Hi Folks,
I am relatively new to TIG, and am practicing welding some 18GA, 3" 304SS Stainless Exhaust Tubing. I am using 1/16 2% Lanthanated Tungsten, .04" Filler (308L?). Backpurging with Argon, #8 Gas Lens, ~15CFH flow rate. I think my peak amperage on the welder is set @ 35A
I know that I need to practice and work on my consistency, but the problem I don't seem to understand is that I appear to be "outrunning" my gas coverage in certain scenarios. For example, if I weld a 4" bead around the diameter of the tubing, the first 3" might turn that dull grey color, where the last inch where I stop welding will remain covered by my post-flow shielding gas, and end up a nice gold / colored shiny color.
Any hints for this? It seems obvious that the metal is still too hot when the shielding gas stops covering it. Do I need less torch angle so more of the gas flows "backward" over the portion of the tubing that I just welded? Move faster with higher amperage? Move slower? More gas flow? Different size cup?
Thanks for the help.
Tig welding tips, questions, equipment, applications, instructions, techniques, tig welding machines, troubleshooting tig welding process
- weldin mike 27
-
Weldmonger
-
Posts:
-
Joined:Fri Apr 01, 2011 10:59 pm
-
Location:Australia; Victoria
Hi there,
Yep try less torch angle, around 25degrees or if you think of the pipe as a clock, 11 or 1 o'clock. Also, only have the tungsten sticking out of the torch as little as possible. no more than 3mm.
Mick
Yep try less torch angle, around 25degrees or if you think of the pipe as a clock, 11 or 1 o'clock. Also, only have the tungsten sticking out of the torch as little as possible. no more than 3mm.
Mick
ajlskater1
- ajlskater1
-
Ace
-
Posts:
-
Joined:Thu Feb 02, 2012 5:32 am
It sounds to me like you mayb welding to slow and over heating the material. When you finish your bead if you are holding the torch over the weld until the post flow runs out, that will cause that last bit of the weld to turn out really nice and color because the weld is sheilded until it has time to cool. What works for me when welding 18 ga 304 is about 60 to 70 amps with a number 7 or 8 diffuser cup and about 20 to 25 cfh on the gas flow depending on the weld. For t joints I like to use a lower cfh and for butt or outside corner joints I the to run 25. I would probly recommend trying some thicker material if you have any available until you get your speed up. Welding thin stainless takes some preactice.
ajlskater1
- ajlskater1
-
Ace
-
Posts:
-
Joined:Thu Feb 02, 2012 5:32 am
One other thing that might help is jody has a video about tungsten stick out lengths and how to figure out if you are getting proper sheilding with the tungsten stick out you are using. I don't hjave the link to it. I know he used a piece of titanium, obviously not everyone had that but a peice of 304 works as well. And another way to tell is your tungsten is out to far is to look at it after you are done welding it should remain nice and silverly, not blue or grey. Hope that helps.
After some more practice last night, I am beginning to think this is my problem. When first starting out, I might get a nice section or two when welding a butt joint between two pieces of 18GA/.049" 304SS. But, as I progress (and as the tubing retains more heat?) I get more and more of the dull grey welds. I've also noticed the metal staying red fairly long at the end of my weld while I'm letting the post-gas run.ajlskater1 wrote:It sounds to me like you mayb welding to slow and over heating the material. When you finish your bead if you are holding the torch over the weld until the post flow runs out, that will cause that last bit of the weld to turn out really nice and color because the weld is sheilded until it has time to cool. What works for me when welding 18 ga 304 is about 60 to 70 amps with a number 7 or 8 diffuser cup and about 20 to 25 cfh on the gas flow depending on the weld.
So, what's the best way to practice avoiding this? Up until now, I've been using about 35-40 peak amps on the welder, starting full bore to get the puddle, and then trying to use the pedal and travel speed to control the puddle as I feed filler. I have not had any problem with burn through, if anything, maybe too much build up and not enough penetration in cases. You mentioned 60-70Amps peak - Sounds like I should I practice with a higher amperage and trying to get my speed up?
I'll see if I can take some pictures next time...
Thanks again for the help.
