My problem is, I don't always cut perfect 45s. And even if I do, the outside edge is difficult to weld without punching through sometimes. I know I can turn the power down or tack-tack-tack it, but I like the welds on my furniture to be wide and flat, which means I need to turn up the heat a bit. (I'm talking MIG welding here). The wide flat welds make it look heavy, even though it's only 16 gauge. I think with an inner sleeve piece like this, I could turn up the heat a good bit. And as a side benefit, it would also help with assembling the piece, since it's usually just me, I end up using lots of clamps and things before I start tacking. These sleeves would kind of keep things together a bit (a little bit) before tacking.
I know I could make something like this, but I'm wondering if something like this exists already, for sale? I've searched around a bit, but I can't seem to find something like this, maybe I'm not using the right search term
For my furniture, I usually use 1" square tubing (mild steel) that is 16 gauge thick. I've greatly exaggerated the wall thickness in these images, so you can better see what I'm talking about.
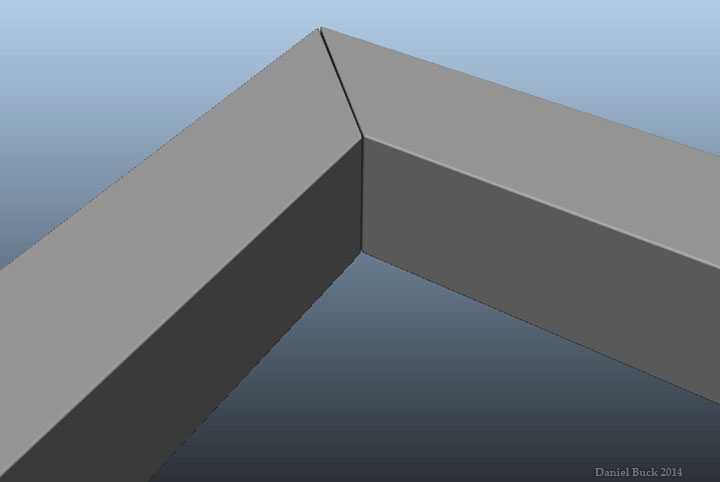

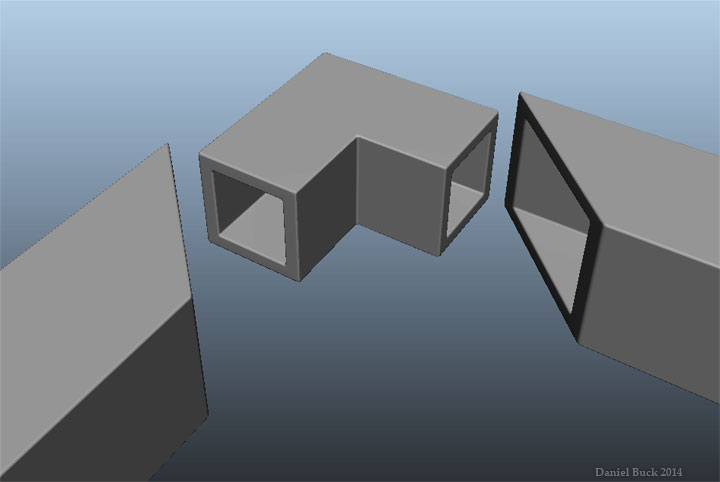