hey guys, wonder if you had some tips for tacking aluminum... I've been playing around welding aluminum sheet and though not great at it, my welds are getting a lot better. Welding up a radiator expansion tank today with .080 6061 welding a 4-sided tank (corner welds, well, more like corner-T welds?), that's basically 10"x3"x3" and it's coming out decent, but the ugliest spots are because of the 20 horrendous tack welds that I struggled with that ended up leaving big uglies where I couldn't quite blend them in once I welded through them... Here's the details of my setup...
Miller Diversion 180 set at 115-125 amps using a foot pedal
#10 cup with large gas lens, #17 torch
3/32" with 2% lanthanated
1/16" Er4043 filler
100% argon at around 12cfm
cleaned with 120 flap disk and acetone
I can't seem to get a quick tack, it's so freakin' easy on steel, but I'm having little luck on aluminum. My biggest issue isn't so much getting the parent metals to puddle but to get them to puddle together (and doing it quickly without sitting forever)... I'll get one of the pieces to melt, then try to get the other to melt, but they only end up melting into each other 1 in 5 times, if that... Either I'm not pedaling in enough amps and I can't get a merged puddle, or I use too much amps and end up starting to blow material away. I've tried to not use filler figuring that would be the easiest way to put down a little tack, but have not had much luck with that either. As far as my general welding bead, it's not the most perfect though it's fairly uniform (for a self-taught amateur only recently playing with aluminum), if anything it's a little too cold and not enough penetration at times (I was fighting using too much heat before and have calmed that down but have gotten a little too cold now but getting better).... I'm theorizing my problem may be that because it's just tacking a cold piece, a short tack just doesn't put enough heat in it to quickly blow the oxide layer away quickly, and that's what I'm struggling with (maybe I should put some heat into the whole piece first???).... Any tips or ideas about what I might be doing wrong? It's driving me to drink, luckily I have plenty of beers or I'd be in deep trouble... lol... thanks
Tig welding tips, questions, equipment, applications, instructions, techniques, tig welding machines, troubleshooting tig welding process
- weldin mike 27
-
Weldmonger
-
Posts:
-
Joined:Fri Apr 01, 2011 10:59 pm
-
Location:Australia; Victoria
Jody has videos on speed tacking. It's all about super good fit up and a quick blast of amps way higher than your actual welding current
I've tried cranking the amps up and have good fit up, but still am struggling.weldin mike 27 wrote:Jody has videos on speed tacking. It's all about super good fit up and a quick blast of amps way higher than your actual welding current
can't believe it took me this many years to buy a diamond wheel for my bench grinder... what a difference
- weldin mike 27
-
Weldmonger
-
Posts:
-
Joined:Fri Apr 01, 2011 10:59 pm
-
Location:Australia; Victoria
thanks!weldin mike 27 wrote:I'll find the video for you. Maybe there is a little step you are missing
can't believe it took me this many years to buy a diamond wheel for my bench grinder... what a difference
- weldin mike 27
-
Weldmonger
-
Posts:
-
Joined:Fri Apr 01, 2011 10:59 pm
-
Location:Australia; Victoria
Tip #1: Grind tungsten to a sharp taper, 3x diameter, with just the tiniest flat just to get rid of the needle point.
Tip#2: Parts must be touching together, it has to be that good of a fit-up
Tip#3: 1-2mm arc length at most fro the highest point of the joint, square at the joint
Tip#4: blast it very quick, less than 0.5s, preferably around 1/3 sec, with MORE than 2x amps per thousandths. For 0.080", I'd suggest no less than 170A.
Here is 16ga (0.063") 6061-T6, no filler, outside corner joint, 80% EN balance, 60Hz, basic SS wire brush, acetone wipe. If your pre-set balance is closer to 70% EN, the arc cone won't be as focused, you might need to add a few more amps above the 2x suggestion I mentioned previously. If the AC Freq is higher than 60Hz, it might balance out, so you do have to play around a bit. Basically I would max out the amperage if it were me with your machine.
I would estimate that I blast it around 1/4 - 1/3 of a second. As fast as the arc comes on, I let up off the pedal.
