The obligatory intro post.
Just bought a cheap HYL 200P AC/DC digital TIG and trying to learn to use it (mostly aluminum). Watched many of the video on youtube and decided I should sign up here for when (not if) I have questions. Building a cart for my welder as the first project, and making it from aluminum angle. Have about 1/3 of the pieces cut and should be welding Tuesday or Wednesday (I hope).
So why a HYL welder? Simply money, don't have enough for a Fronius. This HYL was $400 shipped so I'm in for under $1000 including the metal for the cart, a bunch of filler, some tungstens, and a tungsten grinder for my Hitachi motor tool (fits dremel tools and a bunch of others). I'm sure I left out some accessories that I had to upgrade from my cheapo Hobart 100v fluxcore welder, but you get the idea. Needed to be able to weld aluminum, it's been holding me back on some of the parts that I machine and some of the other things I want to create, so it was finally time to make the next step and the cheap welder was the gateway. It actually seems to have some pretty nice features, especially considering the price. Just hope it lasts long enough to justify the money. Only made some really horrible test welds in 2T mode so far. Then I built a trigger amperage control to hopefully prevent some of the over temp. problems I was having. My biggest problem is lack of experience, and really only one way to gain that, so here I go...
Welcome to the community! Tell us about yourself, your welding interests, skills, specialties, equipment, etc.
- tungstendipper
-
Weldmonger
-
Posts:
-
Joined:Sun Nov 19, 2017 10:09 am
Welcome.
Looking good! Don't forget to clean that ally!
Looking good! Don't forget to clean that ally!
Lincoln MP 210, Lincoln Square Wave 200,
Everlast 210 EXT
Thermal Dynamics 25 Plasma cutter
" Anything that carries your livelihood wants to be welded so that Thor can’t break it."
CJ737
Everlast 210 EXT
Thermal Dynamics 25 Plasma cutter
" Anything that carries your livelihood wants to be welded so that Thor can’t break it."
CJ737
Apparently not clean enough, missing is the black crud on this mess:
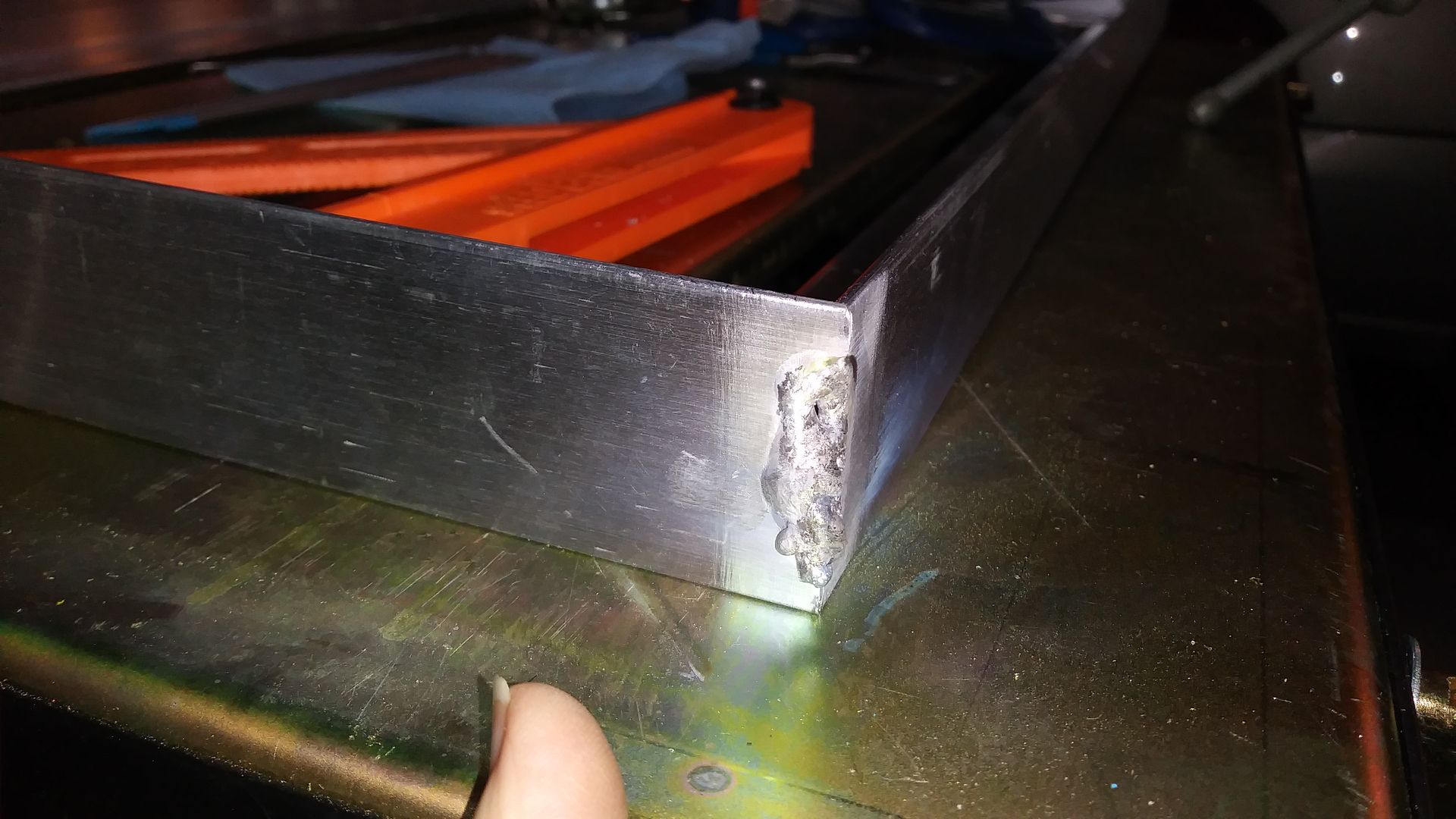
Also the number of electrodes I used last night to just tack 16 spots (one still in the torch), got some cleanup to do for the next phase of construction.
