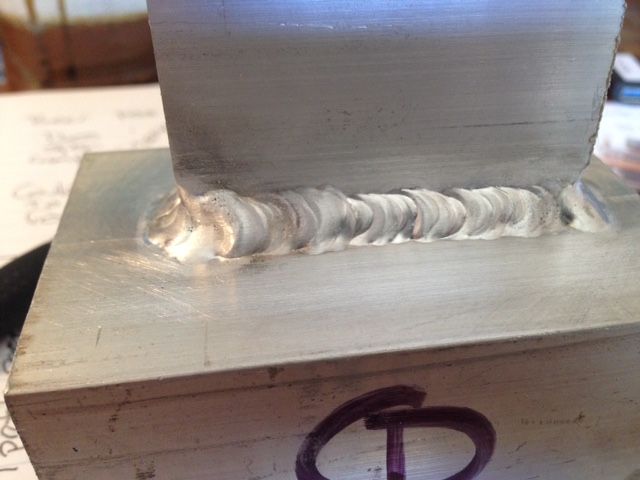
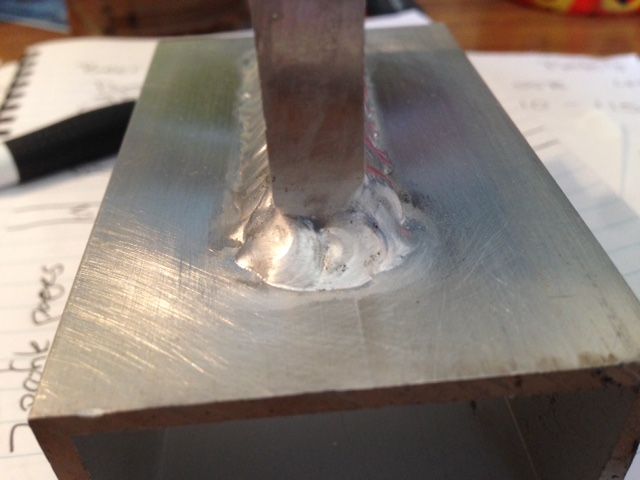
Firstly, please excuse my crappy photos and crappier welding. I like to think this forum needs some comedy relief now and then...
I am welding 5000 series aluminium, thick to thin - in this case 10mm plate to 3mm box section.
I'm using 120 amps @ 120Hz, square wave, 30% cleaning. 2.4mm 2% lanth electrode, #6 gas lens. 7 secs post flow, 2.4mm 5356 filler.
Puddle gets going fairly fast, the piece heats up quickly and so I back off the pedal. Obviously what I need most here is simply practise, but tell me:
1) Would I be better off using thicker filler such as 3.2mm?
2) How about amps? Hotter?
My own thinking is that slightly thicker filler material might help cool and control the puddle a bit, but I am open to suggestions. Happy that the part is strong (have destruction tested with bloody big hammer) but as always after neatness, something I find difficult with short runs like this.
Cheers,
Kym