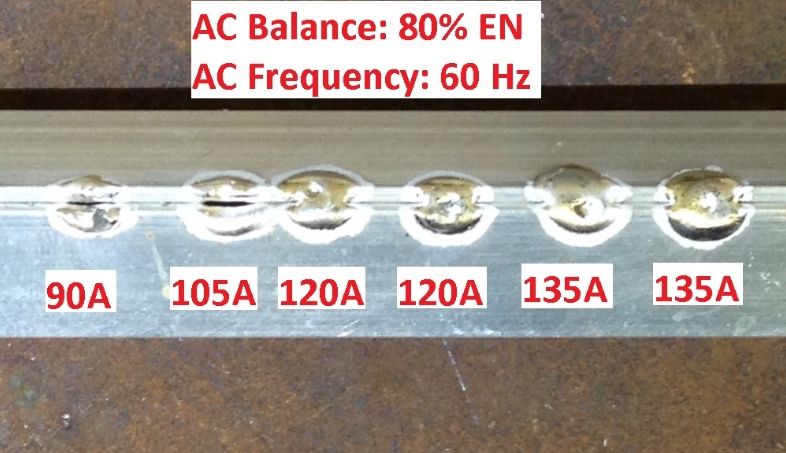
Almost forgot, make sure your pre-flow is already happening if you try this. If there is no argon present and you hit the pedal and douse the metal with that much amperage, it will surely contaminate it and the tungsten. If if not flowing right away, you can bump the pedal very slightly, in order to get the post-gas flowing. This will act as pre-flow right before you actually stomp on the pedal to blast the current.
Not the only way to do it, just how I do it. Good Luck.
Tip#2: Parts must be touching together, it has to be that good of a fit-up
Tip#3: 1-2mm arc length at most fro the highest point of the joint, square at the joint
Tip#4: blast it very quick, less than 0.5s, preferably around 1/3 sec, with MORE than 2x amps per thousandths. For 0.080", I'd suggest no less than 170A.
Here is 16ga (0.063") 6061-T6, no filler, outside corner joint, 80% EN balance, 60Hz, basic SS wire brush, acetone wipe. If your pre-set balance is closer to 70% EN, the arc cone won't be as focused, you might need to add a few more amps above the 2x suggestion I mentioned previously. If the AC Freq is higher than 60Hz, it might balance out, so you do have to play around a bit. Basically I would max out the amperage if it were me with your machine.
I would estimate that I blast it around 1/4 - 1/3 of a second. As fast as the arc comes on, I let up off the pedal.
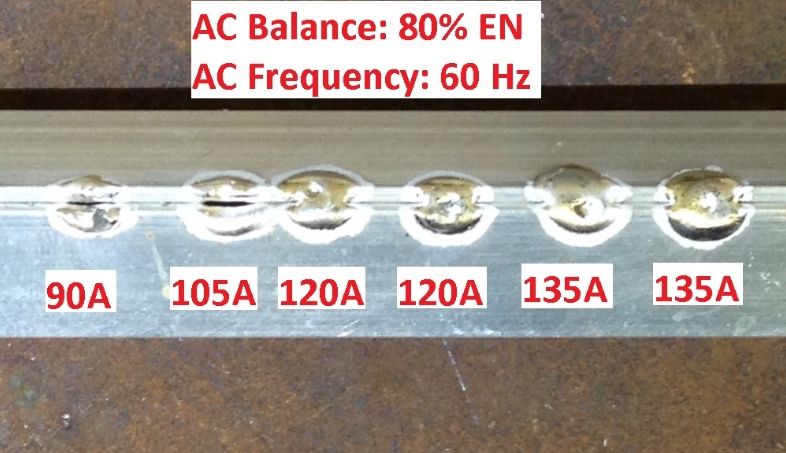
Almost forgot, make sure your pre-flow is already happening if you try this. If there is no argon present and you hit the pedal and douse the metal with that much amperage, it will surely contaminate it and the tungsten. If if not flowing right away, you can bump the pedal very slightly, in order to get the post-gas flowing. This will act as pre-flow right before you actually stomp on the pedal to blast the current.
Not the only way to do it, just how I do it. Good Luck.
Last edited by Oscar on Mon Jun 15, 2015 12:10 am, edited 2 times in total.
