Page 1 of 4
scotch briteing tungsten?
Posted: Tue Aug 09, 2016 4:36 pm
by maker of things
Is it okay to clean soot off a tungsten with scotchbrite? I swear I saw Jody do this in a video. Say if you did not set enough postflow and the tungsten lost it's silver.
Re: scotch briteing tungsten?
Posted: Tue Aug 09, 2016 4:53 pm
by Poland308
Won't cause problems on steel. But if your into high end SS or aluminum. That needs a critical finish then it might be debatable. But most likely as long as it's not contaminated with oil or something it's going to be ok.
Re: scotch briteing tungsten?
Posted: Tue Aug 09, 2016 5:14 pm
by LtBadd
I've used a scotch brite wheel on a bench grinder to clean a just sharpen tungsten, not sure if by hand it would be as effective. If you didn't have enough post flow then SB may not be (aggressive) enough to get the job done.
Re: scotch briteing tungsten?
Posted: Tue Aug 09, 2016 6:37 pm
by Rick_H
I use it on mine, smooths out the starts IMO. I do sharpen with a dedicated tungsten grinder as well.
Re: scotch briteing tungsten?
Posted: Tue Aug 09, 2016 8:44 pm
by Oscar
I use the harbor freight mini 3" bench grinder with the polishing wheel. Cleans/polishes the tungsten very nicely.
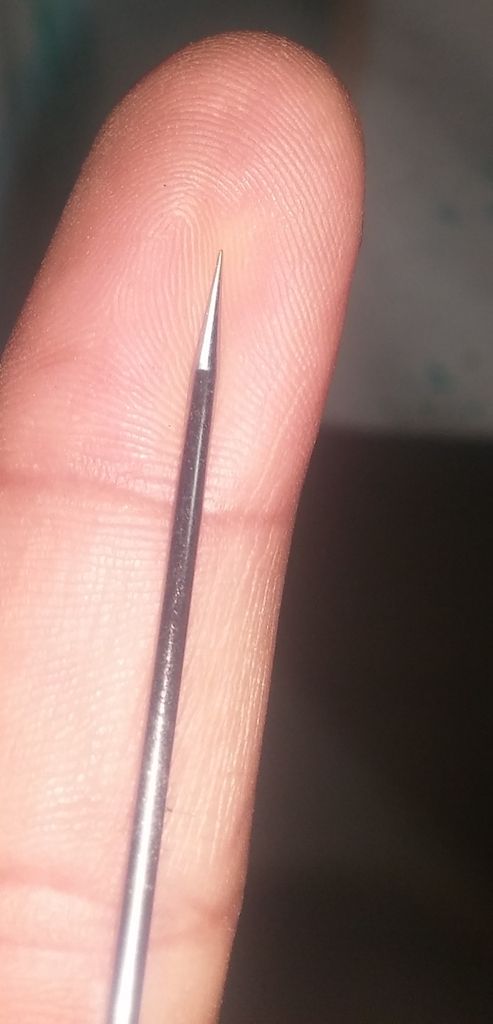
Re: scotch briteing tungsten?
Posted: Tue Aug 09, 2016 9:55 pm
by LtBadd
Oscar wrote:I use the harbor freight mini 3" bench grinder with the polishing wheel. Cleans/polishes the tungsten very nicely.
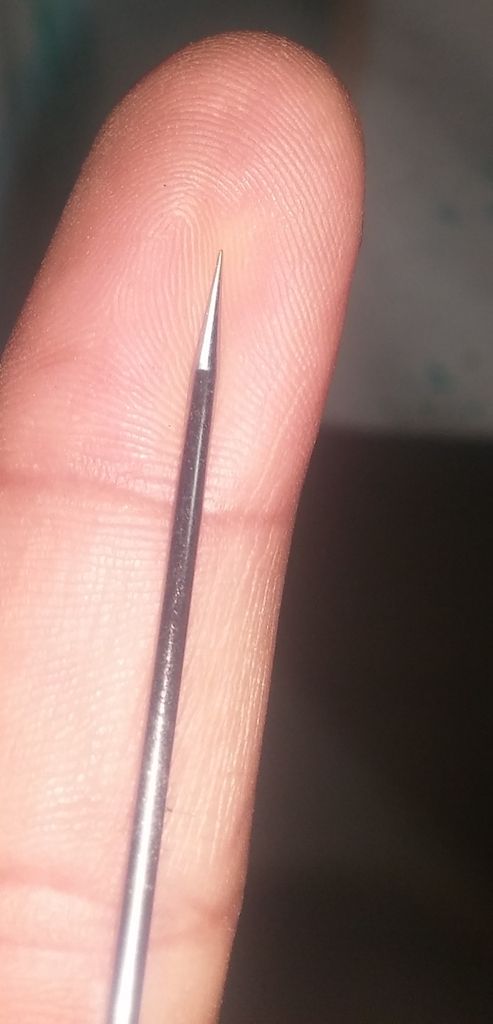
Oscar, do you think it's safe posting your fingerprint on the net?

