As the title describes, I am welding 304 Stainless .065 tubing with back purge. My question is how to control the distortion (low areas) on each side of the weld. This particular customer requests that I sand the weld smooth for polishing. That creates problems with the low areas.
Thanks in advance for any help.
Tig welding tips, questions, equipment, applications, instructions, techniques, tig welding machines, troubleshooting tig welding process
- LtBadd
-
Weldmonger
-
Posts:
-
Joined:Sun Apr 12, 2015 4:00 pm
-
Location:Clearwater FL
-
Contact:
exnailpounder
- exnailpounder
-
Weldmonger
-
Posts:
-
Joined:Thu Dec 25, 2014 9:25 am
-
Location:near Chicago
I just did some .065 SS tubing and I pulsed it but your post is a bit confusing...can you elaborate?
Ifyoucantellmewhatthissaysiwillbuyyouabeer.
I'll assume no filler, full pen since you are back purging. I use 45-48amps straight, 1/16" tung, large cup and gas lens. I also pulse 2.5pps 50% on 50% 55-58amps 1/16" ting gas lens large cup.
Here one polished with an ultra fine scotchbrite belt
Here one polished with an ultra fine scotchbrite belt
- Attachments
-
- IMG_20160814_195522.jpg (30.48 KiB) Viewed 1364 times
I weld stainless, stainless and more stainless...Food Industry, sanitary process piping, vessels, whatever is needed, I like to make stuff.
ASME IX, AWS 17.1, D1.1
Instagram #RNHFAB
ASME IX, AWS 17.1, D1.1
Instagram #RNHFAB
MadisonRods
- MadisonRods
-
New Member
-
Posts:
-
Joined:Tue Jan 13, 2015 12:29 pm
MadisonRods
- MadisonRods
-
New Member
-
Posts:
-
Joined:Tue Jan 13, 2015 12:29 pm
This is pretty typical of what I am getting. Usually one side will sand down fine. Filler is 308/035 @ 40 amps
- Attachments
-
- IMG_1234.JPG (39.17 KiB) Viewed 1300 times
-
- IMG_1230.JPG (35.71 KiB) Viewed 1300 times
I see what's going on. Mainly because I'm guilty of making the same mistakes
You're not lining up the tubes axially. One tube is off to one side by a few thousandths. It's not distortion that is causing low areas---the tube itself is low to begin with, on that side.. I've drawn a red line to illustrate:
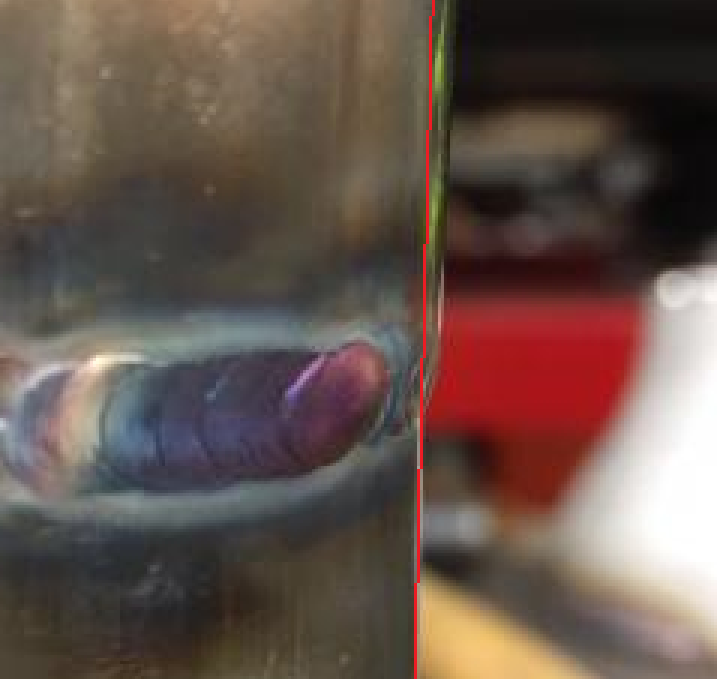
The solution? Either continue grinding that area carefully until it appears properly blended. The right thing would be to get a better fit-up so they are dead-on axially.

