I am looking for some pointers to improve what I have been doing. I usually weld V-band flanges to stainless steel long tube headers. The headers are 304SS and the V-band flange is also 304SS.
Here is what I am using currently
16 gauge 304 SS header
304 SS V-band flange
Miller Dynasty 200DX
Machine set to 77 AMPS max
#9 air cooled torch - gas lense - #5 cup
1/16" 2% lanthanated tungsten toa sharp point
1/16" 309L filler wire
Seems no matter what I do I warp the V-band flange slightly. The last set turned out okay but I am pretty critical of myself. The tacked the flange in approx 8 places and them welded between tacks and moved around 180 deg. from where I just welded. This is a lap joint thick to thin. The headers slides inside a milled grove in the flange.
I guess I am looking for advice on tacking and torch placement when welding. In the past I have just held the torch at a 45 angle between both and just fire up and try to melt both and add filling rod to fuse them. With tacking something like this would I be better off lighting up on the thicker flange and washing it down to the headers (thinner) while adding filler? Once the tacks are done I also find myself at more of a 45 deg angle. I am open to all suggestions to improve my product
Tig welding tips, questions, equipment, applications, instructions, techniques, tig welding machines, troubleshooting tig welding process
- J & J Speed Shop
-
New Member
-
Posts:
-
Joined:Wed Sep 03, 2014 11:49 pm
-
Location:Western New York
- weldin mike 27
-
Weldmonger
-
Posts:
-
Joined:Fri Apr 01, 2011 10:59 pm
-
Location:Australia; Victoria
Make a mock up v band welded to a chunk of plate then weld the pipe flange on while it's bolted to the brace v band one. Stainless bows like a bitch so don't be too hard on yourself
- Braehill
-
Weldmonger
-
Posts:
-
Joined:Sat Jul 06, 2013 11:16 am
-
Location:Near Pittsburgh,Pennsylvania. Steel Buckle of the Rust Belt
J,
If I'm getting a good mental picture here, you're basiclly doing a socket weld, correct? If this is correct then I normally light up on the fitting (usually heavier) and as you said just let the pipe be washed in to the mix. You'll have to add filler to the pipe side of the puddle to keep it from undercutting and this helps keep the pipe on the cooler side of things. It also helps to have things set up so you can start welding and then get moving. Keep your heat input as low as possible by moving as fast as possible.
As a side note, whyu use a 309 rod instead of a 308/308L? The 309 is usually reserved for dis-similar metals, but will work in your case, not a terrible thing, just wondering.
Len
If I'm getting a good mental picture here, you're basiclly doing a socket weld, correct? If this is correct then I normally light up on the fitting (usually heavier) and as you said just let the pipe be washed in to the mix. You'll have to add filler to the pipe side of the puddle to keep it from undercutting and this helps keep the pipe on the cooler side of things. It also helps to have things set up so you can start welding and then get moving. Keep your heat input as low as possible by moving as fast as possible.
As a side note, whyu use a 309 rod instead of a 308/308L? The 309 is usually reserved for dis-similar metals, but will work in your case, not a terrible thing, just wondering.
Len
Now go melt something.
Instagram @lenny_gforce
Len
Instagram @lenny_gforce
Len
- J & J Speed Shop
-
New Member
-
Posts:
-
Joined:Wed Sep 03, 2014 11:49 pm
-
Location:Western New York
Thank you both for the replies. I did use the other half of the flange and the clamp to act as a heat sink, but also welding a thicker plate or block would be great. I need to go shopping to the metal supermarket.Braehill wrote:J,
If I'm getting a good mental picture here, you're basiclly doing a socket weld, correct? If this is correct then I normally light up on the fitting (usually heavier) and as you said just let the pipe be washed in to the mix. You'll have to add filler to the pipe side of the puddle to keep it from undercutting and this helps keep the pipe on the cooler side of things. It also helps to have things set up so you can start welding and then get moving. Keep your heat input as low as possible by moving as fast as possible.
As a side note, whyu use a 309 rod instead of a 308/308L? The 309 is usually reserved for dis-similar metals, but will work in your case, not a terrible thing, just wondering.
