What welding projects are you working on? Are you proud of something you built?
How about posting some pics so other welders can get some ideas?
How about posting some pics so other welders can get some ideas?
Nice can't wait to finally dig into mine
I weld stainless, stainless and more stainless...Food Industry, sanitary process piping, vessels, whatever is needed, I like to make stuff.
ASME IX, AWS 17.1, D1.1
Instagram #RNHFAB
ASME IX, AWS 17.1, D1.1
Instagram #RNHFAB
LS Customs
- LS Customs
-
Ace
-
Posts:
-
Joined:Tue Feb 23, 2016 11:56 pm
thanks, I still havent got a chance to sit down and play with the settings on the welder, etc... but I did weld some aluminum and finish setting up my water cooler... i will mount this on a stand (where i can adjust the angle) and then sit down and practice a little...Rick_H wrote:Nice can't wait to finally dig into mine
i typically try to make something as i practice...
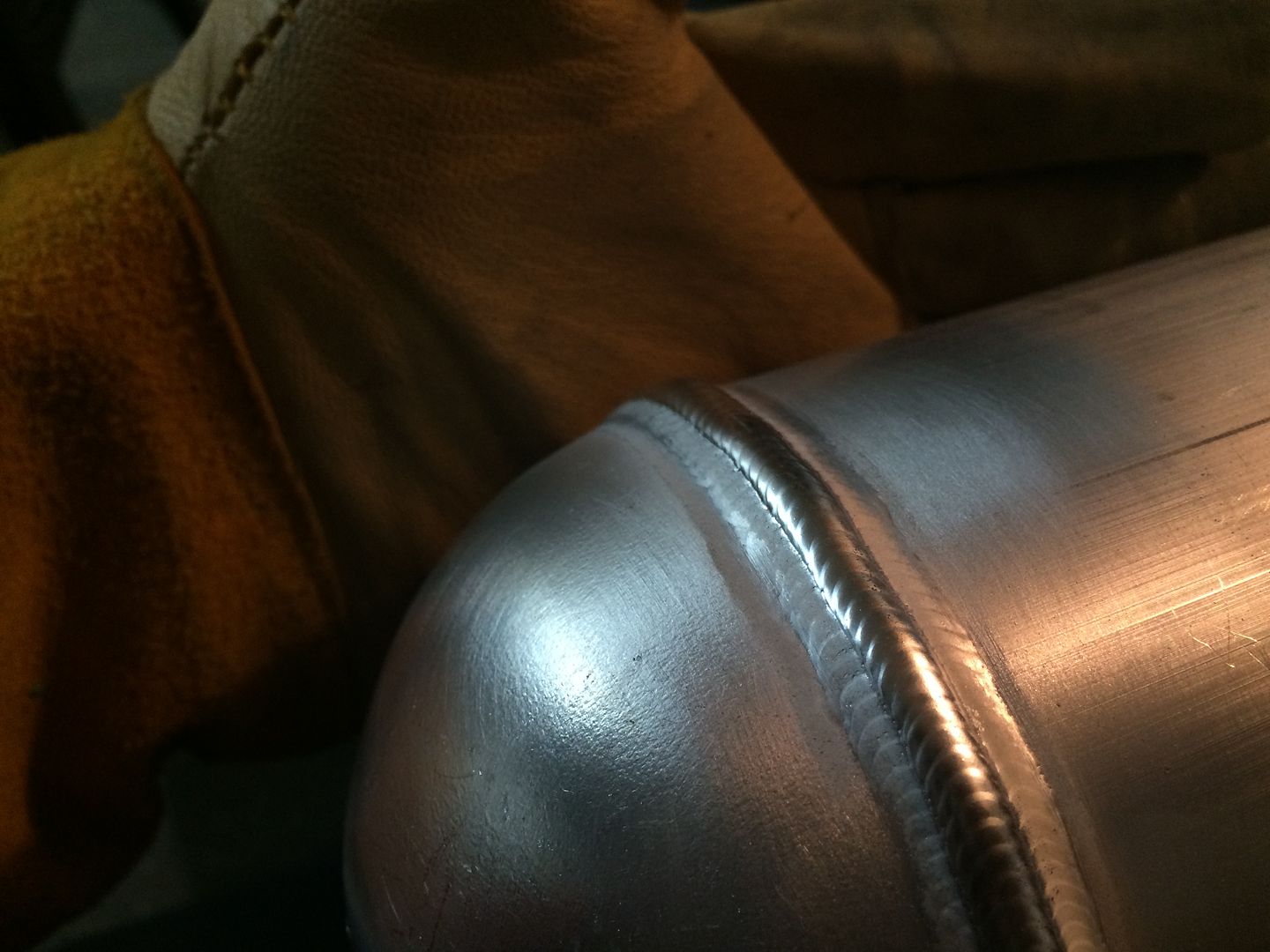
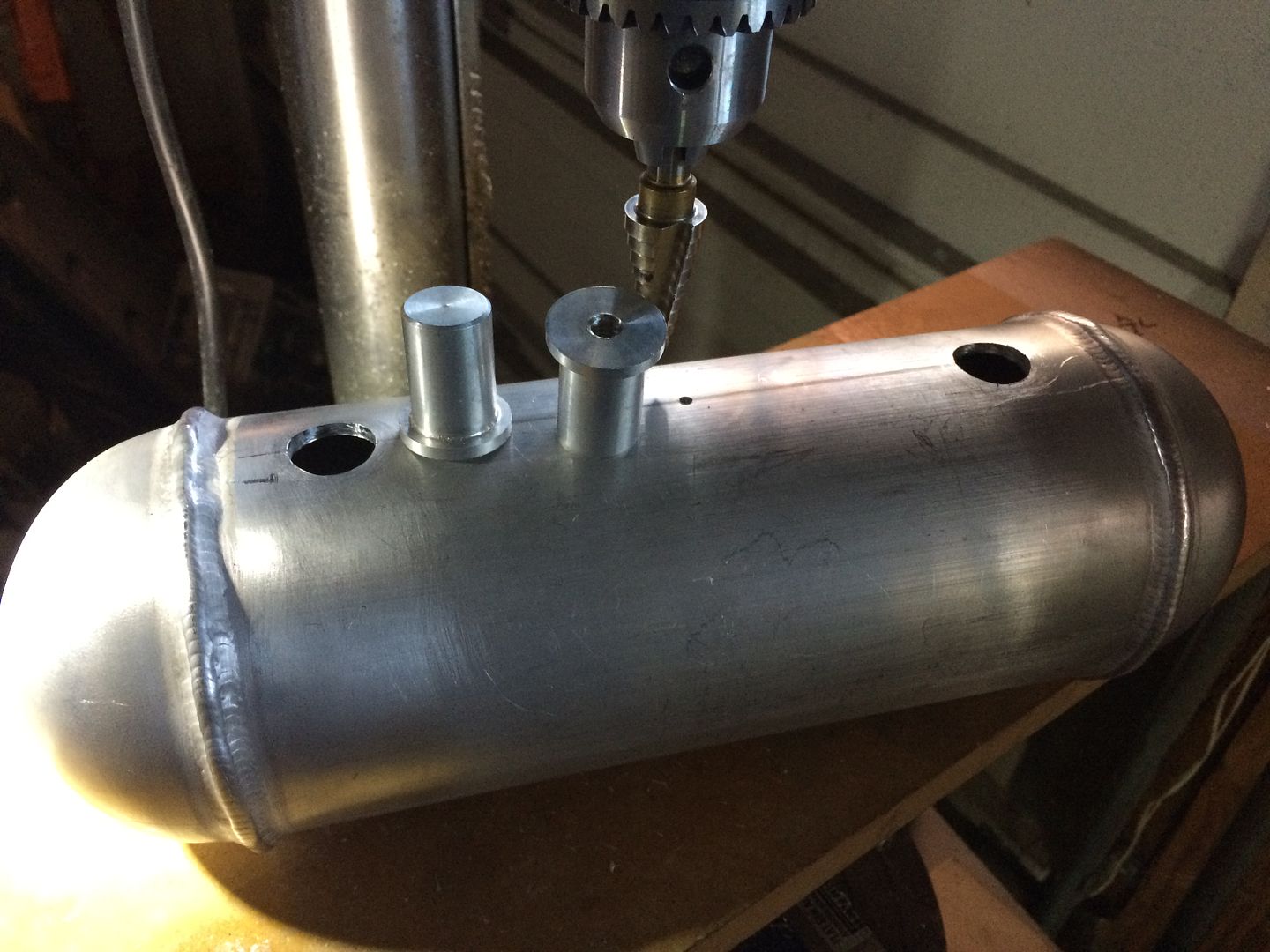
water cooler is working really well too... gotta get garage cleaned up and get some seat time in
LS Customs
- LS Customs
-
Ace
-
Posts:
-
Joined:Tue Feb 23, 2016 11:56 pm
next up is the cosmetic work... paint etc... i could have used a much larger chuck than the 6"... but most of what i want to use this for would be relatively small diameter 8" and smaller... also some oddball shapes, where i would use a jig... i wish i would have bought a 4 jaw independently adjustable chuck, as that would help with non cylinder shaped objects... but i could always pick one up later if i need more versatility than the plates that will bolt to the chuck jaws when needed... the 6" shars chuck was inexpensive and i did not want to trust buying a cheaper Chinese "welding positioner" style chuck... which is much thinner profile, etc... but just about any chuck could be adapted to this setup easily...
i picked up some taller soft jaws... so that i could work around different end caps, etc, when i am welding aluminum tanks... the shorter jaws need to be reversed to open wide enough and then they are not tall enough where they will grab the tubing or pipe, to work with different profiles on end caps, etc... but the soft jaws i picked up off ebay (were $25 shipped) are very tall and i will remove/mill material to make them hold up to approx 8" diameter and also notch them where they would clear around any weld bead profiles on tanks, etc (so the part will clamp evenly and true)... if necessary...