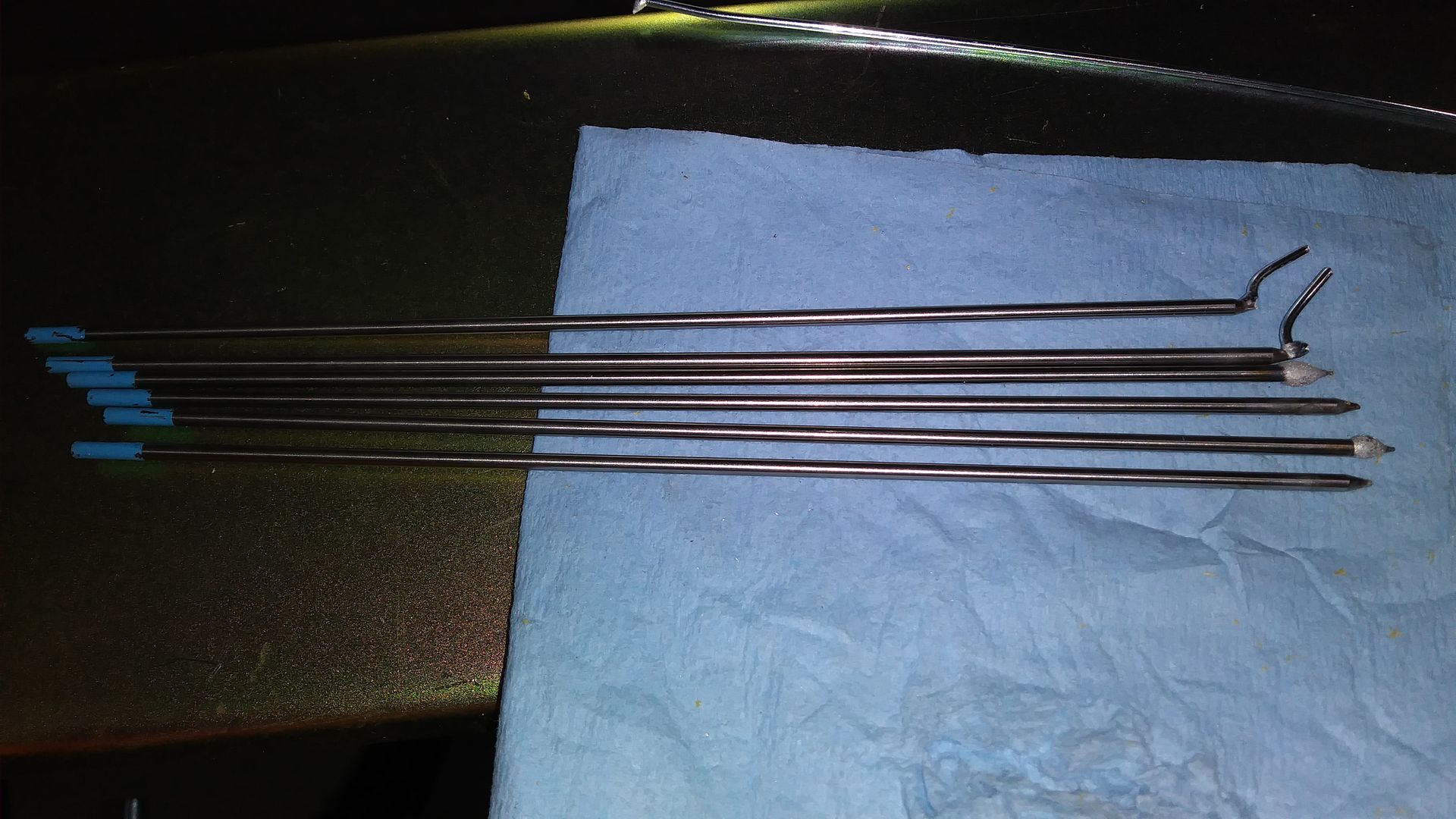
Not sure why the images won't size to fit the window, if you click one of these it will go to photobucket for the full size image.
