I saw some dude on Youtube putting caulk on ugly welds, and I thought it was genius, apart from using a product that would eventually crack and fall off. I have started using epoxy putty to cover welds and make projects look cool. Wonder if anyone else here does this. I just bought a big ol' can of Bondo this morning!
I am doing this for more than one reason.
First of all, I have learned not to use too much weld. I have created projects with welds several inches long where an inch would have been overkill, and the reason was that open joints look bad and let stuff in, including bugs. Using too much weld wasted my time and wire, and it also caused distortion. Weld filler is usually the wrong material for sealing joints.
Second thing, I have been known to make some pretty ugly welds, and grinding gets to be tiresome.
Third, sometimes fairing stuff in with epoxy makes a project look a lot better, even if the welds are pretty.
Fourth, sometimes metal dealers let stuff get pitted and nasty, and it's not like you can make them dig through their stock to find you pretty steel.
General welding questions that dont fit in TIG, MIG, Stick, or Certification etc.
- Chips O'Toole
-
Heavy Hitter
-
Posts:
-
Joined:Thu Dec 01, 2016 12:30 pm
-
Location:FL
This also occurred to me when I was building my 8ft tall MIG cart. I was using mostly 14/16ga 1½" square tubing, and in a few places, I realized that welding out every single joint would have been overkill and also lead to more distortion. I ended up leaving some of them un-welded and simply left them as is before I applied black lacquer paint. I'm not worried about bugs, as they won't be eating the steel anytime soon.
- Chips O'Toole
-
Heavy Hitter
-
Posts:
-
Joined:Thu Dec 01, 2016 12:30 pm
-
Location:FL
In case anyone is interested, I tried Bondo today, and it's impossible to use. It starts out too runny to put in place, and then in a few minutes it turns into something like a cold Sugar Daddy mixed with sawdust. Then it turns into grainy cement.
The thing that worked best for me was a JB Weld Steelstik. Unfortunately, they're expensive for big projects. You have to smooth this stuff out after you apply it, and using gloves, as recommended, makes it impossible. You have to take the gloves off and put water on your fingers.
You're supposed to wear gloves, but it looks like the choice is between 1) safety and a ruined project or 2) a decent-looking result and the possibility of cancer and birth defects and whatever 20 years down the road. I think I made the right choice, because my cart will look really nice next to my coffin.
Maybe Bondo general purpose putty would work. I have not tried it.
The thing that worked best for me was a JB Weld Steelstik. Unfortunately, they're expensive for big projects. You have to smooth this stuff out after you apply it, and using gloves, as recommended, makes it impossible. You have to take the gloves off and put water on your fingers.
You're supposed to wear gloves, but it looks like the choice is between 1) safety and a ruined project or 2) a decent-looking result and the possibility of cancer and birth defects and whatever 20 years down the road. I think I made the right choice, because my cart will look really nice next to my coffin.
Maybe Bondo general purpose putty would work. I have not tried it.
I was socially distant before it was cool.
- Chips O'Toole
-
Heavy Hitter
-
Posts:
-
Joined:Thu Dec 01, 2016 12:30 pm
-
Location:FL
I just saw a video of a guy using a TIG torch to make ugly MIG welds look better. Can't believe I didn't think of that.
I was socially distant before it was cool.
i weld everything.
i'm used to stuff being hosed down or around wash water, so any gap and the tubes just get filled with crud. if its steel any gap rusts, or gets water in there and leaks rust.
i'm used to stuff being hosed down or around wash water, so any gap and the tubes just get filled with crud. if its steel any gap rusts, or gets water in there and leaks rust.
tweak it until it breaks
That's exactly the use-case where 'seam sealer' was invented
Used on spot- or stitch-welded parts that you still want protected and then possibly paint.
It's like a super tenacious caulk that's designed to resist a lot of weather influences and be capable of being painted over. It also stays just a little bit flexible, unlike epoxies, so it won't crack off when parts flex or under thermal expansion and contraction. You can find it in car bodywork shops, but it's used in more manufacturing where joints need sealing over.
Bye, Arno.

Used on spot- or stitch-welded parts that you still want protected and then possibly paint.
It's like a super tenacious caulk that's designed to resist a lot of weather influences and be capable of being painted over. It also stays just a little bit flexible, unlike epoxies, so it won't crack off when parts flex or under thermal expansion and contraction. You can find it in car bodywork shops, but it's used in more manufacturing where joints need sealing over.
Bye, Arno.
i had a chuckle at that. just to show how different places can be, here good trailers are not painted.
tweak it until it breaks
Do ya best, sikaflex the rest!
I was given that as actual advice when I first was an apprentice, it still makes me chuckle hard. I did think it was a joke till I had to cut out a heap of welds on China made structures that "didnt look right" much to my suprise they were 3 tacks covered by a fillet of putty, then covered in epoxy paint.
