Tig welding tips, questions, equipment, applications, instructions, techniques, tig welding machines, troubleshooting tig welding process
Little machine parts
- Attachments
-
- Tight only a little over 1" to get in there...without pulling the machine apart.
- IMG_20161005_170742126_HDR.jpg (28.74 KiB) Viewed 2204 times
-
- IMG_20161004_202958508.jpg (27.34 KiB) Viewed 2204 times
I weld stainless, stainless and more stainless...Food Industry, sanitary process piping, vessels, whatever is needed, I like to make stuff.
ASME IX, AWS 17.1, D1.1
Instagram #RNHFAB
ASME IX, AWS 17.1, D1.1
Instagram #RNHFAB
motox wrote:rick
you must do a lot of yoga.....
craig
The guys were laughing at me, used my elbow on my pedal had my helmet cranked so tight it may have been cutting off circulation (with a hairnet on the grip sucks) straddled 2 pieces of frame..lol Maybe I should start yoga...
Been a lot of little repairs this week, hope to get cranking on some sanitary pipe tonight
I weld stainless, stainless and more stainless...Food Industry, sanitary process piping, vessels, whatever is needed, I like to make stuff.
ASME IX, AWS 17.1, D1.1
Instagram #RNHFAB
ASME IX, AWS 17.1, D1.1
Instagram #RNHFAB
I ended up welding it butted at 65 amps walking the cup. Learned a lot. Wish I got my purge better, this big pipe is tough. I made a dam inside the pipe with cardboard cut into a circle and taped to the interior, with a hole at the top. Ferrule side was a cap with fittings I taped off and brought gas into. It welded out nice but I should have overlapped my previous welds more on my tie ins. I don't see too much more of this size coming across my table any time soon but it was a fun project. Good thing the stuff that touches this weld goes straight to the biodigester.Rick_H wrote:That's sch 10, typical my I'll put a bevel on it and tack, then backpurge and use 3/32" filler..you can get full penetration easier that way.
You can weld sch 10 butted but you have to crank it up to get through.



Little job that tested my patience and skill...
304 screen .050" diameter to 303 bar stock 1/4"...was 548 welds! Superior cup...
304 screen .050" diameter to 303 bar stock 1/4"...was 548 welds! Superior cup...
- Attachments
-
- IMG_20161013_201925596.jpg (46.53 KiB) Viewed 2079 times
-
- IMG_20161013_231837129_BURST001.jpg (67.98 KiB) Viewed 2079 times
-
- IMG_20161014_010526272.jpg (73.5 KiB) Viewed 2079 times
I weld stainless, stainless and more stainless...Food Industry, sanitary process piping, vessels, whatever is needed, I like to make stuff.
ASME IX, AWS 17.1, D1.1
Instagram #RNHFAB
ASME IX, AWS 17.1, D1.1
Instagram #RNHFAB
- LtBadd
-
Weldmonger
-
Posts:
-
Joined:Sun Apr 12, 2015 4:00 pm
-
Location:Clearwater FL
-
Contact:
@LtBadd Man I can't wait till the rest of the shit is gone...only because it was here, to tell the truth most mechanics I work with couldn't tell the difference or even care about the difference. I was mad, you give me something difficult to weld anyway by design, then give me 303 for the frame.... thanks.LtBadd wrote:I know you had fun with this oneRick_H wrote:Little job that tested my patience and skill...
304 screen .050" diameter to 303 bar stock 1/4"...was 548 welds! Superior cup...why was 303 bar used??
When I start mentioning different filler and material grades and why you use what I get the "your just he welding nazi look or you think your better then us look" at time I feel I'm the only one that cares.
An old vendor slid 303 in instead of 304 at a cost savings, the buyer had no clue what the difference was and the vendor said "it will preform the same".
I weld stainless, stainless and more stainless...Food Industry, sanitary process piping, vessels, whatever is needed, I like to make stuff.
ASME IX, AWS 17.1, D1.1
Instagram #RNHFAB
ASME IX, AWS 17.1, D1.1
Instagram #RNHFAB
exnailpounder
- exnailpounder
-
Weldmonger
-
Posts:
-
Joined:Thu Dec 25, 2014 9:25 am
-
Location:near Chicago
Quit complaining...it could have been galvanized screen 

Ifyoucantellmewhatthissaysiwillbuyyouabeer.
exnailpounder wrote:Quit complaining...it could have been galvanized screen

I weld stainless, stainless and more stainless...Food Industry, sanitary process piping, vessels, whatever is needed, I like to make stuff.
