Tig welding tips, questions, equipment, applications, instructions, techniques, tig welding machines, troubleshooting tig welding process
Had a guy contact me about repairing a leaking fuel tank on his boat. The tank was removable and would have been easy money, but because it had fuel in it I declined the job. How do you work on fuel tanks filled with explosive fumes? BTW, TamJeff, loved the piece on working with dirty metals. Thank you!
Everlast PowerTig 250EX, PowerTig 185 Micro, PowerArc 160STH, Miller Trailblazer 301G, Millermatic 140 Auto-Set
Nils
I do a lot of small fuel tank repairs. (did one on Yamaha Virago this morning)
Here's what I do.
1. drain the tank
2. wash it out with Dawn and hot tap water.
3. flush it! Run he hose in the filler and just let it run over the top for at least 5 min.
4. drain and repeat #3
5. drain and blow dry with compressed air
6. argon purge. standard motorcycle tank I do 20cfh for @5 minutes then drop to 5cfh and continue
purging till the welding is finished. Bigger tanks require longer purges. Remember, you are displacing
both hydrocarbon fumes and the oxygen atmosphere.
Jody did a nice video on purge setups using painter's tape. Check that out.
Disclaimer: This is what works for me. It's not the only way and many will tell you a purge is a waste of time.
It may be but for me it's a must. You see, I witnessed a coworker blow his hand slap off welding a motorcycle
tank without a purge. I not only witnessed it but I put a pressure bandage on his stump and put his severed hand
in a cooler full of ice! Then sat with him until the rescue squad arrived!
I do a lot of small fuel tank repairs. (did one on Yamaha Virago this morning)
Here's what I do.
1. drain the tank
2. wash it out with Dawn and hot tap water.
3. flush it! Run he hose in the filler and just let it run over the top for at least 5 min.
4. drain and repeat #3
5. drain and blow dry with compressed air
6. argon purge. standard motorcycle tank I do 20cfh for @5 minutes then drop to 5cfh and continue
purging till the welding is finished. Bigger tanks require longer purges. Remember, you are displacing
both hydrocarbon fumes and the oxygen atmosphere.
Jody did a nice video on purge setups using painter's tape. Check that out.
Disclaimer: This is what works for me. It's not the only way and many will tell you a purge is a waste of time.
It may be but for me it's a must. You see, I witnessed a coworker blow his hand slap off welding a motorcycle
tank without a purge. I not only witnessed it but I put a pressure bandage on his stump and put his severed hand
in a cooler full of ice! Then sat with him until the rescue squad arrived!
noddybrian
- noddybrian
-
Weldmonger
-
Posts:
-
Joined:Thu Jan 24, 2013 12:13 pm
I guess we all have our own variations on this and strangely it's diesel that is the highest risk ( in my opinion ) as tiny amounts can adhere in difficult to reach areas - then as heat from the welding causes it to form a vapor it can explode when you thought the tank was clean.
The method I use.
1 drain tank - if possible remove filler point / gauge sender to allow a view inside & get wet shop vac to remove as much fuel as possible.
2 as alot of fuel won't mix easily with water / detergent put a small amount of a something like isopropanol in & swill round - drain / vacuum out - now whats left should mix more readily
3 I have a short lance with a drain cleaning multi jet nozzle fitted that goes on my steam cleaner - I put some detergent in the tank first - then blast it around with the steam cleaner - once tank is full empty & rinse out - if it's a very big tank you may end up just getting some water in & turning the tank over a few times with forklift / gantry crane.
4I like to blow the tank out as dry as possible & usually leave a plastic welding / paint stripper hot air gun blowing in it till dry.
5 now if your argon is cheap then by all means use it to purge - in the UK however it is extremely expensive - whereas CO2 is cheap - I use the small cylinders as used in bars ( around 10 > 20 liter capacity ) - simply hold cylinder inverted point the outlet into the filler neck of the tank & give it a good blast on the cylinder valve ( no regulator fitted ) - liquid CO2 will blast into the tank & some will lay on the bottom - but at room temperature some will turn to gas & fill the tank - it will displace everything else being the heavier gas - now tape up the filler leaving a small hole - as you weld the tank heat will keep making the gas expand & constantly escape taking anything else with it.