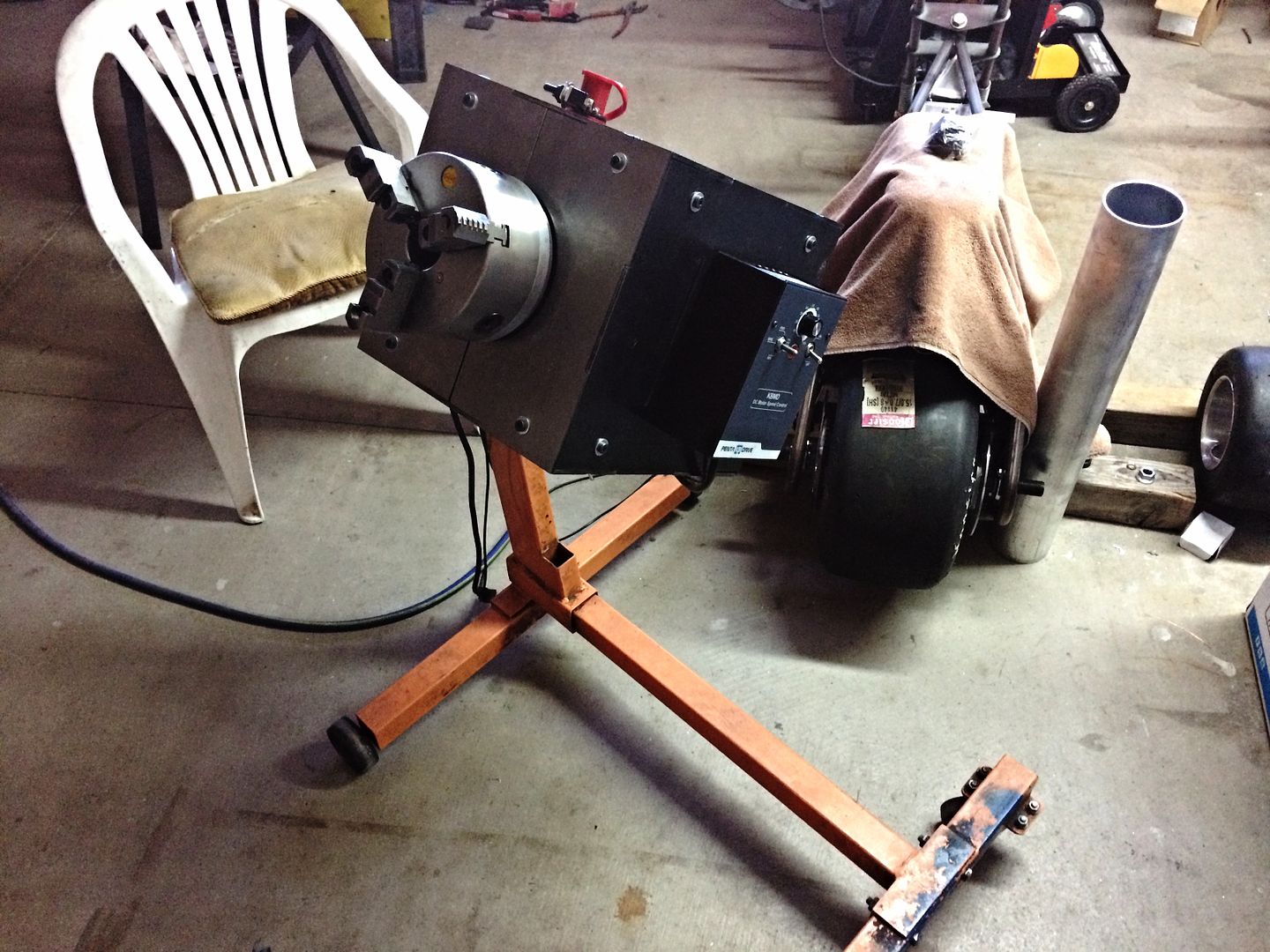
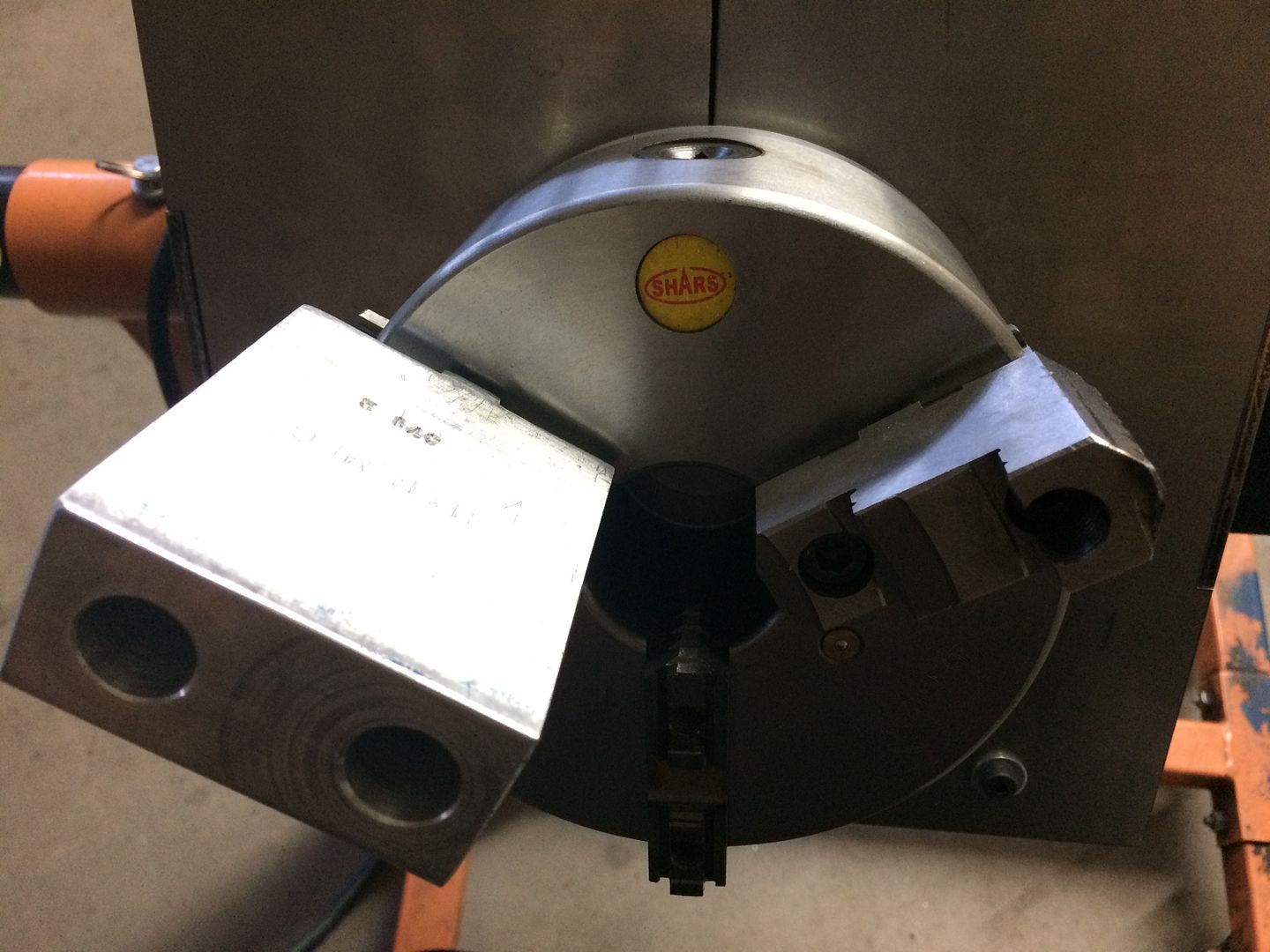
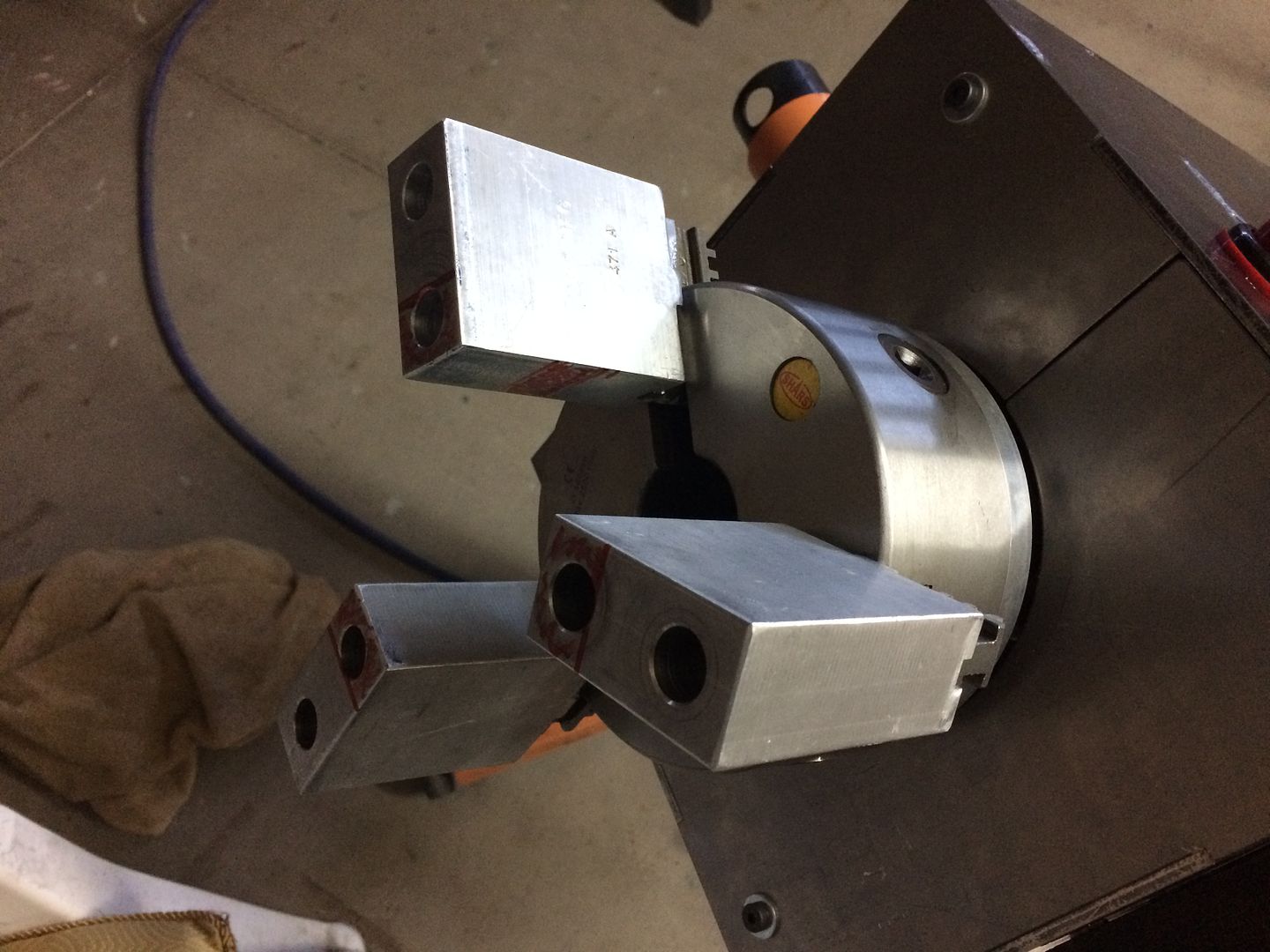
i picked up some taller soft jaws... so that i could work around different end caps, etc, when i am welding aluminum tanks... the shorter jaws need to be reversed to open wide enough and then they are not tall enough where they will grab the tubing or pipe, to work with different profiles on end caps, etc... but the soft jaws i picked up off ebay (were $25 shipped) are very tall and i