Want to get back to the torch tomorrow. It's Spring Break, so I'll just be welding at home this week.
I'll repeat the coping weld with the home torch, and compare to the school TIG.
Been trying hard to come up with other fun projects.
Definitely need to work on my tack welding. I've been doing a quick blast, sometimes with a bit of filler rod to prevent burning a hole. Works great for practice coupons, but isn't going go cut it for fabrication. I need to tack using minimal rod, and also melt a minimal amount of the parent metal. That way, I can cut the tacks and reuse the pieces. Will take some practice.
Planning on doing a Razor Blade Challenge. Should be fun.
Planning on welding some nuts & bolts together. I've see it done a lot for different reasons.
Would like to weld some motorcycle cast aluminum. Need to get some trashed aluminum side covers to practice on. No idea where to find them, though.
Wasn't able to get scrap titanium. The titanium coupons I made were from brand new retail stock. I've already started dipping into my good stuff, too. Grabbed some nice 1/8" aluminum to practice on:
The aluminum half pipe was really fun. Moving the torch from the top, to the side, I wasn't maintaining a proper angle, or tight arc, or both. The fillet welds look a bit shoddy, but strong. Fillet welds are hard for me, so I'm happy. Had a good run on the other side.
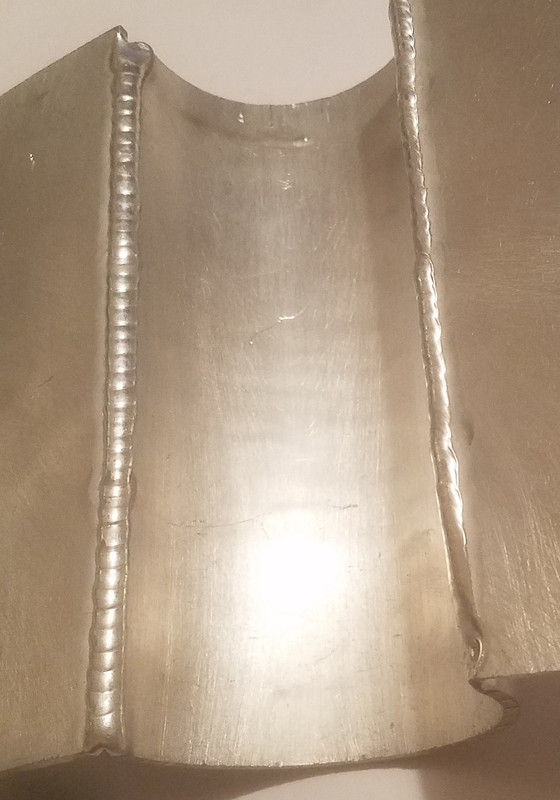