mig and flux core tips and techniques, equipment, filler metal
- AussieWelder
-
New Member
-
Posts:
-
Joined:Mon May 08, 2017 10:21 am
-
Location:Rockville MD
I'm running my first practice beads on 3/8" by 3" hot rolled steel bar. After running a few of these, and trying to get the Miller 140 autoset welder dialed in (amperage and wire feed speed), I have sliced across the work so far. I was chagrined to find no evidence of penetration.
I am using 75/25 gas mix, .030 wire. I cleaned up the surface prior to each bead.
Am I reading this situation correctly? Photos attached. I will continue to try different combinations of settings, but I had hoped to find at least some evidence of penetration here.
I know that the most basic problem here is that I am attempting welds on material that is outside the specs of this welder, but I was hoping that with good technique and settings, I would be able to compensate for at least some of the shortfalls of an underpowered system.
- Attachments
-
- IMG_4878.JPG (34.3 KiB) Viewed 4466 times
-
- IMG_4882.JPG (46.99 KiB) Viewed 4466 times
Grant
Enthusiastic 'Beginning Pro'
Rockville MD
Miller 140 Autoset welder (120 volt)
Enthusiastic 'Beginning Pro'
Rockville MD
Miller 140 Autoset welder (120 volt)
If the base metal is too thick, you'll never get the penetration needed. If your machine is limited on its capacity,you can preheat the base to aide in penetration. But your issue is more than just too little current, you have some technique errors as well.
Your travel speed is too fast.
Your arc length is probably too long as well.
Your metal doesn't cleaned up at all either. It needs to be bright shiny metal with MIG.
Your travel speed is too fast.
Your arc length is probably too long as well.
Your metal doesn't cleaned up at all either. It needs to be bright shiny metal with MIG.
- AussieWelder
-
New Member
-
Posts:
-
Joined:Mon May 08, 2017 10:21 am
-
Location:Rockville MD
Thanks CJ.
Is the arc length primarily decided by how far your nozzle tip is from the welding surface? Most of the time, I felt that I had it about as close as it could possibly be. I will try some subsequent runs of bead with slower travel speed.
I am still not getting a good look at the puddle as it is being formed. I think this might be a factor that is leading me to run the weld a bit 'blind'. I have my helmet set at 8 (lightest setting) and have also put in an optical 2 x piece.
I appreciate this.
Grant.
Is the arc length primarily decided by how far your nozzle tip is from the welding surface? Most of the time, I felt that I had it about as close as it could possibly be. I will try some subsequent runs of bead with slower travel speed.
I am still not getting a good look at the puddle as it is being formed. I think this might be a factor that is leading me to run the weld a bit 'blind'. I have my helmet set at 8 (lightest setting) and have also put in an optical 2 x piece.
I appreciate this.
Grant.
Grant
Enthusiastic 'Beginning Pro'
Rockville MD
Miller 140 Autoset welder (120 volt)
Enthusiastic 'Beginning Pro'
Rockville MD
Miller 140 Autoset welder (120 volt)
Farmwelding
- Farmwelding
-
Weldmonger
-
Posts:
-
Joined:Thu Mar 10, 2016 11:37 pm
-
Location:Wisconsin
Arc length is officially the distance from the end of the contact tip to the base metal. Generally for short circuit mig I use 3/8-1/2¨AussieWelder wrote:Thanks CJ.
Is the arc length primarily decided by how far your nozzle tip is from the welding surface? Most of the time, I felt that I had it about as close as it could possibly be. I will try some subsequent runs of bead with slower travel speed.
I am still not getting a good look at the puddle as it is being formed. I think this might be a factor that is leading me to run the weld a bit 'blind'. I have my helmet set at 8 (lightest setting) and have also put in an optical 2 x piece.
I appreciate this.
Grant.
A student now but really want to weld everyday. Want to learn everything about everything. Want to become a knower of all and master of none.
Instagram: @farmwelding
Nick
Instagram: @farmwelding
Nick
- MinnesotaDave
-
Weldmonger
-
Posts:
-
Joined:Sun Oct 27, 2013 10:57 pm
-
Location:Big Lake/Monticello MN, U.S.A.