I've welded many tanks by this method without problem - but obviously take this advise at your own discretion - it's not something that's commonly taught & I'm not sure if the safety police have yet come up with a " safe " procedure.
The method I use.
1 drain tank - if possible remove filler point / gauge sender to allow a view inside & get wet shop vac to remove as much fuel as possible.
2 as alot of fuel won't mix easily with water / detergent put a small amount of a something like isopropanol in & swill round - drain / vacuum out - now whats left should mix more readily
3 I have a short lance with a drain cleaning multi jet nozzle fitted that goes on my steam cleaner - I put some detergent in the tank first - then blast it around with the steam cleaner - once tank is full empty & rinse out - if it's a very big tank you may end up just getting some water in & turning the tank over a few times with forklift / gantry crane.
4I like to blow the tank out as dry as possible & usually leave a plastic welding / paint stripper hot air gun blowing in it till dry.
5 now if your argon is cheap then by all means use it to purge - in the UK however it is extremely expensive - whereas CO2 is cheap - I use the small cylinders as used in bars ( around 10 > 20 liter capacity ) - simply hold cylinder inverted point the outlet into the filler neck of the tank & give it a good blast on the cylinder valve ( no regulator fitted ) - liquid CO2 will blast into the tank & some will lay on the bottom - but at room temperature some will turn to gas & fill the tank - it will displace everything else being the heavier gas - now tape up the filler leaving a small hole - as you weld the tank heat will keep making the gas expand & constantly escape taking anything else with it.
I've welded many tanks by this method without problem - but obviously take this advise at your own discretion - it's not something that's commonly taught & I'm not sure if the safety police have yet come up with a " safe " procedure.
- Otto Nobedder
-
Weldmonger
-
Posts:
-
Joined:Thu Jan 06, 2011 11:40 pm
-
Location:Near New Orleans
I have a caution for the idea of a wet/dry vac for removing fuel, simply because it should have and "explosion-proof" rated motor and it's exhaust vented safely. This is expensive and impractical for a one-off job. Fuel/air mixtures have a very narrow range of "combustability", but the exhaust from a shop-vac will be all over the map, and one errant spark at the wrong moment...
I do agree with isopropanol or even methanol as a diluant during the drain/rinse, to make a detergent wash more effective. I rarely do gas or deisel tanks... I usually work on liquid hydrogen tanks, but surprisingly, they are far easier to purge, since LHY boils at -423F, so once the tank is at room temp, all liquid is long gone, and all gas is displaced with nitrogen. Welds are then locally purged with argon.
The keys are removing all liquid fuel, displacing all remaining vapor as best you can, and displacing all oxygen. Nitrogen is cheaper, but argon has an advantage... It's heavier than air, and after an initial fast purge to displace as much O2 and vapor as possible, a very slow purge through a diffuser near the bottom of the tank will displace all remaining oxygen and make the tank safe to weld on.
I'll add that I like the CO2 idea for purge on aluminum and steel tanks, but would not recommend it (or nitrogen) on SS tanks. CO2 is an "active gas", affecting the weld, and austenitic stainless is prone to "nitrogen embrittlement". I know neither apply to the original post, but in any discussion of fuel tanks, I like to share as much as I can, so no one takes advice for one type of repair and expects it to apply to another.
Steve S
I do agree with isopropanol or even methanol as a diluant during the drain/rinse, to make a detergent wash more effective. I rarely do gas or deisel tanks... I usually work on liquid hydrogen tanks, but surprisingly, they are far easier to purge, since LHY boils at -423F, so once the tank is at room temp, all liquid is long gone, and all gas is displaced with nitrogen. Welds are then locally purged with argon.
