Tig welding tips, questions, equipment, applications, instructions, techniques, tig welding machines, troubleshooting tig welding process
I have seen a lot of race car related aluminum welds on thin material where the weld bead seems very wide or large , however burn through on the back side is non existent. Specifically on pit pal products ( utility trays and the like from 16 gage). How do they accomplish this. I would normally use wire size same as material thickness ( 1/16 in this case) Do you think a larger filler wire would give this effect?
You'll probably need a backing plate. Stainless or copper. If you have an inverter welder then triangle mode is designed for welding thin aluminum. Clamp it down good or its will bow up on you. You might wanna try pulsing with the peddle too.
Raymond
Everlast PowerTIG 255EXT
Everlast PowerTIG 255EXT
If you can, turning the frequency down helps too. Here's a pic of when I was goofing around with frequency. The narrow bead is 200 or 400 I forget now, the wide is like 40.
- welding-frequency.png (380.41 KiB) Viewed 1856 times
Wide bead width with little backside fusion can be a result of AC frequency and/or EP/EN percentage.
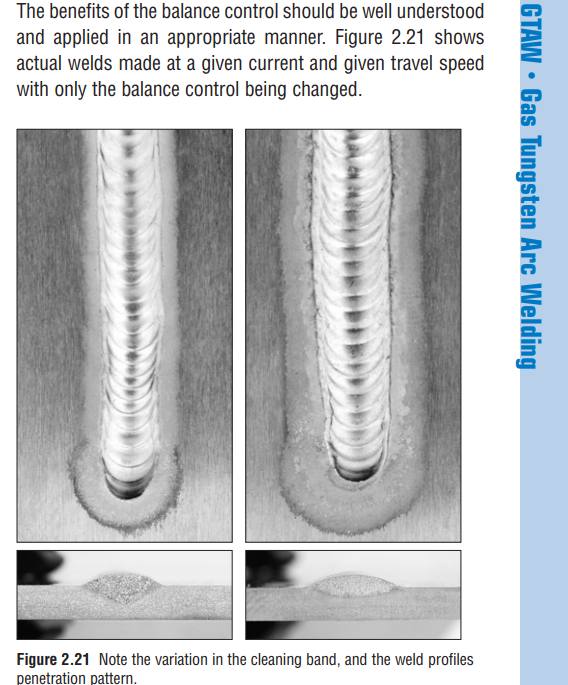
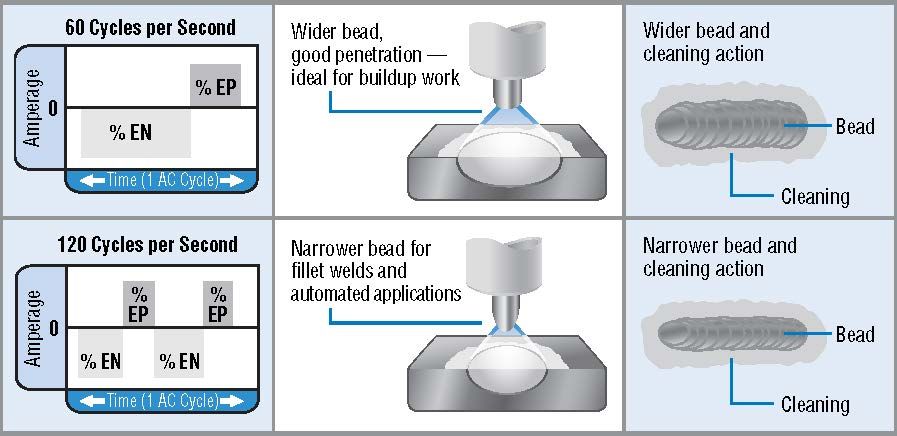
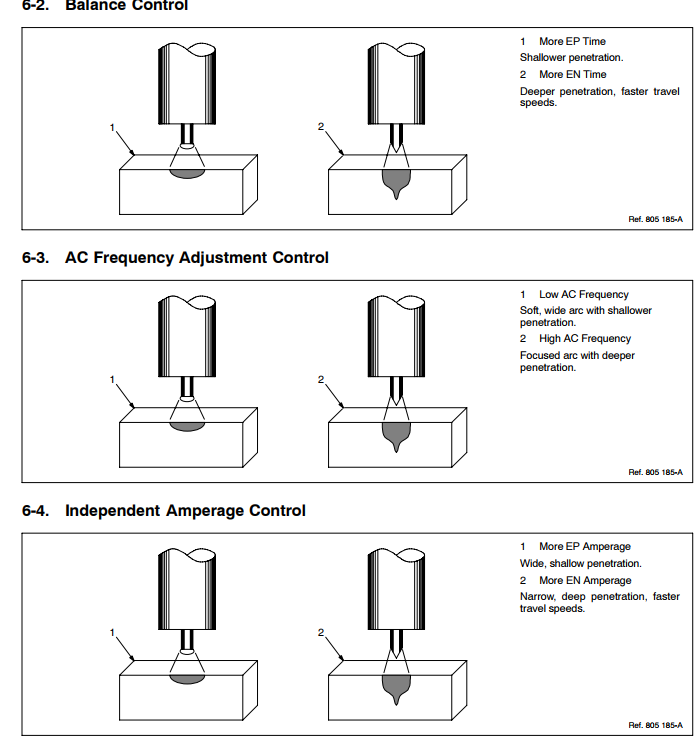
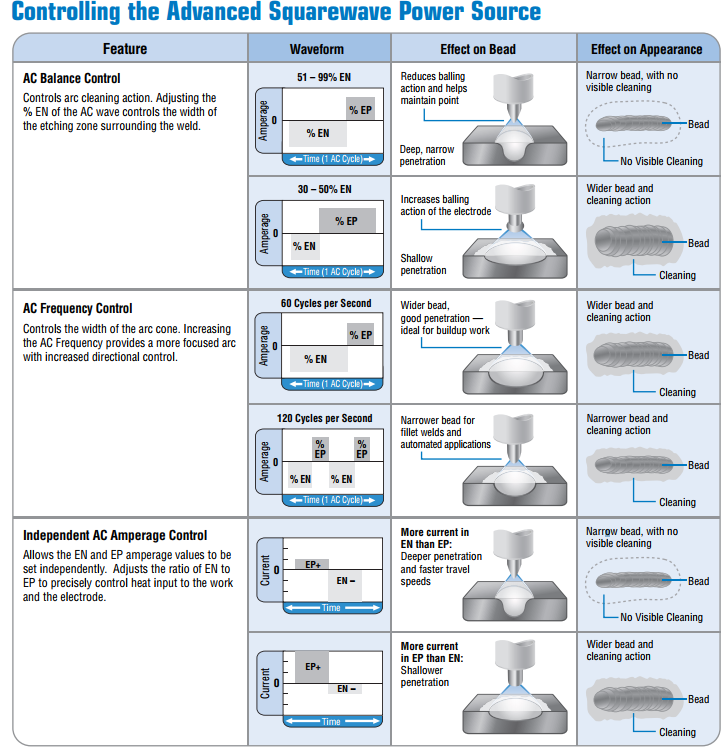
- AC Frequency
- Lower = Wider bead with less penetration
- Higher = Narrower bead with increased penetration
- AC Balance (with respect to bead width)
- Higher EN% = increased penetration with a slight side-effect of narrower bead
- Lower EN% = less penetration with a slight side-effect of wider bead.
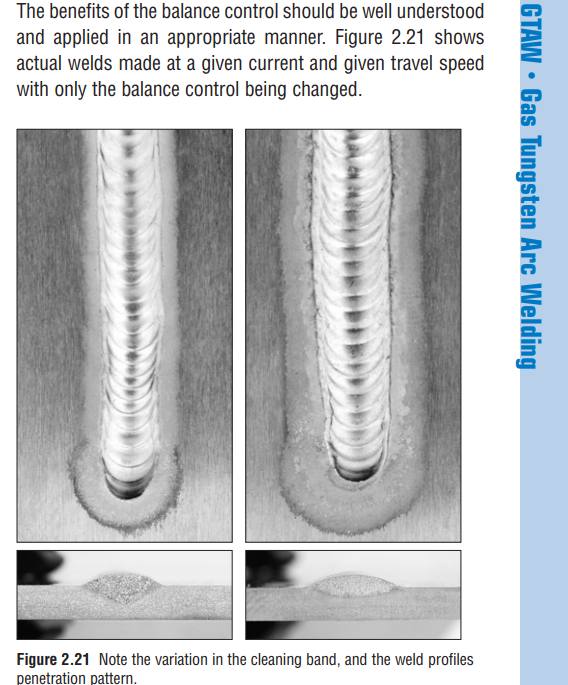
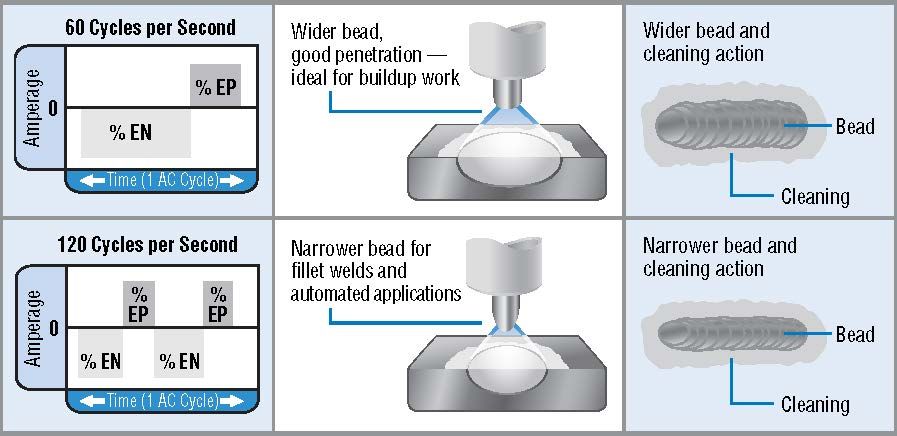
