Hi everyone!
My name is Chris and I am a welding novice. I like to design and build things, but where structural integrity is required I get someone else to do it for me. However, I want to change that. Starting with welding light steel, I would like to move to chromoly and maybe one day learn to TIG aluminium.
So I went out and bought an $80 buzz box AC arc welder and a packet of electrodes. The most common rod in Australia is a 6013, and even the pro welding suppliers will recommend it. Anyway, I have been mucking around with a few projects, the latest of which is a hoist for my motorcycle. I want it to be able to hold about 100 kg or so; just the front wheel off the ground sort of thing. I found a bunch of galvanised pipe and some 2 mm square tube and got to work. I downloaded a tube miter program - brilliant invention!
So far so good, but I have been noticing my welds are taking in significant slag inclusions. It seems the angle of the electrode has a fair bit to to with it. My welds are hugely improved on when I first started scratching around, but I can't seem to shake these slaggy wormholes. This was one of my best welds - I found that I could get a good burn going for about 8 mm, then I would have to lift up and wait for it to cool a bit before going again. If I tried to do it in one pass the tube would blow out.
Stopping and starting didn't always leave inclusions, and this had a bit to do with the electrode angle - not too steep but not laying down either. I'm drawing about 90-100 amps (it's not real reliable) and 40 V at open circuit (it sags down to about 24 V while welding). Electrodes are 2.5 mm, but I found little difference between these and 3.2 mm rods. Both are 6013s.
Any advice is much appreciated!
Cheers,
Chris
Stick Welding Tips, Certification tests, machines, projects
- Otto Nobedder
-
Weldmonger
-
Posts:
-
Joined:Thu Jan 06, 2011 11:40 pm
-
Location:Near New Orleans
You're doing remarkably well for an $80 buzz-box with an open-circuit voltage that low.
Part of the problem is that you're welding on galvanized. Beware the fumes. They're not really harmful, but in excess, they'll make you feel like hell for about a day.
Either get away from galvanized, or grind every bit off anywhere near your weld, and I think you'll see an improvement.
On material that thin, it's not unusual (escpecially with a low-end machine without good current/voltage control) to have to stop and start to keep from blowing out the pipe. To avoid inclusions in your stops and starts, use a wire-wheel in a grinder on the slag before you start again.
Steve S
Part of the problem is that you're welding on galvanized. Beware the fumes. They're not really harmful, but in excess, they'll make you feel like hell for about a day.
Either get away from galvanized, or grind every bit off anywhere near your weld, and I think you'll see an improvement.
On material that thin, it's not unusual (escpecially with a low-end machine without good current/voltage control) to have to stop and start to keep from blowing out the pipe. To avoid inclusions in your stops and starts, use a wire-wheel in a grinder on the slag before you start again.
Steve S
jonescg
- jonescg
-
New Member
-
Posts:
-
Joined:Mon Oct 21, 2013 9:31 am
-
Location:Perth, Western Australia
Thanks Steve - I must confess I'm not a complete newcomer to welding, but I am a newcomer to 'trying to do it properly this time'. I have built a welding bench from 6 mm steel so I can clamp stuff to it to hold it steady and in place. It also soaks some heat out of the weld. Welding big stuff is easy - the table came together pretty well with high amps and a slow travel rate, but the thin stuff is where I need practice.
I could go out and buy a MIG but then I would be skipping the fundamentals of welding metal. Plus the stick is just so damn easy to set up and go.
Agree on the galv - I usually grind it all off but the welds will still have inclusions. Maybe part of this is me moving too fast in fear of blowing through the pipe, and the majority is technique I suspect. Getting the welder set up could be a factor, but I found myself going back to the same old 40 V / 80-100 A range. The welder has a 70 V and a 40 V setting, for low (60-80 A) and high (80-130 A) currents, respectively.
Anyway, practice makes the welder. I need more projects before I can move on 
I could go out and buy a MIG but then I would be skipping the fundamentals of welding metal. Plus the stick is just so damn easy to set up and go.
Agree on the galv - I usually grind it all off but the welds will still have inclusions. Maybe part of this is me moving too fast in fear of blowing through the pipe, and the majority is technique I suspect. Getting the welder set up could be a factor, but I found myself going back to the same old 40 V / 80-100 A range. The welder has a 70 V and a 40 V setting, for low (60-80 A) and high (80-130 A) currents, respectively.
- Welder setup.jpg (185.21 KiB) Viewed 2883 times
- welding and shed 001.jpg (245.09 KiB) Viewed 2883 times
- Mitred weld.jpg (235.59 KiB) Viewed 2883 times

Well typical problem when using 6013 welding electrodes, worm holes and at times slag inclusion in the welds plus of course a low penetrating electrode. Used to be my problem before but sure bit the hell out of it by just continuous/constant practice on several materials, thick or thin. Have you tried using 1/16" or 3/32" 6013 rods on thin wall metals ? Them rods are more forgiving on thin walls specially when using a DC weld machine. You'd see the big difference.
If you have some time try watching these videos, you might be able to pickup some tips that will greatly help you in you weld applications. There is another one made by Jody, I just can't find it just now, but its a very nice and informative video discussing on different characteristics of different welding electrodes and how they differ from each applications plus it also says why Jody dislikes the 6013 rods.
See if you can chance upon that video on YouTube.
http://www.youtube.com/watch?v=Z2B36psoNQ4
http://www.youtube.com/watch?v=ILUJlcFkkm8

If you have some time try watching these videos, you might be able to pickup some tips that will greatly help you in you weld applications. There is another one made by Jody, I just can't find it just now, but its a very nice and informative video discussing on different characteristics of different welding electrodes and how they differ from each applications plus it also says why Jody dislikes the 6013 rods.

http://www.youtube.com/watch?v=Z2B36psoNQ4
http://www.youtube.com/watch?v=ILUJlcFkkm8
jonescg
- jonescg
-
New Member
-
Posts:
-
Joined:Mon Oct 21, 2013 9:31 am
-
Location:Perth, Western Australia
The 48 mm pipe was welded with 3.2 mm rods. I tried 2.5 mm rods and to be honest they felt exactly the same, although they had less of a propensity to blow holes. I'd say I will continue using the 2.5 mm rods on thin tube (even down to 1.6 mm wall thickness) but 3.2 mm rods for big stuff.