I was given that as actual advice when I first was an apprentice, it still makes me chuckle hard. I did think it was a joke till I had to cut out a heap of welds on China made structures that "didnt look right" much to my suprise they were 3 tacks covered by a fillet of putty, then covered in epoxy paint.

Ditto here in most parts of europe.
Regulations around vehicle and trailer approvals make it time consuming for any individual to build a trailer and get it approved for road use, so most don't bother and manufactered ones are most of the time hot dipped and not painted at all. Because of gross weight and load ratings and restrictions on drivers licenses for allowable tow weights a lot of alu is used for the upper parts.
A common style general-use trailer (not for carrying cars) for small business use looks someting like this here:
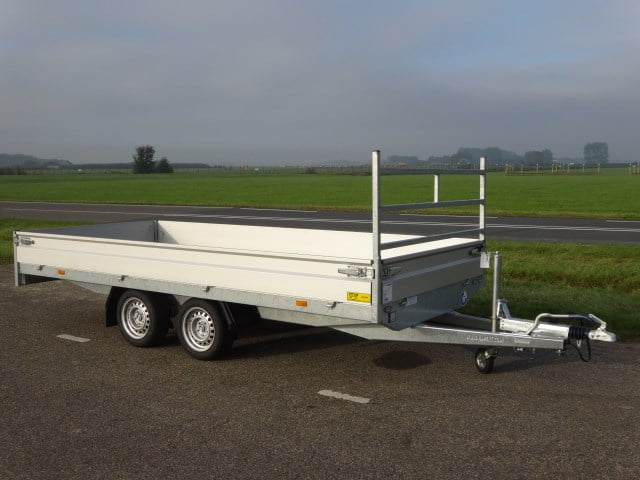
Hot-dipped chassis and frame, alu upper parts, etc. When treated right with proper maintenance these last for ages and ages and still look/work fine after 25+ years.
Bye, Arno.
home made trailers are common here and easy to get approved (a little to easy imho). also easy to get it galved.Arno wrote: ↑Fri Aug 12, 2022 1:19 am
Ditto here in most parts of europe.
Regulations around vehicle and trailer approvals make it time consuming for any individual to build a trailer and get it approved for road use, so most don't bother and manufactered ones are most of the time hot dipped and not painted at all. Because of gross weight and load ratings and restrictions on drivers licenses for allowable tow weights a lot of alu is used for the upper parts.
A common style general-use trailer (not for carrying cars) for small business use looks someting like this here:
Hot-dipped chassis and frame, alu upper parts, etc. When treated right with proper maintenance these last for ages and ages and still look/work fine after 25+ years.
Bye, Arno.
the aluminium side boards is interesting. we typically don't due to cost and they generally bend to much when using tie downs.
tweak it until it breaks
- Chips O'Toole
-
Heavy Hitter
-
Posts:
-
Joined:Thu Dec 01, 2016 12:30 pm
-
Location:FL
The crazy trailer regulations sound a lot like China, where it's illegal to wash your own car or modify it!
Obviously, the rules are excessive. We don't have them here, and we are not experiencing an epidemic of trailer-related deaths.
Obviously, the rules are excessive. We don't have them here, and we are not experiencing an epidemic of trailer-related deaths.
I was socially distant before it was cool.
Return to “Welding Forum General Shop Talk”
Jump to
- Introductions & How to Use the Forum
- ↳ Welcome!
- ↳ Member Introductions
- ↳ How to Use the Forum
- ↳ Moderator Applications
- Welding Discussion
- ↳ Metal Cutting
- ↳ Tig Welding - Tig Welding Aluminum - Tig Welding Techniques - Aluminum Tig Welding
- ↳ Mig and Flux Core - gas metal arc welding & flux cored arc welding
- ↳ Stick Welding/Arc Welding - Shielded Metal Arc Welding
- ↳ Welding Forum General Shop Talk
- ↳ Welding Certification - Stick/Arc Welding, Tig Welding, Mig Welding Certification tests - Welding Tests of all kinds
- ↳ Welding Projects - Welding project Ideas - Welding project plans
- ↳ Product Reviews
- ↳ Fuel Gas Heating
- Welding Tips & Tricks
- ↳ Video Discussion
- ↳ Wish List
- Announcements & Feedback
- ↳ Forum News
- ↳ Suggestions, Feedback and Support
- Welding Marketplace
- ↳ Welding Jobs - Industrial Welding Jobs - Pipe Welding Jobs - Tig Welding Jobs
- ↳ Classifieds - Buy, Sell, Trade Used Welding Equipment
- Welding Resources
- ↳ Tradeshows, Seminars and Events
- ↳ The Welding Library
- ↳ Education Opportunities