hijack alert
started with stick went to OA for welding motorcycle pipes
found TIG and died and went to heaven...
craig
Tig welding tips, questions, equipment, applications, instructions, techniques, tig welding machines, troubleshooting tig welding process
- subwayrocket
-
Ace
-
Posts:
-
Joined:Thu Aug 13, 2015 11:38 pm
-
Location:Scranton/WilkesBarre, Pennsylvania
Haha Thanks ...and Yeah they are...They were so nasty I figured I had to share ! Got those big globs mainly because I was laying on the ground welding straight up overhead and over the frame, exhaust pipe and drive shaft ...and swapping left and right hands to reach . Could hardly reach and ...and couldn't see it thru the shifting helmet. I have played with my buddy's mig a little , I figured for all the small part repairs , motorcycle parts , and aluminum , a TIG machine was better suited . ....That Alum Fab in the dash is pretty sweet !raticus wrote:whoa!!!! man those are some of the ugliest tungstens I've ever seen, I never knew they could get that bad! lol...subwayrocket wrote:Welding in a driver side floor pan ...have to replace part of a body cross member underneath ....
Put in some steel "C" channel across the bad spot....welding upside down, can't see and can't reach nothin...
Here , have a good laugh ! haha
-----------------------------------------Bad Tungstens.jpg------------------------------
Last edited by subwayrocket on Mon Nov 09, 2015 9:38 am, edited 2 times in total.
- MosquitoMoto
-
Weldmonger
-
Posts:
-
Joined:Sat Aug 01, 2015 8:38 am
-
Location:The Land Down Under
Poland308 wrote:Never say never. I don't currently own a mig machine. But if like me you check the prices every now and again then we'll probably both end up owning mig guns.
If it ever came to fabbing up something big where I had to work fast...maybe.
But to get on my favourite hobby horse once again, while the price of a MIG machine wouldn't put me off...the ongoing cost of having to add another gas bottle to my collection certainly would. Just keeping pure argon up to my TIG is already eye-wateringly expensive.
Kym
ex framie
- ex framie
-
Ace
-
Posts:
-
Joined:Sun Aug 09, 2015 1:09 am
-
Location:Brisbane QLD Land of oz
Kym,
For some reason TIG uses a lot more gas than my mig.
Onto my second bottle of argon for tig since I bought the bottles, still have 2/3 of a bottle of mig gas left and I've done a lot more mig than tig.
So that blows that excuse out the door, which mig are you looking at?
For some reason TIG uses a lot more gas than my mig.
Onto my second bottle of argon for tig since I bought the bottles, still have 2/3 of a bottle of mig gas left and I've done a lot more mig than tig.
So that blows that excuse out the door, which mig are you looking at?

Pete
God gave man 2 heads and only enough blood to run 1 at a time. Who said God didn't have a sense of humour.....
God gave man 2 heads and only enough blood to run 1 at a time. Who said God didn't have a sense of humour.....
- MosquitoMoto
-
Weldmonger
-
Posts:
-
Joined:Sat Aug 01, 2015 8:38 am
-
Location:The Land Down Under
Hardy har-har!ex framie wrote:Kym,
For some reason TIG uses a lot more gas than my mig.
Onto my second bottle of argon for tig since I bought the bottles, still have 2/3 of a bottle of mig gas left and I've done a lot more mig than tig.
So that blows that excuse out the door, which mig are you looking at?
Nah, I'll stick with TIG for now. I have about 10 more years of learning to get up to speed before I start considering another class of welding!
Kym
yeah, I'm guessing with TIG you have pre and post flow, that uses a lot of gas... none of that with MIG... I do a lot of MIG at work (I work at a classic car restoration shop, basically doing a lot of MIG trying to repair swiss cheese'd old cars), and a bottle lasts forever... where at home where I do all my TIG, i go through a bottle quicker than I go through consumables)...ex framie wrote:Kym,
For some reason TIG uses a lot more gas than my mig.
Onto my second bottle of argon for tig since I bought the bottles, still have 2/3 of a bottle of mig gas left and I've done a lot more mig than tig.
So that blows that excuse out the door, which mig are you looking at?
can't believe it took me this many years to buy a diamond wheel for my bench grinder... what a difference
MosquitoMoto wrote:Poland308 wrote:Never say never. I don't currently own a mig machine. But if like me you check the prices every now and again then we'll probably both end up owning mig guns.
If it ever came to fabbing up something big where I had to work fast...maybe.
But to get on my favourite hobby horse once again, while the price of a MIG machine wouldn't put me off...the ongoing cost of having to add another gas bottle to my collection certainly would. Just keeping pure argon up to my TIG is already eye-wateringly expensive.