- TRACKRANGER
-
Weldmonger
-
Posts:
-
Joined:Wed Aug 06, 2014 12:48 am
-
Location:Melbourne, Australia
I think these are some of the videos the Weldin Mike mentioned
Gvk8rH05ADU
ny-glWjl9pk
Hope this helps
Trev
Gvk8rH05ADU
ny-glWjl9pk
Hope this helps
Trev
EWM Phonenix 355 Pulse MIG set mainly for Aluminum, CIGWeld 300Amp AC/DC TIG, TRANSMIG S3C 300 Amp MIG, etc, etc
- ldbtx
-
Heavy Hitter
-
Posts:
-
Joined:Thu Jun 13, 2013 12:54 am
-
Location:North Central Texas
-
Contact:
Another one with the fusion tacks is the 2-part playlist for the compressor belt guard.
LDB
LDB
Miller Bobcat 225
Tweco Fabricator 211i
AHP AlphaTIG 200x
Lincoln SP-135+
Hypertherm Powermax 30 Air
ProStar O/A torch
Tweco Fabricator 211i
AHP AlphaTIG 200x
Lincoln SP-135+
Hypertherm Powermax 30 Air
ProStar O/A torch
- weldin mike 27
-
Weldmonger
-
Posts:
-
Joined:Fri Apr 01, 2011 10:59 pm
-
Location:Australia; Victoria
- TRACKRANGER
-
Weldmonger
-
Posts:
-
Joined:Wed Aug 06, 2014 12:48 am
-
Location:Melbourne, Australia
Too easy. I pictured you frantically trying to find those videos during your lunch break instead of eating. Just a little team work!weldin mike 27 wrote:Thanks Trev. Saved me the trouble
EWM Phonenix 355 Pulse MIG set mainly for Aluminum, CIGWeld 300Amp AC/DC TIG, TRANSMIG S3C 300 Amp MIG, etc, etc
- weldin mike 27
-
Weldmonger
-
Posts:
-
Joined:Fri Apr 01, 2011 10:59 pm
-
Location:Australia; Victoria
thanks guys!... and to add to those videos, Jody just posted a new video on tack welding aluminum, which coincidentally enough is also welding a rad recovery tank just like I'm doing...
my machine has no balance or frequency controls, just amperage and the ability to switch between steel and aluminum... I tried pumping up my amperage to max 180 amps, got my preflow going, and as quick a blast as possible, and I still was not able to consistently create a nice fused tack. I'd get it every once in awhile, but not every time. I also tried dropping my amps down to around 1-1/2 my sheet thickness as Jody talked about in his latest vid, at 120amps on my .080, but didn't have that much better luck, it actually worked better with the full on 'Volume to 11' setting (heh)...
like I think i mentioned before, it's very easy for me to tack steel, just doing it on aluminum is what I'm struggling with. I'm wondering if maybe having a questionable ground may be part of my problem. Though I recently built myself my first welding table, it's actually not completed as I haven't had the money yet to buy the 3/8" 29"x48" top, so it's just sitting there next to my actual welding table, which is only an old big folding cafeteria particle board top table that I have a .065" sheet of steel clamped down on top of it and my ground going to the clamp... Not exactly a great setup but has been working fine but maybe it's not as good as I've been thinking, maybe when I'm setting for x-amount of amps it's not really pumping it all through. I'm low on gas but I'm gonna try clamping my ground directly to some scrap and try tacking that way tomorrow and see if I get any different results.
my machine has no balance or frequency controls, just amperage and the ability to switch between steel and aluminum... I tried pumping up my amperage to max 180 amps, got my preflow going, and as quick a blast as possible, and I still was not able to consistently create a nice fused tack. I'd get it every once in awhile, but not every time. I also tried dropping my amps down to around 1-1/2 my sheet thickness as Jody talked about in his latest vid, at 120amps on my .080, but didn't have that much better luck, it actually worked better with the full on 'Volume to 11' setting (heh)...
