Tig welding tips, questions, equipment, applications, instructions, techniques, tig welding machines, troubleshooting tig welding process
Hollywood1
- Hollywood1
-
Ace
-
Posts:
-
Joined:Mon Feb 23, 2015 9:05 am
-
Location:Washington
Do you have to bend part of the aluminum for a fuel cell so the welds will not possibly crack? Saw this somewhere on the internet and was hoping someone could shed some light here. Thanks, John.
Hollywood1
- Hollywood1
-
Ace
-
Posts:
-
Joined:Mon Feb 23, 2015 9:05 am
-
Location:Washington
And if so , how do you bend the the 1/8th inch aluminum without an expensive 3000 dollar bender?
I wouldn't see why...are you talking about a specific section, sump, top etc?
What alum alloy are you using? 6061 you can bend with a nice radius, 90° will even work. 50xx series alum will bens even easier and be less prone to cracking.
I bend it all on a brake.
What alum alloy are you using? 6061 you can bend with a nice radius, 90° will even work. 50xx series alum will bens even easier and be less prone to cracking.
I bend it all on a brake.
I weld stainless, stainless and more stainless...Food Industry, sanitary process piping, vessels, whatever is needed, I like to make stuff.
ASME IX, AWS 17.1, D1.1
Instagram #RNHFAB
ASME IX, AWS 17.1, D1.1
Instagram #RNHFAB
- TRACKRANGER
-
Weldmonger
-
Posts:
-
Joined:Wed Aug 06, 2014 12:48 am
-
Location:Melbourne, Australia
Sometimes because of the way aluminum sheet is rolled, it can essentially have a 'grain'. If you try to bend along the grain it might 'tear', but if you bend across the grain, it's fine.
Bending without a bender is a little tricky, but it's possible to rig up something with blocks of wood. 1/8" thick is challenging though. Does it really need to be such heavy walled?
There's a couple of ideas on YT etc:
xQlHqdudPvU
0DP8Doywrwg
Also:
http://www.homediystuff.com/making-diy- ... al-bender/
Bending without a bender is a little tricky, but it's possible to rig up something with blocks of wood. 1/8" thick is challenging though. Does it really need to be such heavy walled?
There's a couple of ideas on YT etc:
xQlHqdudPvU
0DP8Doywrwg
Also:
http://www.homediystuff.com/making-diy- ... al-bender/
EWM Phonenix 355 Pulse MIG set mainly for Aluminum, CIGWeld 300Amp AC/DC TIG, TRANSMIG S3C 300 Amp MIG, etc, etc
Hollywood1
- Hollywood1
-
Ace
-
Posts:
-
Joined:Mon Feb 23, 2015 9:05 am
-
Location:Washington
Was planning on using 5052. Maybe .090 would be thick enough. I don't mind welding extra, but it would be cool if I could bend it. Most of the 200 dollar or less benders only do .020 mild steel from what I can find.
- MosquitoMoto
-
Weldmonger
-
Posts:
-
Joined:Sat Aug 01, 2015 8:38 am
-
Location:The Land Down Under
I am making up a little sheet metal brake this weekend using pretty heavy steel plate and angle. I'd love if it was able to bend aluminium up to 3mm as I use this thickness for various motorcycle brackets quite often.
If I have any success with this thicker stuff after the build, I'll post up some pics.
Kym
If I have any success with this thicker stuff after the build, I'll post up some pics.
Kym
Hollywood1
- Hollywood1
-
Ace
-
Posts:
-
Joined:Mon Feb 23, 2015 9:05 am
-
Location:Washington
Hollywood1
- Hollywood1
-
Ace
-
Posts:
-
Joined:Mon Feb 23, 2015 9:05 am
-
Location:Washington
Are people bending so they don't have to weld as much or is there another reason as well such as welds cracking easier possibly?
Both..Hollywood1 wrote:Are people bending so they don't have to weld as much or is there another reason as well such as welds cracking easier possibly?
Also when possible get dead soft alum or temper before bending,as mentioned be aware of grain.
