My son is in his final semester of mech engineering and has his capstone project of the ASME design-build of a human powered vehicle..basically a bicycle frame. I volunteered to do the welding so I better get good.
I fishmouthed some 1/2" EMT, then pickled the zinc off with muratic acid. Jigged it tight, 4 tacks and went to work.
It is 0.702" OD with 0.042" wall. Smaller and thinner than the project which has yet to be finalized. EMT is low carbon, the project will be 4130.
Any tips? 50 amps, Rule of 33 on pulser, 0.035" S2 filler and 12 cfh argon through #7.
Tig welding tips, questions, equipment, applications, instructions, techniques, tig welding machines, troubleshooting tig welding process
exnailpounder
- exnailpounder
-
Weldmonger
-
Posts:
-
Joined:Thu Dec 25, 2014 9:25 am
-
Location:near Chicago
It looks kinda cooked but that could be from using acid on it. Welds look good.
Ifyoucantellmewhatthissaysiwillbuyyouabeer.
Yes, practice makes perfect. Thankfully the EMT is dirt cheap as I have a bucket full of drops. But 70 amps on 0.042" carbon steel? I'm rubbing 1/16" thoriated tungsten so that is fine. I might try larger coupons and let it cool a bit. Tacks are colorless as were the first 1/4s..welded thinnest parts first, saving inside corners for last. Joints were tight, zero gap since the steel cuts like butter. Not the same on chrome moly..will get carbide burrs for that. Using a die grinder in a home made jig with rotary files. Then hand file burrs and just breaking edges.
Mind you, I have a regular job too, this avocation keeps me out of bars and trouble. And its a bit more profitable than fantasy football too. I'm the local expert in mower deck welding. Code strength welds blended in better than Earl Scheib body work, all steel no Bondo.
