What welding projects are you working on? Are you proud of something you built?
How about posting some pics so other welders can get some ideas?
How about posting some pics so other welders can get some ideas?
That's great that it is working for you as well as it is. Draw benders always work better than press benders. I always wonder why the ones with top mount hydraulics don't offset the ram relative to the dies instead of putting them inline. That is a common problem I often have to overcome. I end up having to weld 2 90's together. The only upside to welding them together is you are not reliant on the radius of the die itself for smaller hoops.
Miller ABP 330, Syncrowave 250, Dynasty 300 DX.
Honorary member of the Fraternity of Faded Tee Shirts.
Honorary member of the Fraternity of Faded Tee Shirts.
TamJeff, I'm gonna call Pro-Tools tomorrow. It seems that this particular bender can bend different radius with the same die! When you lower the follower to the next position on the tower, it increases the radius. I'm not exactly sure how this works, but, I'll find out tomorrow. I worked in the shop a little today and worked out a little trouble with the fork pivot. I begin assembly on that unit tomorrow.
I can make the radius bigger than the dies by using multiple bend marks and partially bending each section and pro tools has a formula chart for this. From my experience, I can't make them smaller than the dies, at least not with a die that bends 90's or 180's. It seems as if it would have to be a half die for clearance purposes or something and used at multiple indexes.
On the picture of the bait well stand I built in the tubing miters thread, those were made larger by using multiple bend marks indexed apart a certain distance and partially bent until the radii met collectively and I still had to tweak it in the hip bender. Your type of bender will be better suited at this for you not having the hydraulic ram in the way.
On the picture of the bait well stand I built in the tubing miters thread, those were made larger by using multiple bend marks indexed apart a certain distance and partially bent until the radii met collectively and I still had to tweak it in the hip bender. Your type of bender will be better suited at this for you not having the hydraulic ram in the way.
Miller ABP 330, Syncrowave 250, Dynasty 300 DX.
Honorary member of the Fraternity of Faded Tee Shirts.
Honorary member of the Fraternity of Faded Tee Shirts.
Tamjeff, I called Pro-Tools today and spoke to James. He said go ahead and lower the follower to the next hole down on the tower. Be sure to go slow and use your angle guide. I will take pictures of this and let you know how things turn out.
Here's an update on the mini bike. I made the front fork pivot assembly. The tubes that are in there are just for alignment. Those aren't the ones that go there.
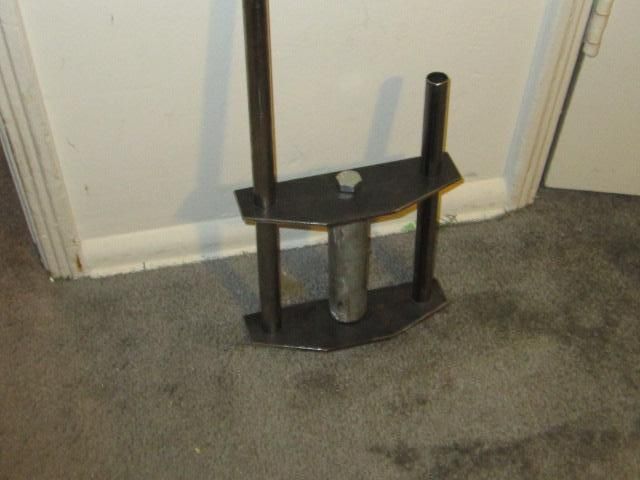
I'm going to make the steering stems myself. They're way to expensive to buy. 1" thick aluminum 2" long, drill 7/8" hole in the center, drill for 1/4 - 20 bolts on each end and voila! I'll post more photos tomorrow.
Here's an update on the mini bike. I made the front fork pivot assembly. The tubes that are in there are just for alignment. Those aren't the ones that go there.
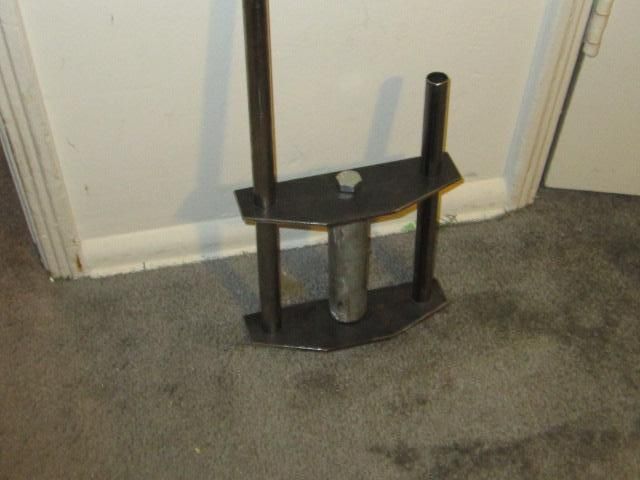
I'm going to make the steering stems myself. They're way to expensive to buy. 1" thick aluminum 2" long, drill 7/8" hole in the center, drill for 1/4 - 20 bolts on each end and voila! I'll post more photos tomorrow.