Re: scotch briteing tungsten?
Posted: Wed Aug 10, 2016 6:59 am
by maker of things
Do you think it would make a difference if the abrasive was used in a axial vs rotational method. i.e. if the scratch lines go around the tungsten will it cause problems like if you ground it that way, or are the scratches so fine it won't matter? Or am I the only one that gets crap all up his tungsten? (not a euphemism).
Re: scotch briteing tungsten?
Posted: Wed Aug 10, 2016 9:09 am
by Oscar
LtBadd wrote:Oscar wrote:I use the harbor freight mini 3" bench grinder with the polishing wheel. Cleans/polishes the tungsten very nicely.
Oscar, do you think it's safe posting your fingerprint on the net?

worst that can happen is someone falsely punches in to go work for me and does my work, lol.
maker of things wrote:Do you think it would make a difference if the abrasive was used in a axial vs rotational method. i.e. if the scratch lines go around the tungsten will it cause problems like if you ground it that way, or are the scratches so fine it won't matter? Or am I the only one that gets crap all up his tungsten? (not a euphemism).
Yes, you will notice a difference if you are using a coarse grained grinding wheel and if you are welding at the lower-end of the amperage range for a given tungsten size. Probably not so much on the upper end, but yea proper tungsten sharpening should be the first think anyone learns about TIG welding.
Re: scotch briteing tungsten?
Posted: Wed Aug 10, 2016 9:17 am
by Rick_H
maker of things wrote:Do you think it would make a difference if the abrasive was used in a axial vs rotational method. i.e. if the scratch lines go around the tungsten will it cause problems like if you ground it that way, or are the scratches so fine it won't matter? Or am I the only one that gets crap all up his tungsten? (not a euphemism).
I have not seen any difference running it either way by hand, it only smoothes the grind which should be pretty smooth.
If your getting a bunch or contamination on the tungsten it is best to snap or cut it off and regrind. If you use a grinder or grinding wheel and grind off the blob you are just impregnating the stone which in turn will put it back on your tungsten when you sharpen
Re: scotch briteing tungsten?
Posted: Wed Aug 10, 2016 12:07 pm
by maker of things
Rick_H wrote: If your getting a bunch or contamination on the tungsten it is best to snap or cut it off and regrind. If you use a grinder or grinding wheel and grind off the blob you are just impregnating the stone which in turn will put it back on your tungsten when you sharpen
snapping off is what I have been doing after co-mingling aluminum and tungsten. Sometimes I just get some of the oxide on the tungsten all the way up to the cup and it never occurred to me to try just scouring it off until I thought I saw Jody do it in a video.
Oscar, I am aware of the potential issues with grinding around the rotational axis so I always grind properly, was wondering if the fine scratches the scotchbrite leaves would do the same thing. Based on the responses so far I'm going to go out on a limb a state that I must have misinterpreted what I saw or thought I saw in the video.
Re: scotch briteing tungsten?
Posted: Wed Aug 10, 2016 12:36 pm
by entity-unknown
I'm a n00b with zero skill but I did learn a bit about the tungsten grind being very critical for any decent arc control especially on AC. When I first started grinding I used the bottom of the arbor and had very inconsistent grind patterns, even some flat spots. When running on AC my arc seemed to spend most of it's time arc'ing to the cup rather than the plate unless I really mashed the pedal that it was like 25% of the time I had arc to the plate. I had basically what looked like radiation burns all over my aluminum and the cup looked horrible amongst a balled tip, and some nasty crap all over the inside of the gas lens, cup, and tungsten.
I RTFM'd and it said I was grinding with the wrong side of the arbor. I should be using the top. I haven't changed any parameters on my machine but since I started grinding using this method I have generally had a decent arc. I still gotta figure out the taper and I'm using a fine point despite their suggestion of a slightly nubbed end for 50+ Amps, but I've actually been able to melt metal and even got some half way decent runs. My tip doesn't ball either so if I've learnd'ed enough properly, I think it's fair to say I'm doing ok otherwise I'd be ballin. Still much to learn but this bit in the manual seemed to be the most important thing for me to even get started.