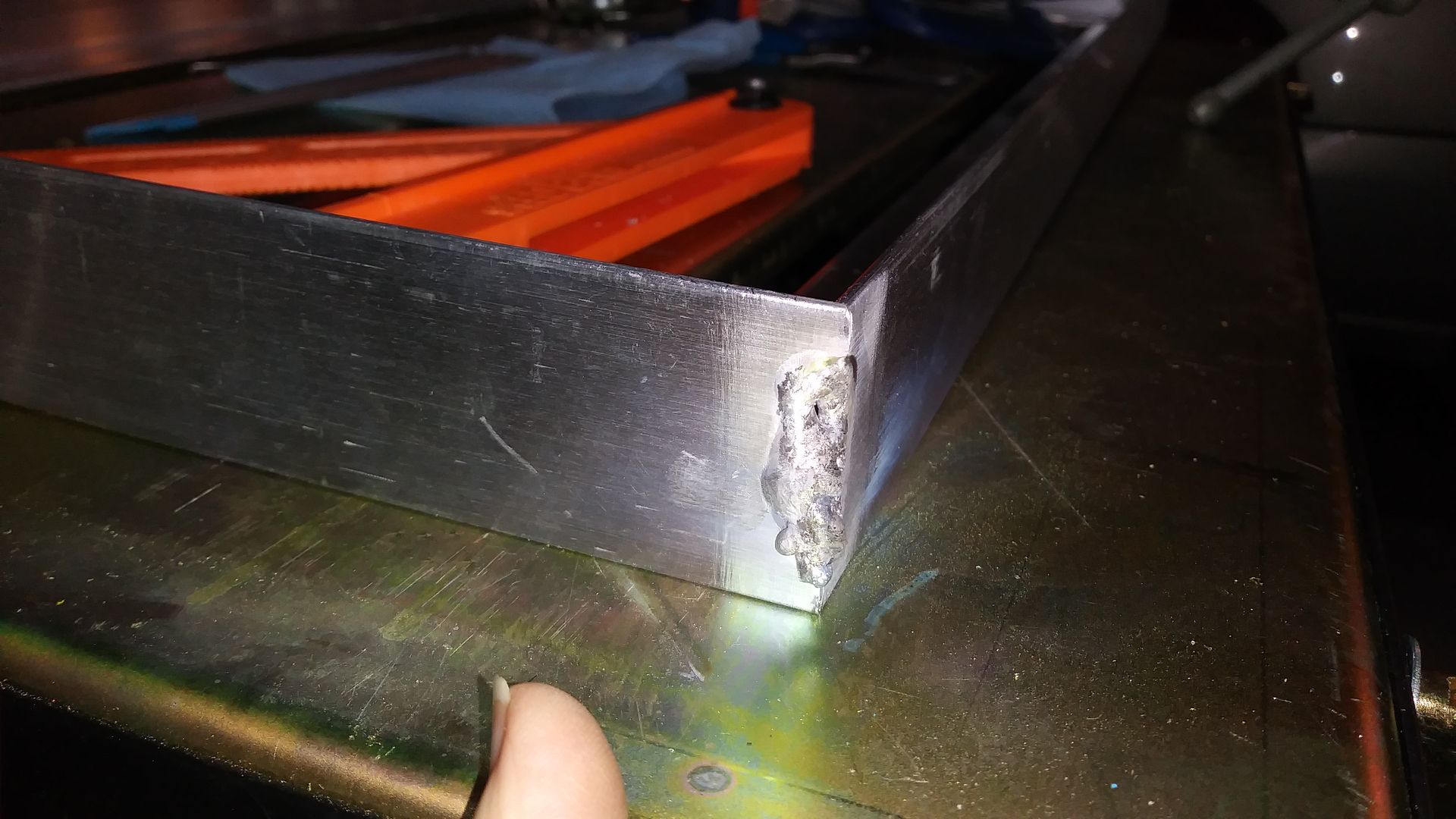
Also the number of electrodes I used last night to just tack 16 spots (one still in the torch), got some cleanup to do for the next phase of construction.
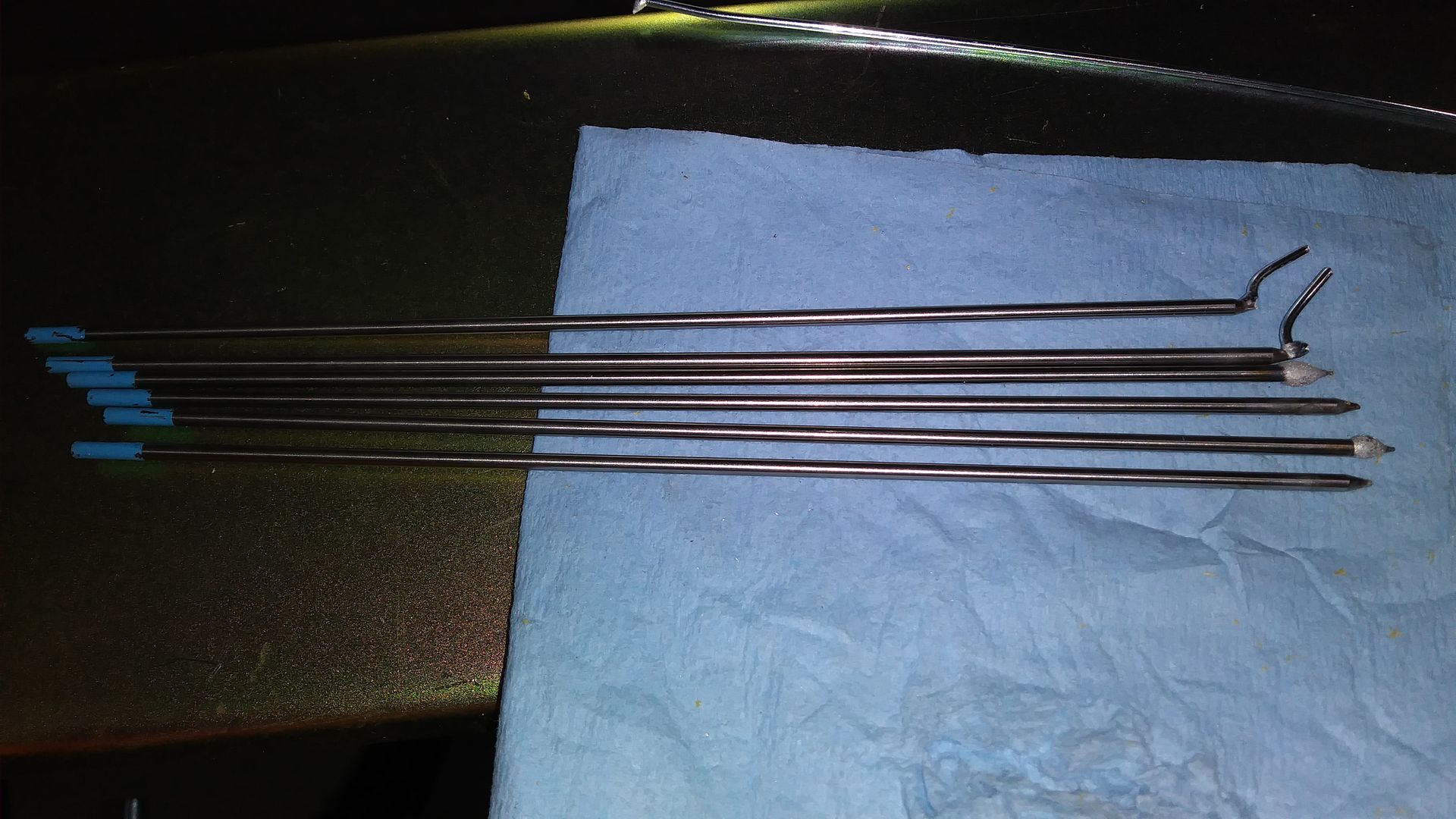
Not sure why the images won't size to fit the window, if you click one of these it will go to photobucket for the full size image.