I think that steering looks ultimately appropriate. I personally like those little custom mods to projects. When I was looking at mini bikes online, that was what I noticed on some was the rather anemic steering setups. I saw some mini bikes with the Briggs (vanguard?) twins mounted on them. . .16hp and up! 70 mph mini bike would surely give someone that 'seat-of-the-pants' feel!
Miller ABP 330, Syncrowave 250, Dynasty 300 DX.
Honorary member of the Fraternity of Faded Tee Shirts.
Honorary member of the Fraternity of Faded Tee Shirts.
Great post, TamJeff! Today, a friend came buy for me to help him weld some repair on his jeep. He filled my tank and gave me 40 bucks for helping him. My first paid welding job! Anyway, I worked on the bike today, a little. I have to use a hole saw to drill the pocket that the pivot tube will sit in. I tipped the drill press platen 25 degrees and clamped the seat frame to the platen. It worked great! I used the old rusty frame as a test piece. The good frame, I'll use tomorrow. The angle seems different than the picture. I can adjust that with the test piece to get it right. I'll take some pictures tomorrow. I will probably weld the whole frame tomorrow. Laying out the lower part of the frame will be very hard. It's a very steep angle.
I'm finally started to put the mini bike together. The angles are almost perfect. The next bike will have the small stuff tweeked a little for better results. I'm going to start on the front end, today. Only bad news is that the notching is impossible without a good notcher. The hole saw is to course and flies everywhere. So, I bought a grinding wheel and shaped it 7/8". It worked great! You don't have to take off very much to get a good fit. When I notched the seat frame 1-1/2", there was no problem. It seems that the small tube are more difficult.