will remove/mill material to make them hold up to approx 8" diameter and also notch them where they would clear around any weld bead profiles on tanks, etc (so the part will clamp evenly and true)... if necessary...
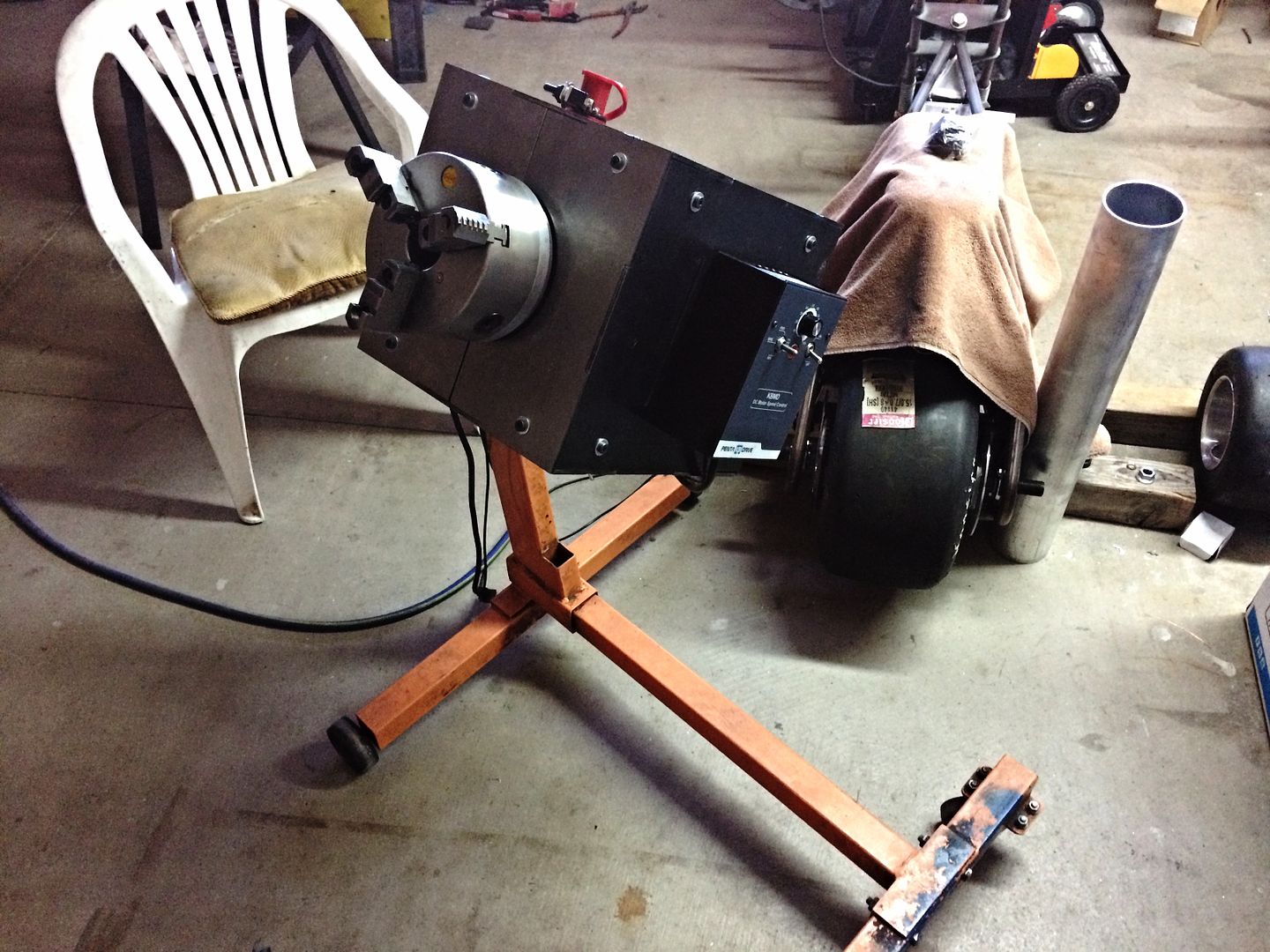
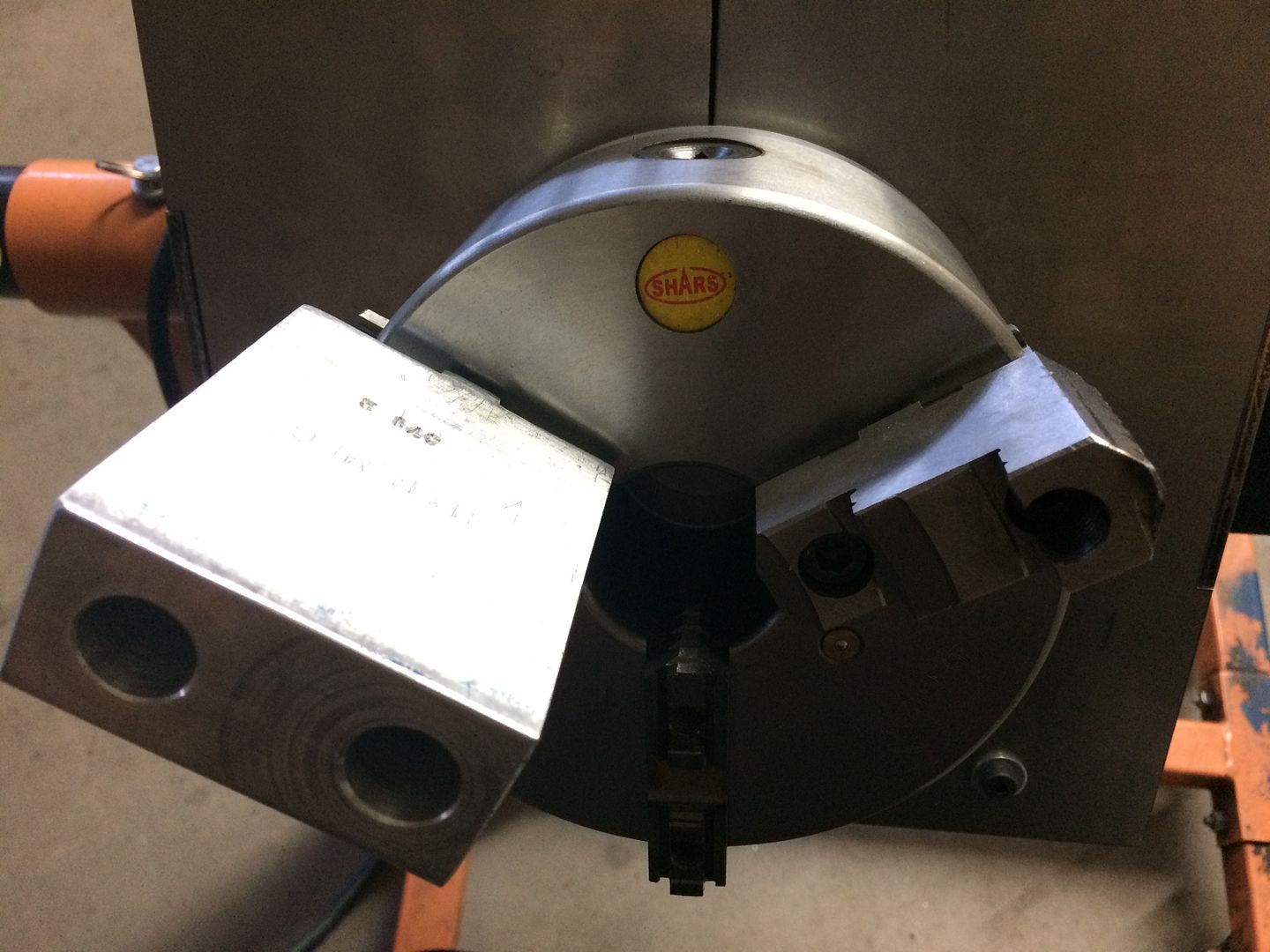
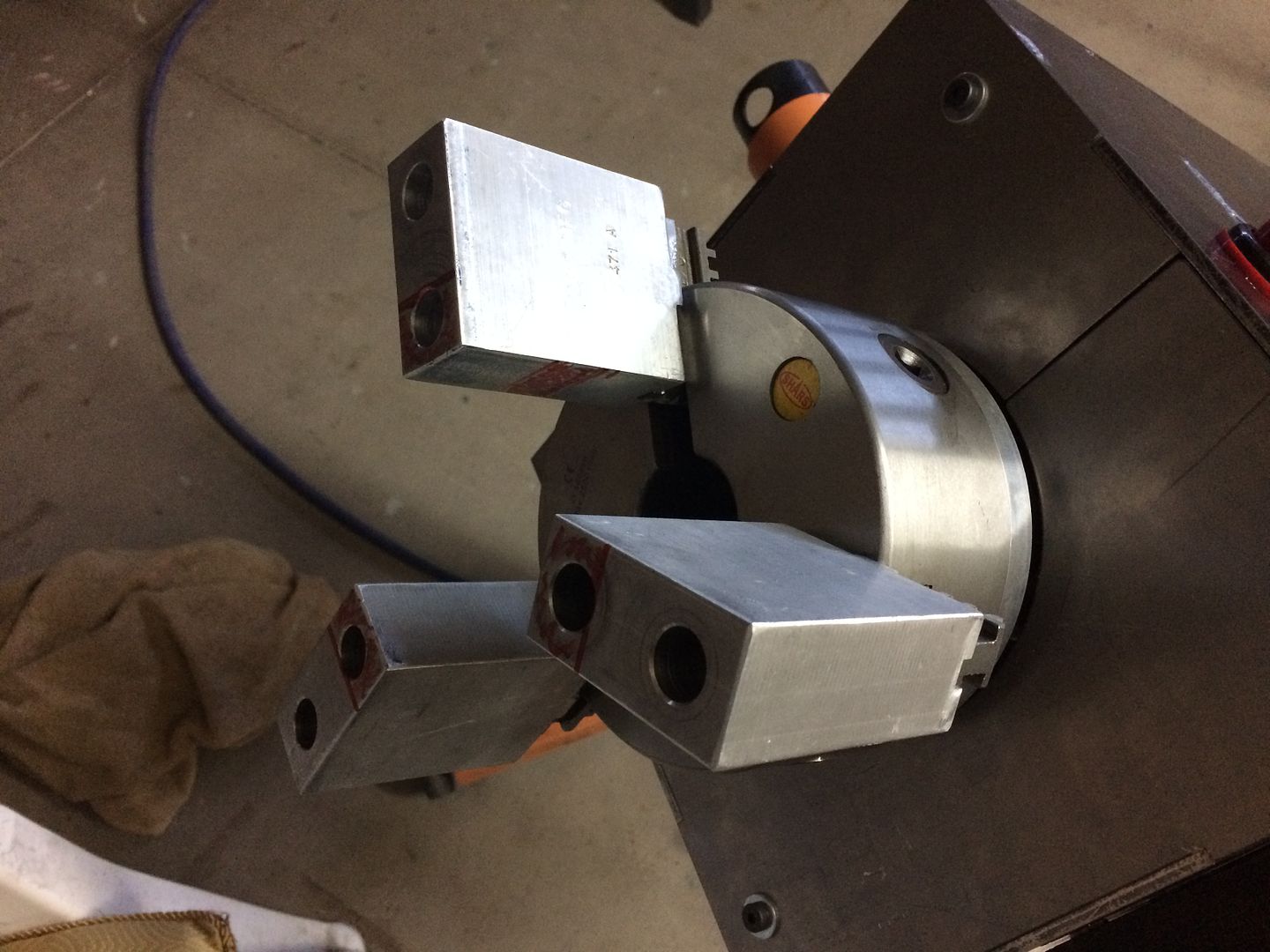
LS Customs
- LS Customs
-
Ace
-
Posts:
-
Joined:Tue Feb 23, 2016 11:56 pm
I also made a hand rest, and a tig torch holder that will bolt to the engine stand also... and though