Again, still a n00b with zero skill but I've been switching between aluminum and steel with a re-grind almost always. Honestly if the tip looked good and I didn't regrind before swapping material, I didn't notice too much issue. As long as I gently grinded off any crap that got on the tungsten from dipping in the aluminum and kept a decent point with what looks like fresh tungsten (even after a few runs) not scaly tungsten, things generally seemed to work out ok beyond what the operator is capable of. It didn't even seem to contaminate the work much but don't take my word on that. The only real contamination I've noticed that surfaces is almost always because I'm not really cleaning my part much as I keep practicing. Seems helpful because I'm seeing the differences between dipping the tip vs. bad cleaning practices. My observations tell me the pepper crap that surfaces is bad cleaning, and the white halo turned to black is always from dipping.
The rest of these experts will give you way better advice but for the n00b having a lot of this fresh in mind I thought this might be helpful too

Re: scotch briteing tungsten?
Posted: Wed Aug 10, 2016 12:42 pm
by maker of things
When I get home I will post some pics, yeah the material was really bad. Some 1/4" 6063 that was in the steel scrap for a long time, then I cleaned it with aluminum oxide sandpaper. All by the book right? At least the part that says "don't do this". I was very anxious to run the dynasty to see if it would trip the breaker so I just went for it. When it welded, it welded nice, when I hit a steel or aluminum oxide inclusion it was 4th of july!
Re: scotch briteing tungsten?
Posted: Wed Aug 10, 2016 12:47 pm
by entity-unknown
Sounds like we're riding the same road to ripples right now
Probably the two most important things every TIG welder I've heard so far express, tungsten and cleaning. If you don't understand these and get em right, you're probably never going to enjoy TIG'in with AMPle frustration. Amps doesn't matter, controls and features don't matter, unless you get these two right.
One random tip I also learned.... make sure that Pedal can stay secure. I got a smooth garage floor and my pedal ran away from me a few times which basically caused me to dip, over heat, under heat, ball my filler, squirm to gain control and simply fail at everything.
Re: scotch briteing tungsten?
Posted: Wed Aug 10, 2016 1:38 pm
by maker of things
I'm not exactly new to welding. I completed the 100 level course (OA and stick) at my local CC a couple decades ago. Lately I have been wanting to improve my welding. I'm watching pretty much all of Jody's vids so I'm picking up some good tips. My aluminum problems were mostly because I have poor technique and was hasty. I just got a bunch of 11ga 3003 aluminum squares to run Jody's welding drills. I bought a hook n loop backer for my angle grinder and a stack of matching scotchbrite pads to clean the surface. I already picked up some acetone so as soon as I can free up some time and it isn't 95 feekin degrees when I get home from work, I will be running the crap out of those.
Re: scotch briteing tungsten?
Posted: Wed Aug 10, 2016 4:07 pm
by Oscar
maker of things wrote:Rick_H wrote: If your getting a bunch or contamination on the tungsten it is best to snap or cut it off and regrind. If you use a grinder or grinding wheel and grind off the blob you are just impregnating the stone which in turn will put it back on your tungsten when you sharpen
snapping off is what I have been doing after co-mingling aluminum and tungsten. Sometimes I just get some of the oxide on the tungsten all the way up to the cup and it never occurred to me to try just scouring it off until I thought I saw Jody do it in a video.
Oscar, I am aware of the potential issues with grinding around the rotational axis so I always grind properly, was wondering if the fine scratches the scotchbrite leaves would do the same thing. Based on the responses so far I'm going to go out on a limb a state that I must have misinterpreted what I saw or thought I saw in the video.
Ah I see. No, the fine scratches the scotchbrite leaves are much much finer than those left by an aluminum oxide grinding wheel. A fine-grit diamond wheel likely does much better of course. I will say though, after scotchbrite'ing myself, it's much too time consuming to get acceptable results in a short amount of time. That is why I resorted to power tools. Takes but a few seconds.
Re: scotch briteing tungsten?
Posted: Wed Aug 10, 2016 4:26 pm
by maker of things

- IMG_20160810_151605288_HDR.jpg (94.11 KiB) Viewed 1752 times
This is what was talking about. On the right is "before" and the left "after". Would you guys normally grind the discolored area after removing the ball?
Re: scotch briteing tungsten?
Posted: Wed Aug 10, 2016 4:40 pm
by exnailpounder
You mentioned using a Dynasty machine. Thats an inverter machine if I am not mistaken. What type of tungsten are you using? You aren't supposed to use pure tungsten on inverter machines if thats what your using. That is one HELL of a balled up tungsten

I have an inverter and I use lanthanated and thoriated and my tungsten never balls like that. I get a little ball at the very tip but thats it. A little more info please.
Re: scotch briteing tungsten?
Posted: Wed Aug 10, 2016 6:16 pm
by entity-unknown
Yeah sorry maker, I realized you're far from a n00b a bit later on. DOH! No more caffeine today...