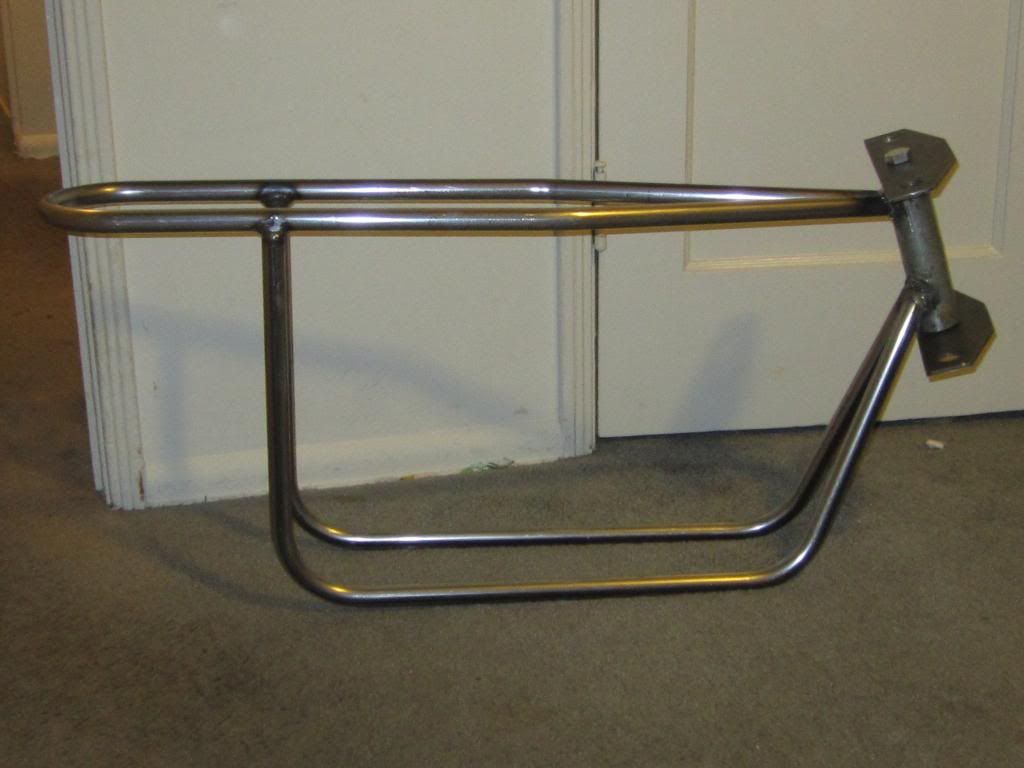
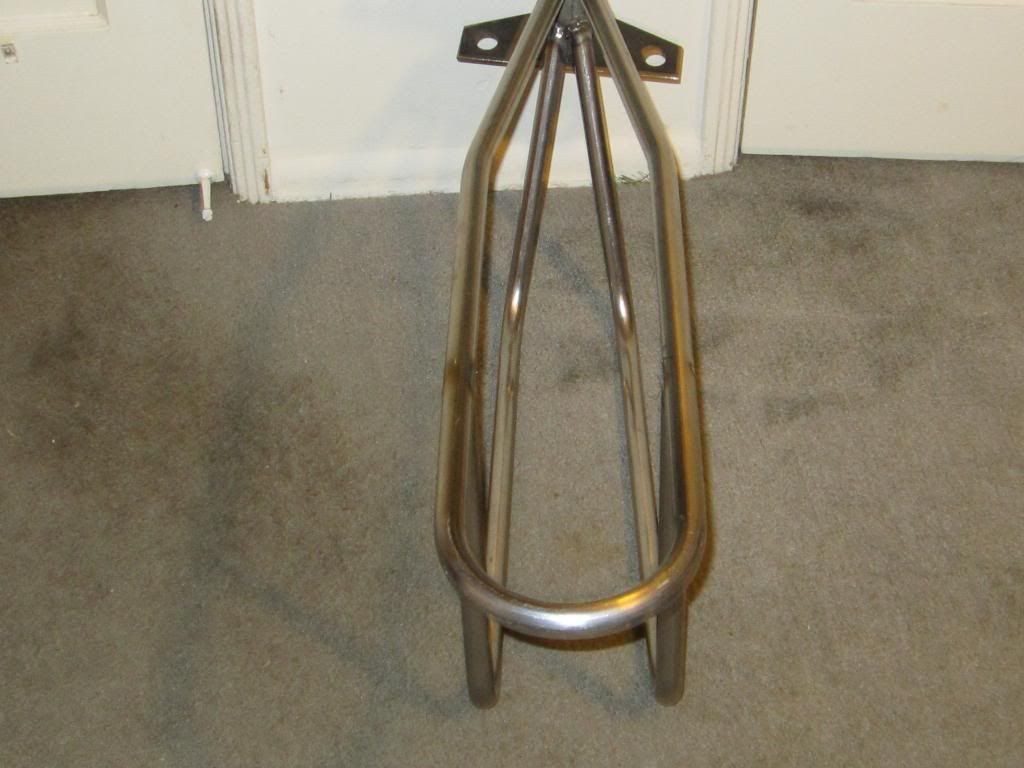
Here, you can see that the lower frames are not exactly parallel. I can add another 5 deg. to that.
I also have to notch out the bottom fork plate where it is hitting the lower frame.
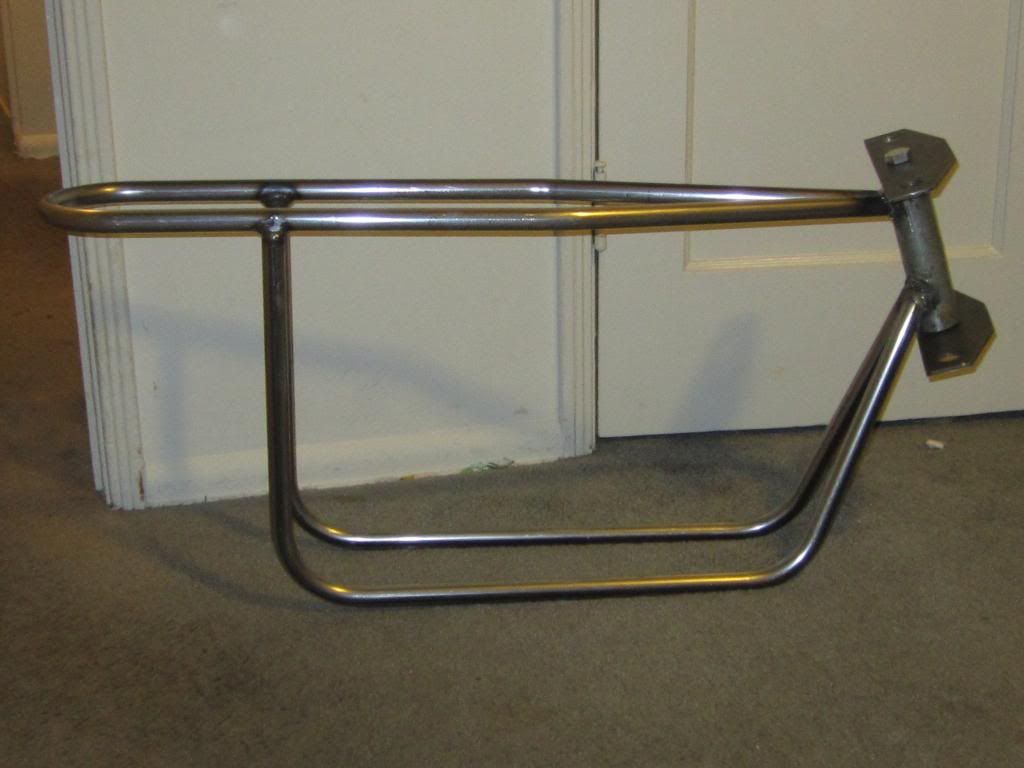
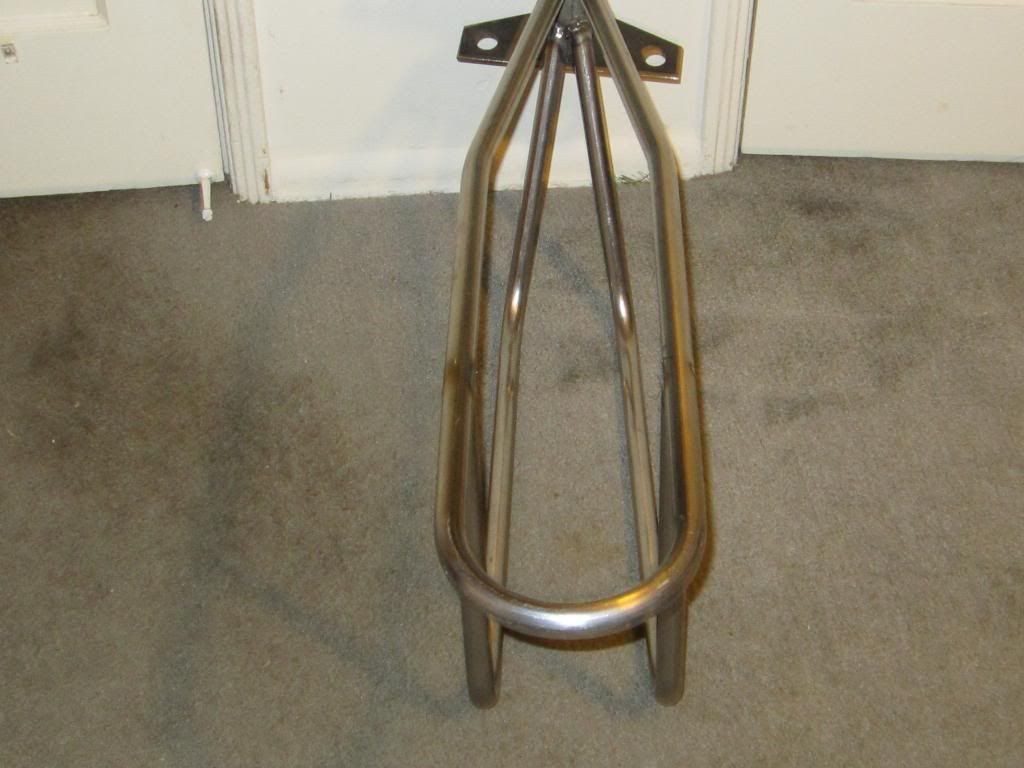
Here, you can see that the lower frames are not exactly parallel. I can add another 5 deg. to that.
I also have to notch out the bottom fork plate where it is hitting the lower frame.
Awesome. Remember that photos are deceiving as well with things that are plumb, square or parallel. When I was building my boat, I set the stem, plumbed it and measured it and referenced it as many different ways possible, snapped a photo for my album, and as I was organizing the photos later that evening, it showed something very wrong, or so I thought. There I was, at 2 am outside rechecking everything thinking disaster. It was the photo that was the culprit.
Miller ABP 330, Syncrowave 250, Dynasty 300 DX.
Honorary member of the Fraternity of Faded Tee Shirts.
Honorary member of the Fraternity of Faded Tee Shirts.
I always have that same fear. If and when I start making a lot of these, I have templates that I will use to make sure that everything is square and welded together correctly. When I built the Takas bender, I had that same fear. But, I followed the directions to the letter. As you can see, it worked great. Something I don't have to worry about. Building the templates is another issue. Those have to be right on.
The biggest issue is, how to sell these. My first choice would be to sell them completed. No issues of customers welding parts wrong. These mini bikes are not easy to put together. Go-Karts-USA sells the frame kits for $900! I don't want a father and son project to go sour. It's easy to blow a hole thru this .065 tube. Anyway, I'm headed out to the shop to start on the front fork unit.