I suspect if my electrode angle was a bit steeper I might avoid some of these inclusions, but surface preparation, having a nice tight joint to weld and getting the angle right will lead to the results I'm after.
There's a lot of bagging of 6013s out there, but it is pretty much the only electrode you can get your hands on here.
I suspect if my electrode angle was a bit steeper I might avoid some of these inclusions, but surface preparation, having a nice tight joint to weld and getting the angle right will lead to the results I'm after.
There's a lot of bagging of 6013s out there, but it is pretty much the only electrode you can get your hands on here.
- weldin mike 27
-
Weldmonger
-
Posts:
-
Joined:Fri Apr 01, 2011 10:59 pm
-
Location:Australia; Victoria
Hey Chris,
If you are from Perth, you hail from one of the greatest welding centres of the country. With some of the best, if not THE best tradesmen/women in the country, so you will be able to find any electrode you desire, if you have a look around. Any of the decent welding supplier (not bunnings) should help you, or drop into a workshop with a carton and see if they can give you a couple to try. Ausclad is one shop I know of that does awesome work.
Mick
If you are from Perth, you hail from one of the greatest welding centres of the country. With some of the best, if not THE best tradesmen/women in the country, so you will be able to find any electrode you desire, if you have a look around. Any of the decent welding supplier (not bunnings) should help you, or drop into a workshop with a carton and see if they can give you a couple to try. Ausclad is one shop I know of that does awesome work.
Mick
jonescg
- jonescg
-
New Member
-
Posts:
-
Joined:Mon Oct 21, 2013 9:31 am
-
Location:Perth, Western Australia
Hey Mick,
Yes, WA is the mining/oil/gas/engineering centre of the world right now. And if you need 1000 of anything made you're in luck. But if you want a one-off you are a bit out of luck. Hence I need to learn how to weld myself.
I might share a bit more of what I'm into.
I am a devotee and evangalist for electric vehicles. All kinds, but especially motorbikes. I like to build and race electric motorcycles. OK, I haven't built or raced many, but this is what gets me out of bed in the morning. If you want to know where all of my money goes, have a read of this thread: http://forums.aeva.asn.au/voltronevo-jo ... c3553.html
I am also working on an electric Honda CRX conversion, but that will be well after the bike gets built.
Since this is a welding forum, I might share a couple of pictures of my bike. I got Randy Ilg from Framecrafters to build it for me. I designed the basic shape and layout of the frame and they did the rest. Man, these guys can weld. TIG I assume, given it's Chromoly.
Sadly, no-one in Australia was keen to help with the welding of the frame. In the end I was very happy to get Framecrafters to do it as they have a long history of building beautiful, fast racing machines. They are explicitly NOT chopper guys; all they do is build race bike frames, which was exactly what I wanted. And for a bargain price too IMO.
The hoist I have been building is to lift the 85 kg, 9 kilowatt hour battery pack from the bike.
I hope to have some offshore work coming up in the next few weeks (Subsea services, ROVs and such) which will go a long way towards paying for this stuff.
Yes, WA is the mining/oil/gas/engineering centre of the world right now. And if you need 1000 of anything made you're in luck. But if you want a one-off you are a bit out of luck. Hence I need to learn how to weld myself.
I might share a bit more of what I'm into.
I am a devotee and evangalist for electric vehicles. All kinds, but especially motorbikes. I like to build and race electric motorcycles. OK, I haven't built or raced many, but this is what gets me out of bed in the morning. If you want to know where all of my money goes, have a read of this thread: http://forums.aeva.asn.au/voltronevo-jo ... c3553.html
I am also working on an electric Honda CRX conversion, but that will be well after the bike gets built.
Since this is a welding forum, I might share a couple of pictures of my bike. I got Randy Ilg from Framecrafters to build it for me. I designed the basic shape and layout of the frame and they did the rest. Man, these guys can weld. TIG I assume, given it's Chromoly.
- Voltron Evo in the house 011.jpg (108.3 KiB) Viewed 2816 times
- Voltron Evo in the house 012.jpg (146.15 KiB) Viewed 2816 times
The hoist I have been building is to lift the 85 kg, 9 kilowatt hour battery pack from the bike.
I hope to have some offshore work coming up in the next few weeks (Subsea services, ROVs and such) which will go a long way towards paying for this stuff.
- Otto Nobedder
-
Weldmonger
-
Posts:
-
Joined:Thu Jan 06, 2011 11:40 pm
-
Location:Near New Orleans
I hate to tell you this, but I think they MIGged your chromoly. Those are some sad looking welds for some very expensive steel, and TIG does not leave spatter.
It looks like they pulsed it, with overlapping spot welds.
Sorry to be the bearer of bad news, but I'd both be angry, and afraid to ride the bike on anything less than a smooth flat surface.
I'll dig, and show you a pic off what that SHOULD look like, and you'll see what I mean.
Check the bottom half of this page:
http://forum.weldingtipsandtricks.com/v ... &start=150
These welds have not been cleaned yet.
That's what chromoly should look like, and it's not perfect by a long shot.
Steve S
It looks like they pulsed it, with overlapping spot welds.
Sorry to be the bearer of bad news, but I'd both be angry, and afraid to ride the bike on anything less than a smooth flat surface.
I'll dig, and show you a pic off what that SHOULD look like, and you'll see what I mean.
Check the bottom half of this page:
http://forum.weldingtipsandtricks.com/v ... &start=150
These welds have not been cleaned yet.
That's what chromoly should look like, and it's not perfect by a long shot.
Steve S
jonescg
- jonescg
-
New Member
-
Posts:
-
Joined:Mon Oct 21, 2013 9:31 am
-
Location:Perth, Western Australia


Good news is, none of their frames have ever suffered a cracked weld in 24 years. Oh, and it was definitely TIG'd. It's infinitely better than anything I've seen done with a MIG.
