Here's my settings
2mm thick aluminum tubing not sure what type
1/16 ER5356 filler
Gas lens #8 cup
3/32 2% Ceriated Tungsten
Argon 20cfh
60amps
Below are some pics of how I did on the surface of tubing.
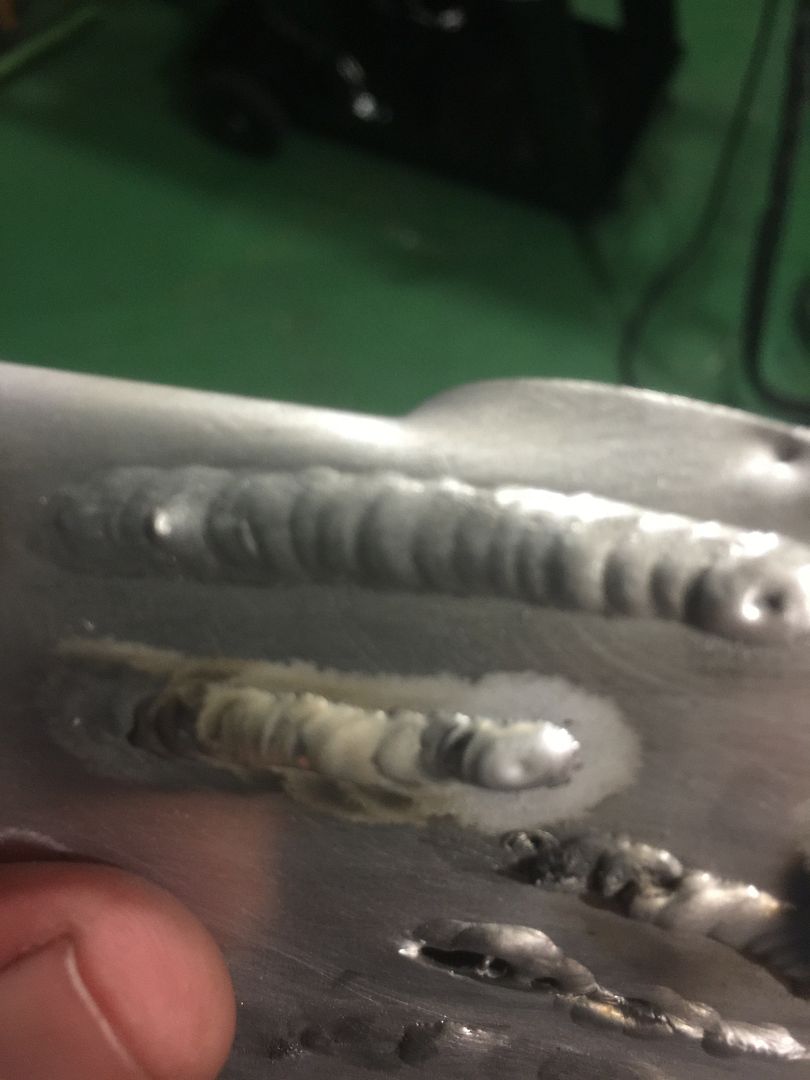
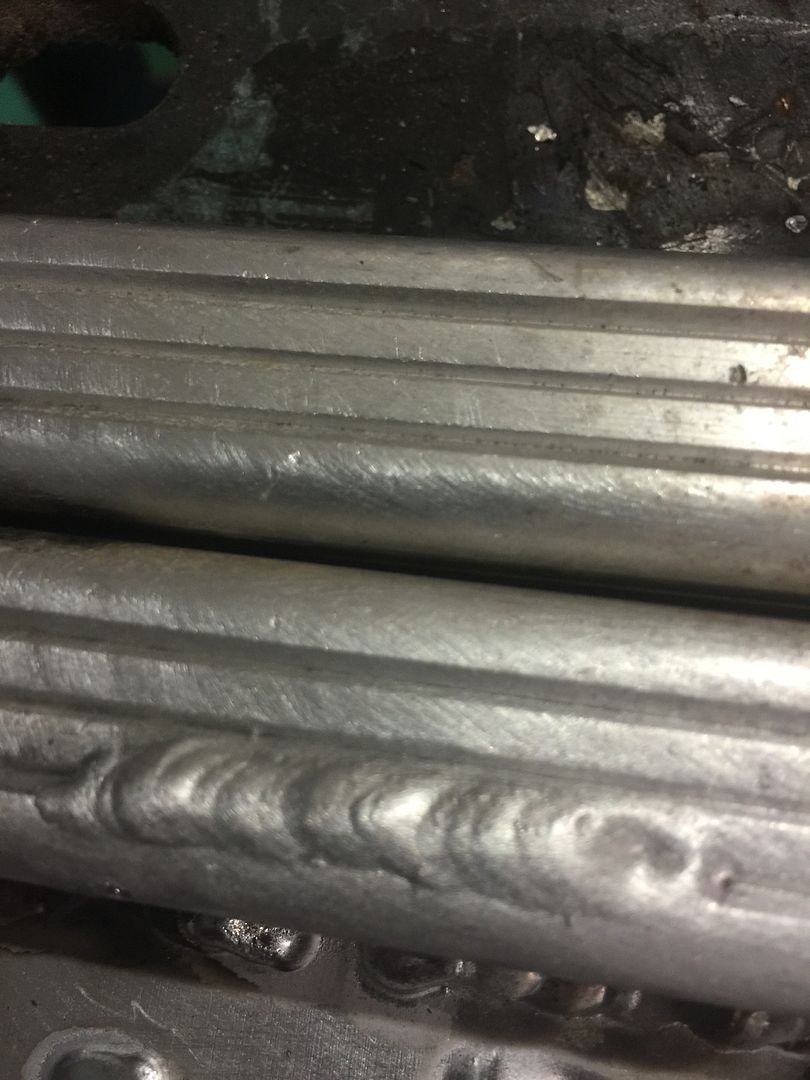
Thank you, Shipj0 for posting these comments! I really like when students interact with each other and share stories and experiences. For my part, I learned to weld so darn long ago that I don't remember the struggles and issues that noobs face. It is one thing to watch video of Jody doing it, then quite another thing to actually go and get the same result. This is a problem that more experienced guys have; they don't recall what it is like to be a noob. Also, being a noob is not just lacking the welding skills, it is learning all of the other things that go along with the welding skills. Just learning the language or being in the environment is a challenge!shipj0 wrote:So I am a Newbie too; so this is like a 2nd grader explaining Algebra to a 1st grader but here are some things that I have done that helped.
1. Keep a journal and write down settings, what your welding and results. Really nice to have when something works and you want to repeat it a week later.
2. Get a small piece of filler rod and practice feeding it through your hand until it is second nature. This is one of the single best things I did to improve my TIG welding. It also makes long and boring meetings more bearable.
