Tig welding tips, questions, equipment, applications, instructions, techniques, tig welding machines, troubleshooting tig welding process
Chris Wilson
- Chris Wilson
-
New Member
-
Posts:
-
Joined:Mon May 19, 2014 10:09 am
I have seen a commercially available automotive turbo manifold cast in nodular cast iron, with a conversion from a troublesome bolted wastegate adapter to a TIG welded on stainless steel tubular adapter. I am assuming it's stainless from the colour change by the weld. Is this a recognised pair of material for TIG welding? I could use a mild steel flange if TIG welding mild steel to cast iron is a better junction. Any tips as to how to do this? Form the looks of the manifold it wasn't done in a muffle oven... Many thanks, great site, and great videos from Jody!
- TRACKRANGER
-
Weldmonger
-
Posts:
-
Joined:Wed Aug 06, 2014 12:48 am
-
Location:Melbourne, Australia
ChrisChris Wilson wrote:I have seen a commercially available automotive turbo manifold cast in nodular cast iron, with a conversion from a troublesome bolted wastegate adapter to a TIG welded on stainless steel tubular adapter. I am assuming it's stainless from the colour change by the weld. Is this a recognised pair of material for TIG welding? I could use a mild steel flange if TIG welding mild steel to cast iron is a better junction. Any tips as to how to do this? Form the looks of the manifold it wasn't done in a muffle oven... Many thanks, great site, and great videos from Jody!
Jody's your man, he's even got a video for you that should get you in position at least:
jJg5RcljNao
Trev