Mind you, I have a regular job too, this avocation keeps me out of bars and trouble. And its a bit more profitable than fantasy football too. I'm the local expert in mower deck welding. Code strength welds blended in better than Earl Scheib body work, all steel no Bondo.
- MosquitoMoto
-
Weldmonger
-
Posts:
-
Joined:Sat Aug 01, 2015 8:38 am
-
Location:The Land Down Under
This is looking nice.
I'm doing something similar, but making clip-on handlebars for a motorcycle. Same kind of joint but with about 7 degrees offset. Looking forward to seeing your finished job.
Kym
I'm doing something similar, but making clip-on handlebars for a motorcycle. Same kind of joint but with about 7 degrees offset. Looking forward to seeing your finished job.
Kym
Another issue is set on vs set in joints. Since I am writing the WPS for these joints, set in or portholed joints might be required. It is common in bicycle frame construction on high end cycles. Saves a tad weight but really makes the weld tricky.
Looks good from here! 75-80A on 0.042" wall!?! Yikes, that's above my pay grade, that's for sure! Try it at your own risk. I suspect one would have to have their technique down really good to pull that off.
If you want to control heat tint/discoloration, try wrapping the T with flat copper braid, somewhat close to the weld joints, but not too close. If it worked for me and titanium, it will work for you.

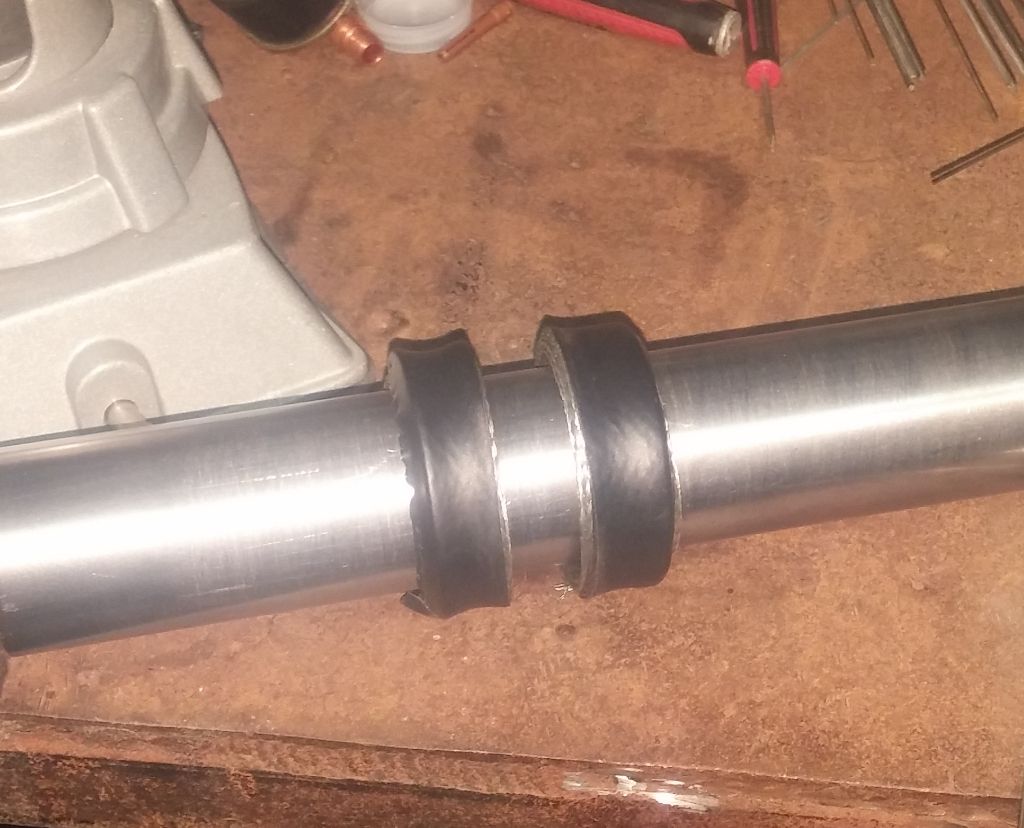
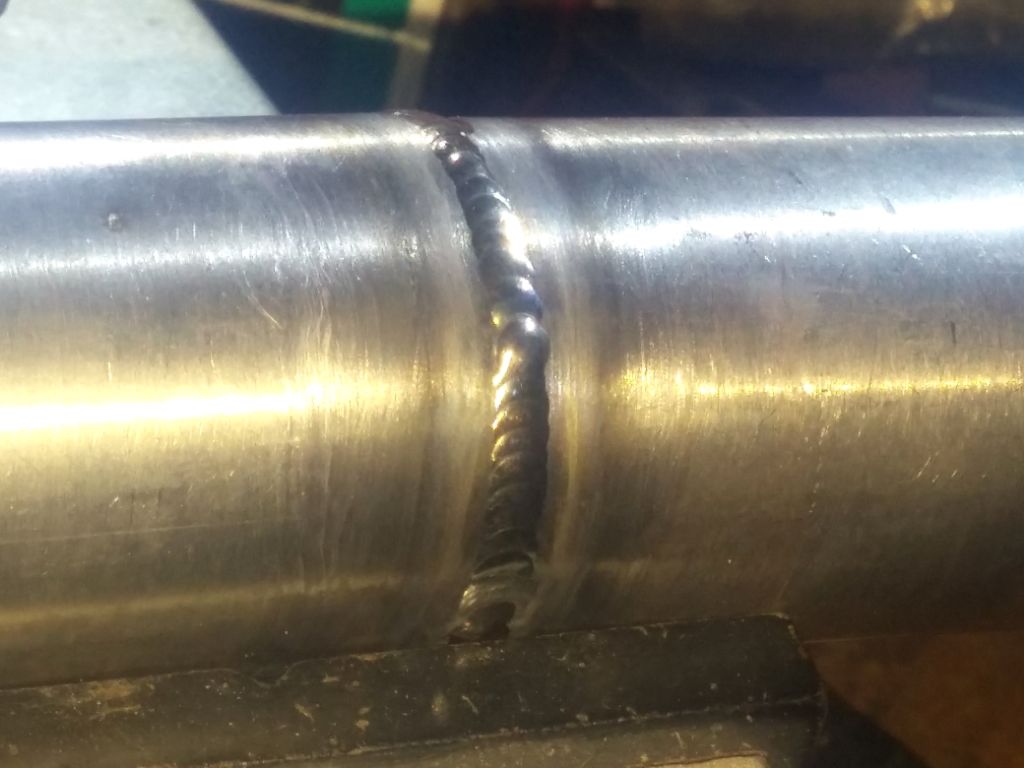
If you want to control heat tint/discoloration, try wrapping the T with flat copper braid, somewhat close to the weld joints, but not too close. If it worked for me and titanium, it will work for you.