Len
Len to answer you question yes it is socket weld after looking at a picture on google. So I should keep the arc on the thick flange and add the filler on the pipe side of the puddle. That is great advice and I will try that next. I see different opinions about moving around the work piece and just keep going where I stopped? I will also have to work on my speed a bit. I seem to be moving my foot around alot but I imagine if I get good you can just keep a contact amperage and use the travel speed and filler metal to control the heat/puddle. As for the 309 I know it isn't the correct filler but it is the only thing I had so I rolled with it. Does the 308 weld better?
Example of what I am doing or trying to do nicely
http://www.deedsengineering.com/2014/03/v-band/
- Braehill
-
Weldmonger
-
Posts:
-
Joined:Sat Jul 06, 2013 11:16 am
-
Location:Near Pittsburgh,Pennsylvania. Steel Buckle of the Rust Belt
J,
To the question of does 308L weld better, not better just different, but I think that you'd find that it welds easier on your project because it flows a tiny bit better than 309L. Stainless is inherently sluggish and requires a little manipulation to get it to go where it needs to go as opposed to mild steel. Maybe that's because it's non-magnetic, not sure, just a guess.
Although not required, it wouldn't hurt to have a backpurge anytime you're welding stainless because cooler is better most times, and the Argon or Nitrogen backpurge helps cool the weld as well as sheilding it. Header pipes aren't critical as far as the backside sugaring, but the purge would help for cooling. You can also cool it with compressed air before moving to your next weld to limit heat input.
Using a heavy chunk of metal for a heat sink will also help. If you already have your v-band welded to a plate, weld that plate to a heavier plate, even if it's just carbon steel, your 309 will work perfectly for that.
Len
To the question of does 308L weld better, not better just different, but I think that you'd find that it welds easier on your project because it flows a tiny bit better than 309L. Stainless is inherently sluggish and requires a little manipulation to get it to go where it needs to go as opposed to mild steel. Maybe that's because it's non-magnetic, not sure, just a guess.
Although not required, it wouldn't hurt to have a backpurge anytime you're welding stainless because cooler is better most times, and the Argon or Nitrogen backpurge helps cool the weld as well as sheilding it. Header pipes aren't critical as far as the backside sugaring, but the purge would help for cooling. You can also cool it with compressed air before moving to your next weld to limit heat input.
Using a heavy chunk of metal for a heat sink will also help. If you already have your v-band welded to a plate, weld that plate to a heavier plate, even if it's just carbon steel, your 309 will work perfectly for that.
Len
Now go melt something.
Instagram @lenny_gforce
Len
Instagram @lenny_gforce
Len
- J & J Speed Shop
-
New Member
-
Posts:
-
Joined:Wed Sep 03, 2014 11:49 pm
-
Location:Western New York
LenBraehill wrote:J,
To the question of does 308L weld better, not better just different, but I think that you'd find that it welds easier on your project because it flows a tiny bit better than 309L. Stainless is inherently sluggish and requires a little manipulation to get it to go where it needs to go as opposed to mild steel. Maybe that's because it's non-magnetic, not sure, just a guess.
Although not required, it wouldn't hurt to have a backpurge anytime you're welding stainless because cooler is better most times, and the Argon or Nitrogen backpurge helps cool the weld as well as sheilding it. Header pipes aren't critical as far as the backside sugaring, but the purge would help for cooling. You can also cool it with compressed air before moving to your next weld to limit heat input.
Using a heavy chunk of metal for a heat sink will also help. If you already have your v-band welded to a plate, weld that plate to a heavier plate, even if it's just carbon steel, your 309 will work perfectly for that.
Len
I will just have to buy a few extra flanges in different sizes to make some heat sinks. I didn't back purge this but it is a good idea. I also only got 1 or 2 spots that it go hot enough on the backside to sugar and it came off easily with a flapping wheel. I was also considering welding the inner lip of the flange to the header tube and just going a fusion weld with no filler there. No sure if this is a good or bad idea?