- tungstendipper
-
Weldmonger
-
Posts:
-
Joined:Sun Nov 19, 2017 10:09 am
You're doing what my name implies... dipping your tungsten. Keep your tungsten above the puddle at about the diameter of the tungsten you're using.
Here a video you need to watch: https://www.youtube.com/watch?v=XSGnCf0Bcto
Here a video you need to watch: https://www.youtube.com/watch?v=XSGnCf0Bcto
Lincoln MP 210, Lincoln Square Wave 200,
Everlast 210 EXT
Thermal Dynamics 25 Plasma cutter
" Anything that carries your livelihood wants to be welded so that Thor can’t break it."
CJ737
Everlast 210 EXT
Thermal Dynamics 25 Plasma cutter
" Anything that carries your livelihood wants to be welded so that Thor can’t break it."
CJ737
- tungstendipper
-
Weldmonger
-
Posts:
-
Joined:Sun Nov 19, 2017 10:09 am
Here's a great video on practicing aluminum welding:
Lincoln MP 210, Lincoln Square Wave 200,
Everlast 210 EXT
Thermal Dynamics 25 Plasma cutter
" Anything that carries your livelihood wants to be welded so that Thor can’t break it."
CJ737
Everlast 210 EXT
Thermal Dynamics 25 Plasma cutter
" Anything that carries your livelihood wants to be welded so that Thor can’t break it."
CJ737
Actually, that first corner picture is the result of too low amps. You applied heat, but not enough to get the puddle to establish before the interior of the ally melted away.tungstendipper wrote:You're doing what my name implies... dipping your tungsten. Keep your tungsten above the puddle at about the diameter of the tungsten you're using.
