Even more impressive!GreinTime wrote:The whole thing was done consecutively alternating joint to joint. I think it's 4" sections maybe?Oscar wrote:The titanium came out nice! Sucks having to wait for it to cool down though.
Sent from my VS995 using Tapatalk
Tig welding tips, questions, equipment, applications, instructions, techniques, tig welding machines, troubleshooting tig welding process
GreinTime
- GreinTime
-
Weldmonger
-
Posts:
-
Joined:Fri Nov 01, 2013 11:20 am
-
Location:Pittsburgh, PA
Those are done with a Dynasty 350 inverter. I'd like to try one with a Syncrowave, just for shits and giggles.dunkster wrote:Super nice consistency on the coolers there Sam!....inverter or transformer machine?
Nice TI work as well....jealous.
Sent from my VS995 using Tapatalk
#oneleggedproblems
-=Sam=-
-=Sam=-
GreinTime
- GreinTime
-
Weldmonger
-
Posts:
-
Joined:Fri Nov 01, 2013 11:20 am
-
Location:Pittsburgh, PA
I don't pay for argonOscar wrote:Even more impressive!GreinTime wrote:The whole thing was done consecutively alternating joint to joint. I think it's 4" sections maybe?Oscar wrote:The titanium came out nice! Sucks having to wait for it to cool down though.
Sent from my VS995 using Tapatalk


Sent from my VS995 using Tapatalk
#oneleggedproblems
-=Sam=-
-=Sam=-
what do you do when work is slow and nothing to do for a few hours, you bend and weld up a brushed stainless mailbox to replace the broken plastic one that was on a rotting pole leaning into your driveway... and throw a quick name letter on it in the last 5 minutes of the day using the notcher and a cut off blade on the grinder... of course the rental house is still nasty but there's a nice shiny mailbox! ha...
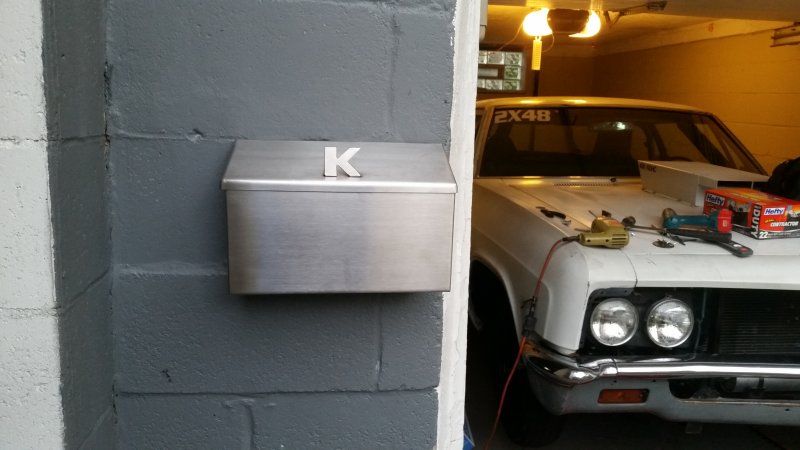
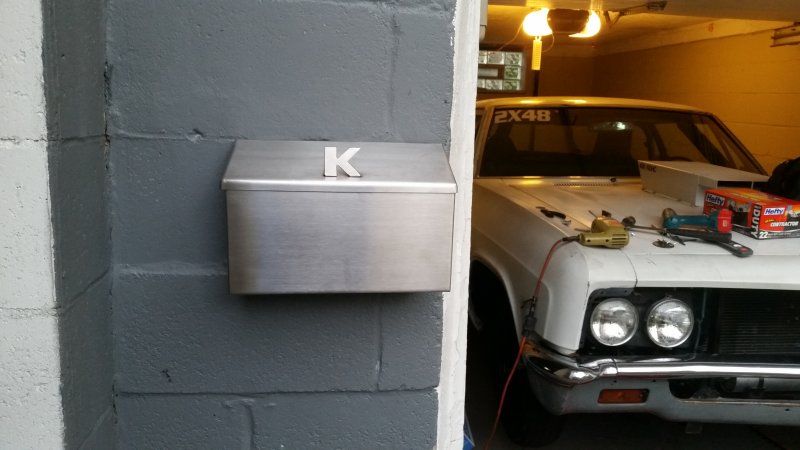
can't believe it took me this many years to buy a diamond wheel for my bench grinder... what a difference
- LtBadd
-
Weldmonger
-
Posts:
-
Joined:Sun Apr 12, 2015 4:00 pm
-
Location:Clearwater FL
-
Contact:
Looks nice!raticus wrote:what do you do when work is slow and nothing to do for a few hours, you bend and weld up a brushed stainless mailbox to replace the broken plastic one that was on a rotting pole leaning into your driveway... and throw a quick name letter on it in the last 5 minutes of the day using the notcher and a cut off blade on the grinder... of course the rental house is still nasty but there's a nice shiny mailbox! ha...
Richard
Website
Website




