skills progressed, that there was always a steady supply of cubs feeling their testosterone always trying to challenge the old guys. I never did when I was coming up, but instead, would let the pros challenge me where it counted. That's how you could tell you had potential just for the fact that they took interest. I still come across old pros from time to time. This place seems to have a good balance of that across the board.
If this was a welding shop, it would have a good team.
General welding questions that dont fit in TIG, MIG, Stick, or Certification etc.
- Otto Nobedder
-
Weldmonger
-
Posts:
-
Joined:Thu Jan 06, 2011 11:40 pm
-
Location:Near New Orleans
I have to agree with that.TamJeff wrote: ...If this was a welding shop, it would have a good team.
I also agree with what you said about the old hands and respect.
You are far more likely to earn respect by asking about what you don't know. You generally lose respect by trying to show them what you do know.
There comes a stage where you have the experience and age where mutual respect is a natural thing, but the "testosterone-laden pups" you described may never reach it, if they don't learn how respect is earned in a trade where people are entitled to call themselves craftsmen.
- Otto Nobedder
-
Weldmonger
-
Posts:
-
Joined:Thu Jan 06, 2011 11:40 pm
-
Location:Near New Orleans
I also have to think, from what I've seen, if you took the top, say, 30 most active posters, here, and ranked there skills in some appropriate way, the #1 for each would be different, if only a little. This has to be the most diverse bunch of welders that ever got on so well.
Even the novices here seem to have a good standing. You get the idea that they would be quick studies just by their enthusiasm alone and with not being afraid to show their work. More than likely, that's how we got to be where we are and it also goes to show that the pros here have not forgotten where they came from. Most of us are our own worst critics by now anyway. All of the best welders I have ever known have seemingly had this in common.
Miller ABP 330, Syncrowave 250, Dynasty 300 DX.
Honorary member of the Fraternity of Faded Tee Shirts.
Honorary member of the Fraternity of Faded Tee Shirts.
Billbong
- Billbong
-
Workhorse
-
Posts:
-
Joined:Thu Oct 04, 2012 10:28 am
-
Location:Melbourne, Australia.
Hi all, just a few words to put into perspective the actual phrase or title Welder, and for that matter a welding business.
If you're a welder, it means you just weld what is put in front of you, no fabricating parts or making parts with other machinery or preparing parts to allow welding to take place.....welding is the final fixing when it is already assembled and in position.
A welding busines per se is an enterprise that welds metal as and when required.....it does not specifically manufacture any item, but as in a woodworking or carpentry busines a welder is the glue mechanic that sticks the wood together when someone else has cut it to a shape and assembled it.
So a welding busines has really got to be a combination of fabrication and mechanical as well and all the disciplines that pertain to being a mechanic or metal worker apply equally before you can actually aply a welding process.
Going to school and learning how to Mig weld only makes you proficient in applying metal to metal that is in a state to be finally fixed permanently together using one process, and if you don't have the expertise to assemble and prepare the parts you are just a welder, the lowest rung on the ladder.
I've seen many people who attempt to be a jack of all trades and having outlayed for a welding set-up now attempt to manufacture with machinery, whereas the knowledge that is present is only sufficient to join metals by one process or another.
A fabricator on the other hand is a much more versatile type of person who would make an item from beginning to end using various processes, and might even use the skills of a person who only did welding as an occupation even though he could do the welding himself but chooses not to tie himself to a bench for hours at a time in one position.
Ian.
If you're a welder, it means you just weld what is put in front of you, no fabricating parts or making parts with other machinery or preparing parts to allow welding to take place.....welding is the final fixing when it is already assembled and in position.
A welding busines per se is an enterprise that welds metal as and when required.....it does not specifically manufacture any item, but as in a woodworking or carpentry busines a welder is the glue mechanic that sticks the wood together when someone else has cut it to a shape and assembled it.
So a welding busines has really got to be a combination of fabrication and mechanical as well and all the disciplines that pertain to being a mechanic or metal worker apply equally before you can actually aply a welding process.
Going to school and learning how to Mig weld only makes you proficient in applying metal to metal that is in a state to be finally fixed permanently together using one process, and if you don't have the expertise to assemble and prepare the parts you are just a welder, the lowest rung on the ladder.
I've seen many people who attempt to be a jack of all trades and having outlayed for a welding set-up now attempt to manufacture with machinery, whereas the knowledge that is present is only sufficient to join metals by one process or another.
