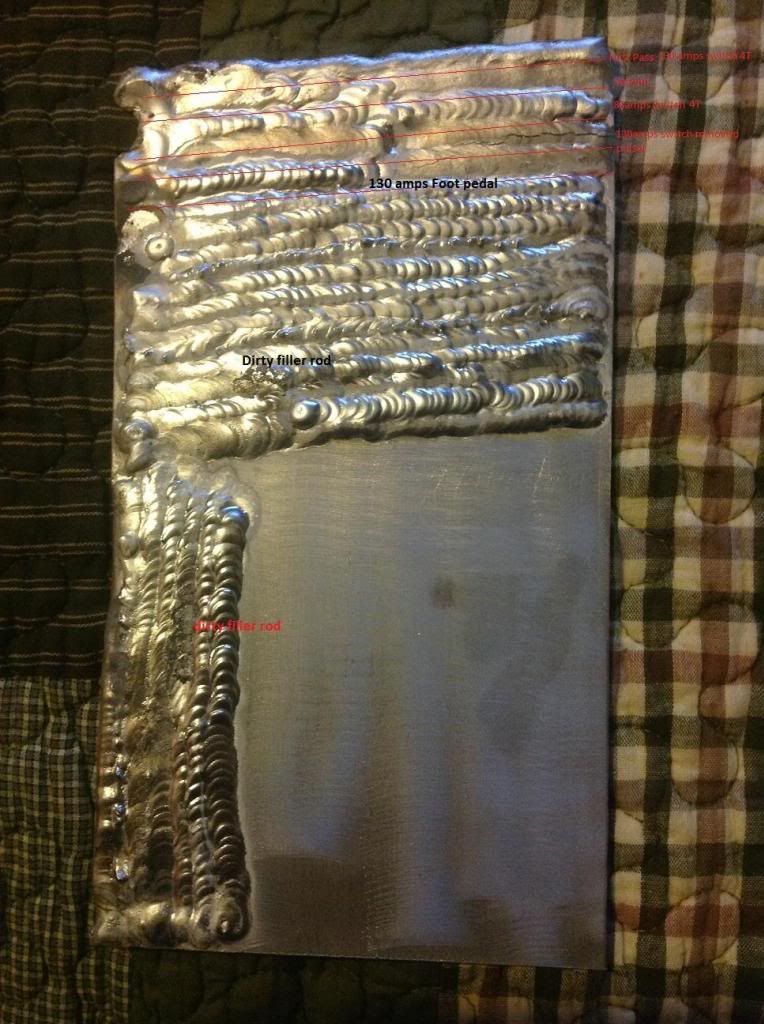
his settings were
amps 130-150
balance 65%-70%
Frequency 100-120hz (i don't have this setting)
Electrode 3/32 slight taper
Argon 11-15 cfh
Cup #5 gas lens
my settings that worked
amps 80 with arc start switch 130 with foot pedal at 60%
Balance 60-70%
Electrode started with taper but balled up to a stub in 2 seconds
Cup #6 no lens
Nothing i could do to narrow the puddle as the ball had it spread pretty wide. But the puddle was a mirror. the first passes at the top of the plate melted the edge right off with A.S.S. and 4T. after 3 passes I went to 80 amps and A.S.S. 4T. I could actually build a bead but then when i finished it was pretty flat and wide with a crack right down the middle. so fed up I eliminated the A.S.S. and my Pulser unit from the equation, the unit was disabled though, and went straight foot pedal. Now i didn't get a stack of dimes per say more like a stack of mixed change but that was mostly due to hand positioning, and getting a rhythm. My lap and T joints were very similar to each other. Reverse keyholed. top corner of shoulder and bottom of the puddle moved far forward from the inside corner and would only be filled by using a lot of filler rod and the puddles were very wide.