3xxx or 11xx series dead soft for fab is one choice
some hints
http://www.amazon.com/Metal-Fabricators ... 0895868709
http://www.woodwardfab.com/product/metal-work-basics/
http://www.woodwardfab.com/media/
some pics when done PLEASE
Everlast 250EX
Miller 250 syncrowave
Sharp LMV Vertical Mill
Takisawa TSL-800-D Lathe
Coupla Bandsaws,Grinders,surface grinder,tool/cutter grinder
and more stuff than I deserve(Thanks Significant Other)
Miller 250 syncrowave
Sharp LMV Vertical Mill
Takisawa TSL-800-D Lathe
Coupla Bandsaws,Grinders,surface grinder,tool/cutter grinder
and more stuff than I deserve(Thanks Significant Other)
Hollywood1
- Hollywood1
-
Ace
-
Posts:
-
Joined:Mon Feb 23, 2015 9:05 am
-
Location:Washington
- Superiorwelding
-
Weldmonger
-
Posts:
-
Joined:Thu Jan 24, 2013 10:13 pm
-
Location:Eddy, TX
I do both on my fuel tanks. I try to have as much formed as possible to keep the labor time down. Usually I am welding up fuel tanks for experimental aircraft so they are in the .030-.100 range and almost always 3003. Be careful with the 6061 as it really shouldn't be bent and will break/crack, especially with a tight radius.
Rick, I have never been successful when bending 6061. What kind of radius are you using to successfully bend it 90 degrees?
-Jonathan
Rick, I have never been successful when bending 6061. What kind of radius are you using to successfully bend it 90 degrees?
-Jonathan
Instagram- @superiorwelding/@learntotig
Twitter- @_JonathanLewis
https://www.learntotig.com
https://www.superiorweldandfab.com
https://www.youtube.com/+SuperiorWeldin ... ATHANLEWIS
Twitter- @_JonathanLewis
https://www.learntotig.com
https://www.superiorweldandfab.com
https://www.youtube.com/+SuperiorWeldin ... ATHANLEWIS
Hollywood1
- Hollywood1
-
Ace
-
Posts:
-
Joined:Mon Feb 23, 2015 9:05 am
-
Location:Washington
Is it structurally okay to just weld all six pieces if you don't mind the extra labor time? Is the rumor true about welds crack easier?
- Superiorwelding
-
Weldmonger
-
Posts:
-
Joined:Thu Jan 24, 2013 10:13 pm
-
Location:Eddy, TX
I'm not sure who told you the welds "crack easier" but I would like a better explanation of that. There are a few scenarios I can think of where this could be possible but unlikely. If you deposit sound welds I would not worry about that at all. And you used the appropriate filler for the base material. Maybe they are speaking of welding 6061 with 5356 and the fact that the 5356 is more prone to cracking, but again there are ways around that. I can also see cracking as an issue if the both the design of the tank and however it is held down were poor, such as putting the tank in a place where is will see stress and load it should not see.
Weld it up and you will be fine.
-Jonathan
Weld it up and you will be fine.
-Jonathan
Instagram- @superiorwelding/@learntotig
Twitter- @_JonathanLewis
https://www.learntotig.com
https://www.superiorweldandfab.com
https://www.youtube.com/+SuperiorWeldin ... ATHANLEWIS
Twitter- @_JonathanLewis
https://www.learntotig.com
https://www.superiorweldandfab.com
https://www.youtube.com/+SuperiorWeldin ... ATHANLEWIS
Hollywood1
- Hollywood1
-
Ace
-
Posts:
-
Joined:Mon Feb 23, 2015 9:05 am
-
Location:Washington
Okay thanks for the info. Ill be using 5052 material with 5356 filler. I appreciate all the help. John
- big gear head
-
Ace
-
Posts:
-
Joined:Thu May 07, 2015 11:46 am
-
Location:KY.
Welding 6 pieces is fine, but there is more heat put into it and there is more of a chance of a leak in a weld. Your welds look pretty good and you may not have any problems with leaks. When I was learning I tried to build a fuel cell for my car and I ended up with several leaks in the welds, and it warped a lot. Mine pretty well looked like crap, and I didn't use it. I've still got it sitting on a shelf in my shop.