i have tested welding with the positioner while holding the torch... i also, attached the torch to the holder and it rotated true enough, where, as long as fit up and part is properly put in the chuck, i can use the torch holder and just hand feed the wire... i wont be doing this though, until i am consistently awesome on and off the machine, as the point for me is to improve my tig welding skills all around... i have the tig pen, which also made it extremely easy to feed wire consistently and leave hand still... but after watching Jodys videos showing hand feed techniques... i just spent a few minutes practicing and i can now feed the wire faster without the tig pen. which allows me to rotate the part as fast as i can keep up with it... versus limiting the speed to as fast as i can rotate the wheel on the tig pen
LS Customs
- LS Customs
-
Ace
-
Posts:
-
Joined:Tue Feb 23, 2016 11:56 pm
and I went ahead and programmed another simple plate, that would correct mount and register a 10" 4 jaw (independent) chuck (which is approx. $135, so inexpensive also) where i would just unbolt the smaller chuck and bolt on the 10" in approx a minute... i may pick this chuck up at some time in the future... for larger diameter or odd shaped parts where i could center them on the chuck easily... I wish i would have purchased this one in the first place... but i did want the ease of the self centered 3 jaw and will prob use that way more often... if i sell this setup or build another... i will use the 10" 4 jaw initially...
