My practice scrap steel here is 1/16th" thick (I think), I had the amps set to a maximum of about 85 or so (keeping the pedal 3/4-full most of the time), 1/16" tungsten 2% lanthanated, and argon at almost 15cfh.
I'm still getting used to moving the torch, holding it differently, trying different movements with the gun, distance from the metal and so on. Also trying things that I know probably won't work well, to see what they look and feel like. I'll do this a good bit more, then next I'd like to try and work on making lots of runs and keeping them consistent.
Does the under cut here suggest I should be doing something different? Or is this normal when not using any filler rod? I've proped the sheet meal up off of my welding table, so that the heat stays on the sheet metal. I figure this is probably a more accurate test method than laying it flat down on the welding table? I'm not going to start using filler rod until I'm more comfortable with the torch.
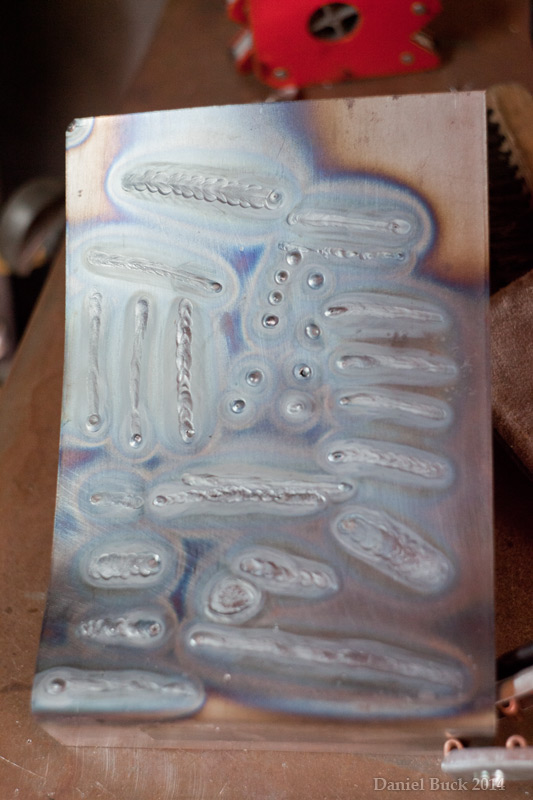
Thanks for any input!