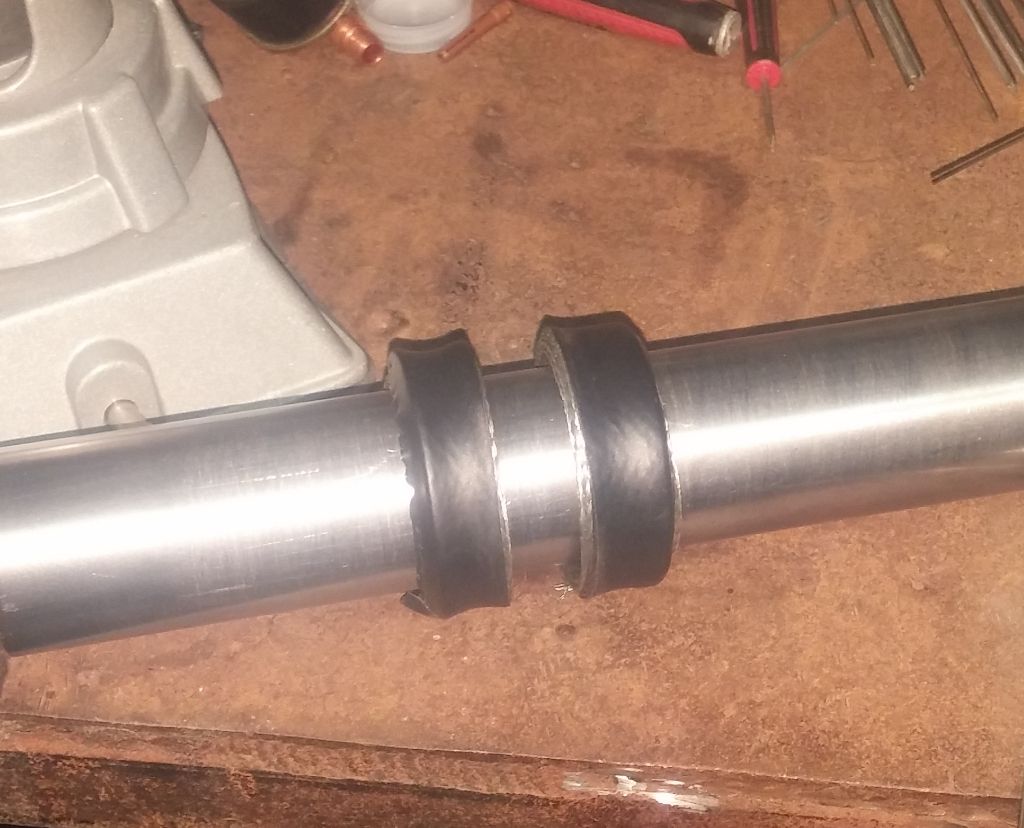
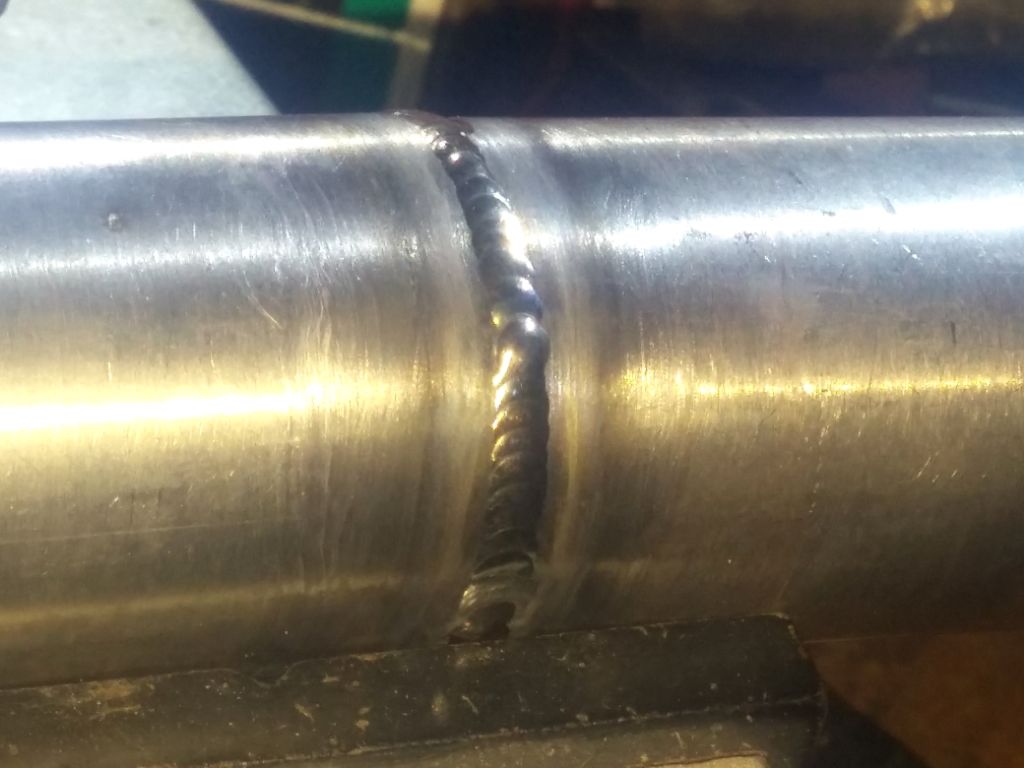
I'm running a 17 torch with std collet so I made a backwoods gas lens using some fine bronze mesh circles I confiscated from a recreational pharmaceutical user
. Hey, it works! I cab get a bit more stickout without adding rainbow colors to the tungsten.