Respectfully, I disagree.Farmwelding wrote: Arc length is officially the distance from the end of the contact tip to the base metal. Generally for short circuit mig I use 3/8-1/2¨
That's CTWD: contact tip to work distance, people also call it stick out.
Arc length is something different, for example with stick welding or spray transfer - then you have an arc length.
From Miller:
"Wire Stick-out
Stick-out is the length of unmelted electrode extending from the tip of the contact tube, and it does not include arc length. Generally, maintain a stick-out of 3/8 in. and listen for that "sizzling bacon" sound. If the arc sounds irregular, one culprit could be that your stick-out is too long, which is an extremely common error."
Lincoln, more in depth: http://www.lincolnelectric.com/en-us/su ... -ctwd.aspx
Last edited by MinnesotaDave on Mon May 15, 2017 3:54 pm, edited 1 time in total.
Dave J.
Beware of false knowledge; it is more dangerous than ignorance. ~George Bernard Shaw~
Syncro 350
Invertec v250-s
Thermal Arc 161 and 300
MM210
Dialarc
Tried being normal once, didn't take....I think it was a Tuesday.
Beware of false knowledge; it is more dangerous than ignorance. ~George Bernard Shaw~
Syncro 350
Invertec v250-s
Thermal Arc 161 and 300
MM210
Dialarc
Tried being normal once, didn't take....I think it was a Tuesday.
Also, how is your gun angle? It shouldn't be more than a few degrees off of 90, but a lot of new to mig guys will end up tilting the gun way over to kind of see what is going on. That just stacks the metal upon itself with virtually no penetration/fusion. This also messes up the contact tip to work distance.
Farmwelding
- Farmwelding
-
Weldmonger
-
Posts:
-
Joined:Thu Mar 10, 2016 11:37 pm
-
Location:Wisconsin
My apologies. Every one else said arc length so I accidentally put that instead of ctwd. Thanks for pointing it out.MinnesotaDave wrote:Respectfully, I disagree.Farmwelding wrote: Arc length is officially the distance from the end of the contact tip to the base metal. Generally for short circuit mig I use 3/8-1/2¨
That's CTWD: contact tip to work distance, people also call it stick out.
Arc length is something different, for example with stick welding or spray transfer - then you have an arc length.
From Miller:
"Wire Stick-out
Stick-out is the length of unmelted electrode extending from the tip of the contact tube, and it does not include arc length. Generally, maintain a stick-out of 3/8 in. and listen for that "sizzling bacon" sound. If the arc sounds irregular, one culprit could be that your stick-out is too long, which is an extremely common error."
Lincoln, more in depth: http://www.lincolnelectric.com/en-us/su ... -ctwd.aspx
A student now but really want to weld everyday. Want to learn everything about everything. Want to become a knower of all and master of none.
Instagram: @farmwelding
Nick
Instagram: @farmwelding
Nick
- Otto Nobedder
-
Weldmonger
-
Posts:
-
Joined:Thu Jan 06, 2011 11:40 pm
-
Location:Near New Orleans
You say you're cleaning the material each pass. I see no evidence the material is anywhere near clean. Define "cleaning" as you are using it.AussieWelder wrote:IMG_4881.JPGHello everyone,
I'm running my first practice beads on 3/8" by 3" hot rolled steel bar. After running a few of these, and trying to get the Miller 140 autoset welder dialed in (amperage and wire feed speed), I have sliced across the work so far. I was chagrined to find no evidence of penetration.
I am using 75/25 gas mix, .030 wire. I cleaned up the surface prior to each bead.
Am I reading this situation correctly? Photos attached. I will continue to try different combinations of settings, but I had hoped to find at least some evidence of penetration here.
I know that the most basic problem here is that I am attempting welds on material that is outside the specs of this welder, but I was hoping that with good technique and settings, I would be able to compensate for at least some of the shortfalls of an underpowered system.
That metal should be bright and shiny before you call it clean. Every bit of that (green?) crap should be gone. It seems to appear in the line of "no penetration" in your cut section. Use a grinder with a hard stone, and make some sparks until the metal is silver in color. Until that is done, there's no use working on settings.