Kym
MIG is great for stuff like roll cages, much easier to get into those tight spots... though I play with TIG mostly to do aluminum stuff and small projects, the MIG is the workhorse for repairs and the bigger stuff... it's super fast and easy to do
can't believe it took me this many years to buy a diamond wheel for my bench grinder... what a difference
- MosquitoMoto
-
Weldmonger
-
Posts:
-
Joined:Sat Aug 01, 2015 8:38 am
-
Location:The Land Down Under
- MosquitoMoto
-
Weldmonger
-
Posts:
-
Joined:Sat Aug 01, 2015 8:38 am
-
Location:The Land Down Under
That's it!
Took ages to get enough heat into the workpiece, but a few boxes later I was in great shape.
Kym
Took ages to get enough heat into the workpiece, but a few boxes later I was in great shape.
Kym
stick welding now eh?MosquitoMoto wrote:
So anyhow, my wife had been whining about her broken oven rack for ages...
![]()
Kym
can't believe it took me this many years to buy a diamond wheel for my bench grinder... what a difference
- MosquitoMoto
-
Weldmonger
-
Posts:
-
Joined:Sat Aug 01, 2015 8:38 am
-
Location:The Land Down Under
- weldin mike 27
-
Weldmonger
-
Posts:
-
Joined:Fri Apr 01, 2011 10:59 pm
-
Location:Australia; Victoria
- MosquitoMoto
-
Weldmonger
-
Posts:
-
Joined:Sat Aug 01, 2015 8:38 am
-
Location:The Land Down Under
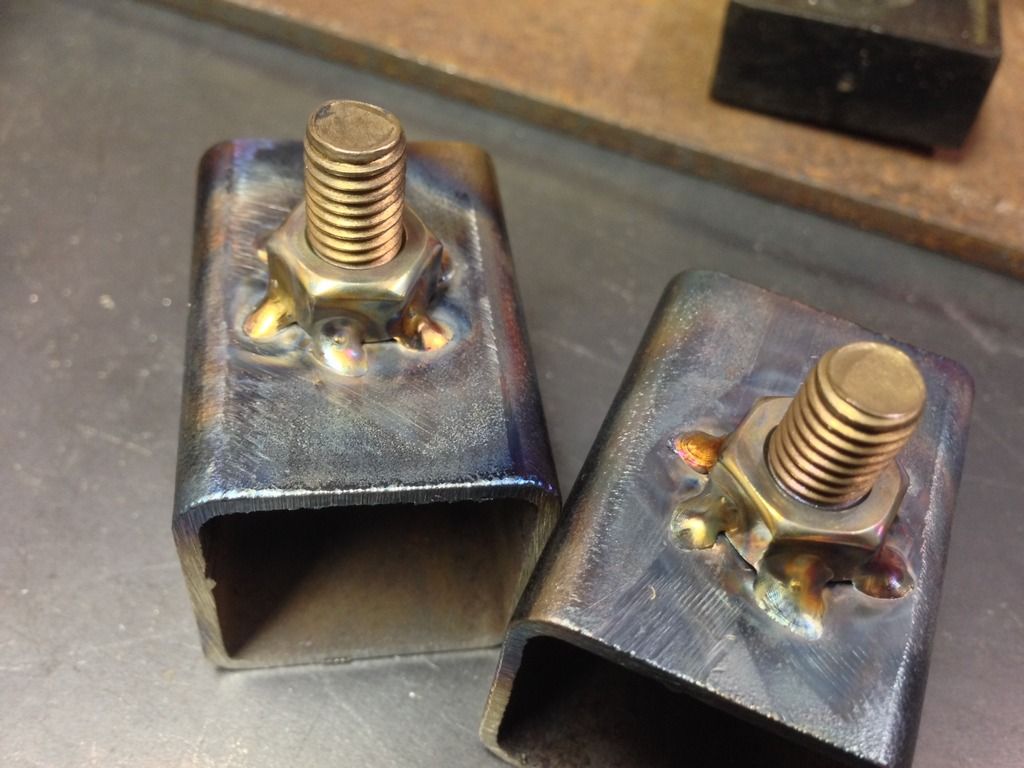
Tacking stainless nuts to carbon steel square tube to make up adjusters for a motorcycle race stand I'm building.
Was going to use some carbon steel nuts I found in the shed but they were used and potentially would have given oil contamination problems. Had some brand new stainless nuts, so used these instead, tacking with ER-309 filler as per Jody's 'differential metals' filler tip.
It's not art, but it worked. Purdy colours!
Kym
Lots of aluminum orders lately.