Here a video you need to watch: https://www.youtube.com/watch?v=XSGnCf0Bcto
Crank up your amps, then, taper off with the pedal before you blow it out. You might find it easier to weld “flat” than vertically in case yuor piece was setup in that orientation.
The welder continues to work better than I do, got the cart mostly tacked together but had one major problem. I was much better with cleaning everything including the filler, and on more wire brush (stainless) to break up the oxide, but one joint really got me. I'm thinking that some of these are getting contaminated from the galvanized surface of the cheapo welding table, is this likely? Thinking I need a big sheet of aluminum to put down.
As you can see, some of my tacks are decent for my skill level, and yes I did turn up the heat by about 10 amps and things went a little better. Think I'm going to turn up the cleaning action another 5% and maybe add a few more amps to start when I'm actually running the welds. Again click on the pictures to get the full image, sorry.
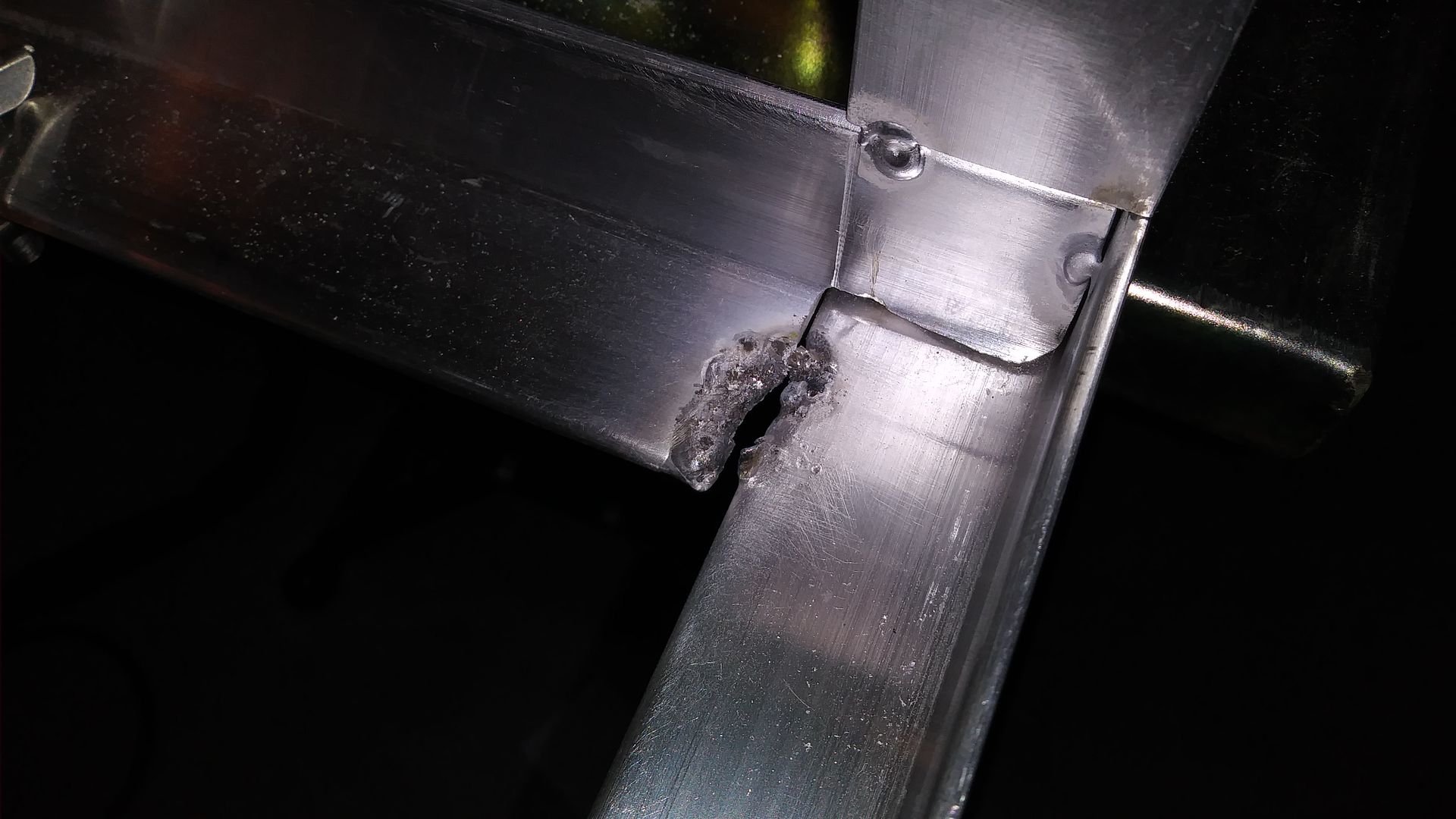
Ugly duckling cart frame:
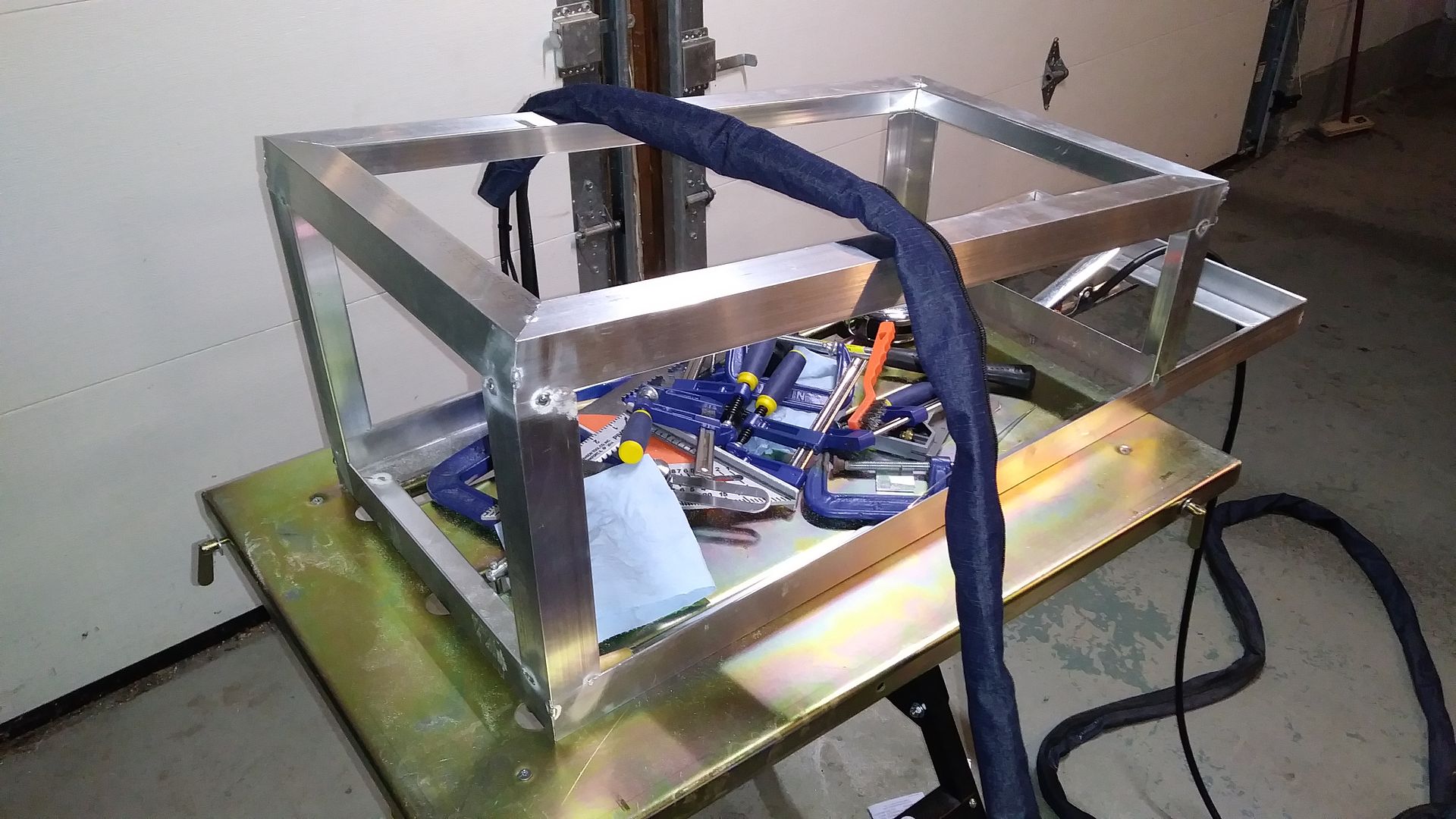
As you can see, some of my tacks are decent for my skill level, and yes I did turn up the heat by about 10 amps and things went a little better. Think I'm going to turn up the cleaning action another 5% and maybe add a few more amps to start when I'm actually running the welds. Again click on the pictures to get the full image, sorry.