The keys are removing all liquid fuel, displacing all remaining vapor as best you can, and displacing all oxygen. Nitrogen is cheaper, but argon has an advantage... It's heavier than air, and after an initial fast purge to displace as much O2 and vapor as possible, a very slow purge through a diffuser near the bottom of the tank will displace all remaining oxygen and make the tank safe to weld on.
I'll add that I like the CO2 idea for purge on aluminum and steel tanks, but would not recommend it (or nitrogen) on SS tanks. CO2 is an "active gas", affecting the weld, and austenitic stainless is prone to "nitrogen embrittlement". I know neither apply to the original post, but in any discussion of fuel tanks, I like to share as much as I can, so no one takes advice for one type of repair and expects it to apply to another.
Steve S
noddybrian
- noddybrian
-
Weldmonger
-
Posts:
-
Joined:Thu Jan 24, 2013 12:13 pm
@ Otto
Thanks for a couple of points there - I should have mentioned the shop vac - the one I use mainly is actually air powered - you simply clip an air hose on the fitting on the top & it works like a venturi - it is essentially a cheap " air mover gun " sitting on top of a plastic tub - & if using it to move nasty fumes I have a long exhaust tube to take outside ( years back I had to repair tanks that carried ammonia). I also have an electric one but that works in a similar way - the air does not pass through the motor - but I agree fuel air mixture blowing around near a brushed motor is not ideal.
Good catch on the CO2 - I've only ever had steel or aluminum tanks in to repair - never had a stainless one so I never gave the active aspect of the gas any thought - only time I get stainless tanks to alter / repair their usually fresh water tanks off boats / RV's & I'll be honest - the state their in time I get to work on them I don't purge the inside with anything - just try to keep a real sharp small tungsten & keep the amps to a minimum - but I do clean them with bleach followed by steam cleaning as they usually have an interesting mix of algae & small critters in !
Thanks for your experience / perspective on this.
Thanks for a couple of points there - I should have mentioned the shop vac - the one I use mainly is actually air powered - you simply clip an air hose on the fitting on the top & it works like a venturi - it is essentially a cheap " air mover gun " sitting on top of a plastic tub - & if using it to move nasty fumes I have a long exhaust tube to take outside ( years back I had to repair tanks that carried ammonia). I also have an electric one but that works in a similar way - the air does not pass through the motor - but I agree fuel air mixture blowing around near a brushed motor is not ideal.
Good catch on the CO2 - I've only ever had steel or aluminum tanks in to repair - never had a stainless one so I never gave the active aspect of the gas any thought - only time I get stainless tanks to alter / repair their usually fresh water tanks off boats / RV's & I'll be honest - the state their in time I get to work on them I don't purge the inside with anything - just try to keep a real sharp small tungsten & keep the amps to a minimum - but I do clean them with bleach followed by steam cleaning as they usually have an interesting mix of algae & small critters in !
Thanks for your experience / perspective on this.
The thing about aluminum boat tanks is, by the time they develop their first 'thru' leak, there are usually more about to occur and if it's an original workmanship issue, the rest of the tank is at least suspect as well. For what a custom boat tank costs, vs the amount of years they last, it's usually false economy to repair one. The last tank I built was over refusal to (it had like 40 other pitted spots) weld the original. By the time I cleaned it, purged and welded it, I would have been half again what a new one costs going by current shop rates, not to mention the work involved removing and re-installing it only to end up with a used tank. To go through all that just to give it a couple years of service is not worth it to me. I treat fuel tank leaks on a boat like one might treat one on an air plane. There is never a good time for it to happen. Fuel saturated flotation foam is a 'bomb' in itself.
Miller ABP 330, Syncrowave 250, Dynasty 300 DX.
Honorary member of the Fraternity of Faded Tee Shirts.
Honorary member of the Fraternity of Faded Tee Shirts.
noddybrian
- noddybrian
-
Weldmonger
-
Posts:
-
Joined:Thu Jan 24, 2013 12:13 pm
@ TamJeff
I agree in principal - but many times the customer " knows best " even if all logic says he's wrong ! as long as he's paying me then I'll go along with it provided it's not unsafe.