Freddie
The reommendation to NOT corner weld aluminum tanks comes from the drag racing community. They recommend bending all the corners so the welds are on straight joints. Not required but recommended. There have been a lot of tank weld joints crack. There is some very severe vibrations in some of the high powered vehicles.
Jim
Jim
Most tanks are strapped in a cradle where severe vibration is a problem. Look under most road vehicles fuel tanks.jauguston wrote:The reommendation to NOT corner weld aluminum tanks comes from the drag racing community. They recommend bending all the corners so the welds are on straight joints. Not required but recommended. There have been a lot of tank weld joints crack. There is some very severe vibrations in some of the high powered vehicles.
Jim
Everlast 250EX
Miller 250 syncrowave
Sharp LMV Vertical Mill
Takisawa TSL-800-D Lathe
Coupla Bandsaws,Grinders,surface grinder,tool/cutter grinder
and more stuff than I deserve(Thanks Significant Other)
Miller 250 syncrowave
Sharp LMV Vertical Mill
Takisawa TSL-800-D Lathe
Coupla Bandsaws,Grinders,surface grinder,tool/cutter grinder
and more stuff than I deserve(Thanks Significant Other)
I was bending 3/16" 6061 diamond plate, 1/4" radius, and I was bending with the grain..I'll snap some pics tomorrow. Typically I won't go over around 45° with 6061 especially in 1/4"+ or it will crack nearly every time.Superiorwelding wrote:I do both on my fuel tanks. I try to have as much formed as possible to keep the labor time down. Usually I am welding up fuel tanks for experimental aircraft so they are in the .030-.100 range and almost always 3003. Be careful with the 6061 as it really shouldn't be bent and will break/crack, especially with a tight radius.
Rick, I have never been successful when bending 6061. What kind of radius are you using to successfully bend it 90 degrees?
-Jonathan
I've welded up all 6 sides on a air to water cooler tank I made years ago, mounted next to a fuel tank in he back of a 8 second fox body with no issues. I do try to bend as much as I can for aesthetics, strength and less welding/heat distortion to worry about.
I weld stainless, stainless and more stainless...Food Industry, sanitary process piping, vessels, whatever is needed, I like to make stuff.
ASME IX, AWS 17.1, D1.1
Instagram #RNHFAB
ASME IX, AWS 17.1, D1.1
Instagram #RNHFAB
- Otto Nobedder
-
Weldmonger
-
Posts:
-
Joined:Thu Jan 06, 2011 11:40 pm
-
Location:Near New Orleans
6063 bends beautifully.
I've bent sch. 40 1/2" pipe to a 4" radius without mandrels, sand, or even shaped u-blocks. Did it around a flange bolted to a table.
6061 has several conditions of temper. T-1 bends pretty well until it work-hardens (and can be annealed). T-6 will not bend worth a crap unless you anneal it first.
6061 will work-harden, and age-harden, so it's still a usable alloy, but it would not be my first choice for a fuel tank.
Steve S
I've bent sch. 40 1/2" pipe to a 4" radius without mandrels, sand, or even shaped u-blocks. Did it around a flange bolted to a table.
6061 has several conditions of temper. T-1 bends pretty well until it work-hardens (and can be annealed). T-6 will not bend worth a crap unless you anneal it first.
6061 will work-harden, and age-harden, so it's still a usable alloy, but it would not be my first choice for a fuel tank.
Steve S
dirtmidget33
- dirtmidget33
-
Heavy Hitter
-
Posts:
-
Joined:Tue May 13, 2014 5:22 pm
I don't mean to take away the fun of you building a tank and I am only offering some info and advice in case you are not aware. If you are looking for a true "fuel cell" there is more than just the metal container. A fuel cell has a flexible rubber type bladder inside a plastic tank and this gets bolted into another box. Now there are various designs some just have the plastic tank with bladder mounted inside. Sprint, midget, champ cars set up like this others have The bladder, plastic, metal or carbon fiber tank. The whole point of the cell is during a wreck the outer casing can get smashed even ripped apart, but the fuel is contained in the flexible bladder. I have personally smashed fuel tanks on midgets all the way back to my cage and bladder stretched and deformed without braking. The metal container itself should never have fuel in it at all if it does your bladder is leaking. Bladders are fuel dependent and made for type of fuel you intend to use, alcohol, gas, nitro, etc. Military airplanes use these same type of bladders with an added self sealing rubber compound. If you really want a true fuel cell suggest buying one as no small shop or backyard shop will have what you need to make the flexible bladder. I have used ones from a company called fuel safe located in Oregon. They can make it out of any material shape you desire. Now if you just want a custom aluminum fuel tank that is not a fuel cell go for it. Just realize this is not a true racing fuel cell and is no better than a factory metal or plastic fuel tank.