EWM Phonenix 355 Pulse MIG set mainly for Aluminum, CIGWeld 300Amp AC/DC TIG, TRANSMIG S3C 300 Amp MIG, etc, etc
Chris Wilson
- Chris Wilson
-
New Member
-
Posts:
-
Joined:Mon May 19, 2014 10:09 am
Thanks, I will watch this fully tonight. Here is a photo (not great, but the best I can get) of how the flange is welded on the commercial version. It looks more like a weld than a braze, what do you reckon? This is not to say it's good or correct of course!
Companies can turn out iffy welds just as well as I can <LOL> Would a mild steel flange be easier / better for welding? There's no NEED for it to be stanless. Thanks. 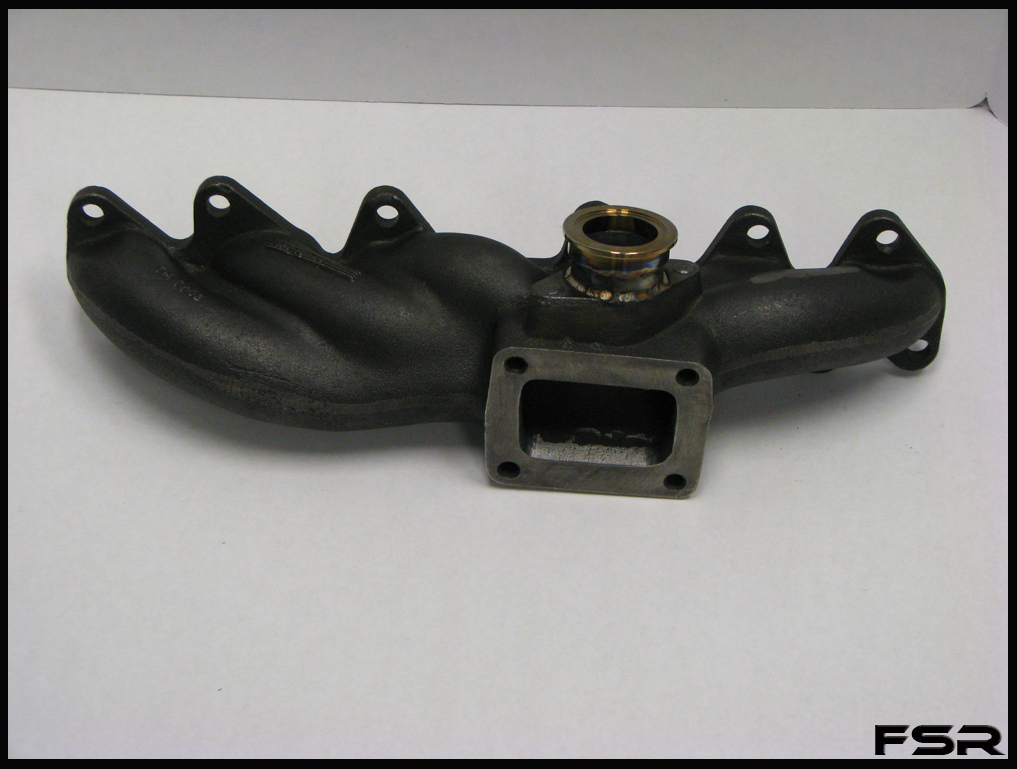

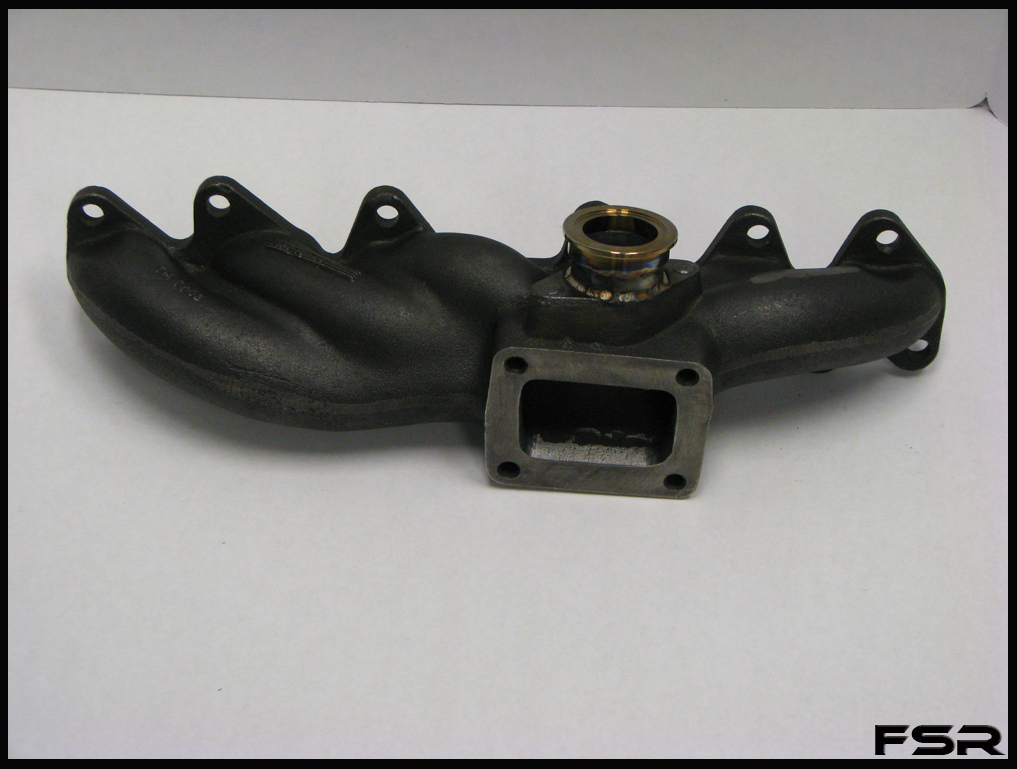
- big gear head
-
Ace
-
Posts:
-
Joined:Thu May 07, 2015 11:46 am
-
Location:KY.
There is going to be a lot of heat in that area. I don't know if the aluminum bronze will hold up to that.
Freddie
Chris Wilson
- Chris Wilson
-
New Member
-
Posts:
-
Joined:Mon May 19, 2014 10:09 am
Indeed, on the engine dyno bright red hot, for sure, and probably close to that with some under bonnet air flow, i am wondering too, if the braze would weaken or melt at those elevated temperatures. If they'd spent a bit more and cast in high nickel content cast iron welding wouldn't be such an issue. But apparently they are nodular cast iron construction.
The example photo does seem to show a 2-piece setup with a short pipe welded onto the manifold and then a stainless V-band flange on the pipe.
The pipe may well be mild steel and welded to the cast iron with a high-nickel based filler rod and then perhaps the (stainless) flange welded onto the pipe with 309?