ASME IX, AWS 17.1, D1.1
Instagram #RNHFAB
ASME IX, AWS 17.1, D1.1
Instagram #RNHFAB
GreinTime
- GreinTime
-
Weldmonger
-
Posts:
-
Joined:Fri Nov 01, 2013 11:20 am
-
Location:Pittsburgh, PA
I feel the same man. 4943 would be a much better choice in filler for what we do at work since all of our welds (for the most part) get finished flush. Mention cost to one of the head welders, he responds "Don't waste your breath, they'll never do it."Rick_H wrote: When I start mentioning different filler and material grades and why you use what I get the "your just he welding nazi look or you think your better then us look" at time I feel I'm the only one that cares.
Ask why we use 308 to weld steel bolts in stainless frames and vice versa... "It's what we have. They'll never buy another alloy, you're wasting your breath. If it bothers you that bad, use 316."
Me: "You guys that are too lazy to grab 70S2 are going to have a bad day if one of those pieces for a quartz wall retainer break and you welded it with 308." "It's what we have on the table, and it welds nicer than carbon wire." This is more of a shiny mill scale versus clean steel issue, as it seems like half the parts are 1027, which is a dream compared to the A500 that the other half of the parts are made from. That oily black coating takes a lot of finesse (and swearing) to get through to where you have clean steel versus polished mill scale. It skins up a weld done with 308, but to the people that happen to look at them as they go out the door, it looks better than a filmy Grey looking weld done with carbon.
I think they summed it up best in podcast 11 with David Blackburn where they talk about "All in welders VS Rod Burners" and I find that the crew on first shift seem to be rod burners, and everyone on second shift tends to be more geared towards understanding why they are doing what they do, or why myself or my shift lead question why they are doing something this way vs another way. I've also been teaching all of them how to use the Dynasty that's in their booth to its full potential, with pulse and amplitude adjustments on AC. First shift could care less, they use a profile one of the guys came up with in a few minutes that gave them relatively decent results.
Sent from my SM-G900V using Tapatalk
#oneleggedproblems
-=Sam=-
-=Sam=-
- LtBadd
-
Weldmonger
-
Posts:
-
Joined:Sun Apr 12, 2015 4:00 pm
-
Location:Clearwater FL
-
Contact:
exnailpounder
- exnailpounder
-
Weldmonger
-
Posts:
-
Joined:Thu Dec 25, 2014 9:25 am
-
Location:near Chicago
Was Tig mandated for these? To me thats totally Mig territory.
Ifyoucantellmewhatthissaysiwillbuyyouabeer.
i like doing that kind of stuff but not 150 of them..........
by the third one your in the groove, buy number 100
it would be WTF.
craig
by the third one your in the groove, buy number 100
it would be WTF.
craig
htp invertig 221
syncrowave 250
miller 140 mig
hypertherm plasma
morse 14 metal devil
syncrowave 250
miller 140 mig
hypertherm plasma
morse 14 metal devil
GreinTime
- GreinTime
-
Weldmonger
-
Posts:
-
Joined:Fri Nov 01, 2013 11:20 am
-
Location:Pittsburgh, PA
I'll take a picture of these chair frames we did when I get to work this afternoon, I think we did 225 over a week, with 3 people per shift welding them... Now they are getting skins, which is taking less time, but are more tedious.motox wrote:i like doing that kind of stuff but not 150 of them..........
by the third one your in the groove, buy number 100
it would be WTF.
craig
Sent from my SM-G900V using Tapatalk
#oneleggedproblems
-=Sam=-
-=Sam=-
- subwayrocket
-
Ace
-
Posts:
-
Joined:Thu Aug 13, 2015 11:38 pm
-
Location:Scranton/WilkesBarre, Pennsylvania
I'm still a student and this is what I did today:
Some schedule 80 carbon pipe in the 6G position, Tig root, Tig out,
Not sure why the photos are rotated that way, probably my cheap phone.
Some schedule 80 carbon pipe in the 6G position, Tig root, Tig out,
Not sure why the photos are rotated that way, probably my cheap phone.
- Attachments
-
- 1020162047.jpg (42.14 KiB) Viewed 1757 times
-
- 1020162047a.jpg (32.36 KiB) Viewed 1757 times
Thanks. Walking the cup. It's a little harder with pipe that big but using a number 12 cup helps a lot. Since it's 6G I do it left handed on one side and right on the other. I'm planning on trying to test soon so hopefully it goes well.Coldman wrote:You did a nice job on the cap. Is that walking the cup or free hand?
Sent from my iPhone using Tapatalk
Best TIG result so far for me, except at the end when I touched the rod to the electrode and things went wonky. I'm about half of an 85cf argon bottle into my TIG career at this point.
