I have had this HF 4x6 probably since 2007 or so. Right when I got it, I discarded the flimsy folding "legs", and made a wood base for it. I later added a hydraulic piston to replace the spring, and for the most part that has been it until last fall (2013). But now that I am starting to do/learn more welding, and cutting metal more often, I decided to "attack" the many weak points, including the over-heating motor (which is obviously too small for the job - some of these actually catch on fire!). I also wanted to add cooling to it, so I decided to do a complete overhaul of the bandsaw. This took about 3 months (on and off), and several purchases spread over the 3 months (I am on a budget, like most people), but now that it is 99% complete, I wanted to share my project.
I of course over-built the base/stand, but I figured I can fairly easily re-use the base with another bandsaw if this one totally needs a replacement later on. I used 1-1/4" (1/8" wall) squared hot rolled steel, and 1-1/4" (1/4" wall) angle iron for the top. Everything was MIG welded with my MIG200 using 0.035" solid wire with about 25cfpm of 75%/35% shielding gas.
I literally have over 100 pictures, so over the next few days I will pick-n-choose some of them to show the progression towards the end product you see below.
Here is the "before" picture - I am checking the size of the new top (notice size of stock motor):
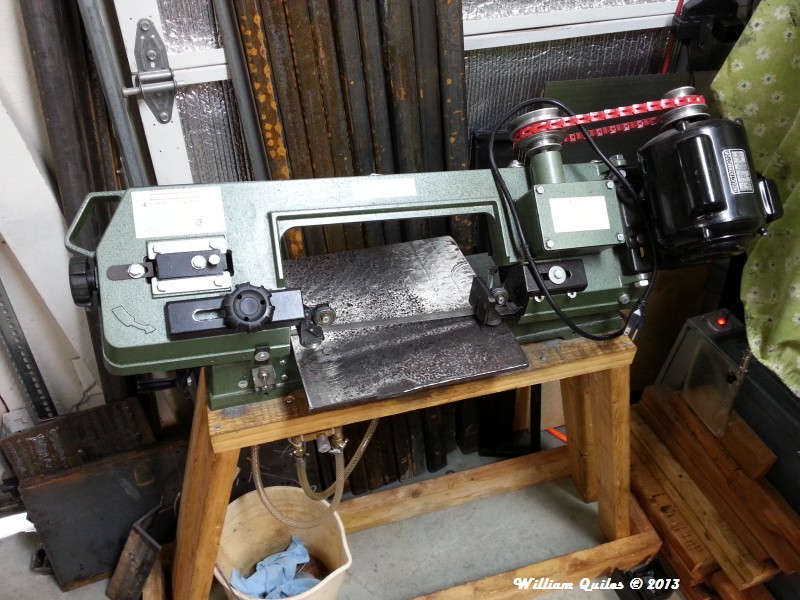
Here is the "raw" new welded base:
Previous wood base next to new base:
Preliminary picture showing the hydraulic piston in place:
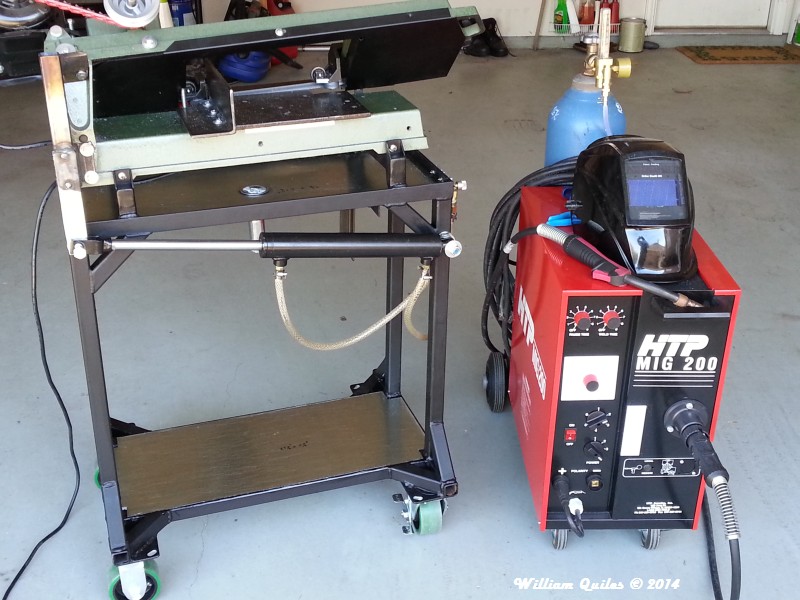
Finished bandsaw after all mods:
- new steel base (2 coats of flat black paint)
- replaced 1/3 HP (Chinese rating!) SP motor with USA-made, Baldor 3/4HP 3P motor (using TECO VFD for variable speed and safety switch)
- new clamping "system" (more on that later)
- making new "arm" for hydraulic system
- adjustable coolant system (running
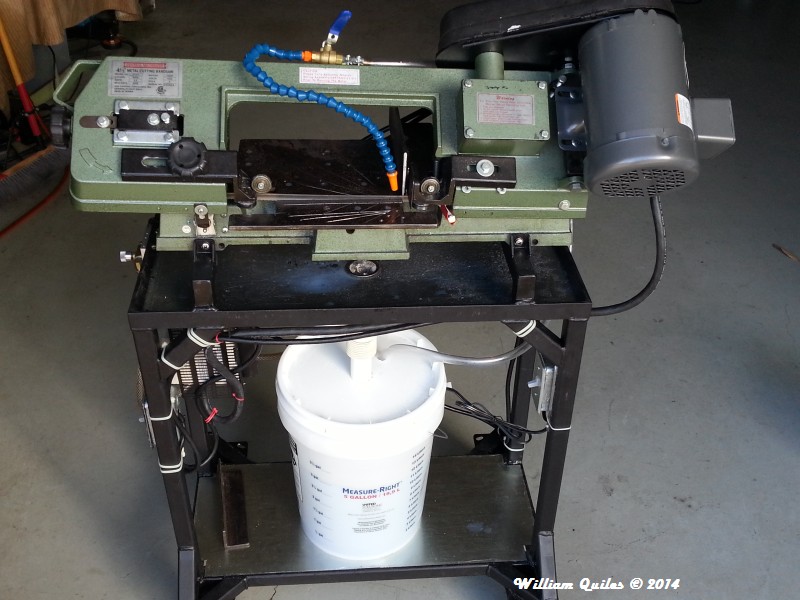
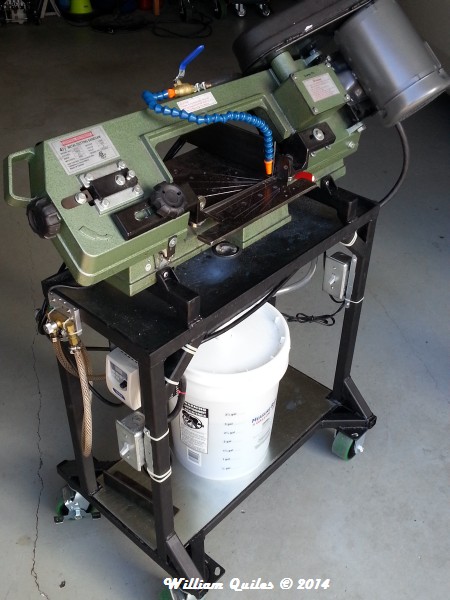
Will