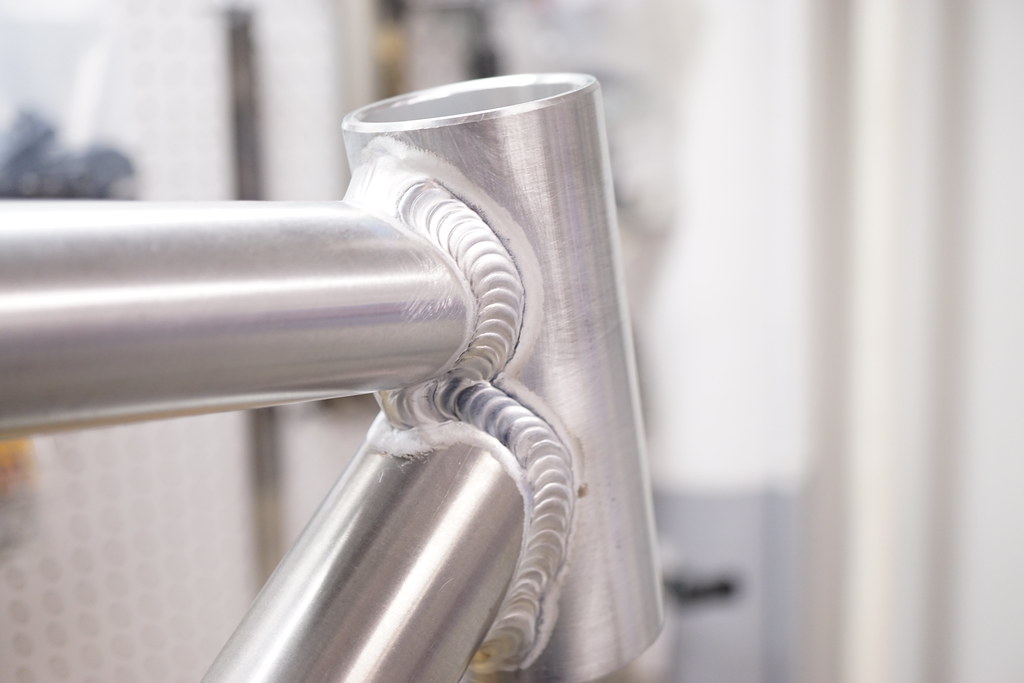
Cyclocross! by Mike Zanconato, on Flickr
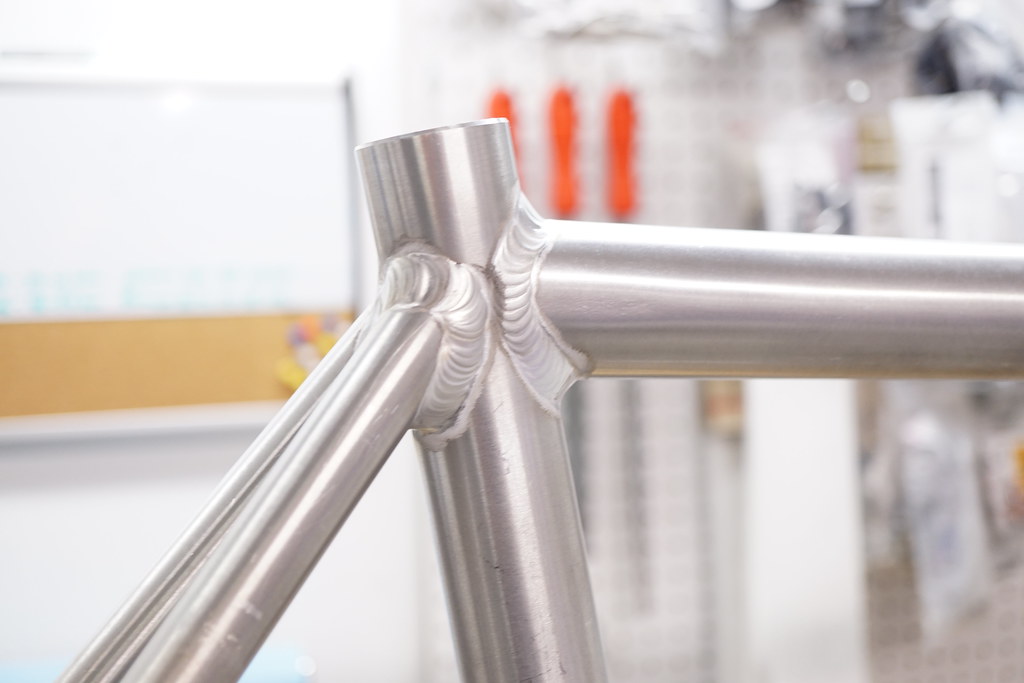
Cyclocross! by Mike Zanconato, on Flickr
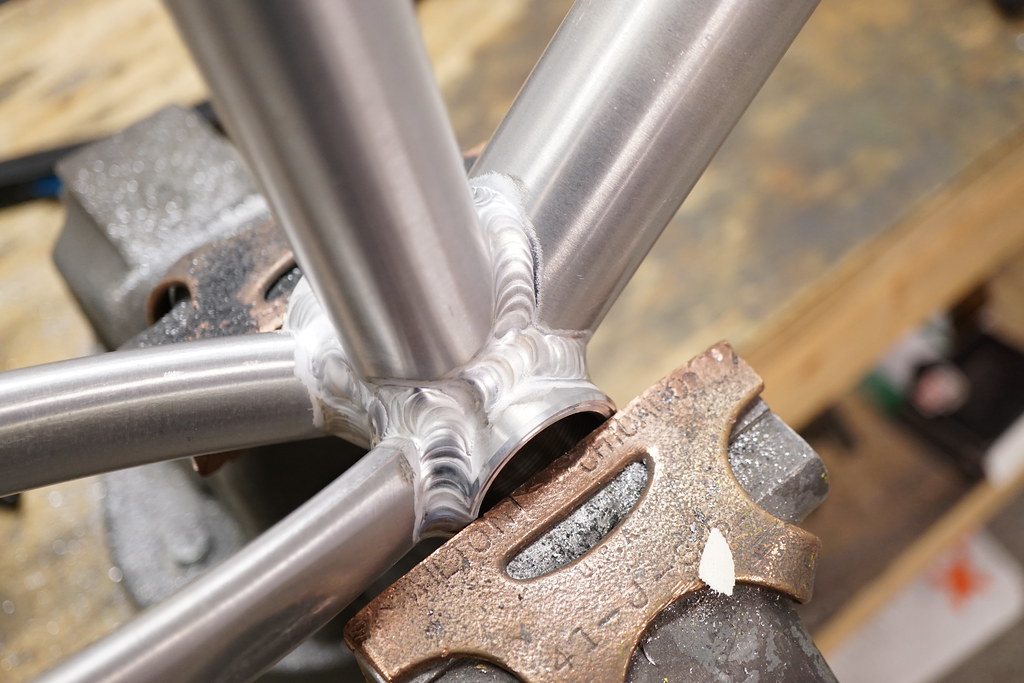