That should at least make the transition between the materials a little more gradual as far as properties go.
Still.. The manifold shown does seem to have OEM bosses for studs for a bolt-on wastegate, so personally I'd sooner look into an adapter that's bolted onto the manifold on 1 end and has a V-band flange (I assume to fit a TIAL or similar wastegate) on the other.
Avoids all the issues with material differences completely. Bolts/studs will probably need to be inconel though if you don't want them to lose strenght and loosen under the high heat.
Bye, Arno.
The pipe may well be mild steel and welded to the cast iron with a high-nickel based filler rod and then perhaps the (stainless) flange welded onto the pipe with 309?
That should at least make the transition between the materials a little more gradual as far as properties go.
Still.. The manifold shown does seem to have OEM bosses for studs for a bolt-on wastegate, so personally I'd sooner look into an adapter that's bolted onto the manifold on 1 end and has a V-band flange (I assume to fit a TIAL or similar wastegate) on the other.
Avoids all the issues with material differences completely. Bolts/studs will probably need to be inconel though if you don't want them to lose strenght and loosen under the high heat.
Bye, Arno.
Welder2008
- Welder2008
-
New Member
-
Posts:
-
Joined:Thu Jul 30, 2015 6:27 pm
Are you wanting to modify an existing manifold to attach a turbo to? Not sure what you're trying to accomplish. Any brazing operation would certainly fail due to the fact that copper/bronze alloys can not be put into service at those temperatures much less adding some back pressure from the exhaust. I would match a flange made from a high nickel-based alloy such as 625 inconel or AL6XN and weld it with 625 or hatelloy W filler. Clean cast iron manifold and preheat to 550 degrees Fahrenheit before welding and allow it to cool wrapped in a fiberglass weld blanket.
- Braehill
-
Weldmonger
-
Posts:
-
Joined:Sat Jul 06, 2013 11:16 am
-
Location:Near Pittsburgh,Pennsylvania. Steel Buckle of the Rust Belt
I don't know what exhaust temps get to in a gasoline engine, but I'm pretty sure that they're nowhere near the 1675*F melting point of bronze. The highest I've seen on a truck's pyrometer is in the neighborhood of 1200*F and that's with a bad injector, usually in the <1000*F range. They're mounted in the turbo outlet pipe though.
I don't disagree with what's been said, just saying what I've seen in my experience.
I'm in the better bolt flange camp on this one unless there's something we're not privy too that makes it fail.
Len
I don't disagree with what's been said, just saying what I've seen in my experience.
I'm in the better bolt flange camp on this one unless there's something we're not privy too that makes it fail.
Len
Now go melt something.
Instagram @lenny_gforce
Len
Instagram @lenny_gforce
Len
Return to “Tig Welding - Tig Welding Aluminum - Tig Welding Techniques - Aluminum Tig Welding”
Jump to
- Introductions & How to Use the Forum
- ↳ Welcome!
- ↳ Member Introductions
- ↳ How to Use the Forum
- ↳ Moderator Applications
- Welding Discussion
- ↳ Metal Cutting
- ↳ Tig Welding - Tig Welding Aluminum - Tig Welding Techniques - Aluminum Tig Welding
- ↳ Mig and Flux Core - gas metal arc welding & flux cored arc welding
- ↳ Stick Welding/Arc Welding - Shielded Metal Arc Welding
- ↳ Welding Forum General Shop Talk
- ↳ Welding Certification - Stick/Arc Welding, Tig Welding, Mig Welding Certification tests - Welding Tests of all kinds
- ↳ Welding Projects - Welding project Ideas - Welding project plans
- ↳ Product Reviews
- ↳ Fuel Gas Heating
- Welding Tips & Tricks
- ↳ Video Discussion
- ↳ Wish List
- Announcements & Feedback
- ↳ Forum News
- ↳ Suggestions, Feedback and Support
- Welding Marketplace
- ↳ Welding Jobs - Industrial Welding Jobs - Pipe Welding Jobs - Tig Welding Jobs
- ↳ Classifieds - Buy, Sell, Trade Used Welding Equipment
- Welding Resources
- ↳ Tradeshows, Seminars and Events
- ↳ The Welding Library
- ↳ Education Opportunities