- Braehill
-
Weldmonger
-
Posts:
-
Joined:Sat Jul 06, 2013 11:16 am
-
Location:Near Pittsburgh,Pennsylvania. Steel Buckle of the Rust Belt
I would think that back welding the inside would only add to the warping problem.
Sent from my iPhone using Tapatalk
Sent from my iPhone using Tapatalk
Now go melt something.
Instagram @lenny_gforce
Len
Instagram @lenny_gforce
Len
I would ditch the 1/16" filler in favor of 0.045". To tack, use a super quick burst aimed mostly at the thick side. With enough amperage and a sufficiently quick arc on-time, you don't have to "wash" anything. The key is a SUPER tight arc length, around 0.5mm.
That is a 1.6mm tungsten, so you can have a frame of reference.
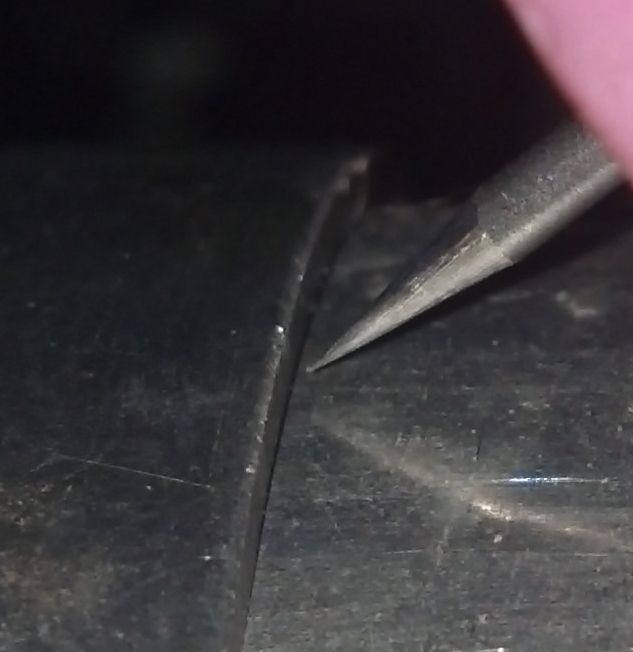
That is a 1.6mm tungsten, so you can have a frame of reference.
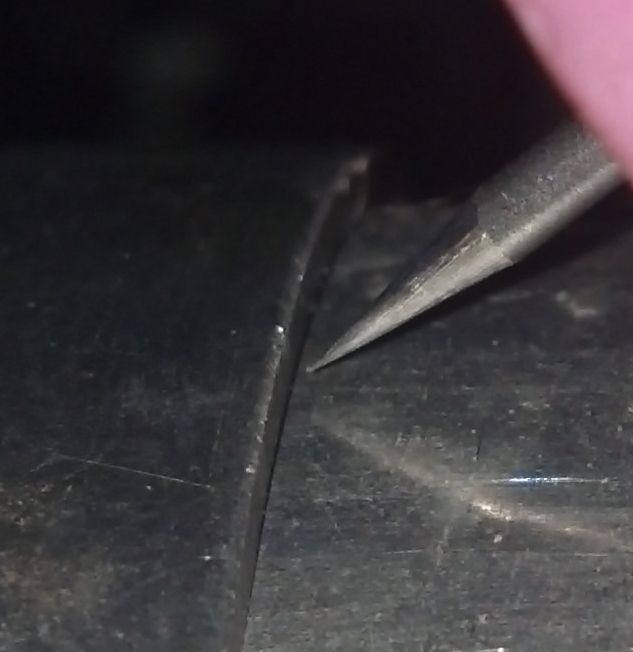
- J & J Speed Shop
-
New Member
-
Posts:
-
Joined:Wed Sep 03, 2014 11:49 pm
-
Location:Western New York
Thank you very much for the advice. I am going down to the LWS and will see if I can purchase some .045" tungsten to try it out. I imagine I should still stick with the 1/16" filler metal?? Trust me I was trying to hold a very tight arc but I need more seat time to get good because super tight I tend to touch the base metal.Oscar wrote:I would ditch the 1/16" filler in favor of 0.045". To tack, use a super quick burst aimed mostly at the thick side. With enough amperage and a sufficiently quick arc on-time, you don't have to "wash" anything. The key is a SUPER tight arc length, around 0.5mm.