A fabricator on the other hand is a much more versatile type of person who would make an item from beginning to end using various processes, and might even use the skills of a person who only did welding as an occupation even though he could do the welding himself but chooses not to tie himself to a bench for hours at a time in one position.
Ian.
- Otto Nobedder
-
Weldmonger
-
Posts:
-
Joined:Thu Jan 06, 2011 11:40 pm
-
Location:Near New Orleans
Ian,
I hope you've looked at Jeff's pictures and posts.
The man transcends "weldor" and "fabricator". He qualifies as "craftsman".
However, your comments are wise words for any Tom, Dick, or Shirley who's been shop-welding for five years and think they are ready to take the plunge.
Steve S
I hope you've looked at Jeff's pictures and posts.
The man transcends "weldor" and "fabricator". He qualifies as "craftsman".
However, your comments are wise words for any Tom, Dick, or Shirley who's been shop-welding for five years and think they are ready to take the plunge.
Steve S
Thanks for the compliment Steve, and thank you for the well thought out post, Billbong. I am a welder 2nd to fabricating, but it seems that most people expect a welding shop to do it all, at least in a non union state. Not having the actual welding skills was always the limiting factor in my case, which is why I went to school for it.
Miller ABP 330, Syncrowave 250, Dynasty 300 DX.
Honorary member of the Fraternity of Faded Tee Shirts.
Honorary member of the Fraternity of Faded Tee Shirts.
seanmurphy265
- seanmurphy265
-
New Member
-
Posts:
-
Joined:Sat Feb 16, 2013 1:26 pm
I've been trying to slowly build my own business on the side. I would like to work for myself when I have all the needed tools. 30k is pretty close to what you will end up spending to get started. I have not spent that much yet, but I know that I will before it's all said and done! I had to purchase insurance and workmans comp to do a job in the fall that was a $7,600.00 quote. When I received payment I paid my insurance and workmans comp for the year, and walked away with $1,000.00 after the bills were paid. My wife and I figured that it would be best to pay the insurance for a year, and if another job comes along that's one less worry! Now that I have liability insurance I wish I would have never worked without it! I've learned that everything you can do to my your business legit helps (insurance, website, credit card payments, etc).
I've purchase new equipment as I am able. I also look at purchases differently now than before; I know ask how can this help me: be more efficient, make the job easier, pay for itself, make me more money, etc. I also get rid of tools that sit for a long time, and then I take that money to purchase something I need.
Being in business is not easy but I still hope to work for myself soon. I have a few bills to pay off and when I get six months income in the bank I will give it a shot!
I've purchase new equipment as I am able. I also look at purchases differently now than before; I know ask how can this help me: be more efficient, make the job easier, pay for itself, make me more money, etc. I also get rid of tools that sit for a long time, and then I take that money to purchase something I need.
Being in business is not easy but I still hope to work for myself soon. I have a few bills to pay off and when I get six months income in the bank I will give it a shot!
foamballer
- foamballer
-
Active Member
-
Posts:
-
Joined:Fri Feb 15, 2013 3:57 am
-
Location:Australia
Tamjeff, I don't have a welding business, but I have a few ideas. I'm in the environmental engineering business. I was hired to start up a satellite office for a capital city based consultancy. As it happens, the parent company was bought up by a multi-national company and all of a sudden I was part of a 30,000 strong work force. I didn't like that much and finally made an offer to buy "my" section of the business (and take the couple of employees I'd hired with me). I can honestly say it is the best career decision I have ever made. There are heaps of things that need to come together to make it work, but the most beneficial thing for me was that I had a big forward contract available. I worked out what the profit/risk was based on previous jobs and openly disclosed this as part of the buyout deal. I effectively paid away half the profit on that job, but having a big long-term contract was worth far more than that. My suggestion is that you try and find such a contract as your opportunity to make your move. Win the work first (make sure the client wants YOU), then make your move.
Back on the welding side. I know a guy who's operating out of a little shed. He's also mobile (which is 60% of his work), but prefers to work in the shed where he's got most of his tools. Seems to be very low overhead. I'd reckon he's got $20K worth of gear if that. He makes a reasonable living. His jobs are: boat repairs/modifications (e.g. transom pods, live bait tanks, ladders, racks, booms, structural repairs), agricultural and earth-moving gear. He's got a little of network of guys he farms out bits of work to so that he can offer a bit more than just welding (sheet metal guy with a good press-brake, mechanical guy for bearings/hydraulics). People keep coming back to him because he's inventive (solves the problem), does nice work, is enthusiastic, a nice bloke and is proud of his work but not arrogant. No job is too small. He charges by the hour (not lump sum), but gives very good estimates and often comes in under his estimated price.
