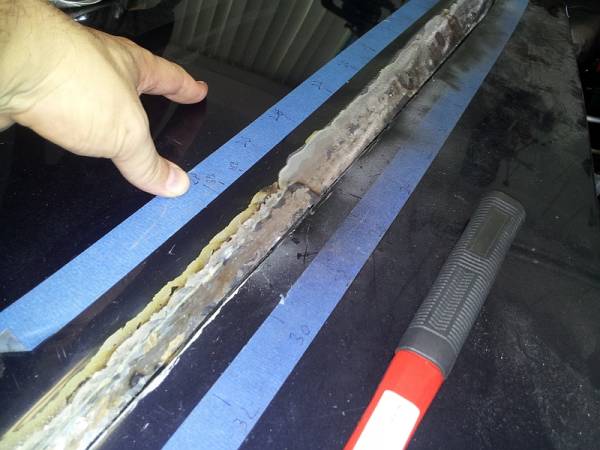
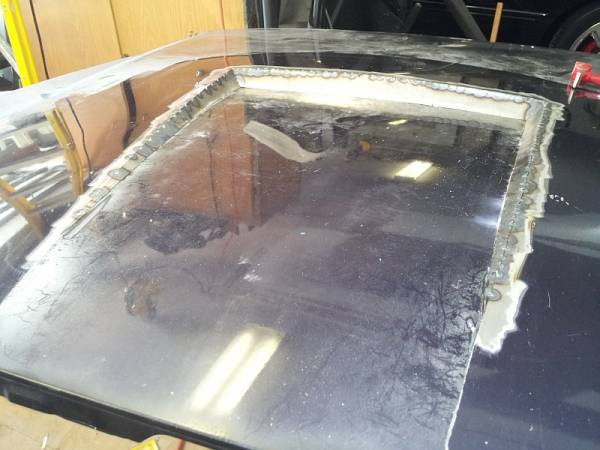
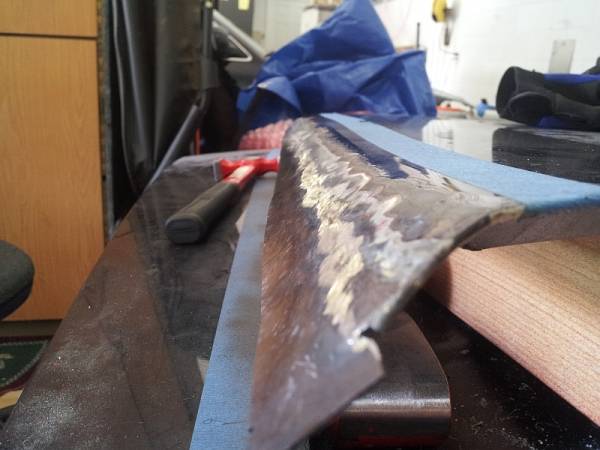
I've got to completely disagree with that. However, there might be someone out there that it might work for. I myself consider tig my strong suit yet I bought a mig specifically for auto body. Doing patch panels on rusty vehicles up here in the North Country, Tig or O/A pretty much burns away whatever you are trying to weld the new patch panel to. In a different environment where you don't have the rust I am sure tig would work. Tig would also be a little softer weld and easier to blend into the other metal. Still more heat and distortion and even more with O/A.frederick flintstone wrote:this is where ALL the restoration shows get it ALL wrong.
I truly hate that they ALL show people MIG welding sheet metal.
fusion TIG welding or even very, very low heat oxy/fuel welding is a far better way to weld auto body sheet metal.
if you TRY do any real metal working to a MIG joint or a TIG weld with filler wire you will be fighting the extra metal.
doing it right is truly an art form that takes practice and very few can do it right.
I would tend to agree and disagree a little.Otto Nobedder wrote:I think most "auto body" people have forgotten the definition of the word, "planish."
Look it up, learn to do it, and the debate goes away.
That extra metal can be used to your advantage, and it doesn't matter which process deposited it.
Steve S