Start out with a bend. I used a 75 deg in this situation but 60 would have worked. I basically just use a line on my table. The lines on the table here were leftover from a previous project. You can also draw in the situation that fits a specific layout target. I just needed these to be identical. Line up where you need the scarph, and put two reference marks. One at the toe (top of photo) and one at the heel.
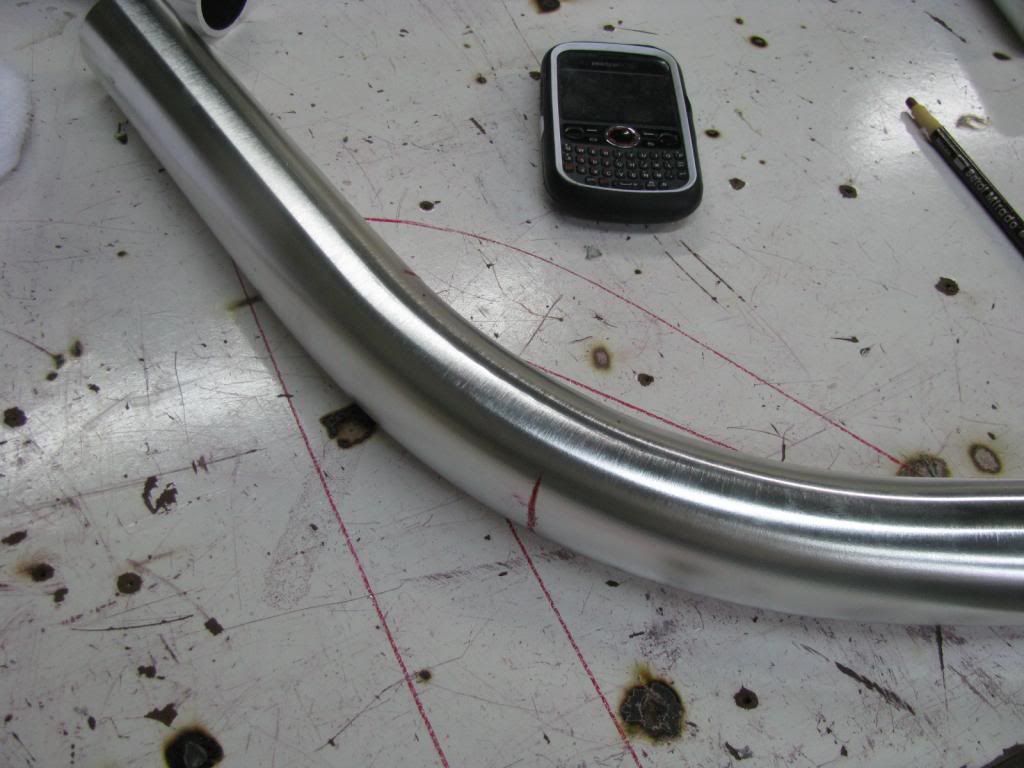
Then draw in your cope profile. I see these in my sleep so I can eyeball them by now at any angle. Other tube fabricators will know what I mean by this. If you aren't familiar with tubing, you can exaggerate these profiles and sneak up on them a little at a time.
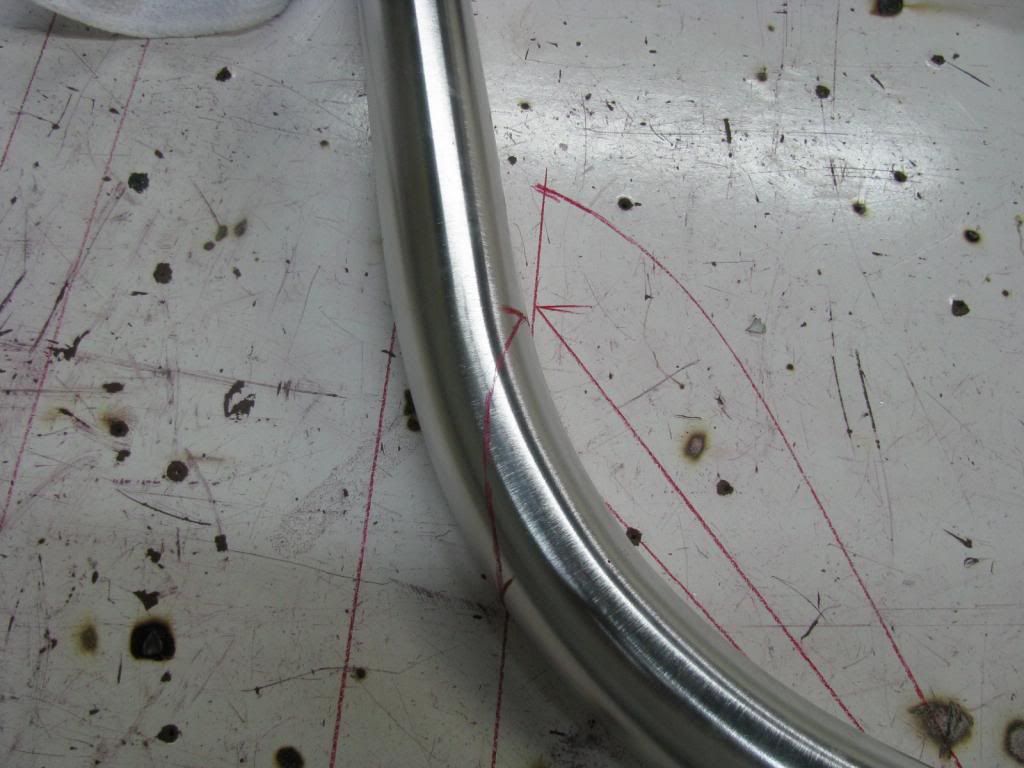
Then just whack the toe off at the line. I use a band saw for 99% of my fit ups. This makes it easier to see where to start the cut that would normally be hidden from view at the saw and keeps the blade from wandering down the curve off of the line.