The biggest issue is, how to sell these. My first choice would be to sell them completed. No issues of customers welding parts wrong. These mini bikes are not easy to put together. Go-Karts-USA sells the frame kits for $900! I don't want a father and son project to go sour. It's easy to blow a hole thru this .065 tube. Anyway, I'm headed out to the shop to start on the front fork unit.
- Otto Nobedder
-
Weldmonger
-
Posts:
-
Joined:Thu Jan 06, 2011 11:40 pm
-
Location:Near New Orleans
To sell the bent tubes for a "weld it" project, you'd better get your lawyer involved. (You do have a lawyer, don't you? You need protection any time you sell anything stupid people can hurt themselves with.) You need some boilerplate that puts the onus for weld quality firmly on the builder. It should be written in such a way as to discourage the unqualified, and might even need a signed "waiver of liability" for your records.
I'm no lawyer, but I'm a firm believer in CYA!
Steve S
I'm no lawyer, but I'm a firm believer in CYA!
Steve S
The first couple of them aren't usually easy. I am thinking the way you are progressing already and fixing your prototype approach as you go along, the subsequent builds are going to go much easier, especially after your tooling evolves with it.CraigLam wrote:I always have that same fear. If and when I start making a lot of these, I have templates that I will use to make sure that everything is square and welded together correctly. When I built the Takas bender, I had that same fear. But, I followed the directions to the letter. As you can see, it worked great. Something I don't have to worry about. Building the templates is another issue. Those have to be right on.