That is a 1.6mm tungsten, so you can have a frame of reference.
- weldin mike 27
-
Weldmonger
-
Posts:
-
Joined:Fri Apr 01, 2011 10:59 pm
-
Location:Australia; Victoria
Oscar said, swap to .045 Filler rod, IE mig wire. And have a 1.6mm tungsten. Lots of numbers, easy to get confused.
I know this is beyond what your looking to do but if you really want to get yourself a well sorted heat sink bolt the steel plate you already have the vband fused to on a thick piece of AL. Is you use heat sink paste (buy at any computer store they used them between the processors and fans etc) you will get a good thermal connection between the bits and since AL absorbs heat faster than steel will maybe perform better.
I keep a 12x12x1.5" plate of AL around for just this kind of thing. I also have a thick copper plate I use at time depending on the circumstances.
Just my .02
I keep a 12x12x1.5" plate of AL around for just this kind of thing. I also have a thick copper plate I use at time depending on the circumstances.
Just my .02
- J & J Speed Shop
-
New Member
-
Posts:
-
Joined:Wed Sep 03, 2014 11:49 pm
-
Location:Western New York
Yeah I just caught that thanks, So stick with my 1/16" (1.6mm) tungsten and switch to a smaller filler metal. Can I ask the logic to that? I assume the larger filler metal would chill the puddle more? or is the larger filler harder to melt into the weld?weldin mike 27 wrote:Oscar said, swap to .045 Filler rod, IE mig wire. And have a 1.6mm tungsten. Lots of numbers, easy to get confused.
It's all a balancing act. The larger filler would chill the puddle more, just as you said. But that can have a counter-effect of needing more amperage to keep the puddle fluid, which then heats up the base metal more, and when welding SS, this is of paramount importance. Otherwise you end up with a cold bead that only sits on the top of the weld joint without sufficient penetration. It can be done, but usually when you are able to do this successfully, you won't need to ask on how to do it. A tighter arc length keeps the puddle hot without unnecessarily heating up the surrounding metal. But to do this, you need to be able to feed a thinner filler between the tungsten tip and the puddle, or else you risk fouling up the tungsten if you touch the filler rod to it. I read that a lot of professional exhaust/header builders use 0.030-0.045" filler. This is because they have usually mastered torch manipulation where they can keep the arc length tight, while still attaining proper fusion depth, and feeding in the appropriate amount of filler. Feeding in a smaller filler faster can have the same effect of chilling the puddle to get a well defined bead appearance, without the penalty of trying to squeeze in a larger filler under an already hotter-than-necessary arc.J & J Speed Shop wrote:Yeah I just caught that thanks, So stick with my 1/16" (1.6mm) tungsten and switch to a smaller filler metal. Can I ask the logic to that? I assume the larger filler metal would chill the puddle more? or is the larger filler harder to melt into the weld?weldin mike 27 wrote:Oscar said, swap to .045 Filler rod, IE mig wire. And have a 1.6mm tungsten. Lots of numbers, easy to get confused.
GreinTime
- GreinTime
-
Weldmonger
-
Posts:
-
Joined:Fri Nov 01, 2013 11:20 am
-
Location:Pittsburgh, PA
Have you ever thought about machining a flange out of aluminum? It would be fairly easy with a lathe. A friend of mine has quite a few turned in different sizes for the ones he welds and he just clamps the assembly on there and then has a little brace underneath to hold the collector level while he welds it.
