Page 1 of 1
i have a problem with my welder
Posted: Sun Feb 07, 2016 11:06 am
by CanMoulder
Hello all
I'm a mold maker
the company i work for has a couple of plants
at the main plant we have a miller Dynasty® 350 (awesome love this thing)
now to my problem
at one of the plants we have an old Hobart tigmatic
i have it set to 0 amps and i am still welding
i have to use this to weld up an edge and it is just blowing it away
I am so used to the 350 at the other plant i am not sure if the hobart is NFG or just not capable of what i am trying to do
any help would be great
this is not my machine but one like it
mine is uglier and more smashed up
Kevin
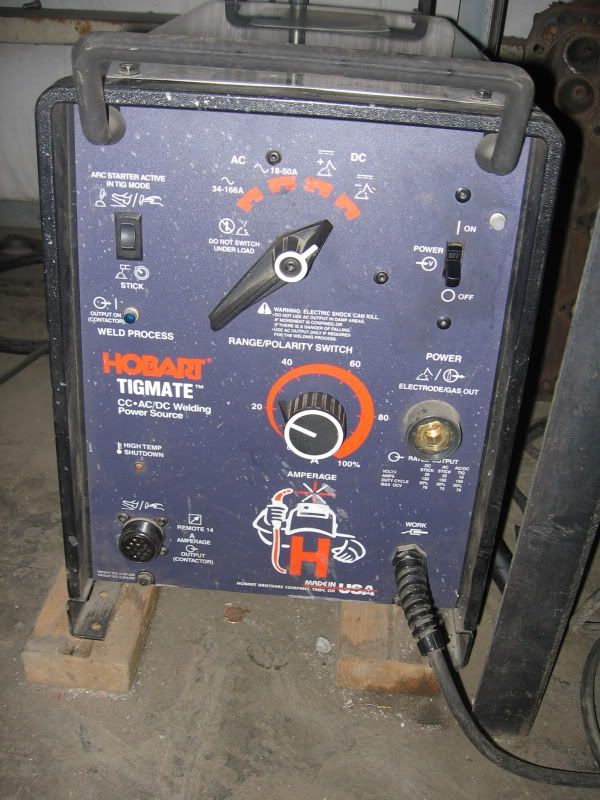
Re: i have a problem with my welder
Posted: Sun Feb 07, 2016 11:26 am
by LtBadd
CanMoulder wrote:Hello all
I'm a mold maker
the company i work for has a couple of plants
at the main plant we have a miller Dynasty® 350 (awesome love this thing)
now to my problem
at one of the plants we have an old Hobart tigmatic
i have it set to 0 amps and i am still welding
i have to use this to weld up an edge and it is just blowing it away
I am so used to the 350 at the other plant i am not sure if the hobart is NFG or just not capable of what i am trying to do
any help would be great
this is not my machine but one like it
mine is uglier and more smashed up
Hello CanMoulder
Sounds like you're trying to repair a mold and need low amperage to buildup an edge, I would guess that you're running up against the minimum amps that the Hobart unit can output. And as you have found out this unit isn't made for precision work.
Is this machine equipped with a foot pedal? After the initial startup surge, can you then weld at a lower amperage?
Re: i have a problem with my welder
Posted: Sun Feb 07, 2016 12:12 pm
by CanMoulder
yes it has a foot pedal
i am on and off it for every dip
i wish i could Show you what i am working on but i like my Job
Block is made out of P20 and i am using a P20 modified Rod as that material is nicer to work after welding
the Hobart is Old i have been here 10 years and it was here 10 years before i got here
i am in Maintenance but Why would you ever need to do Maintenance to a welder (

)
i am basically trying to weld on the side of a wall that is .110" thick and 3/4 of an inch tall
Kevin
Re: i have a problem with my welder
Posted: Mon Feb 08, 2016 1:45 pm
by DSM8
I have experience similar issues with my Miller DialArc, it is incapable of starting at low enough amperage.
See if you can start the arc on a block of Copper or such then move it over to the piece in question. That is the only way I am able to weld thin material with this machine since it's start amps are too high.
Re: i have a problem with my welder
Posted: Mon Feb 08, 2016 7:54 pm
by LtBadd
DSM8 wrote:I have experience similar issues with my Miller DialArc, it is incapable of starting at low enough amperage.
See if you can start the arc on a block of Copper or such then move it over to the piece in question. That is the only way I am able to weld thin material with this machine since it's start amps are too high.
I used to do some mold repair work at a customers shop, unfortunately this was the machine they had, what a challenge!
Re: i have a problem with my welder
Posted: Sat Feb 13, 2016 8:23 am
by CanMoulder
i was hard to do and dose not look as nice as i would have liked
i never thought about using copper to take the High frequency initial hit i will remember that tip
But because a squeaky wheel gets some grease
my lead hand and i talk nice to my Manager
they are looking into buying us a new miller dynasty 280 dx
i am in shock but so happy
Sorry but Blue is my favorite color
Kevin