Hi All,
I seemed to have broken a tap in the worst place. 2005 F150 with a 5.4 motor right side exhaust manifold stud hole in the head. It's about a half inch in the hole. My question can I stick weld to the tap and build up to a nut to turn it out? Thanks for any suggestions.
Terry
Stick Welding Tips, Certification tests, machines, projects
- Otto Nobedder
-
Weldmonger
-
Posts:
-
Joined:Thu Jan 06, 2011 11:40 pm
-
Location:Near New Orleans
Aluminum head? This will help...
I wouldn't "stick" it, if it's buried that deep. This calls for a TIG buildup.
Not saying you can't do it with stick, but you have so many opportunities for inclusions so it will just break again when you twist on it.
Good luck,
Steve S
I wouldn't "stick" it, if it's buried that deep. This calls for a TIG buildup.
Not saying you can't do it with stick, but you have so many opportunities for inclusions so it will just break again when you twist on it.
Good luck,
Steve S
- MinnesotaDave
-
Weldmonger
-
Posts:
-
Joined:Sun Oct 27, 2013 10:57 pm
-
Location:Big Lake/Monticello MN, U.S.A.
Seems I saw a guy post on some website that he stuffed 4 cotter pins down the tap flutes and turned one out.
I've never done it, but it seems like small nails would work on bigger ones as well.
Good Luck
Edit: Found it, post #13
http://weldingweb.com/showthread.php?36 ... stick-arc)
I've never done it, but it seems like small nails would work on bigger ones as well.
Good Luck

Edit: Found it, post #13
http://weldingweb.com/showthread.php?36 ... stick-arc)
Dave J.
Beware of false knowledge; it is more dangerous than ignorance. ~George Bernard Shaw~
Syncro 350
Invertec v250-s
Thermal Arc 161 and 300
MM210
Dialarc
Tried being normal once, didn't take....I think it was a Tuesday.
Beware of false knowledge; it is more dangerous than ignorance. ~George Bernard Shaw~
Syncro 350
Invertec v250-s
Thermal Arc 161 and 300
MM210
Dialarc
Tried being normal once, didn't take....I think it was a Tuesday.
- Braehill
-
Weldmonger
-
Posts:
-
Joined:Sat Jul 06, 2013 11:16 am
-
Location:Near Pittsburgh,Pennsylvania. Steel Buckle of the Rust Belt
Terry,
There's a company named Walton that makes broken tap extractors. They work fairly well. They have four hardened pins that go down into the flutes and then you can usually work them out. We buy them from MSC and I believe Grainger also carries them. I think Irwin has a set but I haven't used theirs, so I can't speak to effectiveness though.
Len
There's a company named Walton that makes broken tap extractors. They work fairly well. They have four hardened pins that go down into the flutes and then you can usually work them out. We buy them from MSC and I believe Grainger also carries them. I think Irwin has a set but I haven't used theirs, so I can't speak to effectiveness though.
Len
Now go melt something.
Instagram @lenny_gforce
Len
Instagram @lenny_gforce
Len
YAHOO......!!!!!!Got it out. The Walton tap extractor worked great. Took about 5 minutes to get it out. Thanks everyone you all really helped.
OK next question the hole is pretty much mucked up. I'm going to drill it and tap to 1/2 x13 for a threaded insert that I like Problem I can only get a Drexel in there any suggestions?
OK next question the hole is pretty much mucked up. I'm going to drill it and tap to 1/2 x13 for a threaded insert that I like Problem I can only get a Drexel in there any suggestions?
- MinnesotaDave
-
Weldmonger
-
Posts:
-
Joined:Sun Oct 27, 2013 10:57 pm
-
Location:Big Lake/Monticello MN, U.S.A.
Good news manTerry W wrote:YAHOO......!!!!!!Got it out. The Walton tap extractor worked great. Took about 5 minutes to get it out. Thanks everyone you all really helped.
OK next question the hole is pretty much mucked up. I'm going to drill it and tap to 1/2 x13 for a threaded insert that I like Problem I can only get a Drexel in there any suggestions?