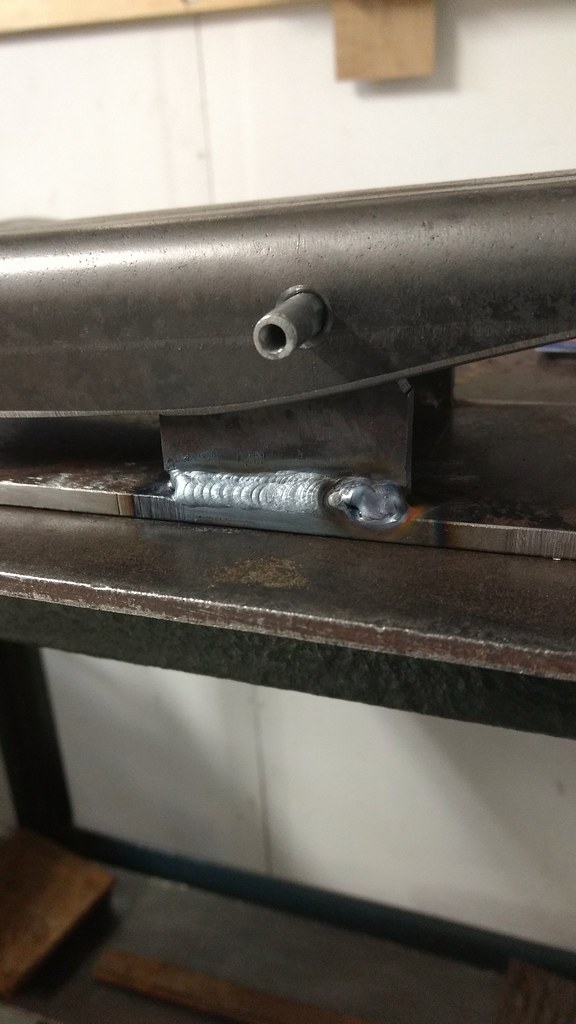
This is for the TIG pedal I am building, it will have three potentiometers, one connected to the pedal and two that will be here on the front, to set the lower and upper range. Copying the actual kemppi pedal on that design feature. You can't just set that on the welder on this machine.
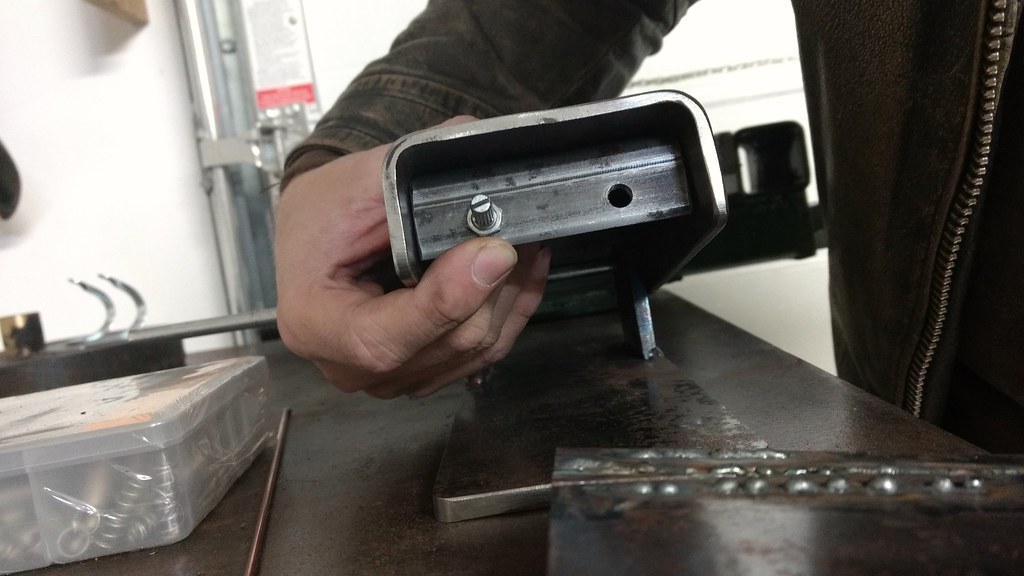
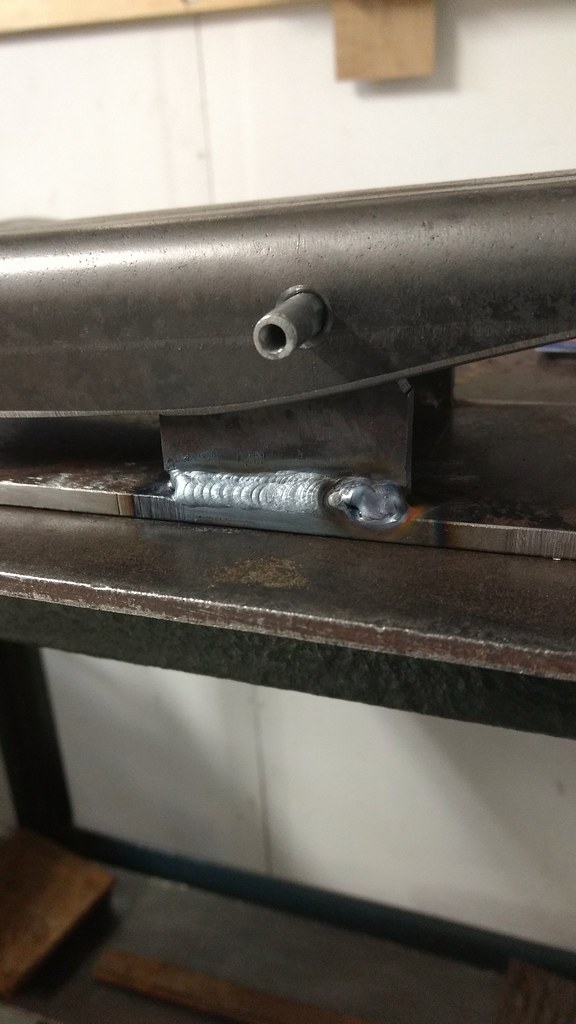
This is for the TIG pedal I am building, it will have three potentiometers, one connected to the pedal and two that will be here on the front, to set the lower and upper range. Copying the actual kemppi pedal on that design feature. You can't just set that on the welder on this machine.