3. Start with some thicker Aluminum, I used 3/16 flat and 1/8 for joints.
4. Get a 10" x 10" sheet and do the welding drill, I got a scrap piece at my local weld shop where I buy all the stuff to support my addiction. For practice, you will probably use around 110 amps on flat metal as a start point. I think I got down to 80 amps at one point when the metal got hot. The TIG Fingers do work very well.
5. Start by using about 85% EN for practice. It's clean aluminum and scrap anyways and the better penetration makes practice easier. Also, when you touch the tungsten, which you will, the aluminum doesn't jump to the tungsten so bad. When practicing, unless I touched the tungsten bad enough to affected the arc significantly, I just kept welding.
6. Practice welding to music or count seconds so you get a rhythm for moving forward and adding filler.
7. As a gauge for practice, with a torch switch if your puddle doesn't form within about 3 seconds, you don't have enough amps, if it forms much faster than 2 seconds your too hot. With a foot pedal you have more control but I used a torch switch to start practicing and have just started with a foot pedal. Have trouble doing three things at once.
Here are the settings I used on my last project for an 1/8"x1/8" outside corner joint just for an example. Preflow-0.5s, Start Amps-50, Upslope-3s, Weld Amps-130, Freq-130, DCEN-85%, Downslope-5s, End Amps-5, Postflow-5s, Argon 18cfm, #6 cup, 3/32" 5356 rod, 3/32" 2% Lanthanated Tungsten. Used torch switch and upslope / downslope to control heat.