Back on the welding side. I know a guy who's operating out of a little shed. He's also mobile (which is 60% of his work), but prefers to work in the shed where he's got most of his tools. Seems to be very low overhead. I'd reckon he's got $20K worth of gear if that. He makes a reasonable living. His jobs are: boat repairs/modifications (e.g. transom pods, live bait tanks, ladders, racks, booms, structural repairs), agricultural and earth-moving gear. He's got a little of network of guys he farms out bits of work to so that he can offer a bit more than just welding (sheet metal guy with a good press-brake, mechanical guy for bearings/hydraulics). People keep coming back to him because he's inventive (solves the problem), does nice work, is enthusiastic, a nice bloke and is proud of his work but not arrogant. No job is too small. He charges by the hour (not lump sum), but gives very good estimates and often comes in under his estimated price.
i own a small business, not essentially welding but car repair (all aspects) and its not all its cracked up to be. but been like this for 5 years and making less now than i did when i started out. i couldn't go work for someone now after being my own entity for so long so i have to keep struggling on unfortunately.
would i do the welding only as a business? heck no. tig/mig/arc is not my thing although i am learning and taking in the info people are giving me and will put this to good practice, welding in the UK isn't a great paid job unless you have huge contracts, then there is the high gas prices and high equipment prices to boot.
would i do the welding only as a business? heck no. tig/mig/arc is not my thing although i am learning and taking in the info people are giving me and will put this to good practice, welding in the UK isn't a great paid job unless you have huge contracts, then there is the high gas prices and high equipment prices to boot.
Has anyone noticed the quality of manufacturing as of late in this country? It's not just the actual offshore jobs they are trying to return here, but the lesser import quality and wages as well. They are basically adhering to the walmartification of America. If it looks like the real thing from 50 ft away, it's good enough. An internet full of people (label whores) who will chime in with hype of a product's worth, for no other reason than to justify their own cheapness, and lack of discipline for saving a few more weeks for the real thing, and heaven forbid someone of obvious skill dares to make a buck off of them. An economy where these so-called, bottom line awareness folks, out of the other corner of their mouths, don't feel a least bit foolish spending 300 dollars on a plastic pair of sunglasses.
There are some notions worth keeping alive. Not for those outlined above, but those few who know what skilled work entails. I take a cab somewhere, it costs 13 dollars, I give the guy a 20. I tip waitresses who work hard 20% and beyond, just for having been there. I am aware of what I spend and how it equates in gallons of gasoline for their cars. The most I may have to sacrifice for such outlandish practices, is that I may have to forego drinking "craft" beer, or a host of foolish apps that make my cell phone "smarter."
To be perfectly honest. . .I am tired of giving good work away to cheapskates. I am to the point where I would rather eat bugs than to perpetuate such an economy, that produces very little with anything of value these days, or, to be lumped in with hacks for the reasons loosely outlined above.
Check this out. This is what we are up against. This is bad by even eyeball standards, yet there is some internet dweeb swearing by it because his cheap-ass got a bargain, even though it costs close to what the real thing does. Then boasted how it is anodized after the fact, where they didn't even bother to get rid of the TIG frost first. This has to be pennies on the dollar piecework at some chop shop, where the bottom line dictates all, mostly centered around greed.