The biggest issue is, how to sell these. My first choice would be to sell them completed. No issues of customers welding parts wrong. These mini bikes are not easy to put together. Go-Karts-USA sells the frame kits for $900! I don't want a father and son project to go sour. It's easy to blow a hole thru this .065 tube. Anyway, I'm headed out to the shop to start on the front fork unit.
I often have to make jigs for one-off runs of projects, even adding in over sized dimensions to allow for weld distortion. Tweaking warpage out of a hundred parts where it could have been compensated for in the jig, often saves me a lot of sweat and time. Say there is a section that gets a cross tube welded in. I will make a slightly over sized spreader that fits in further down so that when it cools and I pull the jig or spreader out, it shrinks to it's designated size.
Miller ABP 330, Syncrowave 250, Dynasty 300 DX.
Honorary member of the Fraternity of Faded Tee Shirts.
Honorary member of the Fraternity of Faded Tee Shirts.
delraydella
- delraydella
-
Weldmonger
-
Posts:
-
Joined:Mon Apr 25, 2011 7:35 pm
-
Location:Detroit, MI
Those are looking great, but i don't think you would want to sell the frame parts unwelded. That would be asking for a lot of trouble as there is too much that can go wrong there. You can't assume that any/all of your customers will be skilled in welding tube or even have the proper equipment to do it.
I would think to start off, start with a few standard frame sizes, motors, tires, etc. If your customers want to customize them beyond that, then it's up to them.
Before you start selling anything, make sure you check on any type of liability insurance you might need, and for any type of warranty you might have to offer on workmanship. You might not need anything, but like Steve S. says..........C.Y.A.!
I would think to start off, start with a few standard frame sizes, motors, tires, etc. If your customers want to customize them beyond that, then it's up to them.
Before you start selling anything, make sure you check on any type of liability insurance you might need, and for any type of warranty you might have to offer on workmanship. You might not need anything, but like Steve S. says..........C.Y.A.!
Welding☞Syncrowave 250,Millermatic 252,30a Spoolgun Cutting☞12" Hi-speed Cutoff Saw, 9x 12 Horizontal Bandsaw Milling☞Gorton 8d Vertical Mill Turning☞Monarch EE Precision Lathe Grinding ☞Brown & Sharpe #5 Surface Grinder
I always appreciate the good advice. I talked it over with my wife and agree that a project like this would be too much for a father-son project. Del is correct. You can't always assume that everyone knows how to weld. Not only that, people underestimate how difficult it is to assemble one of these bikes. Even if they know how to weld, they may loose interest, which could really suck. Even completely finished, the bike will still have to be dis-assembled for shipping. Putting it back together will still take the better part of an afternoon. The best thing about this bike is the warranty. The motor, shocks, bearings, frame, most of the bike is under warranty. Things that are not would be paint, tires, and so on. These are fine details which will be hashed out later.
Soooooooo, guess who I just got off the phone with? Joe Rivello. Who's Joe Rivello? The manufacturer of the Taco Mini Bike 100B. I was a little worried about reproducing a bike that might have a patent on it. After about an hour of patent searching, there was no patent on the bike, but, there was on the name. The name, "100B", is reserved with that design. Can I reproduce that bike? YES! But, I have to give it another name. I was thinking something generic like, "Baja Bike". Suggestions anyone?
Baja Boss? I like it! I took the day off and cleaned that mess up called "my shop". I'm getting rid of that green job box and I already built a work bench that will go crosswise and give me more room. It has a lower shelf for added storage. "Baja Boss". That's great. Baja Boss it is.
delraydella
- delraydella
-
Weldmonger
-
Posts:
-
Joined:Mon Apr 25, 2011 7:35 pm
-
Location:Detroit, MI
How are you finishing the bikes paintwise? Are you doing that, or will you send them out?
Welding☞Syncrowave 250,Millermatic 252,30a Spoolgun Cutting☞12" Hi-speed Cutoff Saw, 9x 12 Horizontal Bandsaw Milling☞Gorton 8d Vertical Mill Turning☞Monarch EE Precision Lathe Grinding ☞Brown & Sharpe #5 Surface Grinder
I discussed that with neighbors and friends, as well. I'm not going to have the bikes powder coated. Too expensive. I'm going to prime the frame with self-etching primer and paint them black. Most of the bikes will be painted black. To powder coat or use an expensive paint on a bike that will take alot of abuse and wind up being repainted, seems foolish. If someone wanted to order, at no extra charge, a specific color, that would be fine. As long as it's an obtainable color. If someone wanted to paint the bike themselves, then I can send the bike just primed-no discount. Someone did e-mail me and asked if I could send just the parts to make it a father and son project. Are you kidding me? Do you realize how hard these bike are to make? And if he blows a hole in the tube, I'm gonna send parts to everyone that messes up? I'd spend most of my time making parts. Anyway, the bikes will be completely assembled, then driven, dis-assembled, crated, then shipped. I already set up an account with UPS.