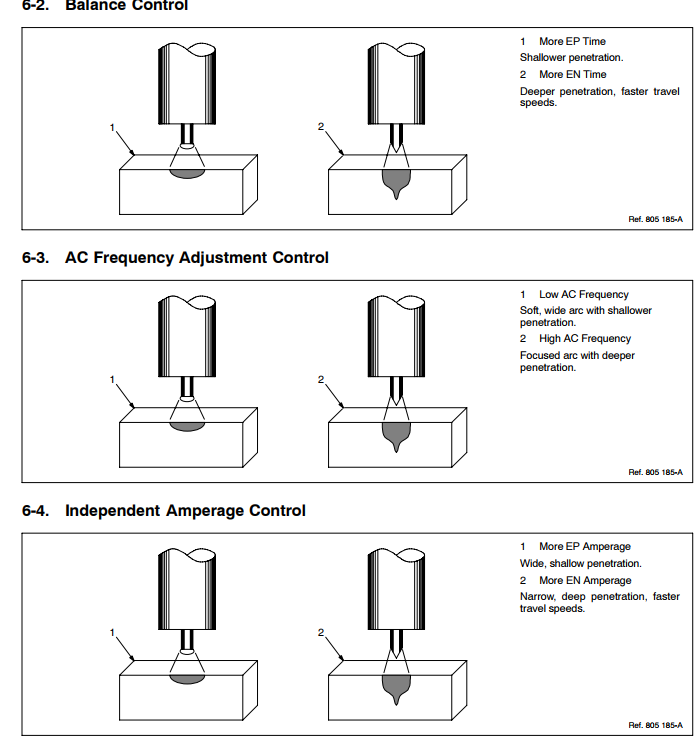
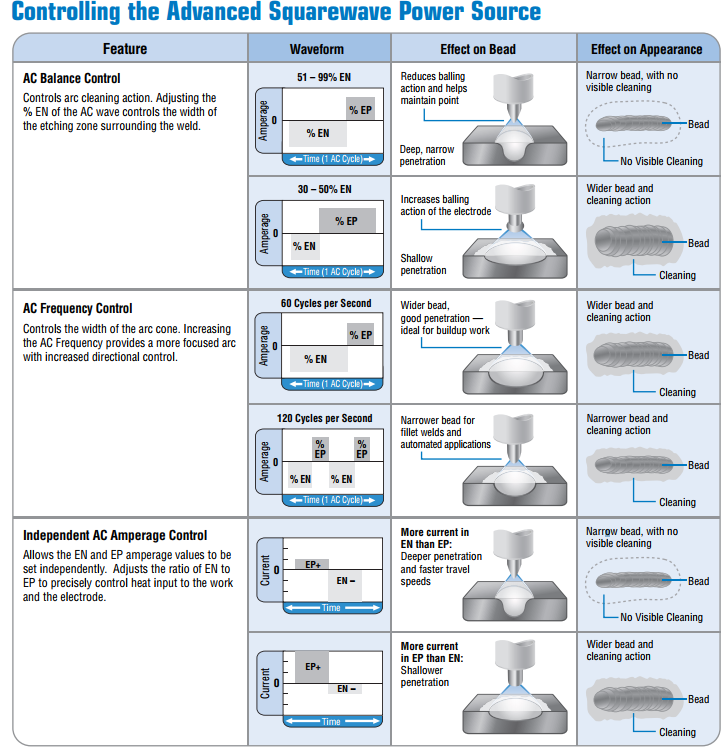
Great info Oscar. The only thing I'd add is that tip shape has a dramatic impact on melt pool width as well. A sharp point will produce a shallower and wider pool then a ball or blunt point. I agree with a backing plate being the way to go but a perfect set up requires pretty much all of this stuff to be at least considered.
-Sandow
-Sandow
Red-hot iron, white-hot iron, cold-black iron; an iron taste, an iron smell, and a babel of iron sounds.
-Charles Dickens
-Charles Dickens
ajlskater1
- ajlskater1
-
Ace
-
Posts:
-
Joined:Thu Feb 02, 2012 5:32 am
You can accomplish that appearance if you pulse foot pedal as you dip and back off quickly after or use pulse function on the machine but I prefer to manually do it, I get better timing being in control vs a machine telling you when to dip.