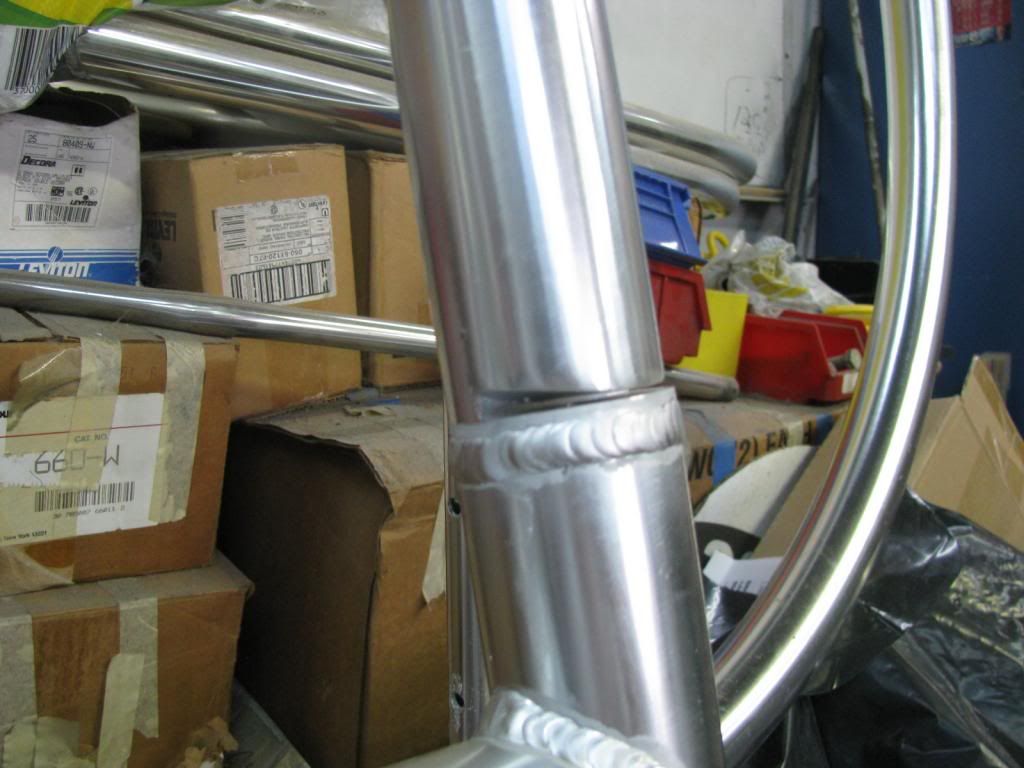
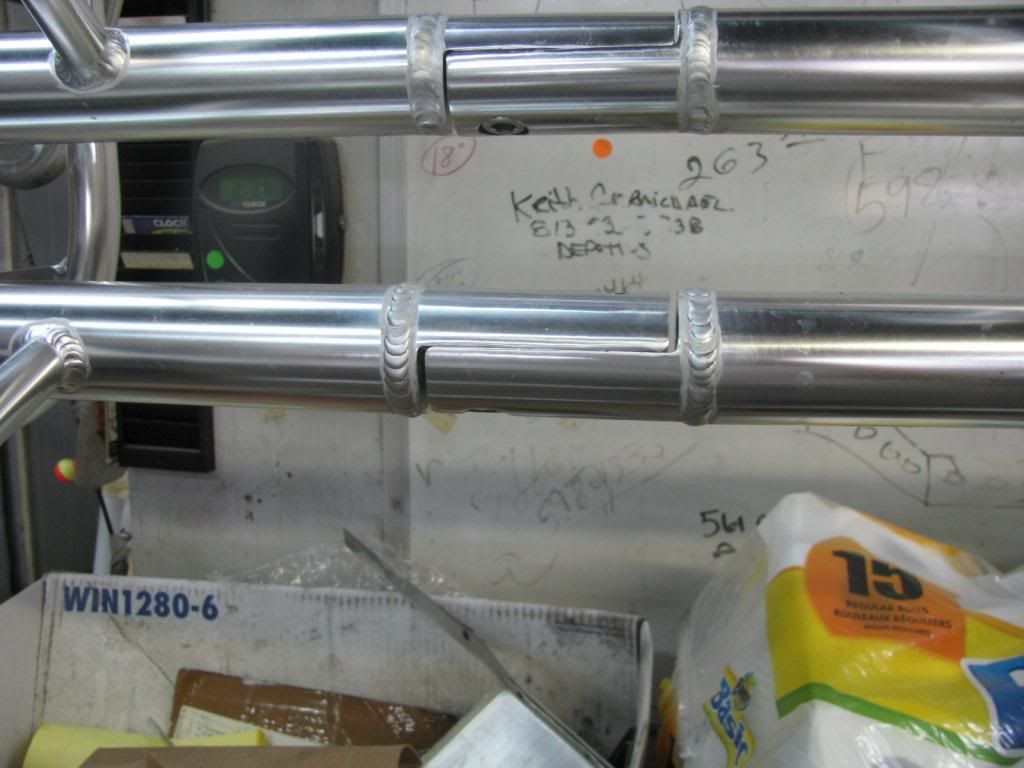
By now I don't care about the money. I can work another job and just do this on the side, for no other reason than to make sure that someone willing to pay a fair price gets what they pay for, even if I do one a year and don't make a living from it at all, and just for general principle.