Steve
I'm no expert but I was also wondering about gas flow. I've a bit of experience with FCAW since 1998 but I'm new to GMAW.
The big adjustment was with being able to see around the mig nozzle, the flux core nozzle is so much easier to see around.
I played with my welders a bit and just settled on the flow gauges set at 20, and maintaining about 1/2" stick out and my beads look acceptable to my uneducated eye, with too much stick out and the flow meters set too low they looked more like your pics.
I also would get some 1/8" material to practice on.
The big adjustment was with being able to see around the mig nozzle, the flux core nozzle is so much easier to see around.
I played with my welders a bit and just settled on the flow gauges set at 20, and maintaining about 1/2" stick out and my beads look acceptable to my uneducated eye, with too much stick out and the flow meters set too low they looked more like your pics.
I also would get some 1/8" material to practice on.
- Otto Nobedder
-
Weldmonger
-
Posts:
-
Joined:Thu Jan 06, 2011 11:40 pm
-
Location:Near New Orleans
Who actually studied the pictures?
Really, I want to know.
Speculating about machine settings and gas flow id all fine and good, once he's welding on CLEAN, SHINY metal, not that green crusty crap in the pictures he shared. I'm serious, study the picture where he cut the "weld", and you'll see that crust continues uninterrupted under the beads he set on top of it.
Really, I want to know.
Speculating about machine settings and gas flow id all fine and good, once he's welding on CLEAN, SHINY metal, not that green crusty crap in the pictures he shared. I'm serious, study the picture where he cut the "weld", and you'll see that crust continues uninterrupted under the beads he set on top of it.
It was mentioned in the first replies (metal prep). I have welded HR steel without full clean prep and gotten decent penetration, so metal prep alone is not the only issue here.Otto Nobedder wrote:Who actually studied the pictures?
Really, I want to know.
Speculating about machine settings and gas flow id all fine and good, once he's welding on CLEAN, SHINY metal, not that green crusty crap in the pictures he shared. I'm serious, study the picture where he cut the "weld", and you'll see that crust continues uninterrupted under the beads he set on top of it.
His welds look really cold despite the (lack of) prep. These attributes are being observed/commented on. But once his beads get/look better, an analysis of penetration will also reveal inclusion of the mill scale that needs to be removed. Walk before you run...
I did. That's why I figured the gun was laid way down. Its incontrovertible that the prep is bad, but then there's also the caterpillar like bead. Easy enough to assume settings due to the lapping, but if you draw a line perpendicular to the eye (or where the weld was stopped/restarted) it appears to be way off from any typical position. Even if the settings were in the "close enough" range, this will result in no penetration/malformed beads.Otto Nobedder wrote:Who actually studied the pictures?
Really, I want to know.
Speculating about machine settings and gas flow id all fine and good, once he's welding on CLEAN, SHINY metal, not that green crusty crap in the pictures he shared. I'm serious, study the picture where he cut the "weld", and you'll see that crust continues uninterrupted under the beads he set on top of it.
- Otto Nobedder
-
Weldmonger
-
Posts:
-
Joined:Thu Jan 06, 2011 11:40 pm
-
Location:Near New Orleans
...but if you start with clean, uncontaminated metal, all the other s#!t you're talking about can be gauged and adjusted. You have no idea what that green crust is, or what effect it's having on this weld. I've never seen mill scale look like that.
"Walk before you run" was stated.
Lace up your shoes, first.
Show me what your settings do on clean metal, and I might be able to tell you something. The unknown crap on the steel is a variable I can't (and these other bright people shouldn't try to) account for in any suggestion I or we might give you.
Steve
"Walk before you run" was stated.
Lace up your shoes, first.
Show me what your settings do on clean metal, and I might be able to tell you something. The unknown crap on the steel is a variable I can't (and these other bright people shouldn't try to) account for in any suggestion I or we might give you.
Steve
- Otto Nobedder
-
Weldmonger
-
Posts:
-
Joined:Thu Jan 06, 2011 11:40 pm
-
Location:Near New Orleans
Quite true, but with .030 wire, it's doable (preheat is advisable). There should be some measurable penetration in this attempt, even if it's only near the toes and doesn't close the root.AKmud wrote:3/8" is pretty thick for that small of machine. Once you get it clean and shiny, hit it with a torch to pre-heat. Your machine is struggling.