What I'm really gonna need help with is the price. I know exactly what the 100B's are going for, $2,000+. And I know why. Most of the parts that Joe Rivello is using are not made by him. He's having the tubes bent by someone else. If you look at the swing arm frame and the rear tire support, it's an "L" bar that's cut. Too many custom parts that my put the 100B out of reach for alot of people.
Mine, low end, about $1200. High end, about $1500. After all the numbers are in and the time spent manufacturing, I'll post the results. BTW, Joe said that the specs for the bike costs about $50,000. There are suttle differences in his bike and mine. I wonder how people will react to a similar bike for alot less money.
What I'm really gonna need help with is the price. I know exactly what the 100B's are going for, $2,000+. And I know why. Most of the parts that Joe Rivello is using are not made by him. He's having the tubes bent by someone else. If you look at the swing arm frame and the rear tire support, it's an "L" bar that's cut. Too many custom parts that my put the 100B out of reach for alot of people.
Mine, low end, about $1200. High end, about $1500. After all the numbers are in and the time spent manufacturing, I'll post the results. BTW, Joe said that the specs for the bike costs about $50,000. There are suttle differences in his bike and mine. I wonder how people will react to a similar bike for alot less money.
They should react to it fine, just for the fact that it's not an inadequate, imported knock off that is pretending to be something else. Anybody that looks for these items, should be able to know what makes it worth the money. Especially if it retains essentially the same service, or perhaps even exceeds that of it's competitors. It's not a bad thing if your product somehow bypasses the trendites and sticker worshipers. A lot of people don't appreciate paying extra for hype.
Miller ABP 330, Syncrowave 250, Dynasty 300 DX.
Honorary member of the Fraternity of Faded Tee Shirts.
Honorary member of the Fraternity of Faded Tee Shirts.
An update. The front fork is almost finished. I've ordered the shocks and will order the tires and wheels in a couple of weeks. By the way, I looked on e-bay and a gentleman is selling a taco 44 for $1700! really? It looks like the 100b, which he mentions. It looks a little like it. He says that they are hard to make, (ya think?). Anyway, I shouldn't have any problem selling these on e-bay.
There is an older fellow up the street from me who collects all the bicycles/parts that people throw away these days. He refurbs them to better than new functionally, and then sets the fleet of them up in his driveway. No for sale sign, nothing. I stopped by and bought a beach cruiser style schwinn for my son and the old gee told me he can barely keep up with the demand. Now he is known for having serviceable bicycles and repairs. Kids stop by his house where he has an air hose plumbed to the exterior of his garage and air their tires up. He teaches them how to tighten spokes and fix flats.CraigLam wrote: Anyway, I shouldn't have any problem selling these on e-bay.
Miller ABP 330, Syncrowave 250, Dynasty 300 DX.
Honorary member of the Fraternity of Faded Tee Shirts.
Honorary member of the Fraternity of Faded Tee Shirts.
I thought I would post a picture of the front fork. I cut away the part where the lower fork support hits the frame. I ordered the shocks, wheels, tires and axles. It should be here by Friday. That's when the fun begins.
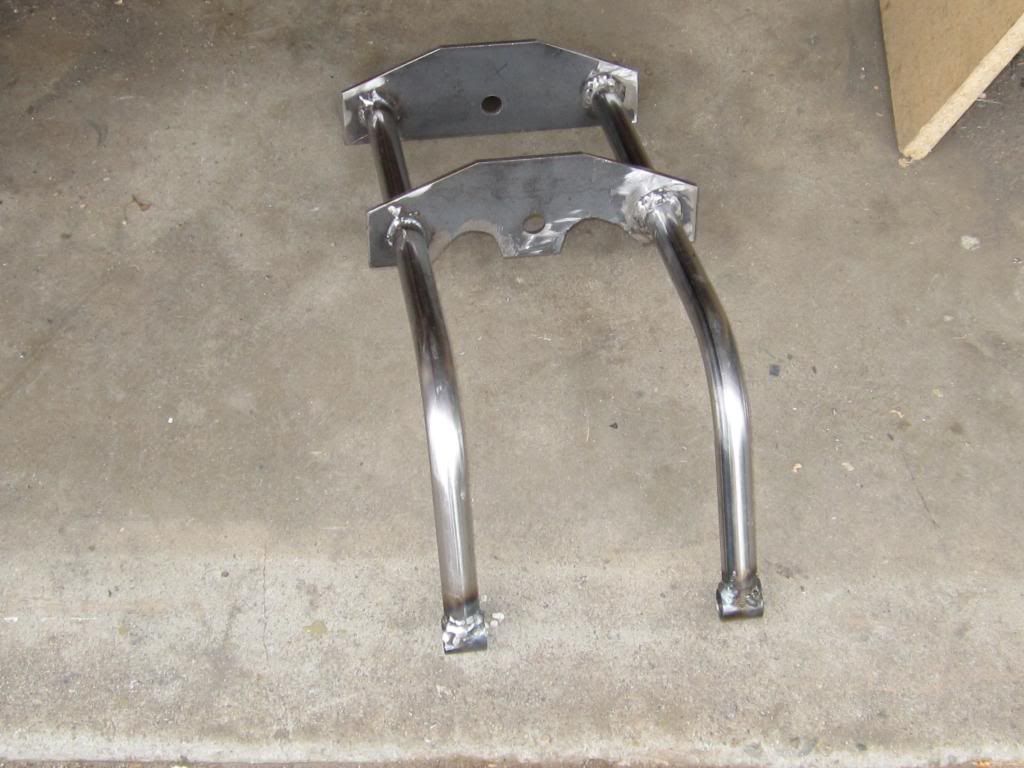
I bought a flap disc and I'm cleaning up the welds. Some are good enough they don't need cleaning. As I make more bikes, I should get better at this.