Like I said don't want to ruin your project but just inform you. Will gladly answer questions about the tanks with info I know if you have any. There are several manufacturers for these I suggested one I personally used for many years and they have a good reputation in Indy, USAC,POWRI, NASCAR, Score, and many others. I just don't want to see anyone get burnt or hurt in race cars if they can avoid it. I have lost friends, and both dad and me have been severely hurt in cars by odd ball wrecks.you never know what can happen. Simpson had to change a safety device cause it had a massive failure in one of my wrecks that they never would have foreseen. Luckily the failure didn't add to injuries but it could have. No guarantees of coming back once you strap into a race car.
Like I said don't want to ruin your project but just inform you. Will gladly answer questions about the tanks with info I know if you have any. There are several manufacturers for these I suggested one I personally used for many years and they have a good reputation in Indy, USAC,POWRI, NASCAR, Score, and many others. I just don't want to see anyone get burnt or hurt in race cars if they can avoid it. I have lost friends, and both dad and me have been severely hurt in cars by odd ball wrecks.you never know what can happen. Simpson had to change a safety device cause it had a massive failure in one of my wrecks that they never would have foreseen. Luckily the failure didn't add to injuries but it could have. No guarantees of coming back once you strap into a race car.
why use standard nozzles after gas lens where invented. Kinda of like starting fires by rubbing sticks together.
Hollywood1
- Hollywood1
-
Ace
-
Posts:
-
Joined:Mon Feb 23, 2015 9:05 am
-
Location:Washington
Type in fuel cell at Jegs or Summit Racing and you'll come up with both aluminum and steel cans with bladders. Rci makes both but still calls them fuel cells. Most of my drag racing buddies all have aluminum boxes with fuel in them. I guess there is a lot of people misusing the term.
I've welded quite a few tanks in my time and repaired my share of cracked welds on tanks as well. The problem with most failed welds is that many people, in spite of their welding skills, do not know how to set up a proper open corner and maintain the same reveal throughout as it is being welded. You don't want to be able to see the sheared edge of the joint on the interior, as this can telegraph through as an eventual crack. In other words, weld penetration should go through the corner completely and the weld should peak through on the inside so that the crisp edge on the interior is fused as well.
Also, there are other reasons for using a break, such as, cross breaking the panels to avoid oil canning as the fuel inside, heats and cools, or gets sloshed around, even with baffles welded in and to add rigidity to larger panels. Many sheet metal suppliers will have the ability to bend the panels for you for less than you can weld them for realistically.
This is how I usually order my parts, and will often order flanges bent on the baffles as well so I don;t have to weld both sides of them. It ends up saving me hours and with less distortion to the tank sides.