There are some notions worth keeping alive. Not for those outlined above, but those few who know what skilled work entails. I take a cab somewhere, it costs 13 dollars, I give the guy a 20. I tip waitresses who work hard 20% and beyond, just for having been there. I am aware of what I spend and how it equates in gallons of gasoline for their cars. The most I may have to sacrifice for such outlandish practices, is that I may have to forego drinking "craft" beer, or a host of foolish apps that make my cell phone "smarter."
To be perfectly honest. . .I am tired of giving good work away to cheapskates. I am to the point where I would rather eat bugs than to perpetuate such an economy, that produces very little with anything of value these days, or, to be lumped in with hacks for the reasons loosely outlined above.
Check this out. This is what we are up against. This is bad by even eyeball standards, yet there is some internet dweeb swearing by it because his cheap-ass got a bargain, even though it costs close to what the real thing does. Then boasted how it is anodized after the fact, where they didn't even bother to get rid of the TIG frost first. This has to be pennies on the dollar piecework at some chop shop, where the bottom line dictates all, mostly centered around greed.
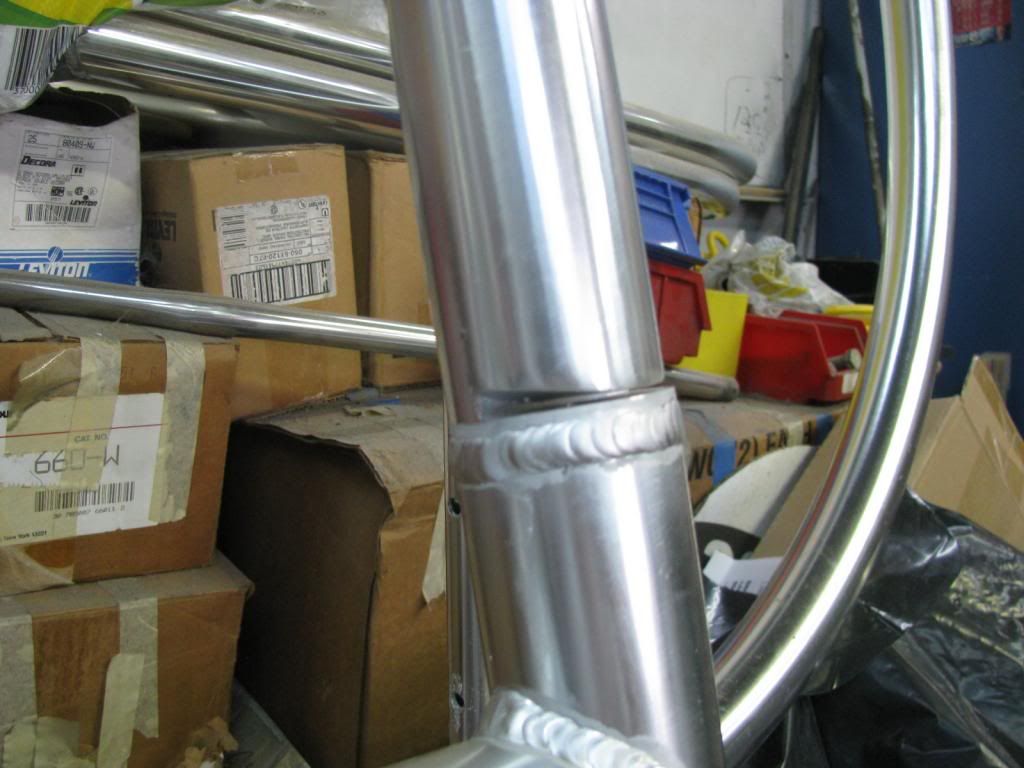
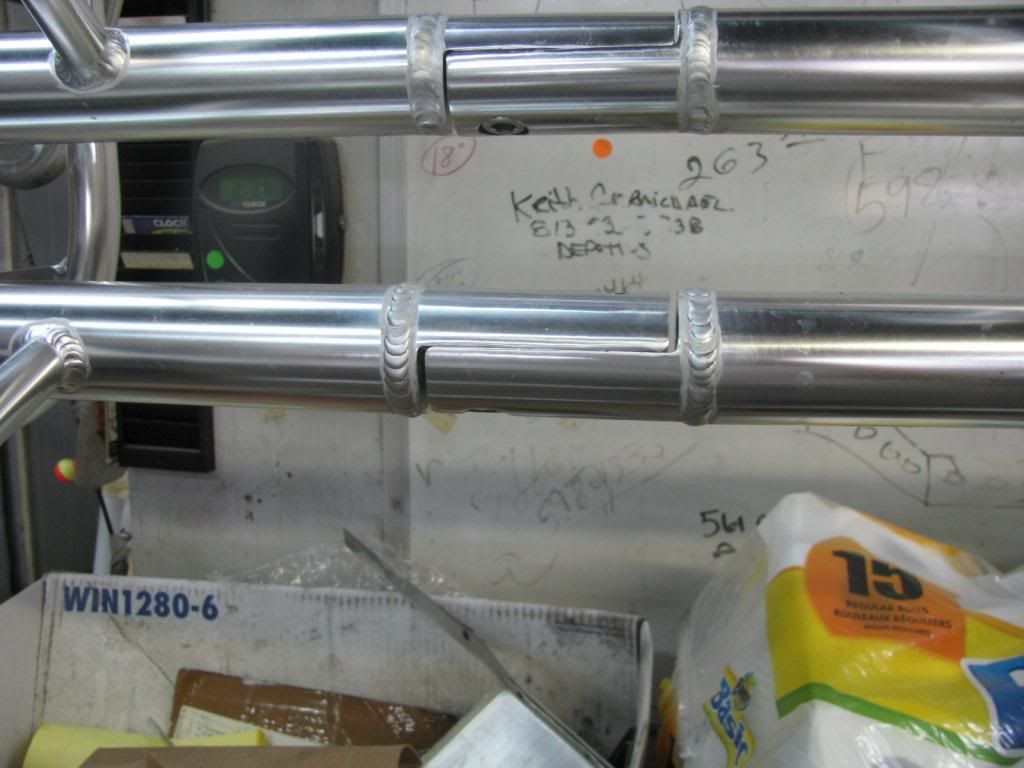
By now I don't care about the money. I can work another job and just do this on the side, for no other reason than to make sure that someone willing to pay a fair price gets what they pay for, even if I do one a year and don't make a living from it at all, and just for general principle.
Miller ABP 330, Syncrowave 250, Dynasty 300 DX.
Honorary member of the Fraternity of Faded Tee Shirts.
Honorary member of the Fraternity of Faded Tee Shirts.
- Otto Nobedder
-
Weldmonger