like I think i mentioned before, it's very easy for me to tack steel, just doing it on aluminum is what I'm struggling with. I'm wondering if maybe having a questionable ground may be part of my problem. Though I recently built myself my first welding table, it's actually not completed as I haven't had the money yet to buy the 3/8" 29"x48" top, so it's just sitting there next to my actual welding table, which is only an old big folding cafeteria particle board top table that I have a .065" sheet of steel clamped down on top of it and my ground going to the clamp... Not exactly a great setup but has been working fine but maybe it's not as good as I've been thinking, maybe when I'm setting for x-amount of amps it's not really pumping it all through. I'm low on gas but I'm gonna try clamping my ground directly to some scrap and try tacking that way tomorrow and see if I get any different results.
can't believe it took me this many years to buy a diamond wheel for my bench grinder... what a difference
- Otto Nobedder
-
Weldmonger
-
Posts:
-
Joined:Thu Jan 06, 2011 11:40 pm
-
Location:Near New Orleans
One issue I rarely hear mentioned in a discussion of tacking aluminum, particularly thin stuff, is gas flow. I like a high gas flow when welding, but this can interfere with tacking. Molten aluminum runs like water, and excess gas can push the molten edges apart. I notice you mentioned pre-flow, so make sure that runs long enough to eliminate the pressure surge. (I don't have pre-flow at work, so I run a minimum arc for a few seconds to let the surge go, as well as locate my electrode and rod where I want them before mashing the pedal.)
It may be worth experimenting with your gas flow while tacking.
Steve S
It may be worth experimenting with your gas flow while tacking.
Steve S
- Braehill
-
Weldmonger
-
Posts:
-
Joined:Sat Jul 06, 2013 11:16 am
-
Location:Near Pittsburgh,Pennsylvania. Steel Buckle of the Rust Belt
I think the key to tacking thin sheet metal is that small overlap that Jody used in the latest video. The edge melts off and becomes the filler that's needed. That has worked for me in the past and I just used this same method last night on some 1/8" flat strap.
Len
Len
Now go melt something.
Instagram @lenny_gforce
Len
Instagram @lenny_gforce
Len
yeah I think I'm ok with my pre-flow as I'm always a little slow starting an arc... thanks
as far as overlap, yeah I'll give that a try... I guess with overlap you have to aim your torch accordingly to take advantage of that.. probably a lot of my issues is torch position, one thing I've noticed with TIG is everything has to be perfect it seems, especially torch angle... and I have a hard time keeping my hands from shaking when running a bead, but with tacking it's not an issue, just a point and shoot deal...
as far as overlap, yeah I'll give that a try... I guess with overlap you have to aim your torch accordingly to take advantage of that.. probably a lot of my issues is torch position, one thing I've noticed with TIG is everything has to be perfect it seems, especially torch angle... and I have a hard time keeping my hands from shaking when running a bead, but with tacking it's not an issue, just a point and shoot deal...
can't believe it took me this many years to buy a diamond wheel for my bench grinder... what a difference
Return to “Tig Welding - Tig Welding Aluminum - Tig Welding Techniques - Aluminum Tig Welding”
Jump to
- Introductions & How to Use the Forum
- ↳ Welcome!
- ↳ Member Introductions
- ↳ How to Use the Forum
- ↳ Moderator Applications
- Welding Discussion
- ↳ Metal Cutting
- ↳ Tig Welding - Tig Welding Aluminum - Tig Welding Techniques - Aluminum Tig Welding
- ↳ Mig and Flux Core - gas metal arc welding & flux cored arc welding
- ↳ Stick Welding/Arc Welding - Shielded Metal Arc Welding
- ↳ Welding Forum General Shop Talk
- ↳ Welding Certification - Stick/Arc Welding, Tig Welding, Mig Welding Certification tests - Welding Tests of all kinds
- ↳ Welding Projects - Welding project Ideas - Welding project plans
- ↳ Product Reviews
- ↳ Fuel Gas Heating
- Welding Tips & Tricks
- ↳ Video Discussion
- ↳ Wish List
- Announcements & Feedback
- ↳ Forum News
- ↳ Suggestions, Feedback and Support
- Welding Marketplace
- ↳ Welding Jobs - Industrial Welding Jobs - Pipe Welding Jobs - Tig Welding Jobs
- ↳ Classifieds - Buy, Sell, Trade Used Welding Equipment
- Welding Resources
- ↳ Tradeshows, Seminars and Events
- ↳ The Welding Library
- ↳ Education Opportunities