Yes I am using a foot pedal.I kind of have a hook up for argon through my job.big gear head wrote:Gordian, you didn't mention a foot pedal. Are you using one? If not then that's going to make it harder for you to learn.
Practice will make you better. You can't practice too much. I know that argon is expensive, but weld as much as you can afford. I've been TIG welding for 30 years, but I still practice when I have time. I just get some scrap pieces and start welding in every direction.
Thanks for your advice.I have been laying beads down and will continue to until it because second nature and I know exactly what torch is going to do.i need to practice edges as I keep blowing out material.i have a diversion 180 so I'm limited on settings.shipj0 wrote:So I am a Newbie too; so this is like a 2nd grader explaining Algebra to a 1st grader but here are some things that I have done that helped.
1. Keep a journal and write down settings, what your welding and results. Really nice to have when something works and you want to repeat it a week later.
2. Get a small piece of filler rod and practice feeding it through your hand until it is second nature. This is one of the single best things I did to improve my TIG welding. It also makes long and boring meetings more bearable.
3. Start with some thicker Aluminum, I used 3/16 flat and 1/8 for joints.
4. Get a 10" x 10" sheet and do the welding drill, I got a scrap piece at my local weld shop where I buy all the stuff to support my addiction. For practice, you will probably use around 110 amps on flat metal as a start point. I think I got down to 80 amps at one point when the metal got hot. The TIG Fingers do work very well.
5. Start by using about 85% EN for practice. It's clean aluminum and scrap anyways and the better penetration makes practice easier. Also, when you touch the tungsten, which you will, the aluminum doesn't jump to the tungsten so bad. When practicing, unless I touched the tungsten bad enough to affected the arc significantly, I just kept welding.
6. Practice welding to music or count seconds so you get a rhythm for moving forward and adding filler.
7. As a gauge for practice, with a torch switch if your puddle doesn't form within about 3 seconds, you don't have enough amps, if it forms much faster than 2 seconds your too hot. With a foot pedal you have more control but I used a torch switch to start practicing and have just started with a foot pedal. Have trouble doing three things at once.
Here are the settings I used on my last project for an 1/8"x1/8" outside corner joint just for an example. Preflow-0.5s, Start Amps-50, Upslope-3s, Weld Amps-130, Freq-130, DCEN-85%, Downslope-5s, End Amps-5, Postflow-5s, Argon 18cfm, #6 cup, 3/32" 5356 rod, 3/32" 2% Lanthanated Tungsten. Used torch switch and upslope / downslope to control heat.
First, I would pat myself on the back, have a shot of Jameson, and enjoy a little success - that group of beads looks quite improved. There are plenty of frustrations still to come but that is part of the fun of succeeding so don't forget to celebrate.Gordian79 wrote:Thanks for your advice.I have been laying beads down and will continue to until it because second nature and I know exactly what torch is going to do.i need to practice edges as I keep blowing out material.i have a diversion 180 so I'm limited on settings.
Like that practice plate. Looks like a cityscape. Think I may try something like that.big gear head wrote:Gordian, you didn't mention a foot pedal. Are you using one? If not then that's going to make it harder for you to learn.
Practice will make you better. You can't practice too much. I know that argon is expensive, but weld as much as you can afford. I've been TIG welding for 30 years, but I still practice when I have time. I just get some scrap pieces and start welding in every direction.
I'm going to try that I figure that happens because as I'm welding the piece gets hotter so I won't need as much heat.big gear head wrote:When you get close to an edge you need to back off on the pedal. Pay close attention to the width of the bead and when it starts getting wider back off on the heat. Pulsing works very well and is something that you should practice. Push the pedal down and get a puddle started, dip the rod and let it melt in, then back off of the pedal without loosing the arc. Then move forward just a little and do the same thing again. It's kind of like making a bunch of tack welds connected together. This works very well around edges. Also there is nothing wrong with making short welds, repositioning your hands and starting back where you stopped.
Return to “Tig Welding - Tig Welding Aluminum - Tig Welding Techniques - Aluminum Tig Welding”