Cyclocross! by Mike Zanconato, on Flickr
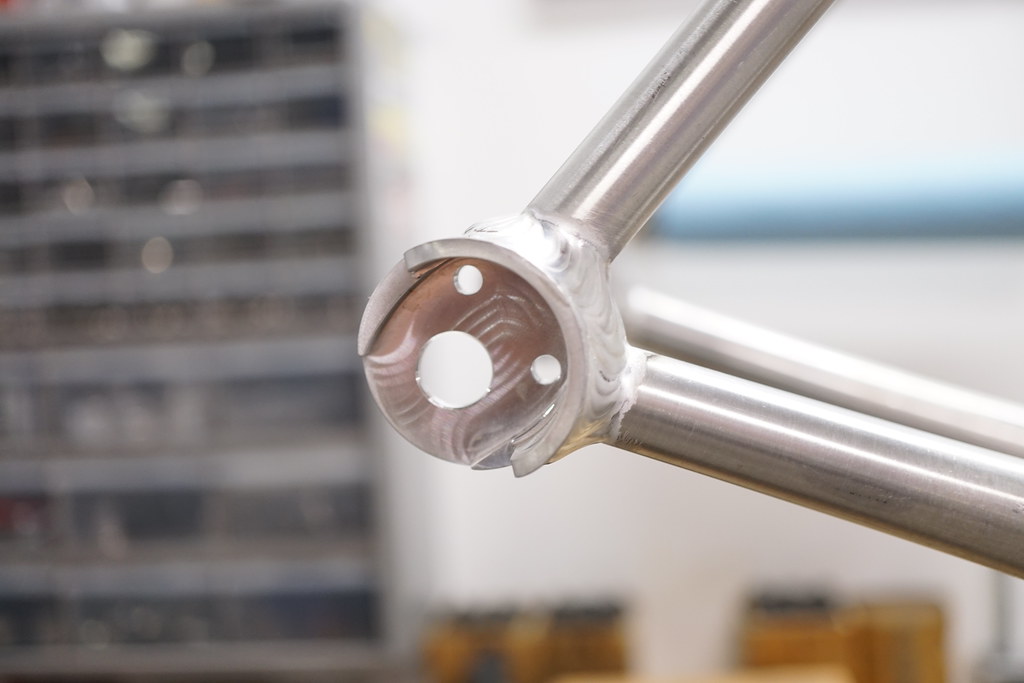
Cyclocross! by Mike Zanconato, on Flickr
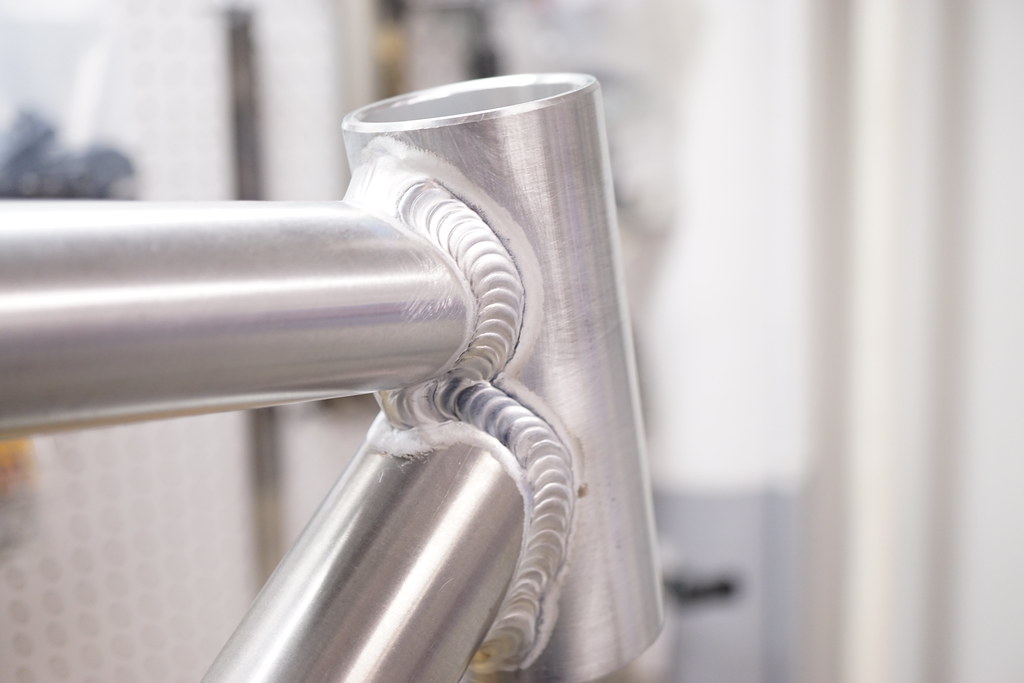
Cyclocross! by Mike Zanconato, on Flickr