Oh well each to their own. The frame hasn't been cleaned up yet, no. I'm waiting to have everything else installed and sized up before brushing and polishing the frame ready for painting. 4130 Chromoly isn't all that expensive compared to the rest of the bike...
Just hope I can shore up plenty of work in the future. Then the welding toybox might have to expand

- weldin mike 27
-
Weldmonger
-
Posts:
-
Joined:Fri Apr 01, 2011 10:59 pm
-
Location:Australia; Victoria
Hey,
If you are looking for someone to help you with getting a few welds done, im an admin on a facebook group for welding, with access to lots of people,who would jump at the chance to earn a bit of cash. PM me if you are interested.
Mick
If you are looking for someone to help you with getting a few welds done, im an admin on a facebook group for welding, with access to lots of people,who would jump at the chance to earn a bit of cash. PM me if you are interested.
Mick
coldman
- coldman
Hi, if you are in Perth, try any engineers supplies like Blackwoods (J. Blackwood & Son) and ask them for a pack of WIA AUSTARC 16 TC welding rods in 2.4mm, they will definately sell you one packet. These are good quality low hydrogen rods and will do a better job for you (no worm holes) than the 6013 rods you are using now. Ideally these rods should be dry out of an oven, but for low implication work like your 100kg hoist frame it is ok to use out of the packet. To restart a used rod, flick some flux off the end of the rod with a gloved finger to expose the wire end and it will restart ok. Keep control of your angle, no more than about 10 degrees, in some positions straight in is good too. Good luck!
If no luck with Blackwoods, ebay is the go.
If no luck with Blackwoods, ebay is the go.
jonescg
- jonescg
-
New Member
-
Posts:
-
Joined:Mon Oct 21, 2013 9:31 am
-
Location:Perth, Western Australia
Thanks guys! I picked up some 2.5 mm rods from Osborne Park Welding Supplies. CIG weld Satincraft or something. Still 6013s though. I found no difference between them and the Bunnings brand stuff, but my technique has everything to do with it
For little 25-30 mm welds, I cut the electrode in half - the shorter rod gives me more control. Any electrode which results in fewer slag inclusions I am keen to try.
I had a bit more of a play with the welder today. Flies are getting really bad in Perth now, so I ran out of patience by the afternoon. I was playing around with 1.6 mm square steel tube doing butt joints on the 6013 2.5 mm rods. Something I am finding is that unless I have the amps cranked right up to about 100 A or so, the weld penetration is really poor. Trouble is, blowing holes through light steel is a cinch at this current. The difference between good penetration and holes is about 1 second!
I did get some satisfactory welds, but only if I ran a hot electrode for about 15 mm and stopped, let it cool, chip the slag and brush, then while the tip is still hot, get back into it to finish the pass. I'd get an inclusion, but no holes at least. Will upload some pics in a minute.
Sure, a MIG would do the light stuff much better than stick, but stick is just so convenient!

I had a bit more of a play with the welder today. Flies are getting really bad in Perth now, so I ran out of patience by the afternoon. I was playing around with 1.6 mm square steel tube doing butt joints on the 6013 2.5 mm rods. Something I am finding is that unless I have the amps cranked right up to about 100 A or so, the weld penetration is really poor. Trouble is, blowing holes through light steel is a cinch at this current. The difference between good penetration and holes is about 1 second!
I did get some satisfactory welds, but only if I ran a hot electrode for about 15 mm and stopped, let it cool, chip the slag and brush, then while the tip is still hot, get back into it to finish the pass. I'd get an inclusion, but no holes at least. Will upload some pics in a minute.
- Thin tube stick welding 001.jpg (89.42 KiB) Viewed 2506 times
- Thin tube stick welding 002.jpg (79.59 KiB) Viewed 2506 times
- weldin mike 27
-
Weldmonger
-
Posts:
-
Joined:Fri Apr 01, 2011 10:59 pm
-
Location:Australia; Victoria
Hey,
You are going alright. Those electrodes go alright. One trick for 6013s is to hold at the start of your run for a second, even with a slight jiggle of your rod, this allows the pool to heat up, float the slag out and push it to the back of the pool. The way to know if you have a nice weld forming is the slag will form a definate line at the back of the pool. If you are getting inclusions, you wil see the slag swirling around all over., Another good way to learn is to crank the heat up, way past you would normally use, this will generally force the slag out and back, do it on thicker steel, so you dont just burn through.
Mick
You are going alright. Those electrodes go alright. One trick for 6013s is to hold at the start of your run for a second, even with a slight jiggle of your rod, this allows the pool to heat up, float the slag out and push it to the back of the pool. The way to know if you have a nice weld forming is the slag will form a definate line at the back of the pool. If you are getting inclusions, you wil see the slag swirling around all over., Another good way to learn is to crank the heat up, way past you would normally use, this will generally force the slag out and back, do it on thicker steel, so you dont just burn through.
Mick
jonescg
- jonescg
-
New Member
-
Posts:
-
Joined:Mon Oct 21, 2013 9:31 am
-
Location:Perth, Western Australia
Hi all,
I think I have worked out my stick welding issues and have progressed to a stage where I can call myself "competent". Not the prettiest of welds, but given the welder has three settings (off, on and 13 settings of useless) I seem to have worked it out.
I'm using 2.5 mm rods which are much better than 2 mm rods, even on thick stuff. They just don't get consumed so fast. I seem to have the best chance of a good weld if the metal is ground back to shiny steel and the joint is perfect or very close to it. Gaps and holes only tend to get bigger if you let them. Secondly, I seem to run pretty hot amperages. Any colder it wants to form inclusions and stick, and the penetration is woeful. The downside is I have to use my dabbing technique to weld 1.6 mm tube. It creates the odd inclusion, but the weld is infinitely stronger than anything I could do on lower current settings (and higher OCVs). Finally, welding 3 mm thick steel is a piece of piss. You just keep a steady hand and it sort of welds itself.
These 6013 rods are alright I think. For what I'm doing anyway.