I had planned on getting a stubby gas lens kit but had emergency surgery on my GSD that burned through all my mad money. Good thing for overtime at my other job.
I have annealed some bare12 gauge copper wire to chill the HAZ during welding. Next torch time is next week. I've a 55 hour work week starting tonight plus whatever falls out on the shade tree side.

I had planned on getting a stubby gas lens kit but had emergency surgery on my GSD that burned through all my mad money. Good thing for overtime at my other job.
I have annealed some bare12 gauge copper wire to chill the HAZ during welding. Next torch time is next week. I've a 55 hour work week starting tonight plus whatever falls out on the shade tree side.
Welding SOON. Right now it is metal massage with a tube bender. One bend is 3" centerline radius on 0.058" wall 3/4" OD tube. Too tight unless inside support so tubes are bent after filling with Woods metal, an alloy of bismuth, lead, tin and cadmium that melts at 158 °F. It bends like tin, minus the cry. Yes, taking precaution against lead and cadmium by melting under water with a drop of vinegar to keep pH below 7. No fumes and no oxides. Just have to dispose of that water carefully. Only a few ounces.
The tubes also needed normalizing to bend so I made a tube furnace with 6" stainless chimney liner, ceramic wool and a few plate scraps. Heated the ID with a torch and monitored the exhaust temp with a thermocouple. Then plugged both ends and let it cool for two hours. Tubes had slight warpage which was easy to remove with the tube roll machine.
I have one butt joint and then it is miter time. I work 4-10s so three days off is all the time I can devote the unless I take time off. No pressure though..it will be done by April.
The tubes also needed normalizing to bend so I made a tube furnace with 6" stainless chimney liner, ceramic wool and a few plate scraps. Heated the ID with a torch and monitored the exhaust temp with a thermocouple. Then plugged both ends and let it cool for two hours. Tubes had slight warpage which was easy to remove with the tube roll machine.
I have one butt joint and then it is miter time. I work 4-10s so three days off is all the time I can devote the unless I take time off. No pressure though..it will be done by April.
Coped tube welding is one heck of a complex weld.
The change in angle is so marked as you weld.
I'm no expert by any stretch but one thing that helped me was to think about the joint in distinct parts.
The right angle side is a fillet weld. The flat side is a lap weld. Subtle differences in where you direct the heat and how much filler you add.
The change in angle is so marked as you weld.
I'm no expert by any stretch but one thing that helped me was to think about the joint in distinct parts.
The right angle side is a fillet weld. The flat side is a lap weld. Subtle differences in where you direct the heat and how much filler you add.
Great tip! Only a few joints not at right angles. Gas lens plus huge stick out. I'm planning every weld since first view of the drawings.
The welding will be the easiest part. Bending tubes is the worst.
The welding will be the easiest part. Bending tubes is the worst.
Listen to this guy. He is the tube welding master!zank wrote:I think it looks great. Repetition will get you far!
I hope he doesn't mind...
https://www.flickr.com/photos/zanconato ... 560833492/
I am not worthy of his praise..forgive me for I am but an unclean welding dilettante.
I have lots of scrap to practice with as the bending is done and only the copes on bent sections need to be done. The students got the straights coped by the machine shop on the milling machine using end mills.
I have lots of scrap to practice with as the bending is done and only the copes on bent sections need to be done. The students got the straights coped by the machine shop on the milling machine using end mills.
Here is a crude drawing of frame subassy. Also welded would be steering knuckle- kingpins and minor attachment points.
Here is the roll hoop. I made plywood templates for bends to preserve sanity. They worked great in bending.