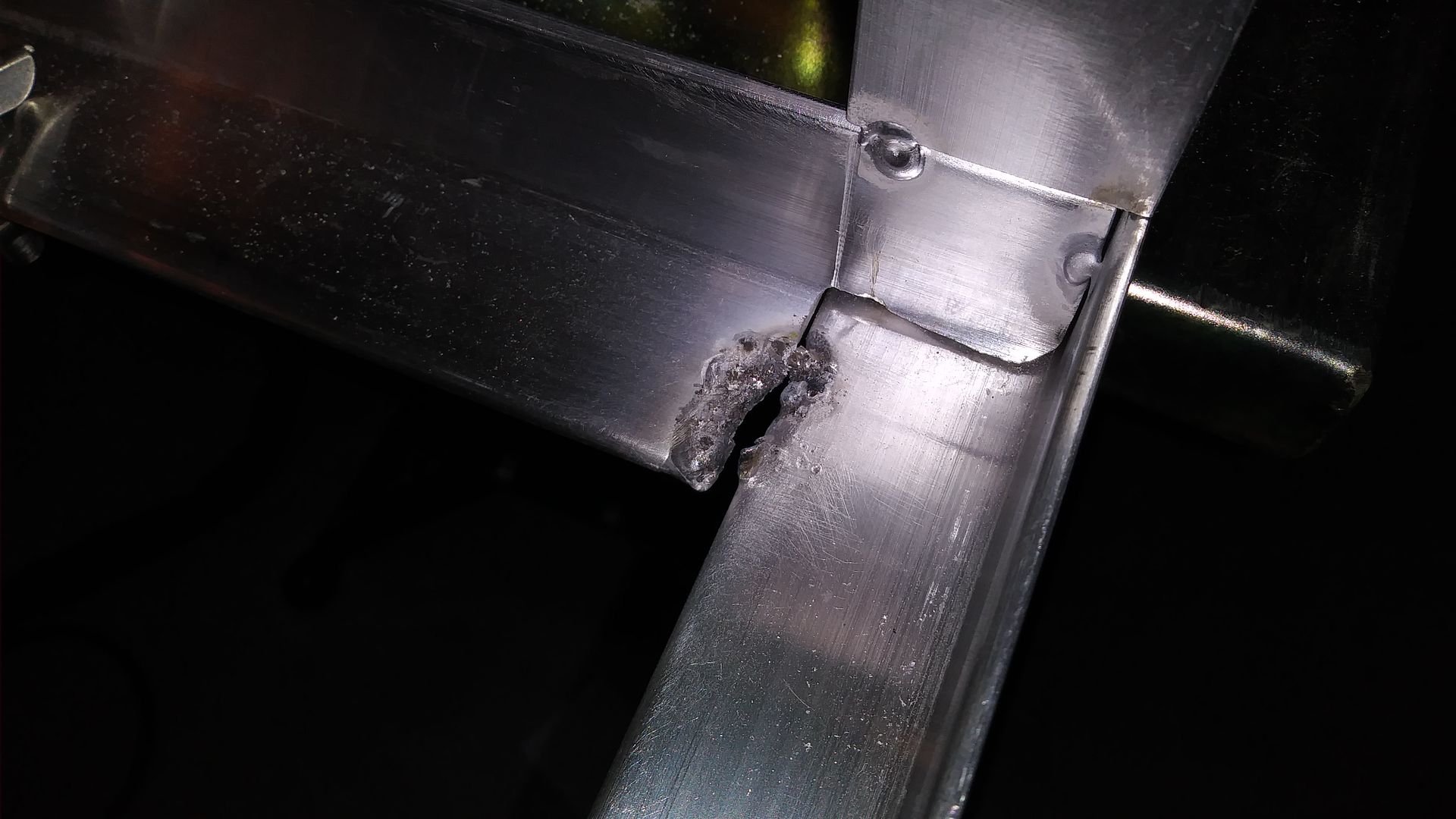
Ugly duckling cart frame:
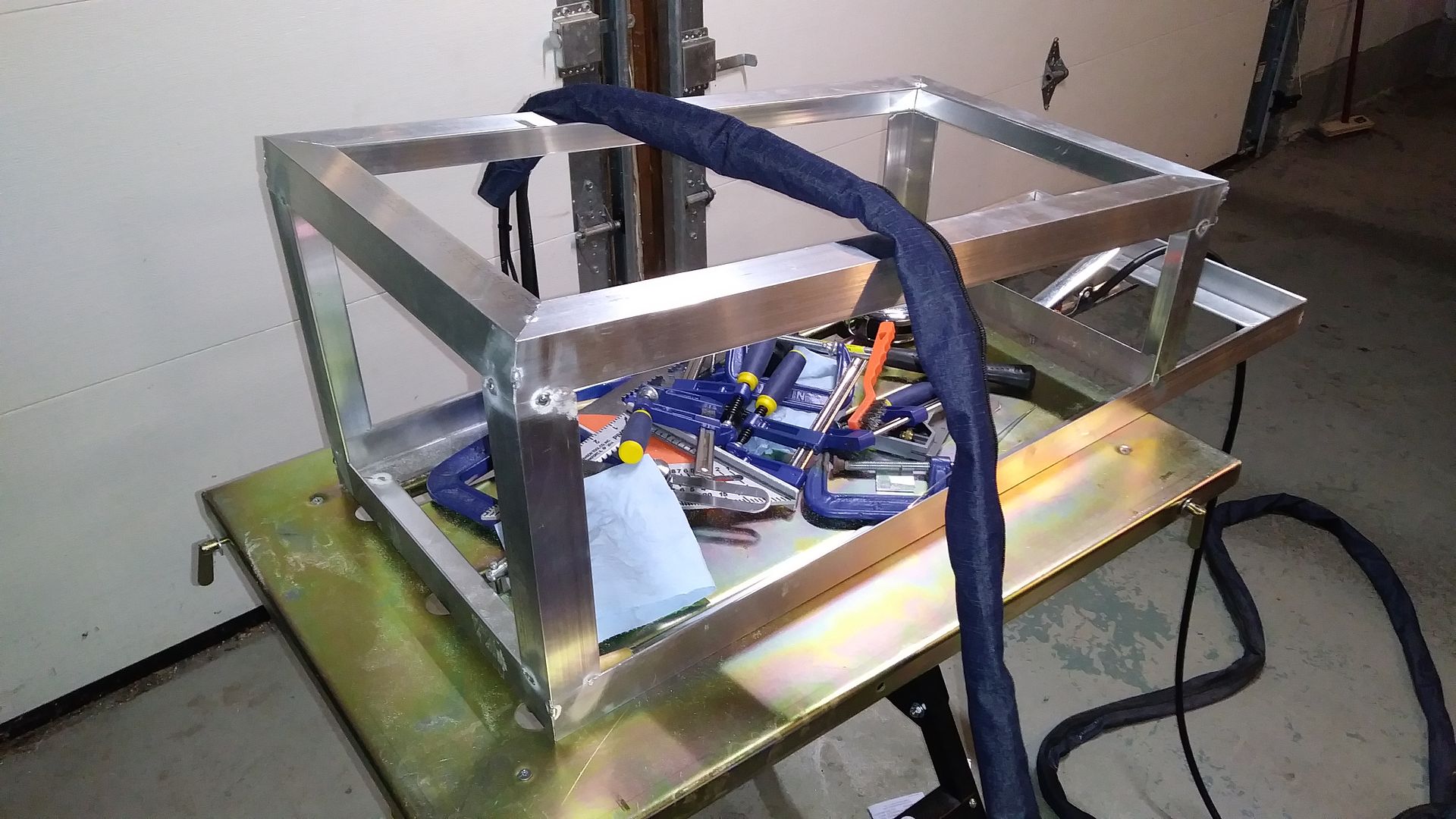
You definitely don’t want to weld near galvanized metal. The fumes are lethal.
I suspect that joint is still the same original problem, heat control. When you weld a butt joint, establish the arc on one side, then quickly whip across to get the other side puddles up. This requires proper arc length. If you point directly into the middle of the joint, any gap will burn away before getting a puddle. High heat, very quickly, filler, taper off the heat. That will help eliminate the craters you’re getting in some of your tacks.
I suspect that joint is still the same original problem, heat control. When you weld a butt joint, establish the arc on one side, then quickly whip across to get the other side puddles up. This requires proper arc length. If you point directly into the middle of the joint, any gap will burn away before getting a puddle. High heat, very quickly, filler, taper off the heat. That will help eliminate the craters you’re getting in some of your tacks.
- weldin mike 27
-
Weldmonger
-
Posts:
-
Joined:Fri Apr 01, 2011 10:59 pm
-
Location:Australia; Victoria
I can't be sure, but I think you might have anodised aluminium angle. That has an thicker oxide coating that is applied by an electric process. It kind of welds like the metal underneath is melting but the surface is still solid. (think of a melted block of chocolate inside the aluminium foil) its still weldable, (very, in fact) but you just need to adjust the technique. Not my forte, so I won't go into it too much.
So they welder is broken. Every time I turn the power switch I hear the gas solenoid trigger, then my preflow timer expires and it tries to start an arc, then errors out. Waiting for parts that probably won't fix it, but have to work in the order they tell me.
But what this allowed me to find was that my flowmeter is JUNK! It will flow at about 15cfh while I set it up, but depending on the amount of time between welds, it may come back the next time with the set 15cfh, or only about 5cfh and I get a purple tungsten on the bad welds. I think this might be from gas. All these bad welds have in common:
hard starts
angry tone to the buzz
bad welds with black crud
Does that sound like poor gas coverage?
Going to tear into the flowmeter and see if there is something I can fix, and then probably buy a "better" one. The knob on the top of the flow meter feels wrong and is very hard to get the ball floating at anything less than 15cfh. I'm expecting to find a rotten O ring inside, or some other garbage getting in the way.
But what this allowed me to find was that my flowmeter is JUNK! It will flow at about 15cfh while I set it up, but depending on the amount of time between welds, it may come back the next time with the set 15cfh, or only about 5cfh and I get a purple tungsten on the bad welds. I think this might be from gas. All these bad welds have in common:
hard starts
angry tone to the buzz
bad welds with black crud
Does that sound like poor gas coverage?
Going to tear into the flowmeter and see if there is something I can fix, and then probably buy a "better" one. The knob on the top of the flow meter feels wrong and is very hard to get the ball floating at anything less than 15cfh. I'm expecting to find a rotten O ring inside, or some other garbage getting in the way.
Until you resolve your gas issue, it’s impossible to troubleshoot other possible contributing factors.
Jody sells a good quality flow meter on his website
https://weldmongerstore.com/collections ... -with-hose
Once you get gas and your machine working properly, you will probably find it easier to get stable, quality beads
Jody sells a good quality flow meter on his website
https://weldmongerstore.com/collections ... -with-hose
Once you get gas and your machine working properly, you will probably find it easier to get stable, quality beads

Took the pressure adjust apart to clean it out, this meter is just garbage, thanks for the recommendation on a replacement. Got 10% off and free shipping.