This is a remodel of a poling platform. The customer bought a new motor with a jack and the platform had to be elevated 12 inches. I also had to add steps in the front due to the width of the fiberglass top.
Sent from my SCH-I545 using Tapatalk
- LtBadd
-
Weldmonger
-
Posts:
-
Joined:Sun Apr 12, 2015 4:00 pm
-
Location:Clearwater FL
-
Contact:
Looks good, welds and fab work!Warrenh wrote:
This is a remodel of a poling platform. The customer bought a new motor with a jack and the platform had to be elevated 12 inches. I also had to add steps in the front due to the width of the fiberglass top.
Sent from my SCH-I545 using Tapatalk
Richard
Website
Website
- 5th Street Fab
-
Guide
-
Posts:
-
Joined:Sun Jan 15, 2017 1:08 am
Battery tray for my truck from this weekend
Before cutting up the brackets and redoing them




After





And installed where it'll never be seen again.

Sent from my SM-G920V using Tapatalk
Before cutting up the brackets and redoing them




After





And installed where it'll never be seen again.

Sent from my SM-G920V using Tapatalk
- MosquitoMoto
-
Weldmonger
-
Posts:
-
Joined:Sat Aug 01, 2015 8:38 am
-
Location:The Land Down Under
- 5th Street Fab
-
Guide
-
Posts:
-
Joined:Sun Jan 15, 2017 1:08 am
Ya it was a bummer after I installed it haha oh well!MosquitoMoto wrote:Very nice!
Don't you hate hiding the good stuff?
Moz
Sent from my SM-G920V using Tapatalk
the welding process is smaw (stick) we use 7018 for the vessel. This weld is a code or stamped weld it will be QCed under 31.12 boiler code ( no under cut or any indication while they pt it) and stamped with ASME stamp .after that we will hydro the tank to 300 psi twice the stamped pressure. This vessel is apart of a water treatment plant for a power house. Definitely not glamorous but I love what I do and being challenged every day and pushed to weld at a very high standard has put me and a very fortunate situation!Coldman wrote:Maybe not glamorous to you but involves serious skill and experience. Good job!
Now you have to elaborate on process and procedure used please.
Had to repair some dirty old stainless can't always be weldporn with new material at a bench. There is something satisfying about welding all curled up like a pretzel.
I couldn't get to the backside of this weld really good to clean a couple spots gave me issues.
I couldn't get to the backside of this weld really good to clean a couple spots gave me issues.
- Attachments
-
- All ground out
- IMG_20170703_103237349.jpg (25.23 KiB) Viewed 4321 times
-
- IMG_20170703_112641899.jpg (24.54 KiB) Viewed 4321 times
-
- IMG_20170703_133703977.jpg (21.93 KiB) Viewed 4321 times
I weld stainless, stainless and more stainless...Food Industry, sanitary process piping, vessels, whatever is needed, I like to make stuff.
ASME IX, AWS 17.1, D1.1
Instagram #RNHFAB
ASME IX, AWS 17.1, D1.1
Instagram #RNHFAB
- LtBadd
-
Weldmonger
-
Posts:
-
Joined:Sun Apr 12, 2015 4:00 pm
-
Location:Clearwater FL
-
Contact:
We all know that's true, good work as always RickRick_H wrote:Had to repair some dirty old stainless can't always be weldporn with new material at a bench. There is something satisfying about welding all curled up like a pretzel.
I couldn't get to the backside of this weld really good to clean a couple spots gave me issues.
Richard
Website
Website
Bingo wrote:Well on this Friday we get back in our tig rigs 4" sch 40 70s6 ( not my favorite wire for carbon) welding under code 31.3
Nice work, I prefer 70s2 if allowed personally.
I weld stainless, stainless and more stainless...Food Industry, sanitary process piping, vessels, whatever is needed, I like to make stuff.
ASME IX, AWS 17.1, D1.1
Instagram #RNHFAB
ASME IX, AWS 17.1, D1.1
Instagram #RNHFAB
Making a new turbo back system for my MK4 TDI, 3" dp, 3" straight system....and I know you guys are shocked it's stainless and sanitary welded. 