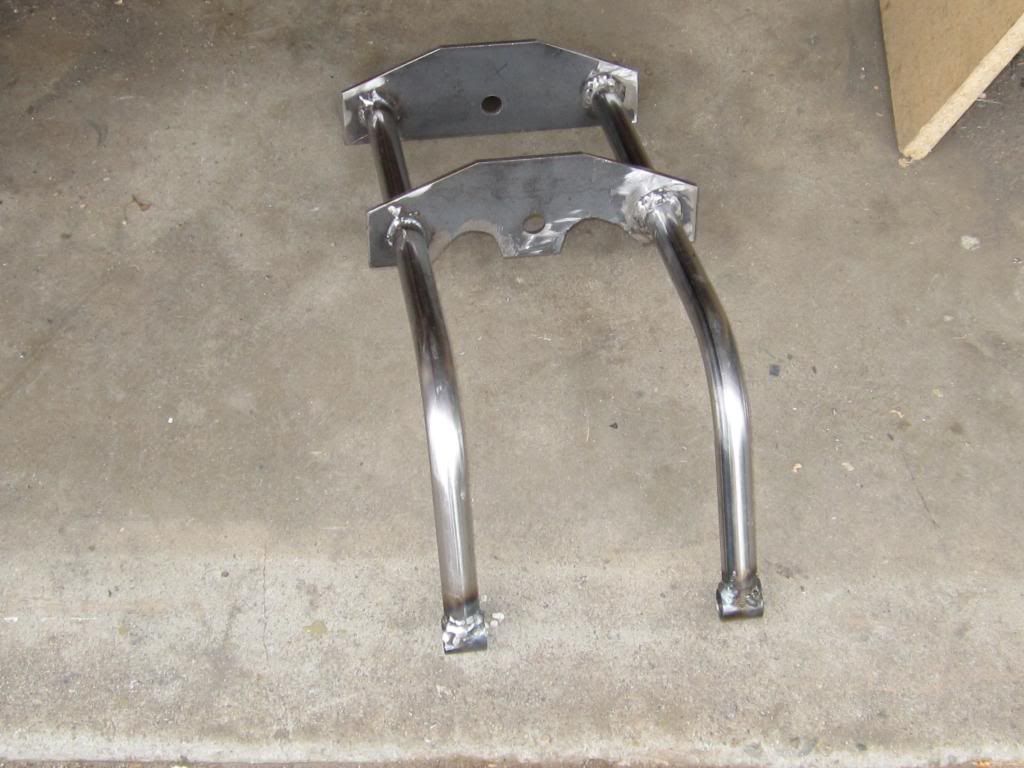
I bought a flap disc and I'm cleaning up the welds. Some are good enough they don't need cleaning. As I make more bikes, I should get better at this.
Hi Craig,
You might want to think about building yourself a frame jig to make holding and welding up the frame a lot easier. You can make them as complex (or simple) as you want. Google "home made motorcycle frame jig" will give you more information that you ever wanted to know but you really need to look into this.
Free plot files are available here for down load; http://chopperhandbook.com/jigs2.htm
Mechworks has a real good set you can purchase as well at the bottom of this page; http://www.mechwerks.com/Frame_Jig.htm
Admittedly these may be it bit more than needed for a mini bike frame but the point is you need to be able to set the rake (angle) of the neck and keep it true with the rear tire when it's welded in place.
Just $.02 worth from an old scooter tramp.
You might want to think about building yourself a frame jig to make holding and welding up the frame a lot easier. You can make them as complex (or simple) as you want. Google "home made motorcycle frame jig" will give you more information that you ever wanted to know but you really need to look into this.
Free plot files are available here for down load; http://chopperhandbook.com/jigs2.htm
Mechworks has a real good set you can purchase as well at the bottom of this page; http://www.mechwerks.com/Frame_Jig.htm
Admittedly these may be it bit more than needed for a mini bike frame but the point is you need to be able to set the rake (angle) of the neck and keep it true with the rear tire when it's welded in place.
Just $.02 worth from an old scooter tramp.

Go break something, then you can weld it back the right way.