Re: scotch briteing tungsten?
Posted: Wed Aug 10, 2016 6:58 pm
by maker of things
No sweat. Either way it's still off to practice running beads right?
Re: scotch briteing tungsten?
Posted: Wed Aug 10, 2016 9:20 pm
by Oscar
Unless you dipped into the puddle, just grind the whole thing back down to a point. Then you can scotchbrite the outside oxidation to get it nice and clean.
But like the others said, you have bigger problems if your tungsten is balling that much. You need to either jump to a bigger tungsten size depending on your weld parameters, of you need to adjust your weld parameters in the first place.
Re: scotch briteing tungsten?
Posted: Wed Aug 10, 2016 9:26 pm
by exnailpounder
Oscar wrote:Unless you dipped into the puddle, just grind the whole thing back down to a point. Then you can scotchbrite the outside oxidation to get it nice and clean.
But like the others said, you have bigger problems if your tungsten is balling that much. You need to either jump to a bigger tungsten size depending on your weld parameters, of you need to adjust your weld parameters in the first place.
That ball was so big it should have hair growing on it. I never used pure on my inverter but I am betting that this is what happens when you do.
Re: scotch briteing tungsten?
Posted: Wed Aug 10, 2016 10:06 pm
by Oscar
exnailpounder wrote:Oscar wrote:Unless you dipped into the puddle, just grind the whole thing back down to a point. Then you can scotchbrite the outside oxidation to get it nice and clean.
But like the others said, you have bigger problems if your tungsten is balling that much. You need to either jump to a bigger tungsten size depending on your weld parameters, of you need to adjust your weld parameters in the first place.
That ball was so big it should have hair growing on it. I never used pure on my inverter but I am betting that this is what happens when you do.
Yup, you unnecessarily give up so much arc control. All advanced inverter settings go out the window once that half-moon shows it's face.
Re: scotch briteing tungsten?
Posted: Thu Aug 11, 2016 2:29 am
by GreinTime
Oscar wrote:exnailpounder wrote:Oscar wrote:Unless you dipped into the puddle, just grind the whole thing back down to a point. Then you can scotchbrite the outside oxidation to get it nice and clean.
But like the others said, you have bigger problems if your tungsten is balling that much. You need to either jump to a bigger tungsten size depending on your weld parameters, of you need to adjust your weld parameters in the first place.
That ball was so big it should have hair growing on it. I never used pure on my inverter but I am betting that this is what happens when you do.
Yup, you unnecessarily give up so much arc control. All advanced inverter settings go out the window once that half-moon shows it's face.
For what it's worth, I can run at 330a on AC for 10 hours and never dull the end of an 1/8" tungsten (taking it swimming excluded) with one of the Dynasty 350s at work. At 310a on a Sync 250 with Max penetration (68% EN) the same piece of La lasts 5-6" at full pedal before it looks like some sort of creature. It makes for some interesting arc starts after that point, but it's not worth sharpening again until I dip because it works.
Tungsten is critical to providing the best experience possible while practicing, but it's worth welding with a piece of shit as well as you don't always have extras and/or a grinder to freshen it up on the fly.
Sent from my SM-G900V using Tapatalk
Re: scotch briteing tungsten?
Posted: Thu Aug 11, 2016 5:13 am
by maker of things
That's just what I could find laying around that had the oxidization on it. I don't even like pure tungsten on a transfomer machine. Those pieces are 3/32 ceriated that I dipped and then kept trying to weld with. I think that is from when I was welding some 1/4" from the same scrap aluminum with my longevity. I had so much oxide floating on top of the puddle, I think the only thng that made the weld stick was the shear volume of profanity that I was hurling at it.
Re: scotch briteing tungsten?
Posted: Sun Aug 14, 2016 2:56 pm
by entity-unknown
While it's not tungsten, I found scotch brite for the ER70S2 Filler was very helpful. I noticed some others saying they do it religiously for their stainless steel fillers. Not sure about aluminum but can't see why not.
My filler looked shiny but had packaging issues during shipment and I think it got some dust n stuff and probably was just dirty to begin with. Kinda like shiny aluminum is not clean aluminum..?
I had constant dull welds no matter what I was doing. After a lil scotch brite on the next filler, I started seeing color in my basic beads and welds more often than not which I had never seen before.
There is a lot more to getting good or even slightly pretty welds then just this but it really helps and the three C rules of TIG really apply for EVERYTHING even your filler rod. I think this was responsible for a lot of what appeared to me as me dipping/stabbing my tungsten but I never did and the parts were clean so it was driving me insane. Cleaned the filler rod, things don't look so horrible anywhere anymore (until I screw up).
clean, Clean, CLEAN!