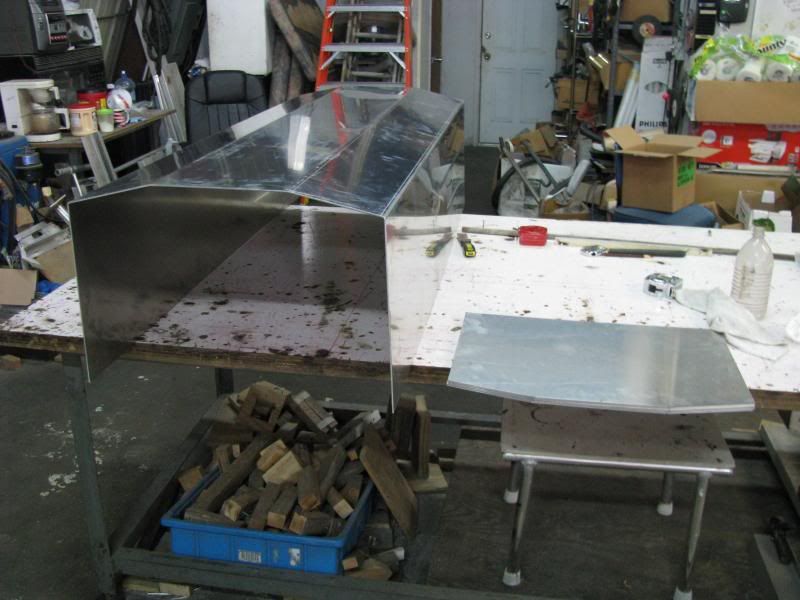
Then I set up the corners precisely for tacks, and then if they suck in too tight, I will expand the tacks with a cold chisel until the proper gap is set.
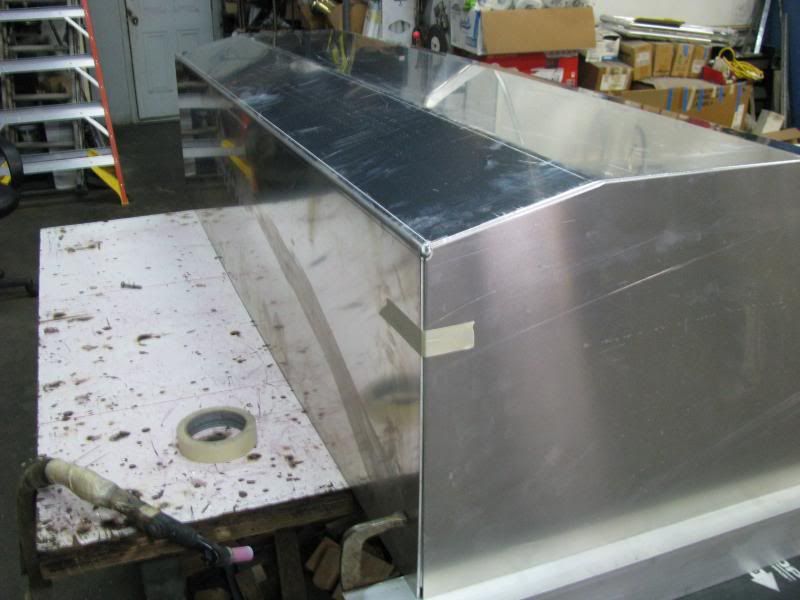
Then I keyhole weld the corners so that the resultant weld is at a 45 degree to the faces, with a good bead of penetration on the inside corners. I have never had one of my welds crack, and distortion of the panels is minimal.
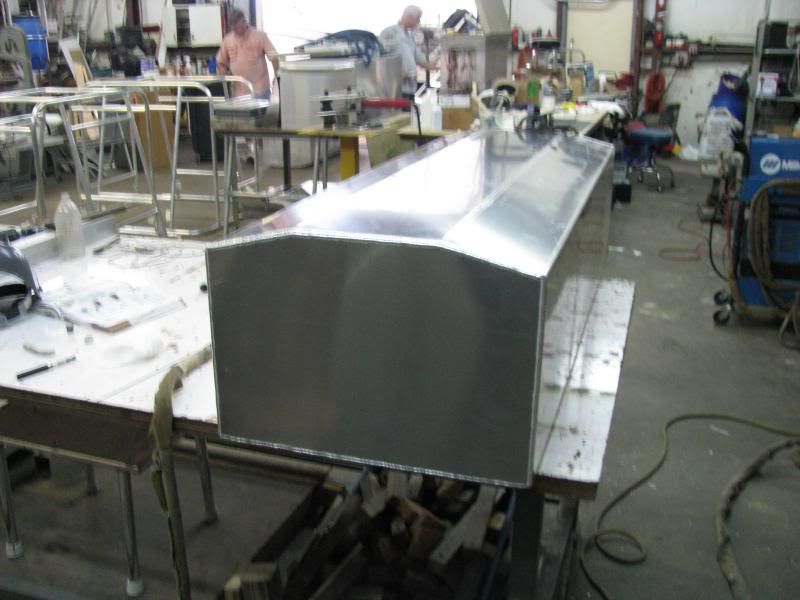
Then they are pressure tested to 5 psi and checked for leaks with soapy water. At any rate, the welds are robust and drawn in such a way so that there is no notable fatigue edge where the edges of the welds meet the panels.