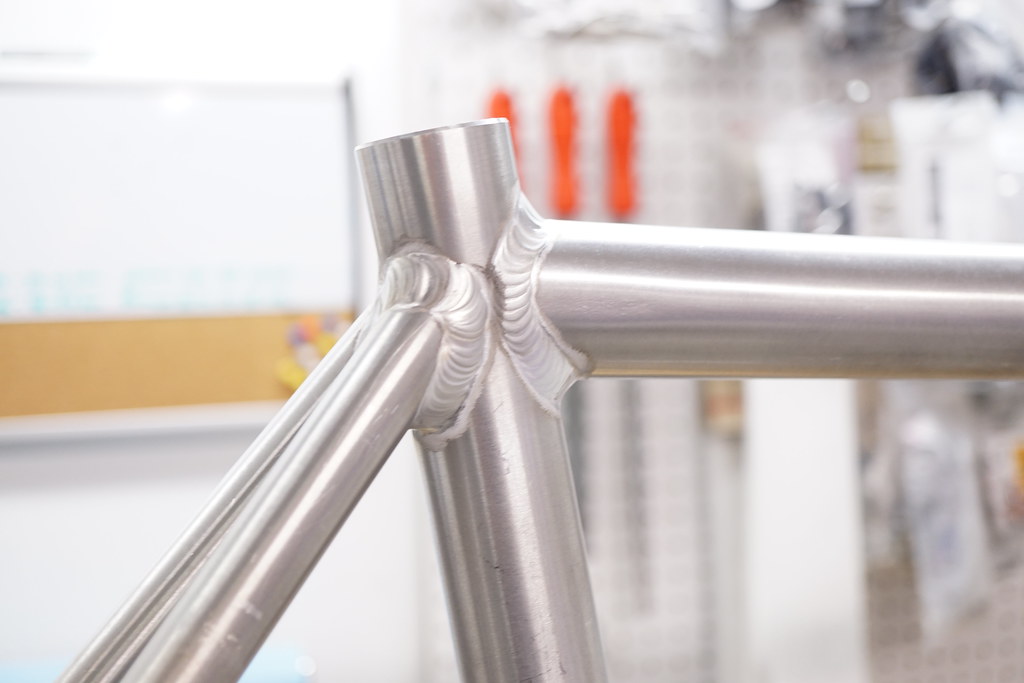
Cyclocross! by Mike Zanconato, on Flickr
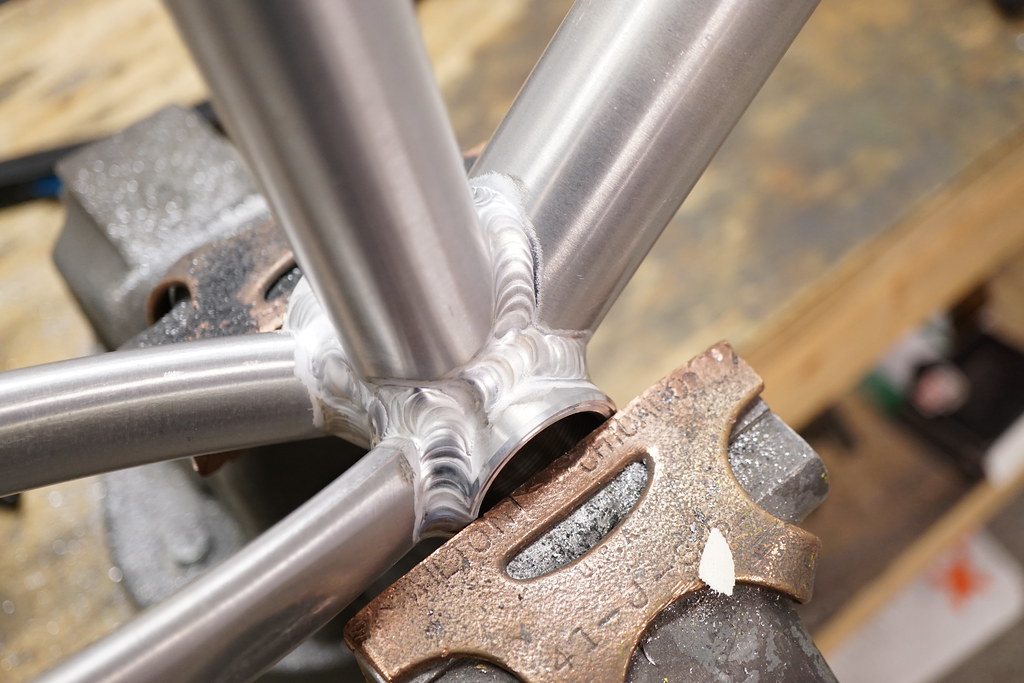
Cyclocross! by Mike Zanconato, on Flickr
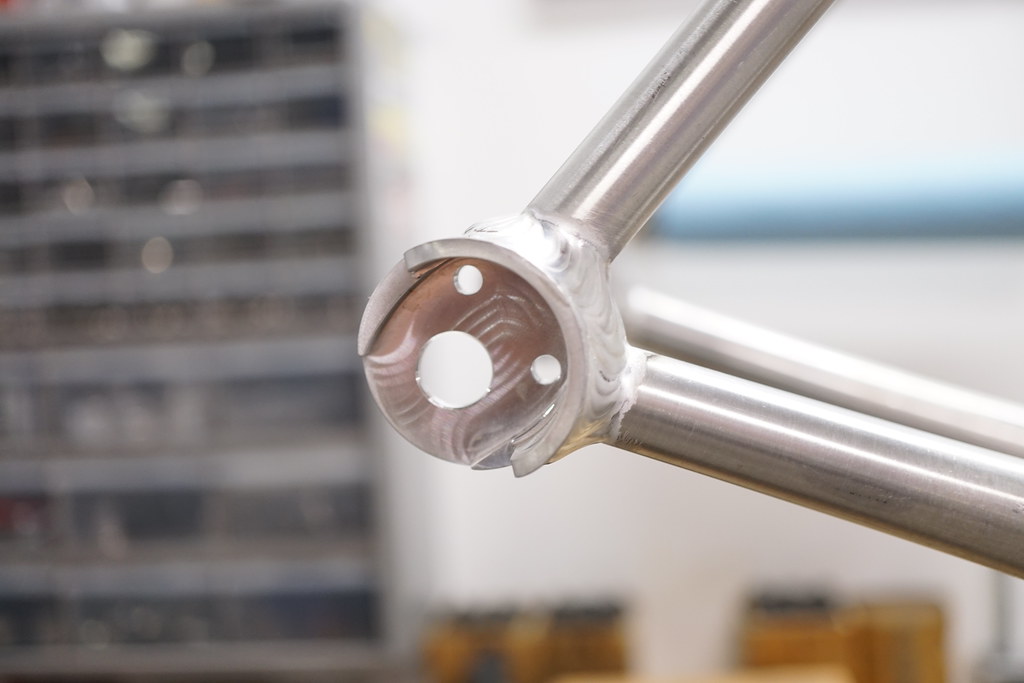
Cyclocross! by Mike Zanconato, on Flickr
- MosquitoMoto
-
Weldmonger
-
Posts:
-
Joined:Sat Aug 01, 2015 8:38 am
-
Location:The Land Down Under
[quote="motox"]zank
complicated and beautiful.......
craig[/w
Like so many of the good things in life.