Before I make any attempt at advice, I want to see an attempt on metal that has been ground until there's no chance of whatever that green crap is to exist in the tiniest pinhole.
This is a case where I wish Grant were my neighbor, so I could go observe and maybe get my hands dirty to get a solution for him.
Steve
Take a deep breath. Let the smoke out slow.
#1. Forget using a 110 welder on 3/8 steel. Period.
#2. Forget using a 110 welder on 3/8 steel. Period.
#3. Go get some 1/8 steel.Leave your machine maxed out. Go weld some 1/8 steel.
Penetrated purty good didnit ?
Ever took a look inside the door on that machine Aussie ? See anything about 3/8 steel ?
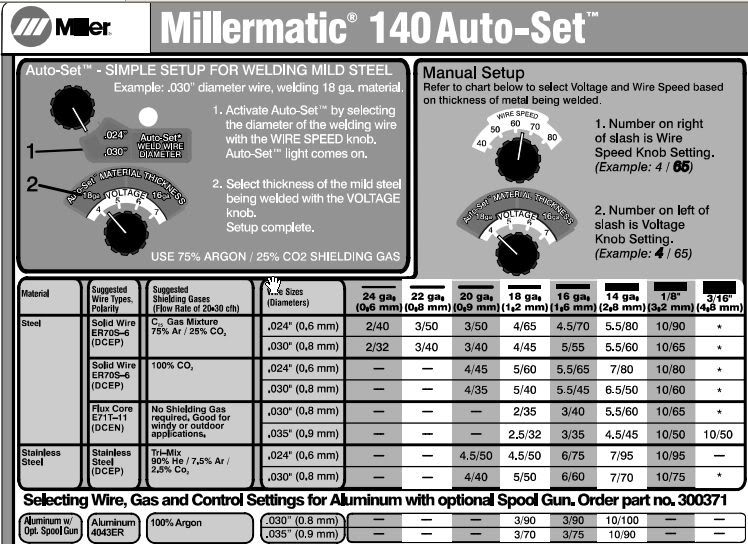
#1. Forget using a 110 welder on 3/8 steel. Period.
#2. Forget using a 110 welder on 3/8 steel. Period.
#3. Go get some 1/8 steel.Leave your machine maxed out. Go weld some 1/8 steel.
Penetrated purty good didnit ?
Ever took a look inside the door on that machine Aussie ? See anything about 3/8 steel ?
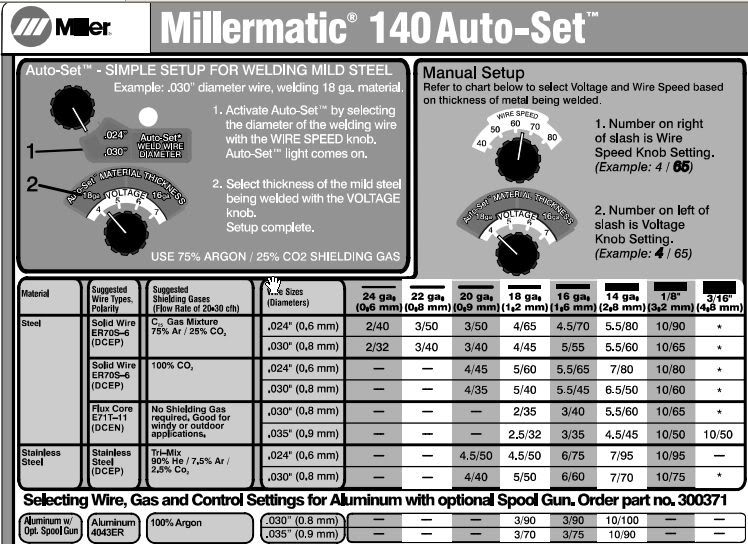
[quote="Antorcha"]Take a deep breath. Let the smoke out slow.
#1. Forget using a 110 welder on 3/8 steel. Period.