Will a small drill fit if you cut off a drill bit to only the length you need?
Or a right angle drill with the shorter bit?
Dave J.
Beware of false knowledge; it is more dangerous than ignorance. ~George Bernard Shaw~
Syncro 350
Invertec v250-s
Thermal Arc 161 and 300
MM210
Dialarc
Tried being normal once, didn't take....I think it was a Tuesday.
Beware of false knowledge; it is more dangerous than ignorance. ~George Bernard Shaw~
Syncro 350
Invertec v250-s
Thermal Arc 161 and 300
MM210
Dialarc
Tried being normal once, didn't take....I think it was a Tuesday.
- Otto Nobedder
-
Weldmonger
-
Posts:
-
Joined:Thu Jan 06, 2011 11:40 pm
-
Location:Near New Orleans
MinnesotaDave's right...
I've cut drill bits down quite short. Figure the length you need from the end of the chuck to the bottom of the hole, and add the total depth of the chuck at that drill size. You'll want a cut-down bit to hit the bottom of the chuck to be sure the jaws will grip the flutes squarely to cut the hole squarely.
There's nothing quite like a right-angle air drill with a 1/2" chuck to accompish the "seemingly impossible"...
Steve S
I've cut drill bits down quite short. Figure the length you need from the end of the chuck to the bottom of the hole, and add the total depth of the chuck at that drill size. You'll want a cut-down bit to hit the bottom of the chuck to be sure the jaws will grip the flutes squarely to cut the hole squarely.
There's nothing quite like a right-angle air drill with a 1/2" chuck to accompish the "seemingly impossible"...
Steve S
I cut down a bit. Tomorrow I'll use the old manifold as a guide and drill the hole. Hopefully I'll be able to tap this without breaking the tap. It's a pretty big tap so I'm not expecting any problems.
Plus I only have to go in about a 1/2 inch.

I have a stud drilling guide that was made for the Porsche 911... similar to:Terry W wrote:I cut down a bit. Tomorrow I'll use the old manifold as a guide and drill the hole. Hopefully I'll be able to tap this without breaking the tap. It's a pretty big tap so I'm not expecting any problems.Plus I only have to go in about a 1/2 inch.

The bolt in the center is to hold centering guides:
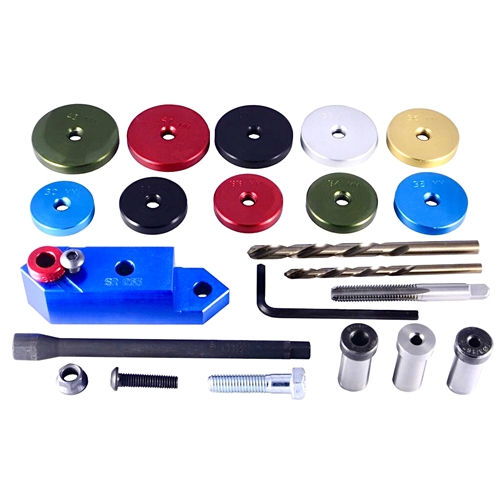
My tool has two screws at an angle to go into the port to center the bushing over the hole. The different drill bushings are for the drill, tap and heli-coil tap
Glen
Miller Dynasty 200DX - Millermatic 350P - Hypertherm Powermax 45 - Hobart Handler 150
Miller Dynasty 200DX - Millermatic 350P - Hypertherm Powermax 45 - Hobart Handler 150
Update in case anyone was wondering how things turned out. There was two pieces of metal in the hole. One from the tap and one from the stud. Took me a few hours with some dental drill bits to remove the metal from the stud. Worked blind most of the time using a mirror and feel. Retapped to a 9/16 - 12 make a plug from a 9/16 bolt and them tapped that to an M8 1.25 same size as the studs for the exhaust manifold.I have a small lathe. Buttoned everything up today and crossed my fingers. Everything seems to be holding and a nice quiet exhaust. That exhaust has been leaking for years. It just got really loud in the last couple of weeks.
I want to thank everyone again for all the help you guys were great. I will play this forward.
Terry W
I want to thank everyone again for all the help you guys were great. I will play this forward.
Terry W
Return to “Stick Welding/Arc Welding - Shielded Metal Arc Welding”
Jump to
- Introductions & How to Use the Forum
- ↳ Welcome!
- ↳ Member Introductions
- ↳ How to Use the Forum
- ↳ Moderator Applications
- Welding Discussion
- ↳ Metal Cutting
- ↳ Tig Welding - Tig Welding Aluminum - Tig Welding Techniques - Aluminum Tig Welding
- ↳ Mig and Flux Core - gas metal arc welding & flux cored arc welding
- ↳ Stick Welding/Arc Welding - Shielded Metal Arc Welding
- ↳ Welding Forum General Shop Talk
- ↳ Welding Certification - Stick/Arc Welding, Tig Welding, Mig Welding Certification tests - Welding Tests of all kinds
- ↳ Welding Projects - Welding project Ideas - Welding project plans
- ↳ Product Reviews
- ↳ Fuel Gas Heating
- Welding Tips & Tricks
- ↳ Video Discussion
- ↳ Wish List
- Announcements & Feedback
- ↳ Forum News
- ↳ Suggestions, Feedback and Support
- Welding Marketplace
- ↳ Welding Jobs - Industrial Welding Jobs - Pipe Welding Jobs - Tig Welding Jobs
- ↳ Classifieds - Buy, Sell, Trade Used Welding Equipment
- Welding Resources
- ↳ Tradeshows, Seminars and Events
- ↳ The Welding Library
- ↳ Education Opportunities