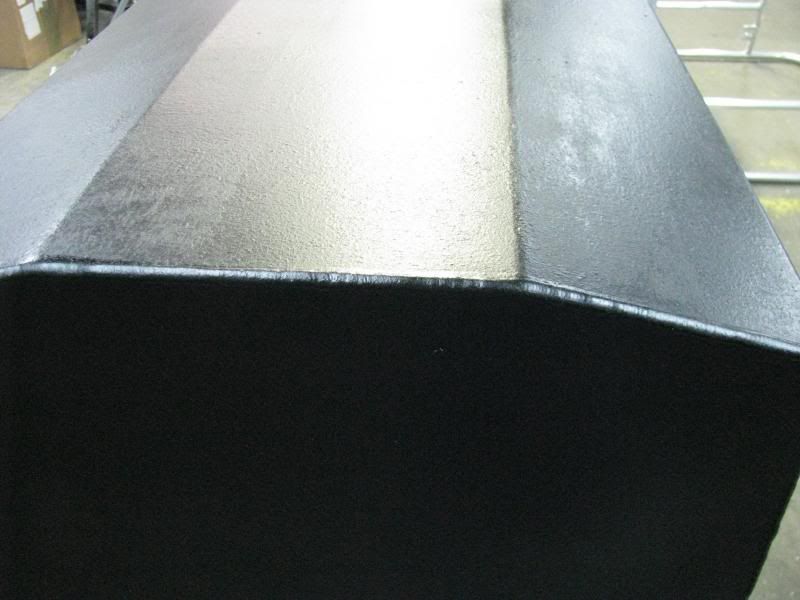
Also, there are other reasons for using a break, such as, cross breaking the panels to avoid oil canning as the fuel inside, heats and cools, or gets sloshed around, even with baffles welded in and to add rigidity to larger panels. Many sheet metal suppliers will have the ability to bend the panels for you for less than you can weld them for realistically.
This is how I usually order my parts, and will often order flanges bent on the baffles as well so I don;t have to weld both sides of them. It ends up saving me hours and with less distortion to the tank sides.
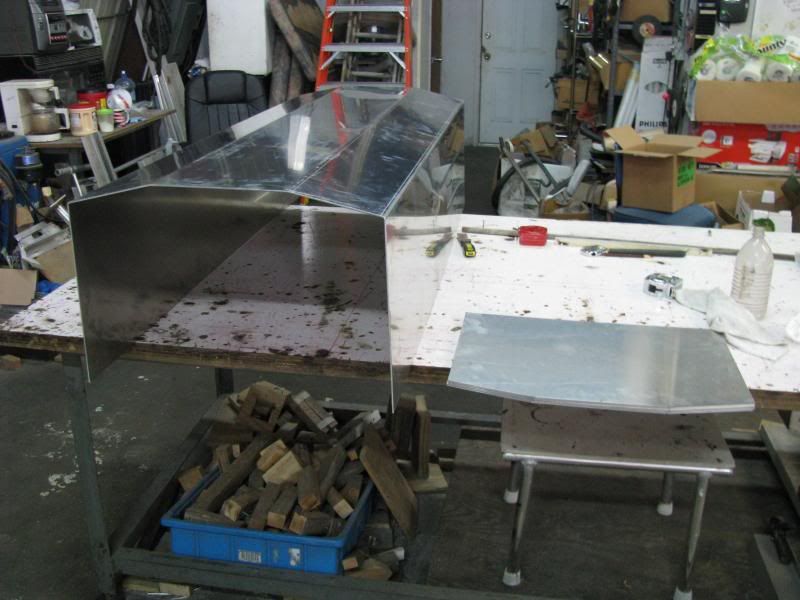
Then I set up the corners precisely for tacks, and then if they suck in too tight, I will expand the tacks with a cold chisel until the proper gap is set.