RedIron881
- RedIron881
-
Workhorse
-
Posts:
-
Joined:Fri Mar 23, 2012 9:29 am
-
Location:Phoenix, AZ
Another thing to keep in mind is as your welding you should be backing off on the pedal (here and there) to keep the heat a little more under control. Once the metal is hot it just get hotter! Moving faster and lightly backing off on the amps as you go (as needed) will help.
Practice makes Perfect
Practice makes Perfect
I think the "don't overdo the torch angle" is good advice, and also the "try hotter and faster" is good advise.
What "hotter and faster" means by the way, is use *more* current to melt the puddle faster, and in turn, move the torch more quickly (you need the manual skills with moving the torch and adding filling rod when necessary, which is where practice comes in) and in the end you will end up inputting *less* heat energy than if you used less current (which is sort of counter-intuitive result, but it's the way it works.)
If it's sitting there red hot for very long (like say 10+ seconds) after you stop the arc, then yeah you are really roasting it.
Another thing you can do is weld it in stitches (short lengths), and give it time to cool down in between stitches. Stainless conducts away heat very slowly. Bathing both sides of it in Argon doesn't help because argon conducts heat away very poorly also. Although it will keep it from oxidizing.
Also, check out this video; his results welding stainless tubing are excellent:
http://www.everlastgenerators.com/forum ... ding-Video
What "hotter and faster" means by the way, is use *more* current to melt the puddle faster, and in turn, move the torch more quickly (you need the manual skills with moving the torch and adding filling rod when necessary, which is where practice comes in) and in the end you will end up inputting *less* heat energy than if you used less current (which is sort of counter-intuitive result, but it's the way it works.)
If it's sitting there red hot for very long (like say 10+ seconds) after you stop the arc, then yeah you are really roasting it.
Another thing you can do is weld it in stitches (short lengths), and give it time to cool down in between stitches. Stainless conducts away heat very slowly. Bathing both sides of it in Argon doesn't help because argon conducts heat away very poorly also. Although it will keep it from oxidizing.
Also, check out this video; his results welding stainless tubing are excellent:
http://www.everlastgenerators.com/forum ... ding-Video
ajlskater1
- ajlskater1
-
Ace
-
Posts:
-
Joined:Thu Feb 02, 2012 5:32 am
Well to be honest speed just comes with a lot of time welding. Like they say practice makes perfect. One other tip that I for got to mention is you can also manually pulse the foot pedal while adding the rod. That is kind of a harder technique to get down but once you are able to run a decent normal bead using that technique can help you get that really nice gold/ silver bead
This can also to be done with the pulse function on some of the new inverter machine but I prefer to do it maunally because I like to control the pulses and not have to go at a set pulsing like the machine gives you. So my best advice is get a bunch of scrap set the machine a little hotter and just start praticing and like someone else said you will need to back off the pedal gradually as you weld, especially with stainless because it retrains heat so bad. Good luck. Hope you post some pics of nice welds soon.

Hello from a newbie. I have the same problem and i ve experimented with more argon flow with a little better results. Still need much improve.. I can make a fairly enough nice weld at 2 pieces but i need to weld pipes and there the troubles begin. Any help appreciated! Photos of destruction..