- Attachments
-
- IMG_20170707_112251881.jpg (43.72 KiB) Viewed 4852 times
-
- IMG_20170707_112225483.jpg (40.09 KiB) Viewed 4852 times
I weld stainless, stainless and more stainless...Food Industry, sanitary process piping, vessels, whatever is needed, I like to make stuff.
ASME IX, AWS 17.1, D1.1
Instagram #RNHFAB
ASME IX, AWS 17.1, D1.1
Instagram #RNHFAB
Only until he fires it up...Bingo wrote:Clean!

I'm going to have to work on my pipe welding, I want one for my TDI, but can't stand the thought of paying what the commercial offerings are asking!
-Josh
Greasy fingered tinkerer.
Greasy fingered tinkerer.
Yeah there was no way I was going to pay near $300 for a DP, I actually don't have a ton of money in everything front to back. I bought some fittings from Andron Stainless, if I knew how to pie cut or.could easily cut those at home I would have saved even more. It's been fun...have to mock it up today to get the angle of the DP right and make the middle section....then just weld it and add hangers. I used a 2"-3" reducer at the flange so I'd have bolt clearance, and a Vibrant Flex joint.hey_allen wrote:Only until he fires it up...Bingo wrote:Clean!![]()
I'm going to have to work on my pipe welding, I want one for my TDI, but can't stand the thought of paying what the commercial offerings are asking!
I weld stainless, stainless and more stainless...Food Industry, sanitary process piping, vessels, whatever is needed, I like to make stuff.
ASME IX, AWS 17.1, D1.1
Instagram #RNHFAB
ASME IX, AWS 17.1, D1.1
Instagram #RNHFAB
GreinTime
- GreinTime
-
Weldmonger
-
Posts:
-
Joined:Fri Nov 01, 2013 11:20 am
-
Location:Pittsburgh, PA
Prototype done for the 10th Gen Civic Intercooler and Charge Pipe setup.
First time welding cast with 5356, can't say I'm really a fan. I don't know if I'll get to weld anymore of these, but we'll see if I can weld one with 5356, 4043, and 4943 back to back to back (batch work is nice for testing some times) with identical settings and see who can tell what!


Sent from my VS995 using Tapatalk
First time welding cast with 5356, can't say I'm really a fan. I don't know if I'll get to weld anymore of these, but we'll see if I can weld one with 5356, 4043, and 4943 back to back to back (batch work is nice for testing some times) with identical settings and see who can tell what!



Sent from my VS995 using Tapatalk
#oneleggedproblems
-=Sam=-
-=Sam=-
Return to “Tig Welding - Tig Welding Aluminum - Tig Welding Techniques - Aluminum Tig Welding”
Jump to
- Introductions & How to Use the Forum
- ↳ Welcome!
- ↳ Member Introductions
- ↳ How to Use the Forum
- ↳ Moderator Applications
- Welding Discussion
- ↳ Metal Cutting
- ↳ Tig Welding - Tig Welding Aluminum - Tig Welding Techniques - Aluminum Tig Welding
- ↳ Mig and Flux Core - gas metal arc welding & flux cored arc welding
- ↳ Stick Welding/Arc Welding - Shielded Metal Arc Welding
- ↳ Welding Forum General Shop Talk
- ↳ Welding Certification - Stick/Arc Welding, Tig Welding, Mig Welding Certification tests - Welding Tests of all kinds
- ↳ Welding Projects - Welding project Ideas - Welding project plans
- ↳ Product Reviews
- ↳ Fuel Gas Heating
- Welding Tips & Tricks
- ↳ Video Discussion
- ↳ Wish List
- Announcements & Feedback
- ↳ Forum News
- ↳ Suggestions, Feedback and Support
- Welding Marketplace
- ↳ Welding Jobs - Industrial Welding Jobs - Pipe Welding Jobs - Tig Welding Jobs
- ↳ Classifieds - Buy, Sell, Trade Used Welding Equipment
- Welding Resources
- ↳ Tradeshows, Seminars and Events
- ↳ The Welding Library
- ↳ Education Opportunities