#oneleggedproblems
-=Sam=-
-=Sam=-
GreinTime
- GreinTime
-
Weldmonger
-
Posts:
-
Joined:Fri Nov 01, 2013 11:20 am
-
Location:Pittsburgh, PA
- uploadfromtaptalk1423813466516.png (554.62 KiB) Viewed 3650 times
#oneleggedproblems
-=Sam=-
-=Sam=-
That's a good idea for me to produce! I just need to learn how to use my new Lathe/Mill/Drill machineGreinTime wrote:Have you ever thought about machining a flange out of aluminum? It would be fairly easy with a lathe. A friend of mine has quite a few turned in different sizes for the ones he welds and he just clamps the assembly on there and then has a little brace underneath to hold the collector level while he welds it.

- Superiorwelding
-
Weldmonger
-
Posts:
-
Joined:Thu Jan 24, 2013 10:13 pm
-
Location:Eddy, TX
Or use your new fancy Street or Strip Concept back purge kit!!GreinTime wrote:The one pictured above has a 1/8npt barb in it for purging as well, then you would only have to put foil over the ends or whatever.
-Jonathan
Instagram- @superiorwelding/@learntotig
Twitter- @_JonathanLewis
https://www.learntotig.com
https://www.superiorweldandfab.com
https://www.youtube.com/+SuperiorWeldin ... ATHANLEWIS
Twitter- @_JonathanLewis
https://www.learntotig.com
https://www.superiorweldandfab.com
https://www.youtube.com/+SuperiorWeldin ... ATHANLEWIS
GreinTime
- GreinTime
-
Weldmonger
-
Posts:
-
Joined:Fri Nov 01, 2013 11:20 am
-
Location:Pittsburgh, PA
Well yeah, I would you clown lol. I don't have any of the flanges turned to v-bands, although I could probably use the lathe at the school pretty easily to make some.
#oneleggedproblems
-=Sam=-
-=Sam=-
I tried that (using MIG wire) as TIG filler by straightening, and it's just too much hassle. www.weldingsupply.com has TIG filler rod in 0.045" straight-cut lengths, in all sorts of flavors. "Filler Metal Queen" on Ebay sells 10lbs boxes of 308L 0.045" TIG filler rod at reasonable pricing.weldin mike 27 wrote:Oscar said, swap to .045 Filler rod, IE mig wire. And have a 1.6mm tungsten. Lots of numbers, easy to get confused.
Turbocripple
- Turbocripple
-
New Member
-
Posts:
-
Joined:Wed Apr 19, 2017 4:02 pm
Sorry to bump an old thread, however while searching for information on v band welding I came across a solution that looks very promising. It is a two sided purge block and heat sink that attaches to the v band with the standard coupler. Hope that helps, Follow the link below
http://www.streetorstripconcept.com/bac ... -tools.php
http://www.streetorstripconcept.com/bac ... -tools.php
Return to “Tig Welding - Tig Welding Aluminum - Tig Welding Techniques - Aluminum Tig Welding”
Jump to
- Introductions & How to Use the Forum
- ↳ Welcome!
- ↳ Member Introductions
- ↳ How to Use the Forum
- ↳ Moderator Applications
- Welding Discussion
- ↳ Metal Cutting
- ↳ Tig Welding - Tig Welding Aluminum - Tig Welding Techniques - Aluminum Tig Welding
- ↳ Mig and Flux Core - gas metal arc welding & flux cored arc welding
- ↳ Stick Welding/Arc Welding - Shielded Metal Arc Welding
- ↳ Welding Forum General Shop Talk
- ↳ Welding Certification - Stick/Arc Welding, Tig Welding, Mig Welding Certification tests - Welding Tests of all kinds
- ↳ Welding Projects - Welding project Ideas - Welding project plans
- ↳ Product Reviews
- ↳ Fuel Gas Heating
- Welding Tips & Tricks
- ↳ Video Discussion
- ↳ Wish List
- Announcements & Feedback
- ↳ Forum News
- ↳ Suggestions, Feedback and Support
- Welding Marketplace
- ↳ Welding Jobs - Industrial Welding Jobs - Pipe Welding Jobs - Tig Welding Jobs
- ↳ Classifieds - Buy, Sell, Trade Used Welding Equipment
- Welding Resources
- ↳ Tradeshows, Seminars and Events
- ↳ The Welding Library
- ↳ Education Opportunities