Sometimes though the tank itself is still good but has been mounted badly & has been damaged by movement that can easily be repaired with a doubling patch or a recent tank I welded needed a large outlet for a transfer pump added as the owner was fitting a secondary tank the other side & an extra pair of pick up pipes & a return for a new onboard generator & Eberspatch heater - so sometimes an alteration is valid - I now try to convince anyone I make a new tank for to have a large removable cover big enough to get your arm through & mount all level senders / fittings to this - that way you can see in the tank for cleaning & remove / replace pipe fitting or add new ones as needed without removing the tank - that said - I don't get many tanks to work on.
I did recently refuse to repair an aluminum fresh water tank much to the annoyance of the customer - but it was so badly attacked by electrolysis it was way beyond salvage - I also questioned whether the material was suitable for potable water on a boat he lived on - after a little research into what grade aluminum was used if I made a new replacement we were led to believe that aluminum was not advised at all - a mate put him in touch with a company that makes plastic tanks to order & that's what he now has - he's quite happy as although it cost some he now has safe water & this new material is claimed never to need sterilizing or treatment for bacteria.
I agree in principal - but many times the customer " knows best " even if all logic says he's wrong ! as long as he's paying me then I'll go along with it provided it's not unsafe.
Sometimes though the tank itself is still good but has been mounted badly & has been damaged by movement that can easily be repaired with a doubling patch or a recent tank I welded needed a large outlet for a transfer pump added as the owner was fitting a secondary tank the other side & an extra pair of pick up pipes & a return for a new onboard generator & Eberspatch heater - so sometimes an alteration is valid - I now try to convince anyone I make a new tank for to have a large removable cover big enough to get your arm through & mount all level senders / fittings to this - that way you can see in the tank for cleaning & remove / replace pipe fitting or add new ones as needed without removing the tank - that said - I don't get many tanks to work on.
I did recently refuse to repair an aluminum fresh water tank much to the annoyance of the customer - but it was so badly attacked by electrolysis it was way beyond salvage - I also questioned whether the material was suitable for potable water on a boat he lived on - after a little research into what grade aluminum was used if I made a new replacement we were led to believe that aluminum was not advised at all - a mate put him in touch with a company that makes plastic tanks to order & that's what he now has - he's quite happy as although it cost some he now has safe water & this new material is claimed never to need sterilizing or treatment for bacteria.
Agreed, in some situations. It's just not worth it to me to do it. Figure a 90 gallon tank takes 350.00 in fuel or so to fill one time. Saving that much by repairing equals one offshore trip around these parts anyway. So you kind of see where such a practice starts to seem kind of redundant in the grand scheme of things with regards to boats/boating.
When I point out the above cost/usage analysis to the customer, most will not have thought about it that way and will see the light 99% of the time.
I've repaired them successfully before but I always felt that they were getting a better deal than I was, with the risk all on me and heaven forbid it spring another leak.
When I point out the above cost/usage analysis to the customer, most will not have thought about it that way and will see the light 99% of the time.
I've repaired them successfully before but I always felt that they were getting a better deal than I was, with the risk all on me and heaven forbid it spring another leak.
Miller ABP 330, Syncrowave 250, Dynasty 300 DX.
Honorary member of the Fraternity of Faded Tee Shirts.
Honorary member of the Fraternity of Faded Tee Shirts.
I think you will sleep better avoiding that job. Some people that do it all the time think nothing of it. I've worked on fuel depots at the port and I was never comfortable in that environment, even with fume sniffer devices and all that. Only thing between me and live fuel was a valve and a rubber pipe pig. Weld 5 minutes and have to evacuate the area and restart every time a truck came and went. Have welded up a bunch of diesel tanks as well with fuel still in them.Nils wrote:Had a guy contact me about repairing a leaking fuel tank on his boat. The tank was removable and would have been easy money, but because it had fuel in it I declined the job. How do you work on fuel tanks filled with explosive fumes? BTW, TamJeff, loved the piece on working with dirty metals. Thank you!
