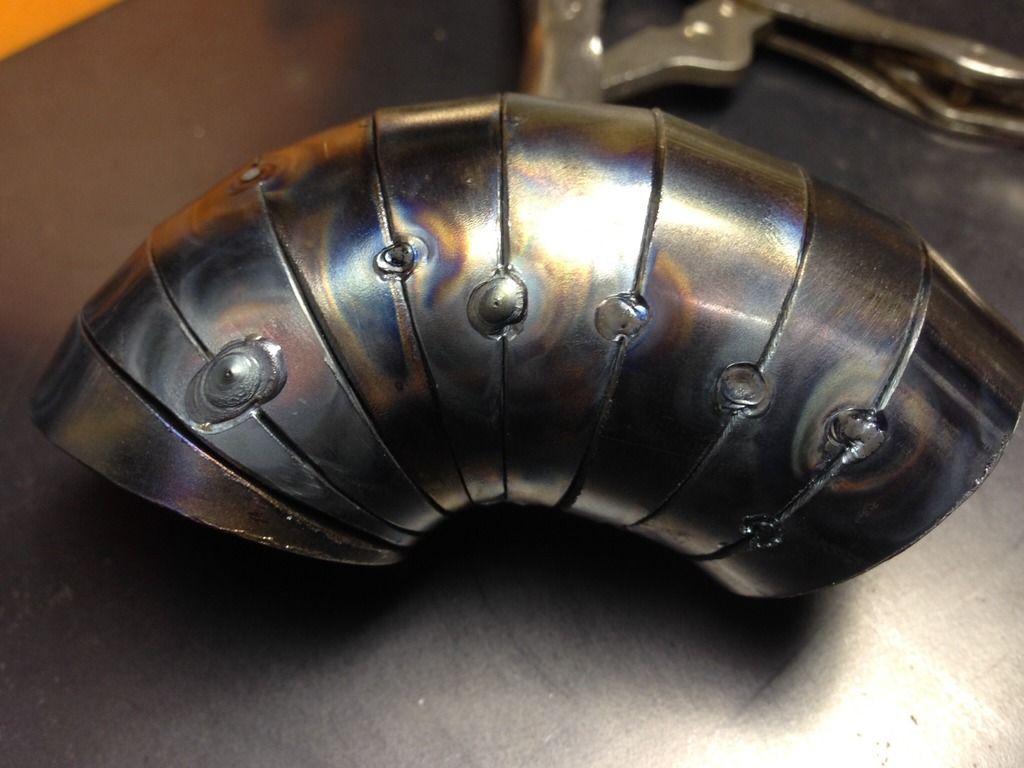
Hey all, resident noob here.
Experimenting with lobster backing for the first time. Mild steel, 41mm OD and 1.6mm wall thickness (that's one sixteenth from memory...)
All steel cleaned and cleaned again, then wiped over with acetone. I'm using a 2% Lanthanated electrode sharpened to a point, 15cfm or so argon with a gas lens. 35 amps.
Okay, fit up isn't great. But why are my tacks so rubbish? Some of them seem bubbly almost like unpurged stainless.
I caught myself once or twice just shutting down the pedal (afraid of burn through) rather than backing off gradually, and I made a note of it and started backing off more gradually.
Is there something specifically wrong here, or do I simply need more practise at tacking steel?
And finally, I have some 1.6mm ER70S6 filler rod. Is this rod too thick or about right? Feels to me like I need a lot of heat to melt 1.6, and I might be better off with 1mm rod.
Any tips? Happy for any and all feedback.
Cheers,
Kym