Also this meter is metric, so I was going between about 30-40 cfh and about 6 cfh when it was not right. Uggg.
Down to half a tank and not much work done. Hope I can get this welder working again soon.
Also this meter is metric, so I was going between about 30-40 cfh and about 6 cfh when it was not right. Uggg.
Down to half a tank and not much work done. Hope I can get this welder working again soon.
Got the new flow meter, haven't taken it out of the package yet. Thanks to Jody for getting it to me fast (been sitting there for a while now).
Got the part they sent, didn't fix the welder. Trying to coordinate with them to troubleshoot which is going to be difficult. Been dealing with lawyers, insurance, doctors and just feeling generally defeated after a car accident last Monday (the day the parts arrived). Almost don't even care anymore when compared to what I need to work on to just get a new car and the money I'm going to lose. Would be less aggravating to just order a second of the same welder and hope for better luck at this point. At least I might have parts to swap between them to make one of them work.
Got the part they sent, didn't fix the welder. Trying to coordinate with them to troubleshoot which is going to be difficult. Been dealing with lawyers, insurance, doctors and just feeling generally defeated after a car accident last Monday (the day the parts arrived). Almost don't even care anymore when compared to what I need to work on to just get a new car and the money I'm going to lose. Would be less aggravating to just order a second of the same welder and hope for better luck at this point. At least I might have parts to swap between them to make one of them work.
The Hyl welder is done! The importer has shut down their website, no additional product to sell, not answering anymore... Basically just stole my money and ran away. You can look up my review on Amazon, it's the only one with video for the Hyl AC tig welder.
Got a Primeweld Tig225x that I need to finish setting up, been tied up with other projects and just getting around to cleaning up some working space. Hope this works better.
If anyone can help me figure out which off the shelf welder control boards I can use to make the Hyl function again, that would be great. Pretty sure they just used off the shelf boards.
Got a Primeweld Tig225x that I need to finish setting up, been tied up with other projects and just getting around to cleaning up some working space. Hope this works better.
If anyone can help me figure out which off the shelf welder control boards I can use to make the Hyl function again, that would be great. Pretty sure they just used off the shelf boards.
It's not worth any more of your time, or precious money to try and fix a cheap inverter. You would have to have a full electrical diagram from them, documentation on the circuitry, and then hope your diagnosis is correct. Scrap it.Greg_E wrote:The Hyl welder is done! The importer has shut down their website, no additional product to sell, not answering anymore... Basically just stole my money and ran away. You can look up my review on Amazon, it's the only one with video for the Hyl AC tig welder.
If anyone can help me figure out which off the shelf welder control boards I can use to make the Hyl function again, that would be great. Pretty sure they just used off the shelf boards.
The PrimeWeld while being a very inexpensive unit, has gotten some very decent reviews. Your luck may be coming up.
Here's a moral of this regrettable story: Buy quality products, spend your money only once. Otherwise, you'll spend more in the long run. As it is, you're almost $1400 in so far, and for that money you could have bought a Lincoln SquareWave.
Fingers crossed for you with the PrimeWeld.

Sorry to say but yours is the textbook case of why one should avoid cheap products of any kind. What’s the saying? Buy once, cry once? I am not rich enough to buy cheap stuff?
A quality torch, pedal, and regulator already get you to $400. Then a newer generation helmet, jacket and quality TIG gloves. These are prerequisites. Otherwise you’ll keep bleeding money to upgrade from trash into the decent tier, instead of welding.
Hope everything turns out great for you.
Sent from my iPhone using Tapatalk
A quality torch, pedal, and regulator already get you to $400. Then a newer generation helmet, jacket and quality TIG gloves. These are prerequisites. Otherwise you’ll keep bleeding money to upgrade from trash into the decent tier, instead of welding.
Hope everything turns out great for you.
Sent from my iPhone using Tapatalk
HTP Invertig 221H w/ Arctic Chill cooler and CK20 torch
Lincoln MP210 -- SOLD
Optrel Crystal 2.0
Lincoln MP210 -- SOLD
Optrel Crystal 2.0
Return to “Member Introductions”
Jump to
- Introductions & How to Use the Forum
- ↳ Welcome!
- ↳ Member Introductions
- ↳ How to Use the Forum
- ↳ Moderator Applications
- Welding Discussion
- ↳ Metal Cutting
- ↳ Tig Welding - Tig Welding Aluminum - Tig Welding Techniques - Aluminum Tig Welding
- ↳ Mig and Flux Core - gas metal arc welding & flux cored arc welding
- ↳ Stick Welding/Arc Welding - Shielded Metal Arc Welding
- ↳ Welding Forum General Shop Talk
- ↳ Welding Certification - Stick/Arc Welding, Tig Welding, Mig Welding Certification tests - Welding Tests of all kinds
- ↳ Welding Projects - Welding project Ideas - Welding project plans
- ↳ Product Reviews
- ↳ Fuel Gas Heating
- Welding Tips & Tricks
- ↳ Video Discussion
- ↳ Wish List
- Announcements & Feedback
- ↳ Forum News
- ↳ Suggestions, Feedback and Support
- Welding Marketplace
- ↳ Welding Jobs - Industrial Welding Jobs - Pipe Welding Jobs - Tig Welding Jobs
- ↳ Classifieds - Buy, Sell, Trade Used Welding Equipment
- Welding Resources
- ↳ Tradeshows, Seminars and Events
- ↳ The Welding Library
- ↳ Education Opportunities