I think I have worked out my stick welding issues and have progressed to a stage where I can call myself "competent". Not the prettiest of welds, but given the welder has three settings (off, on and 13 settings of useless) I seem to have worked it out.
I'm using 2.5 mm rods which are much better than 2 mm rods, even on thick stuff. They just don't get consumed so fast. I seem to have the best chance of a good weld if the metal is ground back to shiny steel and the joint is perfect or very close to it. Gaps and holes only tend to get bigger if you let them. Secondly, I seem to run pretty hot amperages. Any colder it wants to form inclusions and stick, and the penetration is woeful. The downside is I have to use my dabbing technique to weld 1.6 mm tube. It creates the odd inclusion, but the weld is infinitely stronger than anything I could do on lower current settings (and higher OCVs). Finally, welding 3 mm thick steel is a piece of piss. You just keep a steady hand and it sort of welds itself.
These 6013 rods are alright I think. For what I'm doing anyway.
- This is 1.6 mm steel tube. Stop-start technique leaves the odd tiny hole, but is far stronger than had I rin a colder pass
- Solid welds 003.jpg (132.27 KiB) Viewed 2470 times
- 3 mm angle iron is a cinch to weld. Even the mitered joints are a breeze. I need a die grinder though...
- Solid welds 001.jpg (150.76 KiB) Viewed 2470 times
- Bit wobbly, but otherwise pretty solid.
- Solid welds 002.jpg (82.63 KiB) Viewed 2470 times
- Otto Nobedder
-
Weldmonger