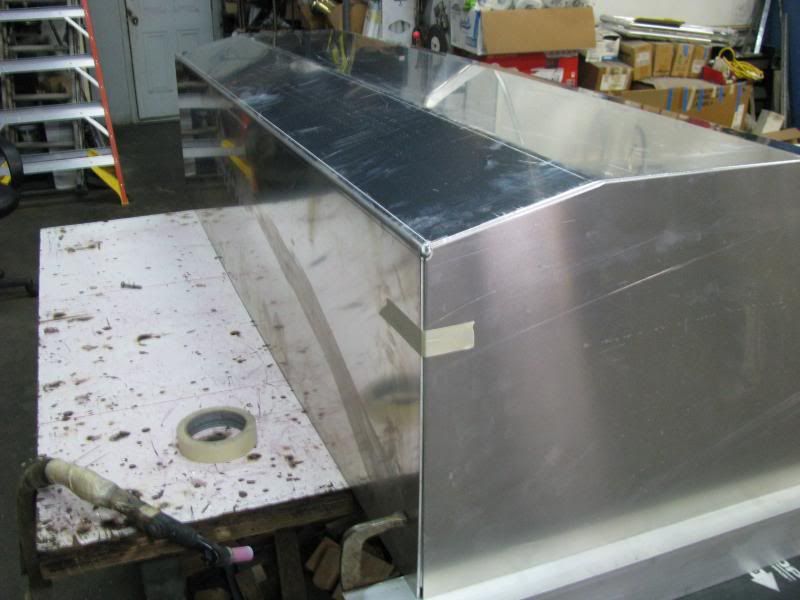
Then I keyhole weld the corners so that the resultant weld is at a 45 degree to the faces, with a good bead of penetration on the inside corners. I have never had one of my welds crack, and distortion of the panels is minimal.
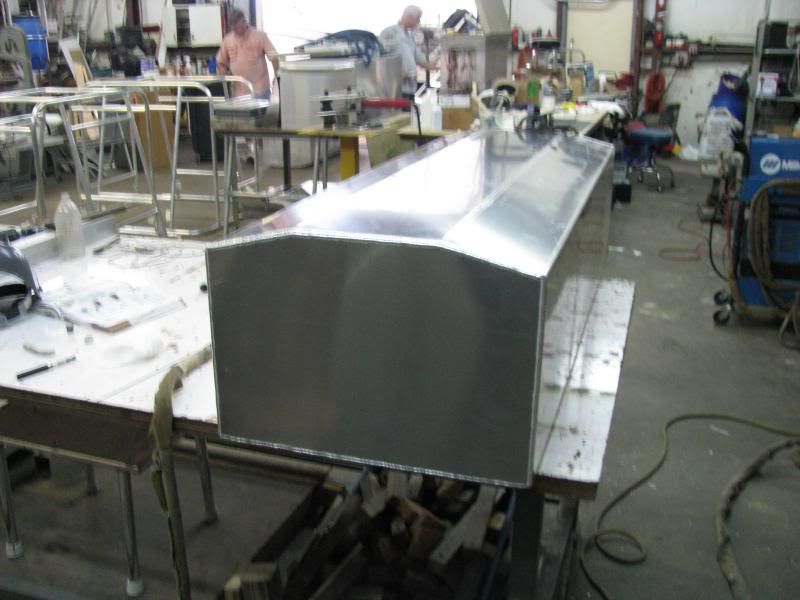
Then they are pressure tested to 5 psi and checked for leaks with soapy water. At any rate, the welds are robust and drawn in such a way so that there is no notable fatigue edge where the edges of the welds meet the panels.