I am always humbled and inspired by Zank's work.
Kym
complicated and beautiful.......
craig[/w
Like so many of the good things in life.
I am always humbled and inspired by Zank's work.
Kym
Thanks guys. You're too kind. It helps that I do the same thing over and over.
Stacking 'em tight today.
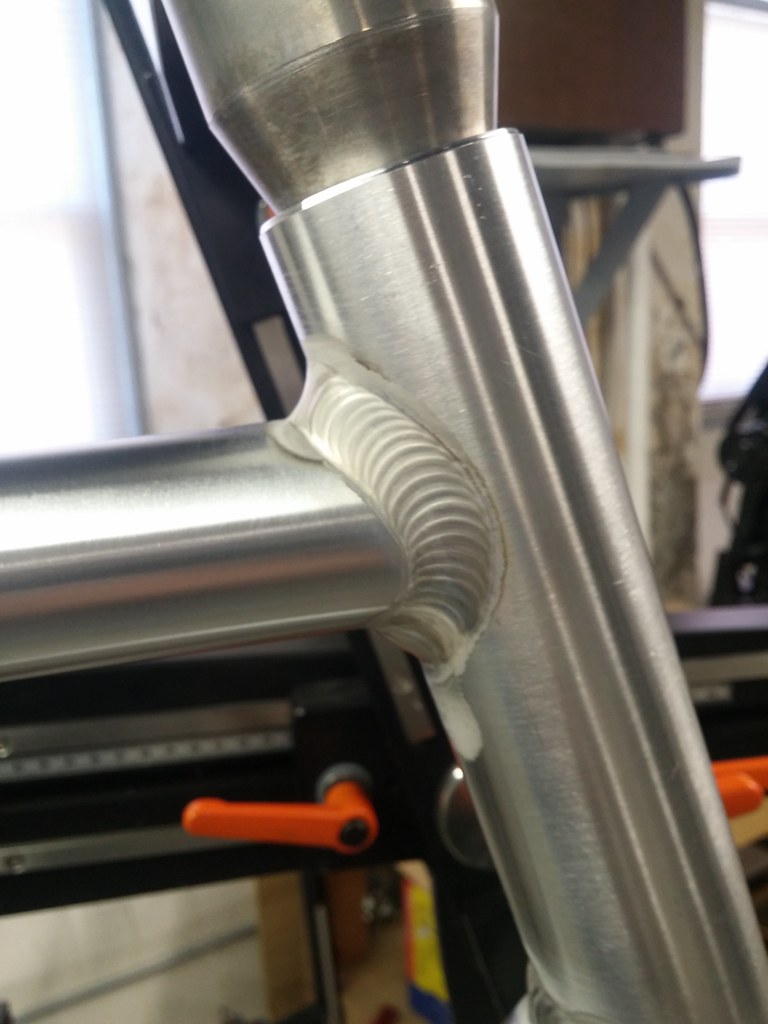
tight stack by Mike Zanconato, on Flickr
Stacking 'em tight today.
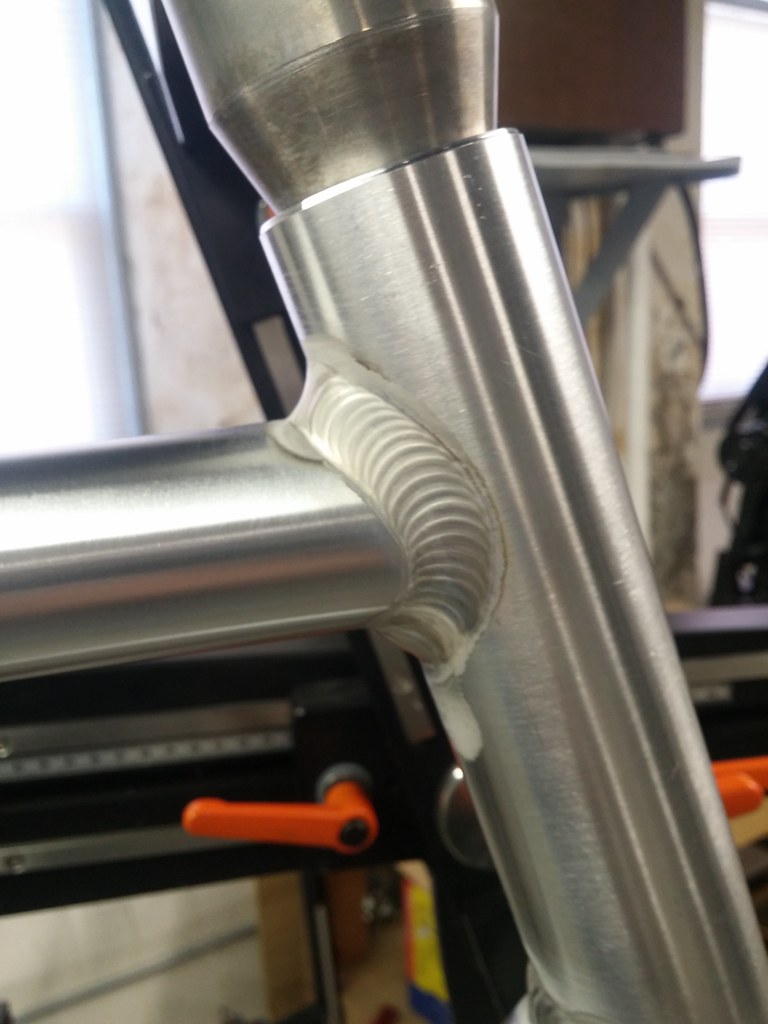
tight stack by Mike Zanconato, on Flickr
Obviously your carefull during your fit up. Any basic recommendations on that front Zank? I'm thinking of doing a interlaced tube frame for an aluminum bench. I've got 1/4 alum plate that's pretty hard not sure just what grade and any tips on keeping the tube frame sq and true would be appreciated. I'd like to get the top about 4 ft up. Figured you probably know about stress, angles, tube size and spacing. I'm not sure were to start on alum.
I have more questions than answers
Josh
Josh
- big gear head
-
Ace
-
Posts:
-
Joined:Thu May 07, 2015 11:46 am
-
Location:KY.
Josh, before you weld aluminum you need to know what it is. You said it's pretty hard, so it could be 7075. That grade of aluminum is classified unwedlable. That doesn't mean that you can't run a bead on it, but it does mean that the weld will likely break at some random time without warning. You should never weld something until you know what it's made of.
Freddie
I wondered. It's hard enough it has some 1/4 20 threaded holes. I was thinking of making the frame more or less a tray that the 1/4 in would drop into for a top.
I have more questions than answers
Josh
Josh
- big gear head
-
Ace
-
Posts:
-
Joined:Thu May 07, 2015 11:46 am
-
Location:KY.
Could be 6061. I put 1/4-20 threads in 6061 all the time.