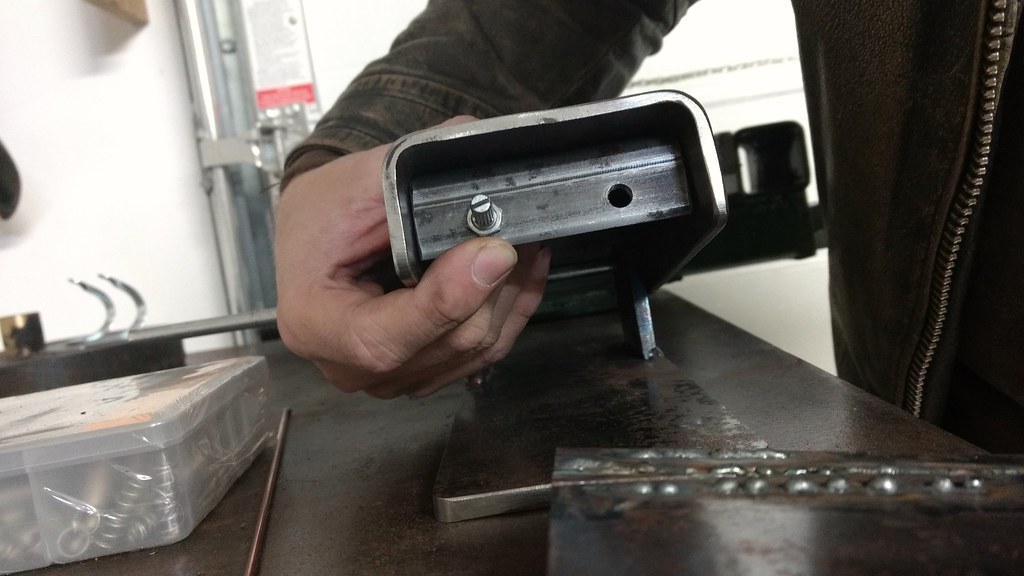
- LtBadd
-
Weldmonger
-
Posts:
-
Joined:Sun Apr 12, 2015 4:00 pm
-
Location:Clearwater FL
-
Contact:
Return to “Tig Welding - Tig Welding Aluminum - Tig Welding Techniques - Aluminum Tig Welding”
Jump to
- Introductions & How to Use the Forum
- ↳ Welcome!
- ↳ Member Introductions
- ↳ How to Use the Forum
- ↳ Moderator Applications
- Welding Discussion
- ↳ Metal Cutting
- ↳ Tig Welding - Tig Welding Aluminum - Tig Welding Techniques - Aluminum Tig Welding
- ↳ Mig and Flux Core - gas metal arc welding & flux cored arc welding
- ↳ Stick Welding/Arc Welding - Shielded Metal Arc Welding
- ↳ Welding Forum General Shop Talk
- ↳ Welding Certification - Stick/Arc Welding, Tig Welding, Mig Welding Certification tests - Welding Tests of all kinds
- ↳ Welding Projects - Welding project Ideas - Welding project plans
- ↳ Product Reviews
- ↳ Fuel Gas Heating
- Welding Tips & Tricks
- ↳ Video Discussion
- ↳ Wish List
- Announcements & Feedback
- ↳ Forum News
- ↳ Suggestions, Feedback and Support
- Welding Marketplace
- ↳ Welding Jobs - Industrial Welding Jobs - Pipe Welding Jobs - Tig Welding Jobs
- ↳ Classifieds - Buy, Sell, Trade Used Welding Equipment
- Welding Resources
- ↳ Tradeshows, Seminars and Events
- ↳ The Welding Library
- ↳ Education Opportunities