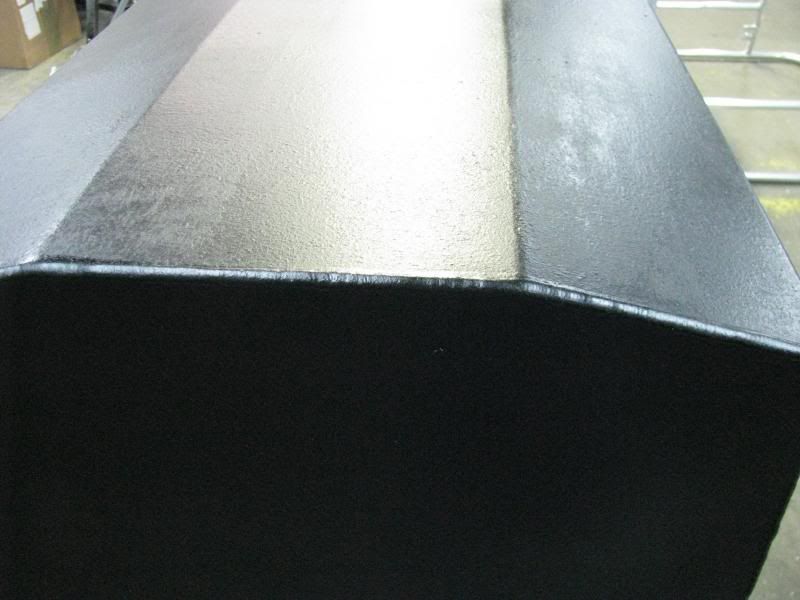
Miller ABP 330, Syncrowave 250, Dynasty 300 DX.
Honorary member of the Fraternity of Faded Tee Shirts.
Honorary member of the Fraternity of Faded Tee Shirts.
- big gear head
-
Ace
-
Posts:
-
Joined:Thu May 07, 2015 11:46 am
-
Location:KY.
Tamjeff, you sure do nice work. That looks great. I'd be very proud to have a tank like that in the back of my Camaro. I may have to give this another try sometime and replace my plastic Jazz fuel cell.
Freddie
- Otto Nobedder
-
Weldmonger
-
Posts:
-
Joined:Thu Jan 06, 2011 11:40 pm
-
Location:Near New Orleans
I'll remind everyone that TamJeff has extensive experience with aluminum, including difficult alloys and surface treatments.
You CAN build a fuel tank like this, but unless you have a bore-scope to examine the inside corners, you should do much practice first on scraps you can examine the back side of. With fuel, contained in the same vehicle you're riding, you want high confidence. The visible surface finish of the welds is only a cosmetic issue, and does not reflect the quality of the weld.
Steve S
You CAN build a fuel tank like this, but unless you have a bore-scope to examine the inside corners, you should do much practice first on scraps you can examine the back side of. With fuel, contained in the same vehicle you're riding, you want high confidence. The visible surface finish of the welds is only a cosmetic issue, and does not reflect the quality of the weld.
Steve S
Return to “Tig Welding - Tig Welding Aluminum - Tig Welding Techniques - Aluminum Tig Welding”
Jump to
- Introductions & How to Use the Forum
- ↳ Welcome!
- ↳ Member Introductions
- ↳ How to Use the Forum
- ↳ Moderator Applications
- Welding Discussion
- ↳ Metal Cutting
- ↳ Tig Welding - Tig Welding Aluminum - Tig Welding Techniques - Aluminum Tig Welding
- ↳ Mig and Flux Core - gas metal arc welding & flux cored arc welding
- ↳ Stick Welding/Arc Welding - Shielded Metal Arc Welding
- ↳ Welding Forum General Shop Talk
- ↳ Welding Certification - Stick/Arc Welding, Tig Welding, Mig Welding Certification tests - Welding Tests of all kinds
- ↳ Welding Projects - Welding project Ideas - Welding project plans
- ↳ Product Reviews
- ↳ Fuel Gas Heating
- Welding Tips & Tricks
- ↳ Video Discussion
- ↳ Wish List
- Announcements & Feedback
- ↳ Forum News
- ↳ Suggestions, Feedback and Support
- Welding Marketplace
- ↳ Welding Jobs - Industrial Welding Jobs - Pipe Welding Jobs - Tig Welding Jobs
- ↳ Classifieds - Buy, Sell, Trade Used Welding Equipment
- Welding Resources
- ↳ Tradeshows, Seminars and Events
- ↳ The Welding Library
- ↳ Education Opportunities