#2. Forget using a 110 welder on 3/8 steel. Period.
#3. Go get some 1/8 steel.Leave your machine maxed out. Go weld some 1/8 steel.
Penetrated purty good didnit ?
Ever took a look inside the door on that machine Aussie ? See anything about 3/8 steel ?
But,,,,even though he won't be able to make a 3/8 bead capable of welding 3/8 in a single pass. He should be just fine welding a bead big enough for 1/8 steel on a 3/8 plate. It won't just stop working because the plates too thick. If he's on good clean steel and gets the machine dialed in then the resulting weld will have good wet in on the edges. Regardless of how thick the base plate is!
#1. Forget using a 110 welder on 3/8 steel. Period.
#2. Forget using a 110 welder on 3/8 steel. Period.
#3. Go get some 1/8 steel.Leave your machine maxed out. Go weld some 1/8 steel.
Penetrated purty good didnit ?
Ever took a look inside the door on that machine Aussie ? See anything about 3/8 steel ?
But,,,,even though he won't be able to make a 3/8 bead capable of welding 3/8 in a single pass. He should be just fine welding a bead big enough for 1/8 steel on a 3/8 plate. It won't just stop working because the plates too thick. If he's on good clean steel and gets the machine dialed in then the resulting weld will have good wet in on the edges. Regardless of how thick the base plate is!
I have more questions than answers
Josh
Josh
Lcgixxer87
- Lcgixxer87
-
New Member
-
Posts:
-
Joined:Fri Jun 02, 2017 5:24 pm
I'm new to mig myself, just done it a few days breaking from my vertical stick. I can get good penetration and a good form up to for the most part on my laps but am having trouble with the lower end piling a little and not penetrating. I think this gun angle tip will be helpful. I do a good tilt in stick, perhaps I need to do a more straight on approach with the mig gunPeteM wrote:Also, how is your gun angle? It shouldn't be more than a few degrees off of 90, but a lot of new to mig guys will end up tilting the gun way over to kind of see what is going on. That just stacks the metal upon itself with virtually no penetration/fusion. This also messes up the contact tip to work distance.
Sent from my iPhone using Tapatalk
Lcgixxer87
- Lcgixxer87
-
New Member
-
Posts:
-
Joined:Fri Jun 02, 2017 5:24 pm
I'm new to mig myself, just done it a few days breaking from my vertical stick. I can get good penetration, pretty beads, and a good form up top for the most part on my laps but am having trouble with the lower end of the bead piling a little. I think this gun angle tip will be helpful. I do a good tilt in stick, perhaps I need to do a more straight on approach with the mig gun
Sent from my iPhone using Tapatalk
Sent from my iPhone using Tapatalk
Return to “Mig and Flux Core - gas metal arc welding & flux cored arc welding”
Jump to
- Introductions & How to Use the Forum
- ↳ Welcome!
- ↳ Member Introductions
- ↳ How to Use the Forum
- ↳ Moderator Applications
- Welding Discussion
- ↳ Metal Cutting
- ↳ Tig Welding - Tig Welding Aluminum - Tig Welding Techniques - Aluminum Tig Welding
- ↳ Mig and Flux Core - gas metal arc welding & flux cored arc welding
- ↳ Stick Welding/Arc Welding - Shielded Metal Arc Welding
- ↳ Welding Forum General Shop Talk
- ↳ Welding Certification - Stick/Arc Welding, Tig Welding, Mig Welding Certification tests - Welding Tests of all kinds
- ↳ Welding Projects - Welding project Ideas - Welding project plans
- ↳ Product Reviews
- ↳ Fuel Gas Heating
- Welding Tips & Tricks
- ↳ Video Discussion
- ↳ Wish List
- Announcements & Feedback
- ↳ Forum News
- ↳ Suggestions, Feedback and Support
- Welding Marketplace
- ↳ Welding Jobs - Industrial Welding Jobs - Pipe Welding Jobs - Tig Welding Jobs
- ↳ Classifieds - Buy, Sell, Trade Used Welding Equipment
- Welding Resources
- ↳ Tradeshows, Seminars and Events
- ↳ The Welding Library
- ↳ Education Opportunities