-
Posts:
-
Joined:Thu Jan 06, 2011 11:40 pm
-
Location:Near New Orleans
Good for you, Jeff!
And thanks for the reminder! I sometimes forget how lucky I am to have a job where "do it 100% right" absolutely trumps "do it quickly", and how rare such jobs are in a Wal-Mart culture.
Steve S
And thanks for the reminder! I sometimes forget how lucky I am to have a job where "do it 100% right" absolutely trumps "do it quickly", and how rare such jobs are in a Wal-Mart culture.
Steve S
You do have a respectable job and you do respectable work. Half of why I follow your threads here. It's obvious that you and the company you work for aren't just trying to get over. My trade used to be the same way when the "old money" was paying for it. It wasn't uncommon for a customer to take out a tape measure and check the work you did. Nowadays, it's all about a bunch of posing and name dropping. There is a couple outfits that do what I do that I respect their work and I will even recommend them without a 2nd thought just for it being the right thing to do.
When I started where I am at now, I told the owner, from much of my own experience, that if he wanted a hack, I wasn't the right guy. I do take longer and I do it right, long having witnessed that there is two realms of this type of work. There is either "custom", or "production", but there is no such animal as "custom production." Yet customers and business owners try to prove that wrong, instead of just aiming for those specific markets.
You may be old enough to remember the discernible difference between things that were built overseas and here. Take metal furniture for instance. The import would be held together with tacks and stitches to where every 1/4" of filler metal must have been inventoried and would break under normal use. Now it's getting harder to tell the difference.