You're not lining up the tubes axially. One tube is off to one side by a few thousandths. It's not distortion that is causing low areas---the tube itself is low to begin with, on that side.. I've drawn a red line to illustrate:
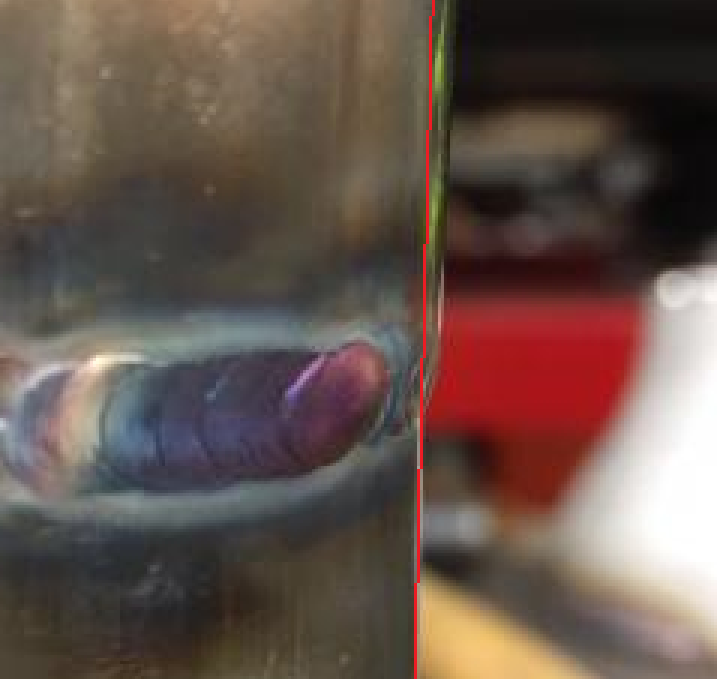
The solution? Either continue grinding that area carefully until it appears properly blended. The right thing would be to get a better fit-up so they are dead-on axially.
I see the same thing as Oscar, alignment and fit up is key. Is what I showed above not acceptable? If not you could sand that area down and feather it out, I have a specific machine that wraps belts around tube, makes life easier.
I weld stainless, stainless and more stainless...Food Industry, sanitary process piping, vessels, whatever is needed, I like to make stuff.
ASME IX, AWS 17.1, D1.1
Instagram #RNHFAB
ASME IX, AWS 17.1, D1.1
Instagram #RNHFAB
What did you end doing?
I weld stainless, stainless and more stainless...Food Industry, sanitary process piping, vessels, whatever is needed, I like to make stuff.
ASME IX, AWS 17.1, D1.1
Instagram #RNHFAB
ASME IX, AWS 17.1, D1.1
Instagram #RNHFAB
MadisonRods
- MadisonRods
-
New Member
-
Posts:
-
Joined:Tue Jan 13, 2015 12:29 pm
Better alignment seems to be my problem. I have started to take a considerable amount of time up front making sure my fitment is the best it can be. I would say 90-95% of my problems have disappeared. Thanks to everybody that took the time to reply to my post!
dave powelson
- dave powelson
-
Guide
-
Posts:
-
Joined:Mon Nov 24, 2014 3:09 am
-
Location:yuba city, CA
MadisonRods wrote:Better alignment seems to be my problem. I have started to take a considerable amount of time up front making sure my fitment is the best it can be. I would say 90-95% of my problems have disappeared. Thanks to everybody that took the time to reply to my post!
Fade out to stop those craters, which are crack generators and can be tight leakers.
Return to “Tig Welding - Tig Welding Aluminum - Tig Welding Techniques - Aluminum Tig Welding”
Jump to
- Introductions & How to Use the Forum
- ↳ Welcome!
- ↳ Member Introductions
- ↳ How to Use the Forum
- ↳ Moderator Applications
- Welding Discussion
- ↳ Metal Cutting
- ↳ Tig Welding - Tig Welding Aluminum - Tig Welding Techniques - Aluminum Tig Welding
- ↳ Mig and Flux Core - gas metal arc welding & flux cored arc welding
- ↳ Stick Welding/Arc Welding - Shielded Metal Arc Welding
- ↳ Welding Forum General Shop Talk
- ↳ Welding Certification - Stick/Arc Welding, Tig Welding, Mig Welding Certification tests - Welding Tests of all kinds
- ↳ Welding Projects - Welding project Ideas - Welding project plans
- ↳ Product Reviews
- ↳ Fuel Gas Heating
- Welding Tips & Tricks
- ↳ Video Discussion
- ↳ Wish List
- Announcements & Feedback
- ↳ Forum News
- ↳ Suggestions, Feedback and Support
- Welding Marketplace
- ↳ Welding Jobs - Industrial Welding Jobs - Pipe Welding Jobs - Tig Welding Jobs
- ↳ Classifieds - Buy, Sell, Trade Used Welding Equipment
- Welding Resources
- ↳ Tradeshows, Seminars and Events
- ↳ The Welding Library
- ↳ Education Opportunities