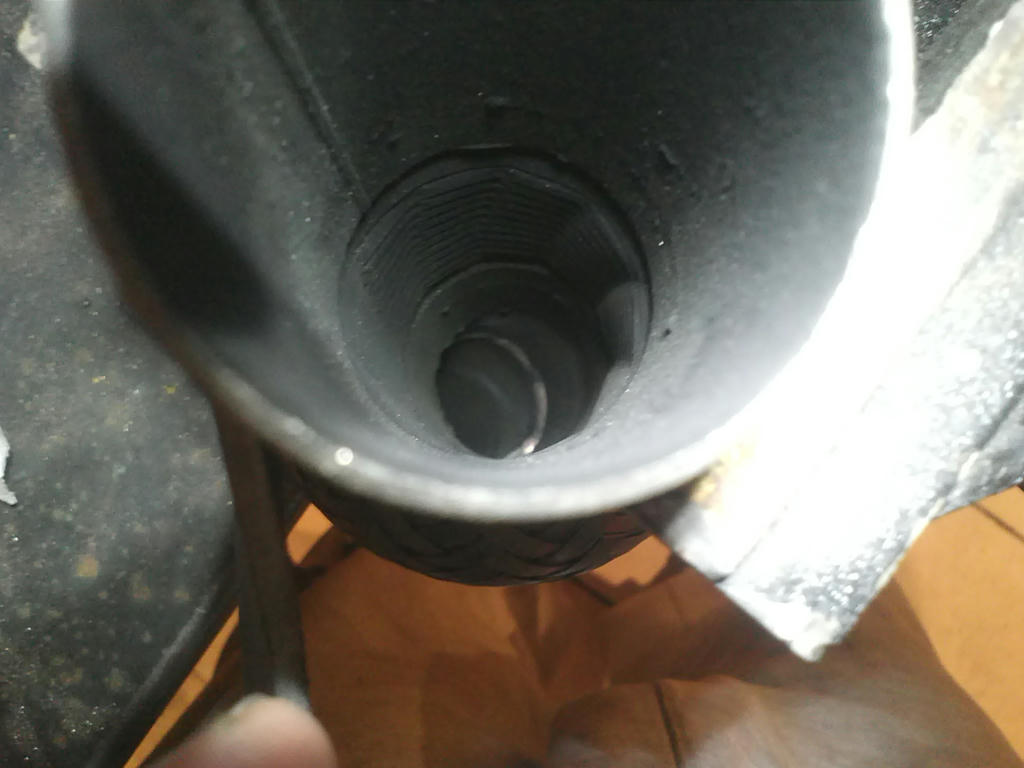
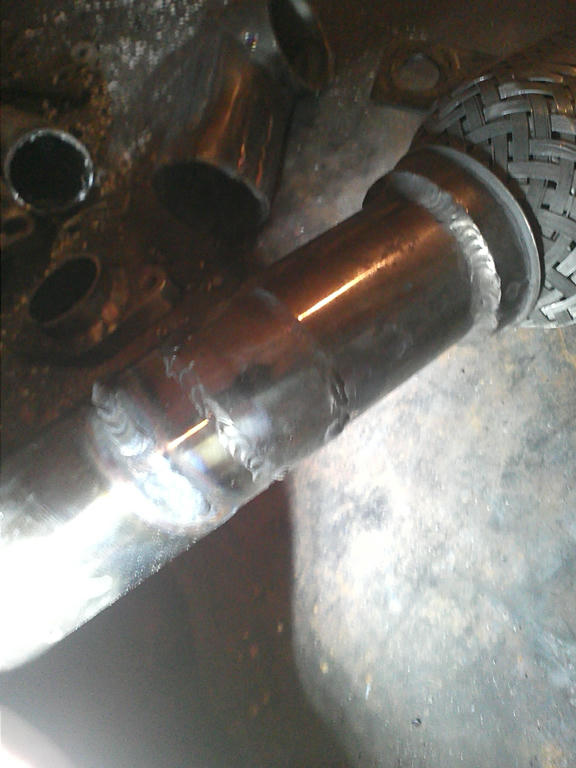
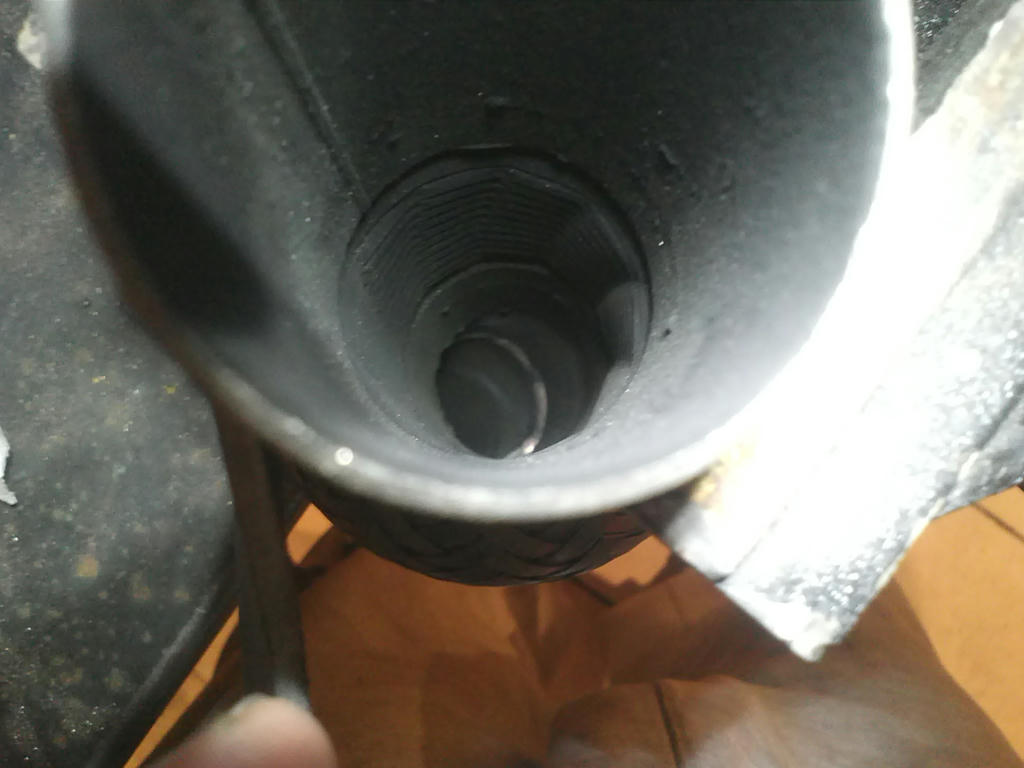
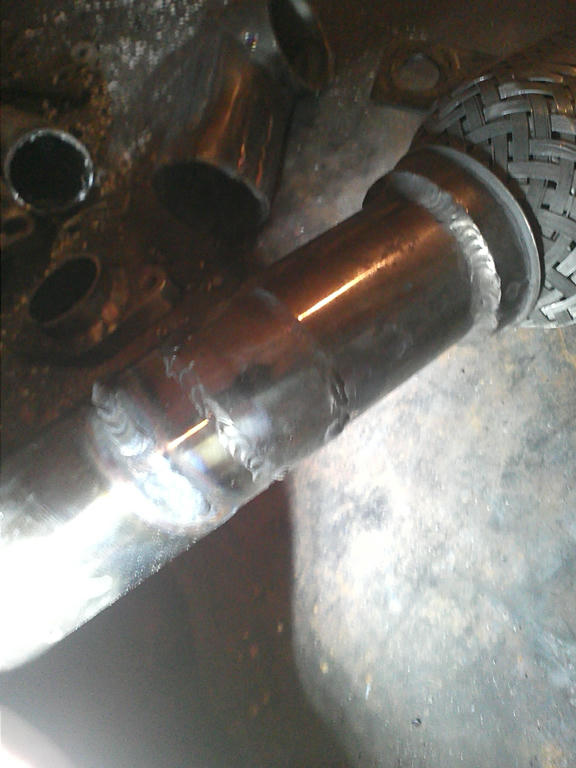
Return to “Tig Welding - Tig Welding Aluminum - Tig Welding Techniques - Aluminum Tig Welding”
Jump to
- Introductions & How to Use the Forum
- ↳ Welcome!
- ↳ Member Introductions
- ↳ How to Use the Forum
- ↳ Moderator Applications
- Welding Discussion
- ↳ Metal Cutting
- ↳ Tig Welding - Tig Welding Aluminum - Tig Welding Techniques - Aluminum Tig Welding
- ↳ Mig and Flux Core - gas metal arc welding & flux cored arc welding
- ↳ Stick Welding/Arc Welding - Shielded Metal Arc Welding
- ↳ Welding Forum General Shop Talk
- ↳ Welding Certification - Stick/Arc Welding, Tig Welding, Mig Welding Certification tests - Welding Tests of all kinds
- ↳ Welding Projects - Welding project Ideas - Welding project plans
- ↳ Product Reviews
- ↳ Fuel Gas Heating
- Welding Tips & Tricks
- ↳ Video Discussion
- ↳ Wish List
- Announcements & Feedback
- ↳ Forum News
- ↳ Suggestions, Feedback and Support
- Welding Marketplace
- ↳ Welding Jobs - Industrial Welding Jobs - Pipe Welding Jobs - Tig Welding Jobs
- ↳ Classifieds - Buy, Sell, Trade Used Welding Equipment
- Welding Resources
- ↳ Tradeshows, Seminars and Events
- ↳ The Welding Library
- ↳ Education Opportunities