http://arweld.net/userfiles/image/008.JPG
I see americans use much slimmer handles and with much more flexible torch hoses and I think, that looks nice. But I don't have a pedal, I couldn't use such a torch unless I mounted a trigger on it, which kinda brings me back to square one doesn't it? i looked up what a pedal for a kemppi would cost and it said 800 euros!!!!??? I found some 3rd party from the UK for 250, still too steep for my shallow pockets.
Only one way to go, build my own. Which turned out to be more difficult than I thought for this welder. It doesn't work like most of you are used to, you set the max current on the welder and that's it. Any remote, hand or foot (I have a hand remote, meant for stick welding) takes over completely. So Kemppi pedals have a min and max adjustment on the pedal itself. I would have to replicate this and I have no electronics skill or experience. Fortunately I was able to get a schematic from Kemppi, and with the help of some electronics forums I was able to start building:
Started out with a scrap u-beam I cut to shape with the portaband
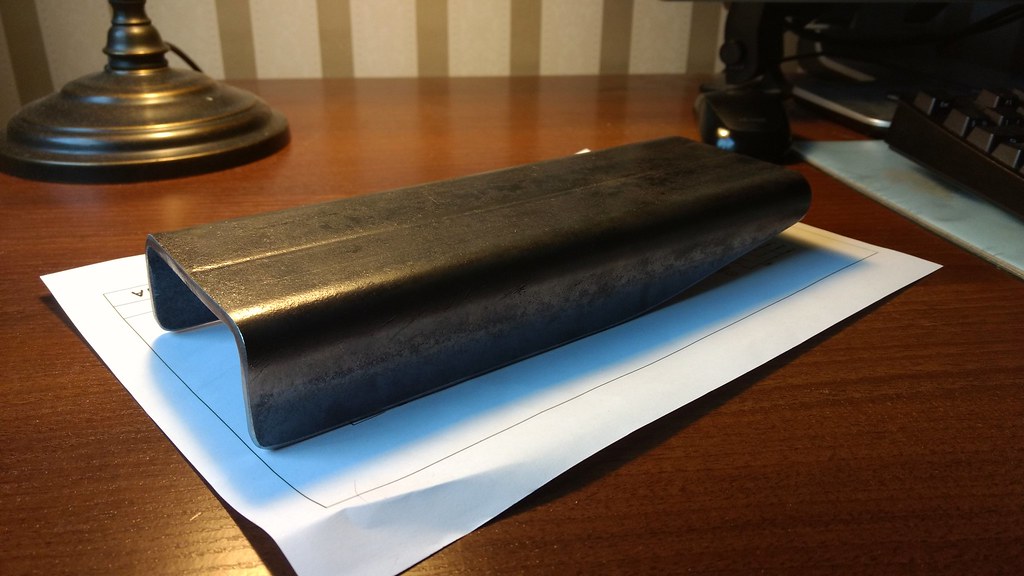
Bottom plate from scraps:
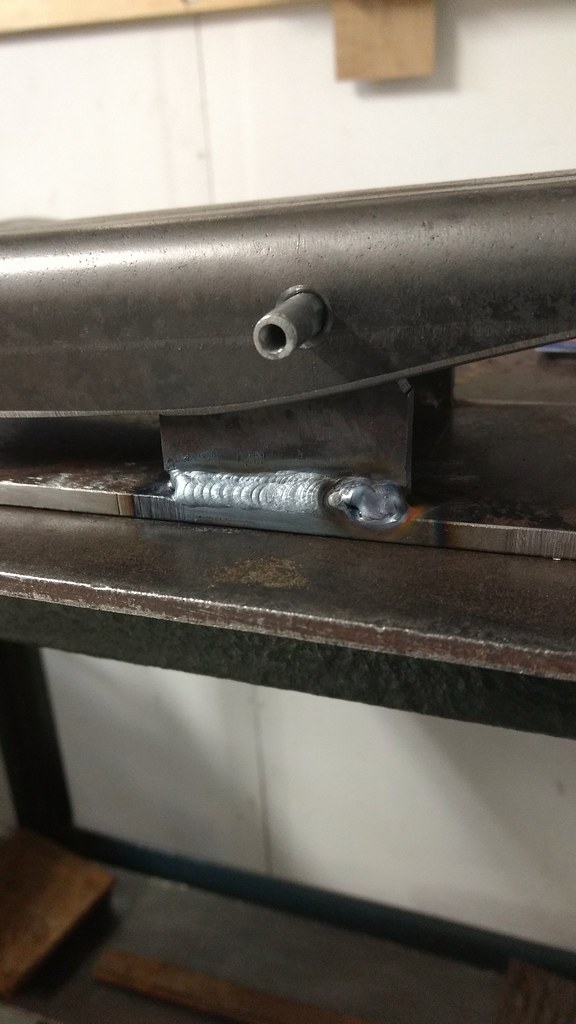
Potentiometers for min and max mounted on the front, copying the kemppi design here. I found some sprockets that fit on the pots, thought they looked cool as knobs:
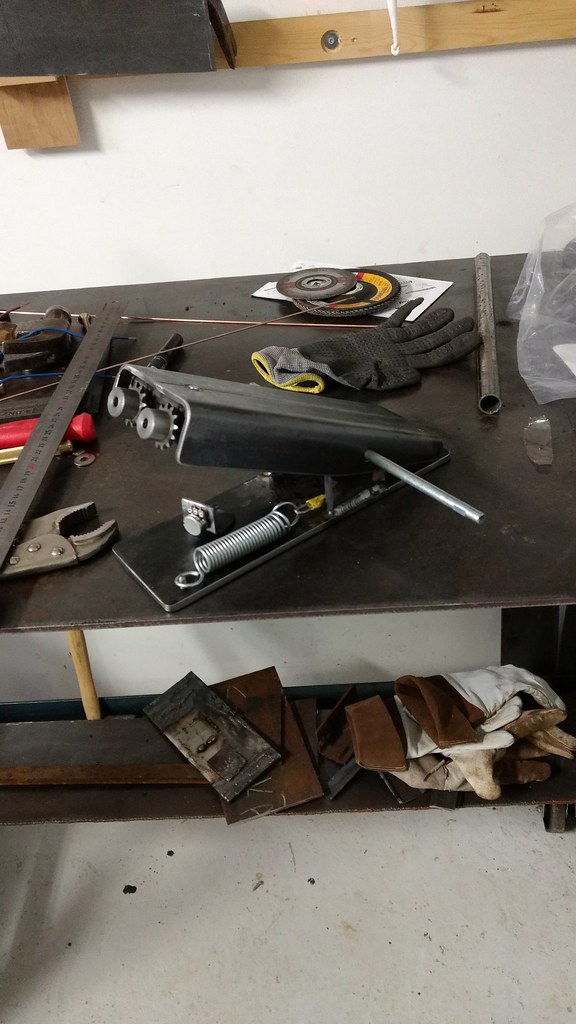
I then made the circuit I had designed in kicad:

Electronics installed:
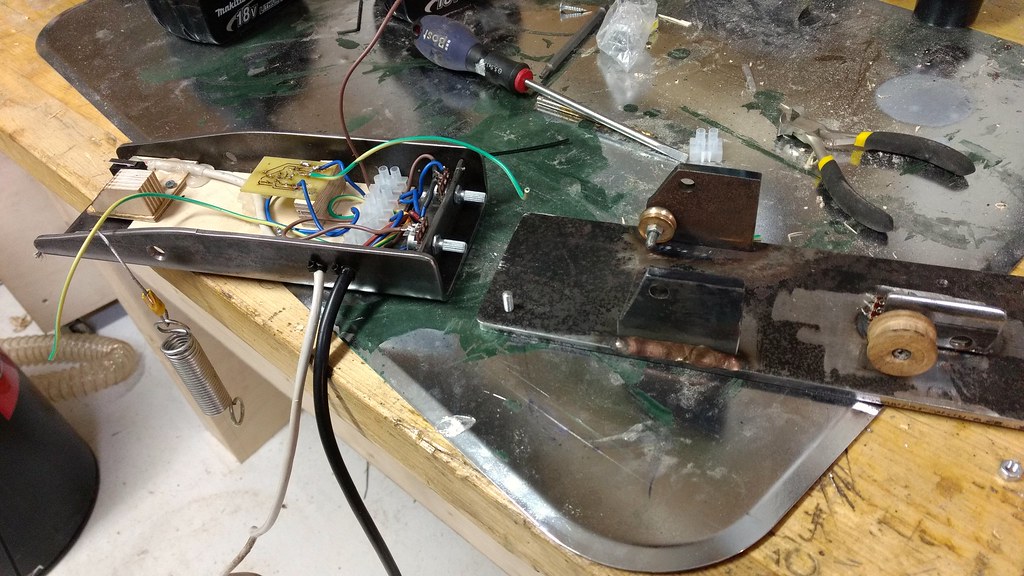
This is where I am now, not yet completely finished, I lack a 4-pin amphenol connector for the microswitch which has a separate connector, but the pedals current adjustment worked correctly when I tested it so all I need is that part (in the mail).
I might redesign it yet, it might make more sense to put the electronics and the min and max adjustment in a separate box on the welder itself and just have the switch and main pot in the pedal, it wold be easier to adjust that way instead of reaching down the front of the pedal.
I've really learned a lot from doing this project, about electronics, PCB design and just how this whole setup works, if it breaks I know I can fix it myself.