I did the repairs on 10 of these 300 gallon portables, all of which still had wet diesel in them. The trick was lift the end I was working on and let the heat from the initial start up evaporate the fuel. No purge, no rinse, nada. I think it amounted to something like 60 linear feet of weld each.
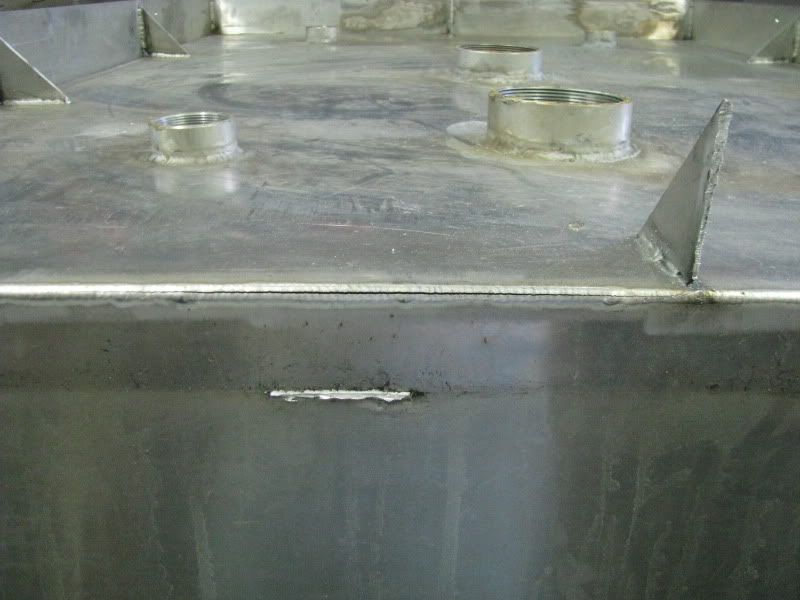
They brought the last two along with a 75 gal tank and I swore it smelled like gasoline and diesel mixed. My boss said it was just stale, yet everyone that walked in that I asked to smell it said they smelled gasoline. I declined to weld it. My boss trusted my instinct when it was all said and done.
Dirty metal is a way of life working with anodized. It's clean dirt, but it teaches you a lot about how to get around contaminated material, or whether it can be welded at all. Cast aluminum has to be the biggest crap shoot out there. That and the invisible salt inclusion that never goes away regardless of how well you prep.
Miller ABP 330, Syncrowave 250, Dynasty 300 DX.
Honorary member of the Fraternity of Faded Tee Shirts.
Honorary member of the Fraternity of Faded Tee Shirts.
Return to “Tig Welding - Tig Welding Aluminum - Tig Welding Techniques - Aluminum Tig Welding”
Jump to
- Introductions & How to Use the Forum
- ↳ Welcome!
- ↳ Member Introductions
- ↳ How to Use the Forum
- ↳ Moderator Applications
- Welding Discussion
- ↳ Metal Cutting
- ↳ Tig Welding - Tig Welding Aluminum - Tig Welding Techniques - Aluminum Tig Welding
- ↳ Mig and Flux Core - gas metal arc welding & flux cored arc welding
- ↳ Stick Welding/Arc Welding - Shielded Metal Arc Welding
- ↳ Welding Forum General Shop Talk
- ↳ Welding Certification - Stick/Arc Welding, Tig Welding, Mig Welding Certification tests - Welding Tests of all kinds
- ↳ Welding Projects - Welding project Ideas - Welding project plans
- ↳ Product Reviews
- ↳ Fuel Gas Heating
- Welding Tips & Tricks
- ↳ Video Discussion
- ↳ Wish List
- Announcements & Feedback
- ↳ Forum News
- ↳ Suggestions, Feedback and Support
- Welding Marketplace
- ↳ Welding Jobs - Industrial Welding Jobs - Pipe Welding Jobs - Tig Welding Jobs
- ↳ Classifieds - Buy, Sell, Trade Used Welding Equipment
- Welding Resources
- ↳ Tradeshows, Seminars and Events
- ↳ The Welding Library
- ↳ Education Opportunities