People tell me, "Well, you just don't understand the complexity of a global economy." Yeah, I understand it plenty, which is exactly why I intend to avoid it as much as possible. I'm just a working slob, yet I understand the value of a job well done and expect to pay accordingly. If I walk into a place of business with a designer facade, and it's obvious that the banks have their hand in every aspect of it's existence, I know what I am paying for. It's not the guy in the back driving an old relic hanging on to a meager existence by a thread, who likely paid his dues 10's of times over for someone else's excessive waistline.
The one thing that many of us do have here, is enough of an education to believably convey our value, above and beyond that of a fancy building full of Chinese tooling, and how to appeal to a market that understands that. I am noticing a trend with a portion of the market that is getting wary of industry as it is practiced today. All they need to know is that a viable alternative exists, and although those may be few and far between, in the long run, it should at least average out, just considering avoiding that type of stress alone, and makes a fool of no one in the process, except for perhaps, the banks.
When I started where I am at now, I told the owner, from much of my own experience, that if he wanted a hack, I wasn't the right guy. I do take longer and I do it right, long having witnessed that there is two realms of this type of work. There is either "custom", or "production", but there is no such animal as "custom production." Yet customers and business owners try to prove that wrong, instead of just aiming for those specific markets.
You may be old enough to remember the discernible difference between things that were built overseas and here. Take metal furniture for instance. The import would be held together with tacks and stitches to where every 1/4" of filler metal must have been inventoried and would break under normal use. Now it's getting harder to tell the difference.
People tell me, "Well, you just don't understand the complexity of a global economy." Yeah, I understand it plenty, which is exactly why I intend to avoid it as much as possible. I'm just a working slob, yet I understand the value of a job well done and expect to pay accordingly. If I walk into a place of business with a designer facade, and it's obvious that the banks have their hand in every aspect of it's existence, I know what I am paying for. It's not the guy in the back driving an old relic hanging on to a meager existence by a thread, who likely paid his dues 10's of times over for someone else's excessive waistline.
The one thing that many of us do have here, is enough of an education to believably convey our value, above and beyond that of a fancy building full of Chinese tooling, and how to appeal to a market that understands that. I am noticing a trend with a portion of the market that is getting wary of industry as it is practiced today. All they need to know is that a viable alternative exists, and although those may be few and far between, in the long run, it should at least average out, just considering avoiding that type of stress alone, and makes a fool of no one in the process, except for perhaps, the banks.
Miller ABP 330, Syncrowave 250, Dynasty 300 DX.
Honorary member of the Fraternity of Faded Tee Shirts.
Honorary member of the Fraternity of Faded Tee Shirts.
- Otto Nobedder
-
Weldmonger
-
Posts:
-
Joined:Thu Jan 06, 2011 11:40 pm
-
Location:Near New Orleans
There is a lot of education here, in a VERY broad cross-section.
I think that's a big part of why I enjoy this forum so much. We're united in welding alone, and diverse in every other aspect of our lives. Where else can you find that without competition and "posing"?
I think that's a big part of why I enjoy this forum so much. We're united in welding alone, and diverse in every other aspect of our lives. Where else can you find that without competition and "posing"?
Return to “Welding Forum General Shop Talk”
Jump to
- Introductions & How to Use the Forum
- ↳ Welcome!
- ↳ Member Introductions
- ↳ How to Use the Forum
- ↳ Moderator Applications
- Welding Discussion
- ↳ Metal Cutting
- ↳ Tig Welding - Tig Welding Aluminum - Tig Welding Techniques - Aluminum Tig Welding
- ↳ Mig and Flux Core - gas metal arc welding & flux cored arc welding
- ↳ Stick Welding/Arc Welding - Shielded Metal Arc Welding
- ↳ Welding Forum General Shop Talk
- ↳ Welding Certification - Stick/Arc Welding, Tig Welding, Mig Welding Certification tests - Welding Tests of all kinds
- ↳ Welding Projects - Welding project Ideas - Welding project plans
- ↳ Product Reviews
- ↳ Fuel Gas Heating
- Welding Tips & Tricks
- ↳ Video Discussion
- ↳ Wish List
- Announcements & Feedback
- ↳ Forum News
- ↳ Suggestions, Feedback and Support
- Welding Marketplace
- ↳ Welding Jobs - Industrial Welding Jobs - Pipe Welding Jobs - Tig Welding Jobs
- ↳ Classifieds - Buy, Sell, Trade Used Welding Equipment
- Welding Resources
- ↳ Tradeshows, Seminars and Events
- ↳ The Welding Library
- ↳ Education Opportunities