I've got a few pieces of 7075 at work that I welded and the weld came out real dull and it separated from the base metal in several places before I was finished. I keep them on my bench to show people that it's a very bad idea to weld 7075. The guys here at work like to order 7075 as much as possible because it machines easier than 6061, but I try to convince them to use 6061 so that it can be welded if they screw up something or if something needs to be added to it.
I've got a few pieces of 7075 at work that I welded and the weld came out real dull and it separated from the base metal in several places before I was finished. I keep them on my bench to show people that it's a very bad idea to weld 7075. The guys here at work like to order 7075 as much as possible because it machines easier than 6061, but I try to convince them to use 6061 so that it can be welded if they screw up something or if something needs to be added to it.
Freddie
Return to “Tig Welding - Tig Welding Aluminum - Tig Welding Techniques - Aluminum Tig Welding”
Jump to
- Introductions & How to Use the Forum
- ↳ Welcome!
- ↳ Member Introductions
- ↳ How to Use the Forum
- ↳ Moderator Applications
- Welding Discussion
- ↳ Metal Cutting
- ↳ Tig Welding - Tig Welding Aluminum - Tig Welding Techniques - Aluminum Tig Welding
- ↳ Mig and Flux Core - gas metal arc welding & flux cored arc welding
- ↳ Stick Welding/Arc Welding - Shielded Metal Arc Welding
- ↳ Welding Forum General Shop Talk
- ↳ Welding Certification - Stick/Arc Welding, Tig Welding, Mig Welding Certification tests - Welding Tests of all kinds
- ↳ Welding Projects - Welding project Ideas - Welding project plans
- ↳ Product Reviews
- ↳ Fuel Gas Heating
- Welding Tips & Tricks
- ↳ Video Discussion
- ↳ Wish List
- Announcements & Feedback
- ↳ Forum News
- ↳ Suggestions, Feedback and Support
- Welding Marketplace
- ↳ Welding Jobs - Industrial Welding Jobs - Pipe Welding Jobs - Tig Welding Jobs
- ↳ Classifieds - Buy, Sell, Trade Used Welding Equipment
- Welding Resources
- ↳ Tradeshows, Seminars and Events
- ↳ The Welding Library
- ↳ Education Opportunities