-
Posts:
-
Joined:Thu Jan 06, 2011 11:40 pm
-
Location:Near New Orleans
Looking much better, Chris,
I'd say you've rounded the corner that frustrates so many new welders, putting together all the pieces to get a decent bead each time.
Those pictures are looking good. Maybe not ready to "frame it and hang it"
but you're on your game now, and practice will do the rest.
Steve S
I'd say you've rounded the corner that frustrates so many new welders, putting together all the pieces to get a decent bead each time.
Those pictures are looking good. Maybe not ready to "frame it and hang it"

Steve S
jonescg
- jonescg
-
New Member
-
Posts:
-
Joined:Mon Oct 21, 2013 9:31 am
-
Location:Perth, Western Australia
Maybe not frame it and hang it, but here's a frame 
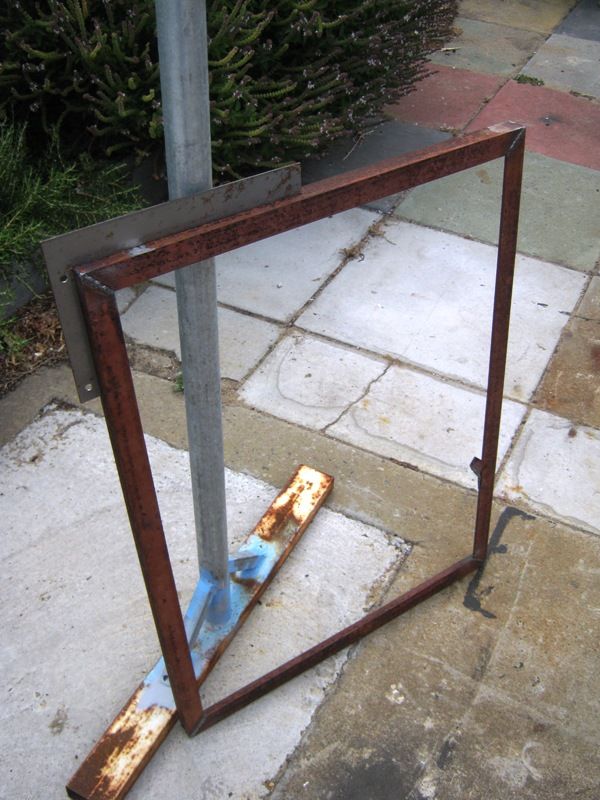
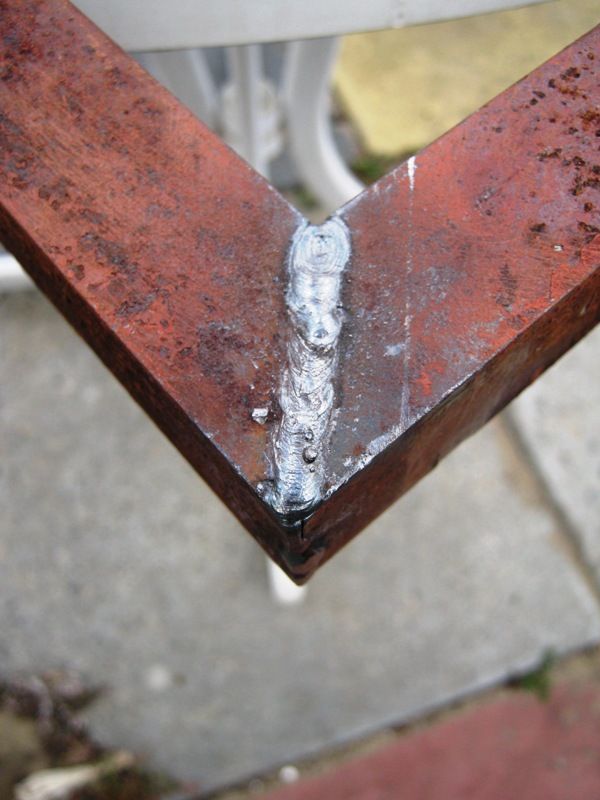
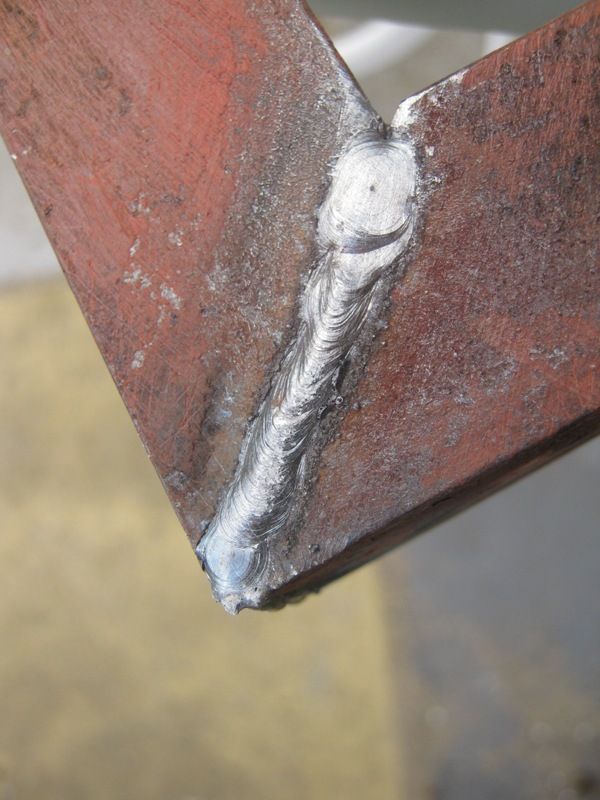
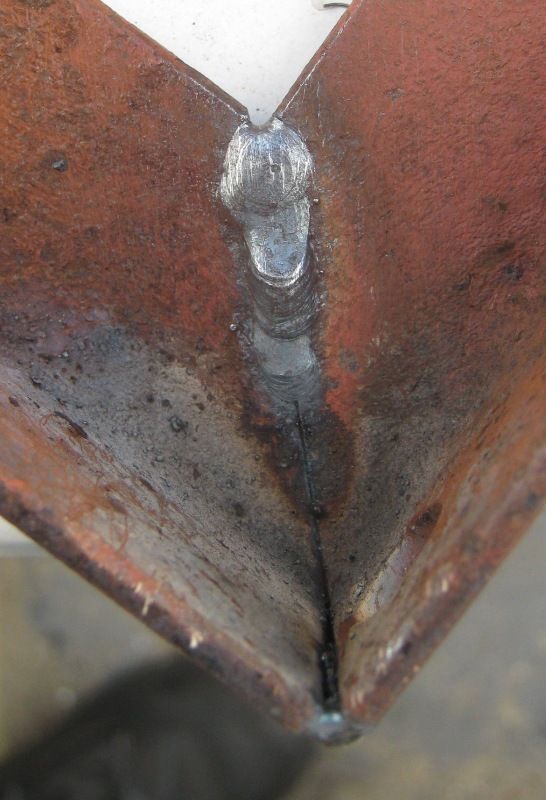
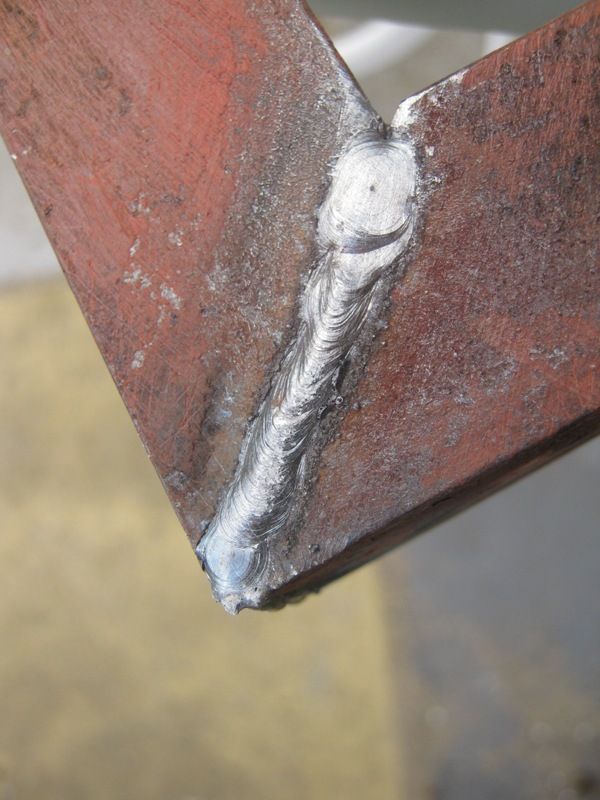
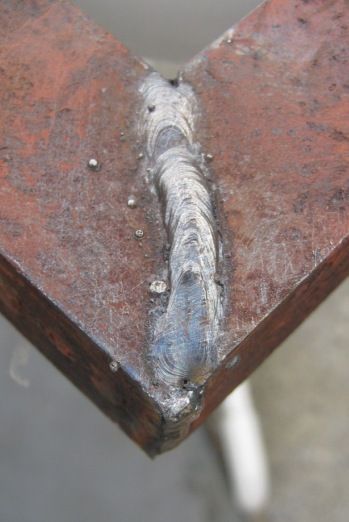
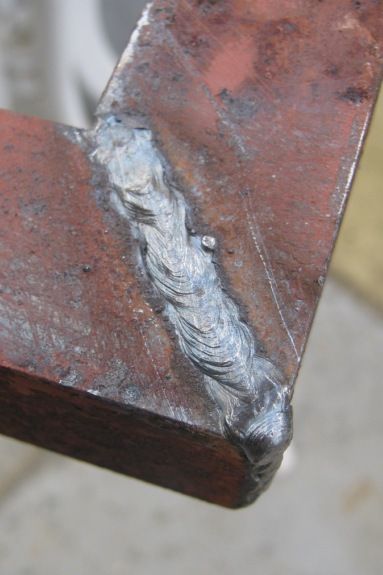
I think I'm doing pretty good! Best of all, it's mostly square which is a real achievement for me. I don't have a decent welding bench, just a small coffee table of 6 mm plate. It's not very flat which makes getting stuff square rather difficult.
Nonetheless, my beads are looking like beads and not hydatid cysts. I found provided I am comfortable, I can generally keep a good travel rate and keep it reasonably straight. Where it wobbles a bit is where I was somewhat awkwardly stanced.