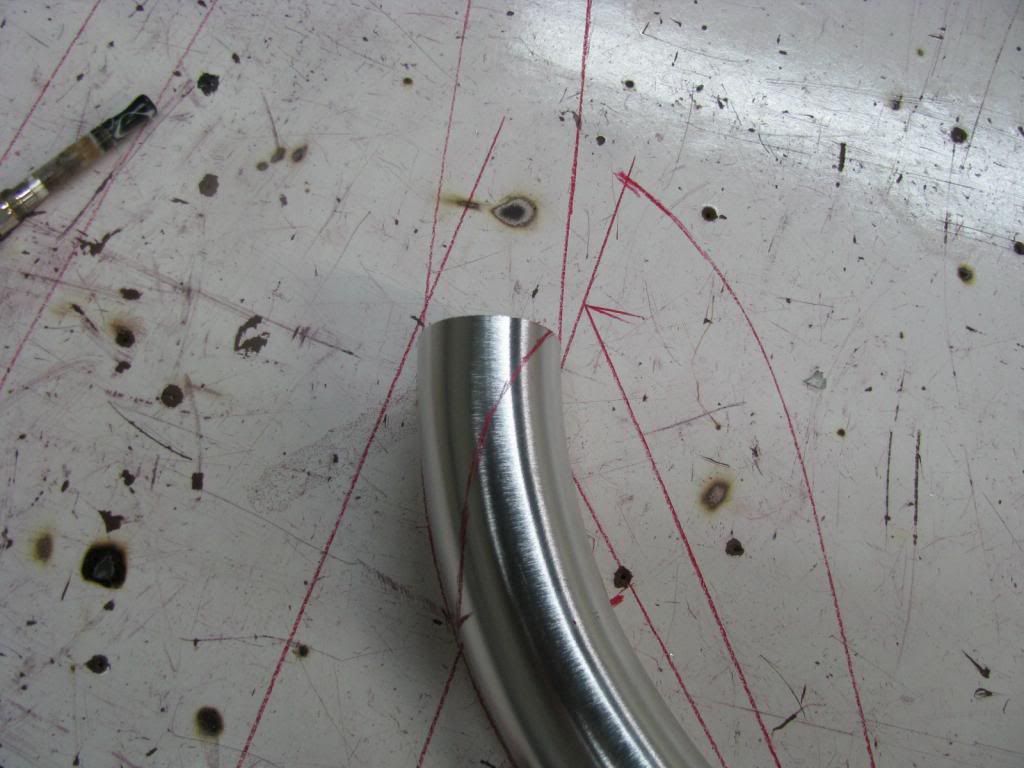
The rest is obvious. You can either trim the 2nd dimension wall thickness shoulders of the profile with the saw, or you can use a die grinder to make it fit really snug. I don't like to finish aluminum too sharply. I don't like welding aluminum on a sharp edge. I leave about a 16th land along the profile. If you were letting this in for plumbing applications, you would have mating bevels ideally, in which to get consistent penetration throughout.
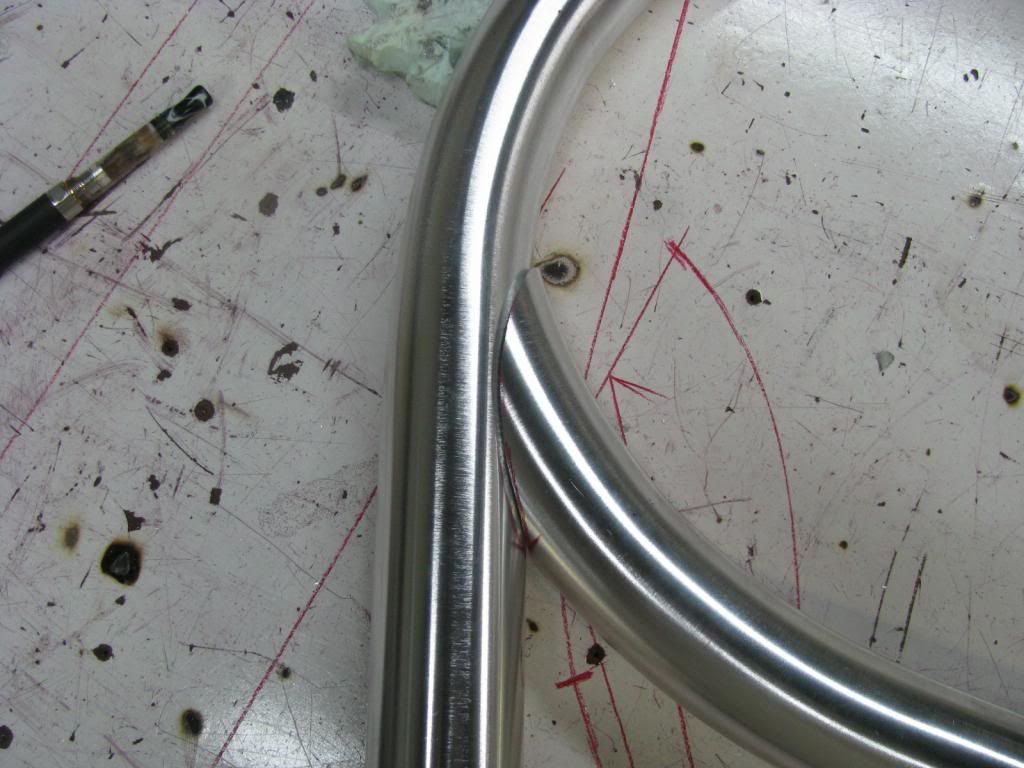