- 0310171147.jpg (24.6 KiB) Viewed 1887 times
- 0307171830.jpg (29.39 KiB) Viewed 1887 times
One other thing..these tubes (4130 a normalized) are highly magnetic. When deburring, all the swarf stays on the end. Will this pose a problem? If so, I can degauss with an alternating current in a coil of wire..a contraption I made to get my bicycle chain cleaner as the Polar power meter uses a strong magnet to determine chain tension and speed..power is simply the product of chain tension and chain speed. Anyhow, wear products would stay in the magnetic chain. Degauss and the swarf washes off in solvent.
Since Jody admitted buying from this chain. .Harbor Freight
Yes, their roll bender. The dies were all wrong but a guy in of all places, Bend OR, makes custom dies for it.
This is a three roll with only the top roll turned by a two foot diameter wheel, the bottom two are on bearings. In addition, I moved the bottom two axles closer and higher to tighten the bend radius.
Tubes are degreased with acetone, then coated in rosin for grip. The top roll is fed down by a healthy sized Acme thread feed screw. I can measure the travel with calipers for repeatability. No visible wrinkles or deformation

This is a three roll with only the top roll turned by a two foot diameter wheel, the bottom two are on bearings. In addition, I moved the bottom two axles closer and higher to tighten the bend radius.
Tubes are degreased with acetone, then coated in rosin for grip. The top roll is fed down by a healthy sized Acme thread feed screw. I can measure the travel with calipers for repeatability. No visible wrinkles or deformation
There have been issues with spring back after removal of the Woods metal filling but another tripthrough the bender fixes it. Out of plane issues are tweaked on the work bench via brute force..slip some 3/4" PVC over the end and use a long tube over that to cold set both bends in plane.
This roller works slowly and only material directly under the middle roller is worked. Not for high volume work but its working fine on this project if only at a near geologic rate
This roller works slowly and only material directly under the middle roller is worked. Not for high volume work but its working fine on this project if only at a near geologic rate

Ever have an "oh CRAP" moment? Yep, scratched cornea. All better now. Bends and copes done, just down to fitting, tacking and welding. Great news is new hole saws at correct speed do a wonderful job at cope miters in the drill press with Harbor Freight tube notcher. 1600 RPM on a 1" Milwaukee bimetallic is golden. Blue chips are the goal so watch feed. No cleanup other than debur.
Have to say Blue Ox Lenox hole saws seem to cut better but are more fragile. But WTH do I know as this is my first CrMo rodeo. I do know when feed and speed are right, it cuts great and fast.
When chips turn blue, all is good. Put heat in swarf and the tool will stay cool.
Have to say Blue Ox Lenox hole saws seem to cut better but are more fragile. But WTH do I know as this is my first CrMo rodeo. I do know when feed and speed are right, it cuts great and fast.
- 0327171809.jpg (26.36 KiB) Viewed 1839 times
Last edited by Keith_J on Tue Mar 28, 2017 2:13 am, edited 1 time in total.
Return to “Tig Welding - Tig Welding Aluminum - Tig Welding Techniques - Aluminum Tig Welding”
Jump to
- Introductions & How to Use the Forum
- ↳ Welcome!
- ↳ Member Introductions
- ↳ How to Use the Forum
- ↳ Moderator Applications
- Welding Discussion
- ↳ Metal Cutting
- ↳ Tig Welding - Tig Welding Aluminum - Tig Welding Techniques - Aluminum Tig Welding
- ↳ Mig and Flux Core - gas metal arc welding & flux cored arc welding
- ↳ Stick Welding/Arc Welding - Shielded Metal Arc Welding
- ↳ Welding Forum General Shop Talk
- ↳ Welding Certification - Stick/Arc Welding, Tig Welding, Mig Welding Certification tests - Welding Tests of all kinds
- ↳ Welding Projects - Welding project Ideas - Welding project plans
- ↳ Product Reviews
- ↳ Fuel Gas Heating
- Welding Tips & Tricks
- ↳ Video Discussion
- ↳ Wish List
- Announcements & Feedback
- ↳ Forum News
- ↳ Suggestions, Feedback and Support
- Welding Marketplace
- ↳ Welding Jobs - Industrial Welding Jobs - Pipe Welding Jobs - Tig Welding Jobs
- ↳ Classifieds - Buy, Sell, Trade Used Welding Equipment
- Welding Resources
- ↳ Tradeshows, Seminars and Events
- ↳ The Welding Library
- ↳ Education Opportunities