Rather pleased with my progress
I was using this as a practice battery box for an electric car conversion. Since it was from recycled steel off the side of the road I'm not too fussed if it never sees another use. I will try to get the rest of the box built soon. It will be holding about 250 kg of battery, so strength is fairly important.

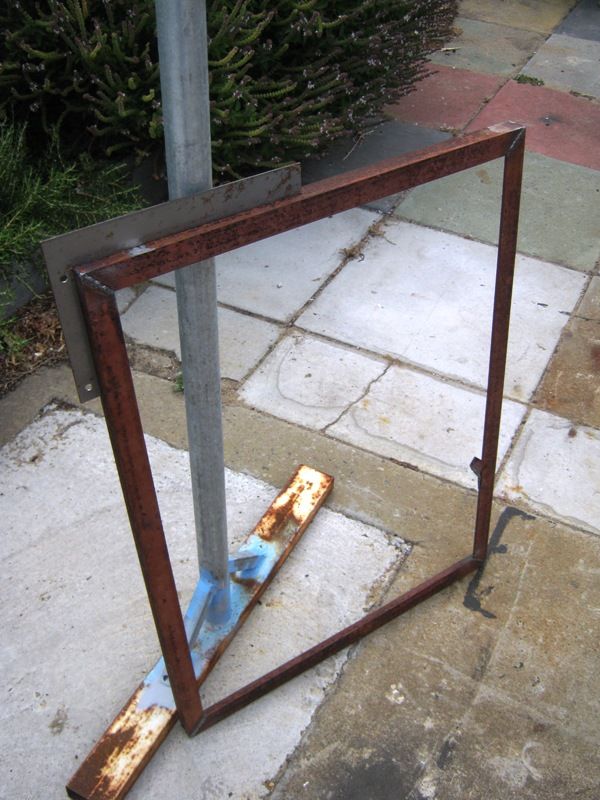
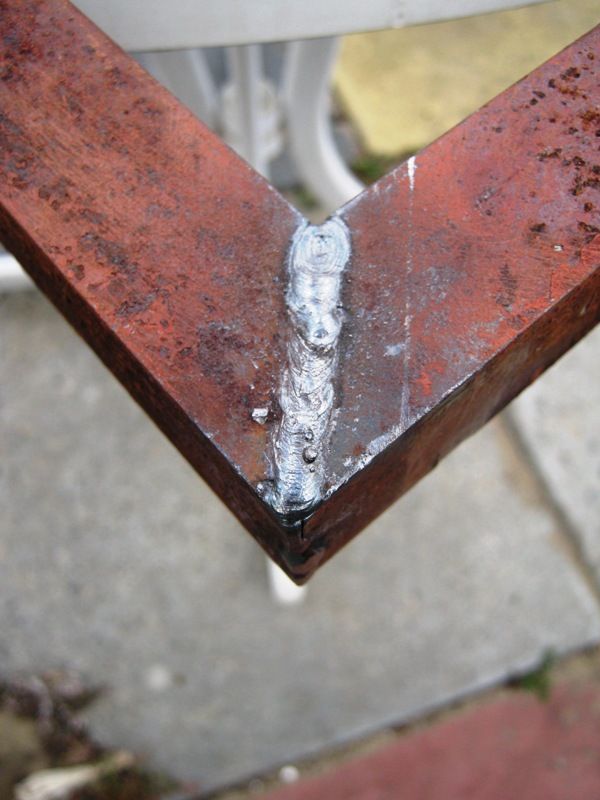
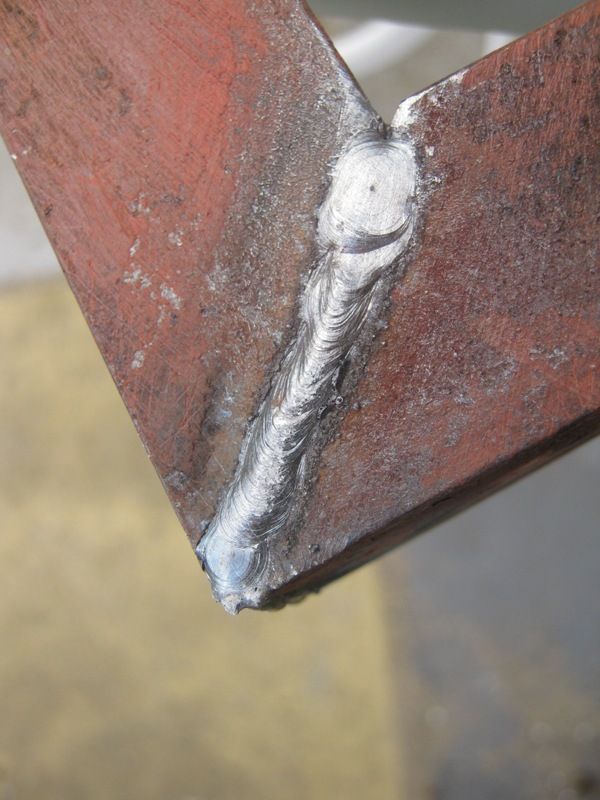
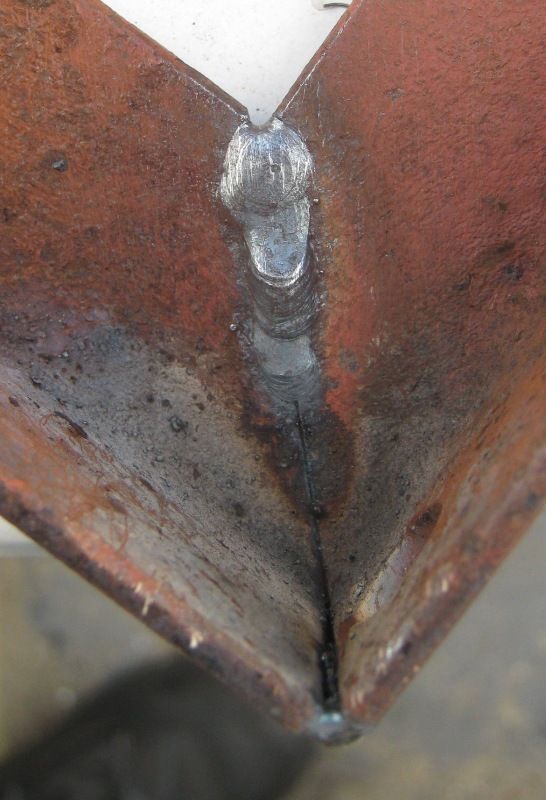
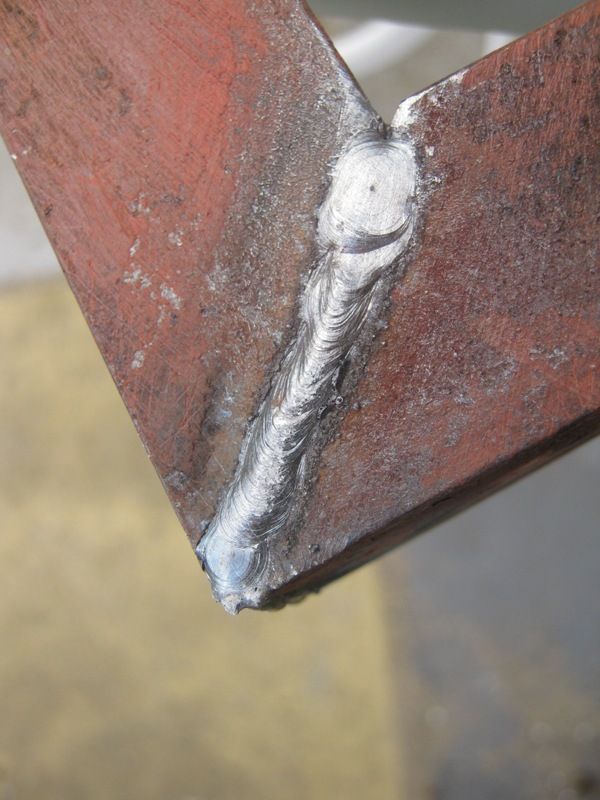
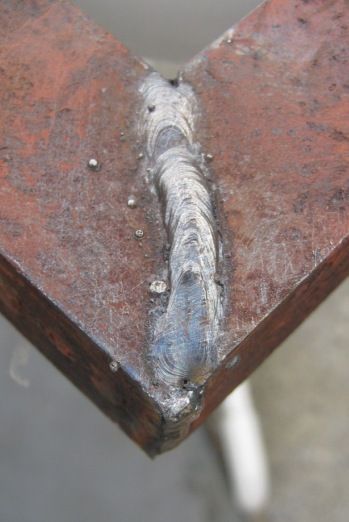
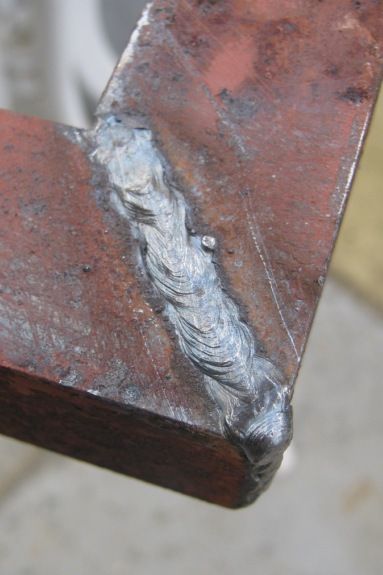
I think I'm doing pretty good! Best of all, it's mostly square which is a real achievement for me. I don't have a decent welding bench, just a small coffee table of 6 mm plate. It's not very flat which makes getting stuff square rather difficult.
Nonetheless, my beads are looking like beads and not hydatid cysts. I found provided I am comfortable, I can generally keep a good travel rate and keep it reasonably straight. Where it wobbles a bit is where I was somewhat awkwardly stanced.
Rather pleased with my progress

Looking pretty good. You might try bumping up the amperage a notch and maybe slow it down, maybe. That will flatten it out a bit and get the toes to dig in a little more.
Everlast PowerTig 250EX, PowerTig 185 Micro, PowerArc 160STH, Miller Trailblazer 301G, Millermatic 140 Auto-Set
- Otto Nobedder
-
Weldmonger
-
Posts:
-
Joined:Thu Jan 06, 2011 11:40 pm
-
Location:Near New Orleans
+1 on what Nils said, but don't stress on it too much. You're at a point where you're putting the pieces together and it's working for you. As you get more comfortable in your skills, make small changes (as Nils suggested) and compare the results.