Bob, thanks for the info. I was going to post earlier, but, all of the parts are not in yet. The mini bike shocks are in and the tires and wheels are due tomorrow by ups by the end of the day. Actually, that was my plan. After all the parts were made and the bike is assembled, every part will have a blue print record with all the pertinent info on that particular print. Then I'm going to shrink the prints and make a kind of manual. Having a Takas bender is a super big advantage. Bending two pipes, using the angle indicator, they will come out exactly the same. Finally, An assembly jig is a very important step. It insures that all the products made from that jig are the same. I appreciate the info greatly. I like the idea that the jigs are lightweight steel and easily dis-assembled for storage. Mechwerks looks a little complicated, but, the message is there. I'll probably use some of those ideas. I also like the idea of the square tube frame build-up. There are still minor adjustments that I have to make with the angle of the side frames. Thanks again Bob, for the info.
FINALLY, my tires, wheels, and shocks came in.
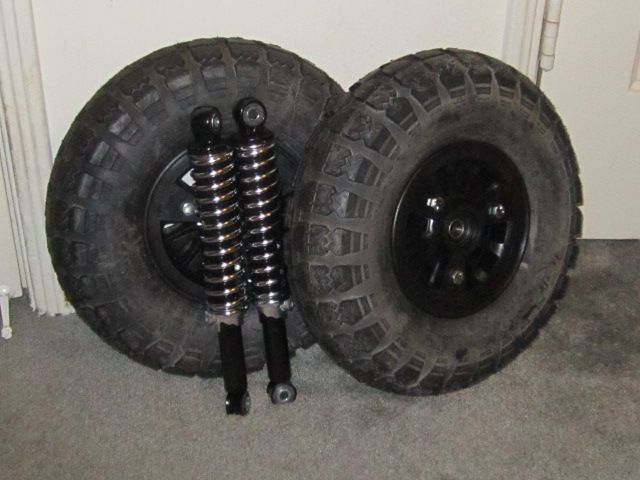
I originally planned for 5.3" wide tires. The supplier strongly suggested that those tires were strictly off-road and would not be a good seller. So, I got a universal tire. It's only 4", but, looks pretty good. I will be laying the suspension and will have my work cut out for me. It will be completely different than the 100b. The rims are Azulite. The aluminum rims were too pricey.
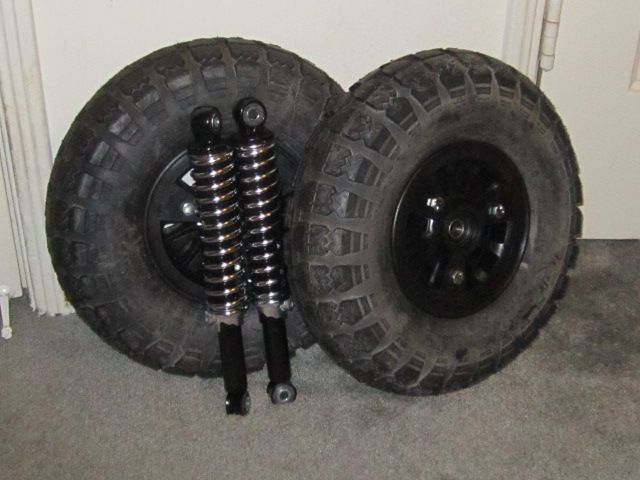
I originally planned for 5.3" wide tires. The supplier strongly suggested that those tires were strictly off-road and would not be a good seller. So, I got a universal tire. It's only 4", but, looks pretty good. I will be laying the suspension and will have my work cut out for me. It will be completely different than the 100b. The rims are Azulite. The aluminum rims were too pricey.
Return to “Welding Projects - Welding project Ideas - Welding project plans”
Jump to
- Introductions & How to Use the Forum
- ↳ Welcome!
- ↳ Member Introductions
- ↳ How to Use the Forum
- ↳ Moderator Applications
- Welding Discussion
- ↳ Metal Cutting
- ↳ Tig Welding - Tig Welding Aluminum - Tig Welding Techniques - Aluminum Tig Welding
- ↳ Mig and Flux Core - gas metal arc welding & flux cored arc welding
- ↳ Stick Welding/Arc Welding - Shielded Metal Arc Welding
- ↳ Welding Forum General Shop Talk
- ↳ Welding Certification - Stick/Arc Welding, Tig Welding, Mig Welding Certification tests - Welding Tests of all kinds
- ↳ Welding Projects - Welding project Ideas - Welding project plans
- ↳ Product Reviews
- ↳ Fuel Gas Heating
- Welding Tips & Tricks
- ↳ Video Discussion
- ↳ Wish List
- Announcements & Feedback
- ↳ Forum News
- ↳ Suggestions, Feedback and Support
- Welding Marketplace
- ↳ Welding Jobs - Industrial Welding Jobs - Pipe Welding Jobs - Tig Welding Jobs
- ↳ Classifieds - Buy, Sell, Trade Used Welding Equipment
- Welding Resources
- ↳ Tradeshows, Seminars and Events
- ↳ The Welding Library
- ↳ Education Opportunities