- 20150220_212120.jpg (56.59 KiB) Viewed 1697 times
Ask and you shall receive...Sandow wrote:Great info Oscar. The only thing I'd add is that tip shape has a dramatic impact on melt pool width as well. A sharp point will produce a shallower and wider pool then a ball or blunt point. I agree with a backing plate being the way to go but a perfect set up requires pretty much all of this stuff to be at least considered.
-Sandow
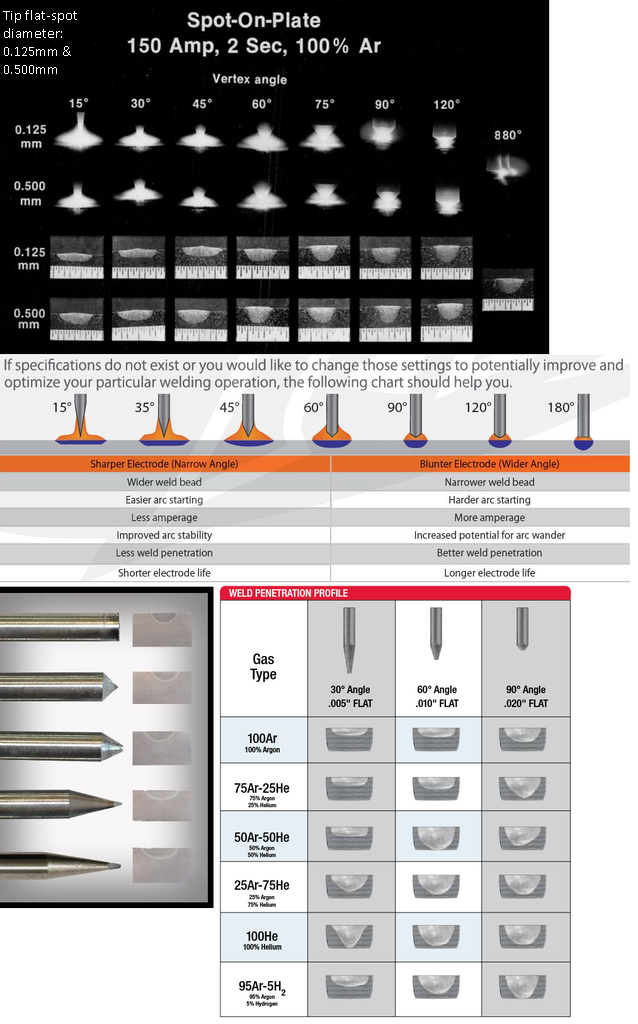
Last edited by Oscar on Fri Jul 08, 2016 10:53 pm, edited 1 time in total.
"Oscars'" posts.



Everlast 250EX
Miller 250 syncrowave
Sharp LMV Vertical Mill
Takisawa TSL-800-D Lathe
Coupla Bandsaws,Grinders,surface grinder,tool/cutter grinder
and more stuff than I deserve(Thanks Significant Other)
Miller 250 syncrowave
Sharp LMV Vertical Mill
Takisawa TSL-800-D Lathe
Coupla Bandsaws,Grinders,surface grinder,tool/cutter grinder
and more stuff than I deserve(Thanks Significant Other)
Return to “Tig Welding - Tig Welding Aluminum - Tig Welding Techniques - Aluminum Tig Welding”
Jump to
- Introductions & How to Use the Forum
- ↳ Welcome!
- ↳ Member Introductions
- ↳ How to Use the Forum
- ↳ Moderator Applications
- Welding Discussion
- ↳ Metal Cutting
- ↳ Tig Welding - Tig Welding Aluminum - Tig Welding Techniques - Aluminum Tig Welding
- ↳ Mig and Flux Core - gas metal arc welding & flux cored arc welding
- ↳ Stick Welding/Arc Welding - Shielded Metal Arc Welding
- ↳ Welding Forum General Shop Talk
- ↳ Welding Certification - Stick/Arc Welding, Tig Welding, Mig Welding Certification tests - Welding Tests of all kinds
- ↳ Welding Projects - Welding project Ideas - Welding project plans
- ↳ Product Reviews
- ↳ Fuel Gas Heating
- Welding Tips & Tricks
- ↳ Video Discussion
- ↳ Wish List
- Announcements & Feedback
- ↳ Forum News
- ↳ Suggestions, Feedback and Support
- Welding Marketplace
- ↳ Welding Jobs - Industrial Welding Jobs - Pipe Welding Jobs - Tig Welding Jobs
- ↳ Classifieds - Buy, Sell, Trade Used Welding Equipment
- Welding Resources
- ↳ Tradeshows, Seminars and Events
- ↳ The Welding Library
- ↳ Education Opportunities