You are now reaching the point where you can start to tell the effect from small changes, and can begin fine-tuning your settings.
You've progressed to this point rather quickly. I think in a few weeks you'll wonder why it seemed so challenging at the start.
Steve S
You are now reaching the point where you can start to tell the effect from small changes, and can begin fine-tuning your settings.
You've progressed to this point rather quickly. I think in a few weeks you'll wonder why it seemed so challenging at the start.
Steve S
jonescg
- jonescg
-
New Member
-
Posts:
-
Joined:Mon Oct 21, 2013 9:31 am
-
Location:Perth, Western Australia
Yes, thanks guys!
I agree - Now I can see what a comfortable stance does versus a more awkward one. Or stick angle, or travel rate, or clean metal or all of these things. Earlier, there were so many things going on it was hard to track each one. It's like my friend telling me how to olly on a skateboard. He said "you just stand on it with your front foot forward, and you kick down... and you just...you know... olly". Thanks Cam
Welding is both a trade skill and a craft. Electricians or bricklayers might talk about proficiency in their trade, but there's not much room for craftsmanship. I guess craftsmanship is the ability to build something functional, and simultaneously take pride in it looking beautiful and complete. Welding lends itself to that more than any other trade, and is possibly why there's so many self appointed masters of metallurgy out there (no-one in here BTW, this place is very helpful!).
The angle iron is 3 mm thick, which is possibly why I have room to bump the amps up a little. I'm going to build a couple of large right triangles for clamping work nice and square. It's hard to get a large frame like this perfect when your set square only extends about 10% the length of the work.
Cheers guys,
Chris
I agree - Now I can see what a comfortable stance does versus a more awkward one. Or stick angle, or travel rate, or clean metal or all of these things. Earlier, there were so many things going on it was hard to track each one. It's like my friend telling me how to olly on a skateboard. He said "you just stand on it with your front foot forward, and you kick down... and you just...you know... olly". Thanks Cam

The angle iron is 3 mm thick, which is possibly why I have room to bump the amps up a little. I'm going to build a couple of large right triangles for clamping work nice and square. It's hard to get a large frame like this perfect when your set square only extends about 10% the length of the work.
Cheers guys,
Chris
jonescg
- jonescg
-
New Member
-
Posts:
-
Joined:Mon Oct 21, 2013 9:31 am
-
Location:Perth, Western Australia
Well today I built myself a Pythagorean triangle. The objective is to get a perfect right angle; one my store-bought squares will hopefully agree with. I just took some angle iron and measured 750 mm, 600 mm and 450 mm and cut them at the approximate angles (53/2, 36/2 and 90/2). I filed them down to a perfect knife edge, making sure it was still square to the flat of the angle iron. I swaged the 36 degree corner on the outside first, then pulled or pushed them so the 450 mm section squeezed in. Then after tacking the 53 degree angle I checked the last angle, which was hopefully 90 degrees. According to my store-bought squares, it wasn't 
It was bloody close though, so I just welded it up anyway. I filed the corners so they were flush and started comparing it to other "square" things I had lying around. It varied, sometimes more, sometimes less. I even used my wife's sewing mat which has a grid of imperial measures, and it agreed with it perfectly. So maybe it is right and the store squares are off? That would explain why I had so much trouble getting my steel frame square yesterday.
I guess the only way to do it would be to make a gigantic Pythagorean triangle, or at least a 45 degree one. The hypotenuse of a 1 x 1 triangle is always sqrt (2), so that might be a more useful one as 45' is a handy measure - certainly more useful than 53.13 degrees...

- 345 triangle 003.jpg (172.96 KiB) Viewed 2043 times
- 345 triangle 002.jpg (196.89 KiB) Viewed 2043 times
- 345 triangle 001.jpg (101.96 KiB) Viewed 2043 times
I guess the only way to do it would be to make a gigantic Pythagorean triangle, or at least a 45 degree one. The hypotenuse of a 1 x 1 triangle is always sqrt (2), so that might be a more useful one as 45' is a handy measure - certainly more useful than 53.13 degrees...
- weldin mike 27
-
Weldmonger
-
Posts:
-
Joined:Fri Apr 01, 2011 10:59 pm
-
Location:Australia; Victoria
The way to tell if you square is out is to put it on a straight edge (edge of bench) and draw a line up the right angle blade. Then flip it over and check against this line, if its good, the line will be the same as your square, if its out the square will show an angled gap.
jonescg
- jonescg
-
New Member
-
Posts:
-
Joined:Mon Oct 21, 2013 9:31 am
-
Location:Perth, Western Australia
Not accounting for the kinks already in the angle iron, I got two parallel linesweldin mike 27 wrote:The way to tell if you square is out is to put it on a straight edge (edge of bench) and draw a line up the right angle blade. Then flip it over and check against this line, if its good, the line will be the same as your square, if its out the square will show an angled gap.

- weldin mike 27
-
Weldmonger
-
Posts:
-
Joined:Fri Apr 01, 2011 10:59 pm
-
Location:Australia; Victoria
Hey,
Thats good, on things like that, if you can get it to under 3mm over a metre, you're doing ok.
Mick
Thats good, on things like that, if you can get it to under 3mm over a metre, you're doing ok.
Mick
jonescg
- jonescg
-
New Member
-
Posts:
-
Joined:Mon Oct 21, 2013 9:31 am
-
Location:Perth, Western Australia
I had my first paying welding job today! Well, the job was for a friend, and the pay was a carton of grog, but still 
My welds actually looked really good - strong, concave and no blow holes. Only a couple of tiny inclusions too. I was welding 1.6 mm steel tube for the most part, and then welding 4 mm plate steel to the tubing. He even said "Geez that stick welding looks so much neater than I expected!" I should get him to send me some pictures to share, but in the meantime I'm just pleased to have reached this level
Might have me another beer...

My welds actually looked really good - strong, concave and no blow holes. Only a couple of tiny inclusions too. I was welding 1.6 mm steel tube for the most part, and then welding 4 mm plate steel to the tubing. He even said "Geez that stick welding looks so much neater than I expected!" I should get him to send me some pictures to share, but in the meantime I'm just pleased to have reached this level

Return to “Stick Welding/Arc Welding - Shielded Metal Arc Welding”
Jump to
- Introductions & How to Use the Forum
- ↳ Welcome!
- ↳ Member Introductions
- ↳ How to Use the Forum
- ↳ Moderator Applications
- Welding Discussion
- ↳ Metal Cutting
- ↳ Tig Welding - Tig Welding Aluminum - Tig Welding Techniques - Aluminum Tig Welding
- ↳ Mig and Flux Core - gas metal arc welding & flux cored arc welding
- ↳ Stick Welding/Arc Welding - Shielded Metal Arc Welding
- ↳ Welding Forum General Shop Talk
- ↳ Welding Certification - Stick/Arc Welding, Tig Welding, Mig Welding Certification tests - Welding Tests of all kinds
- ↳ Welding Projects - Welding project Ideas - Welding project plans
- ↳ Product Reviews
- ↳ Fuel Gas Heating
- Welding Tips & Tricks
- ↳ Video Discussion
- ↳ Wish List
- Announcements & Feedback
- ↳ Forum News
- ↳ Suggestions, Feedback and Support
- Welding Marketplace
- ↳ Welding Jobs - Industrial Welding Jobs - Pipe Welding Jobs - Tig Welding Jobs
- ↳ Classifieds - Buy, Sell, Trade Used Welding Equipment
- Welding Resources
- ↳ Tradeshows, Seminars and Events
- ↳ The Welding Library
- ↳ Education Opportunities