but this would bolt on the same as the other adapter I made...
back
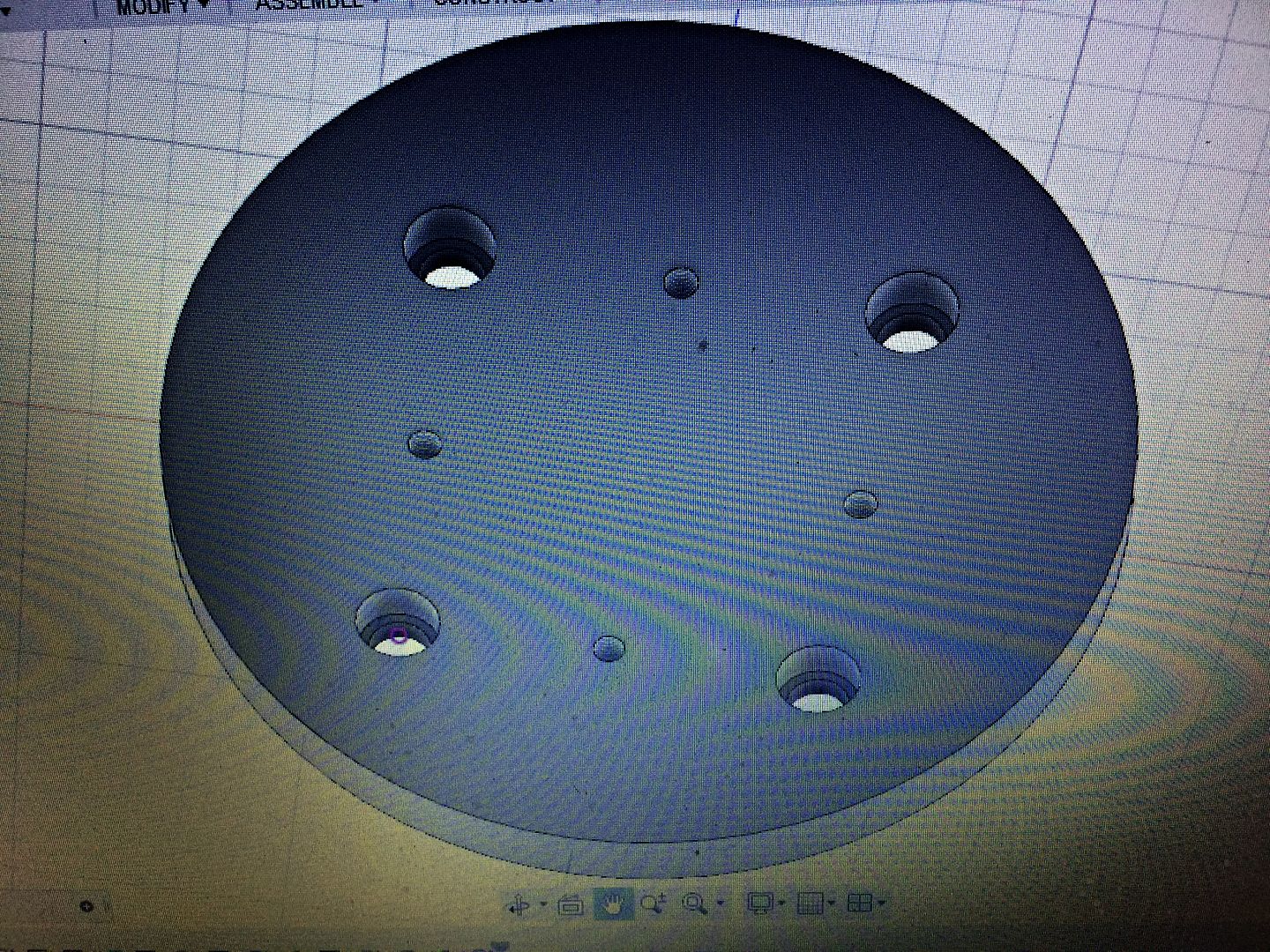
front
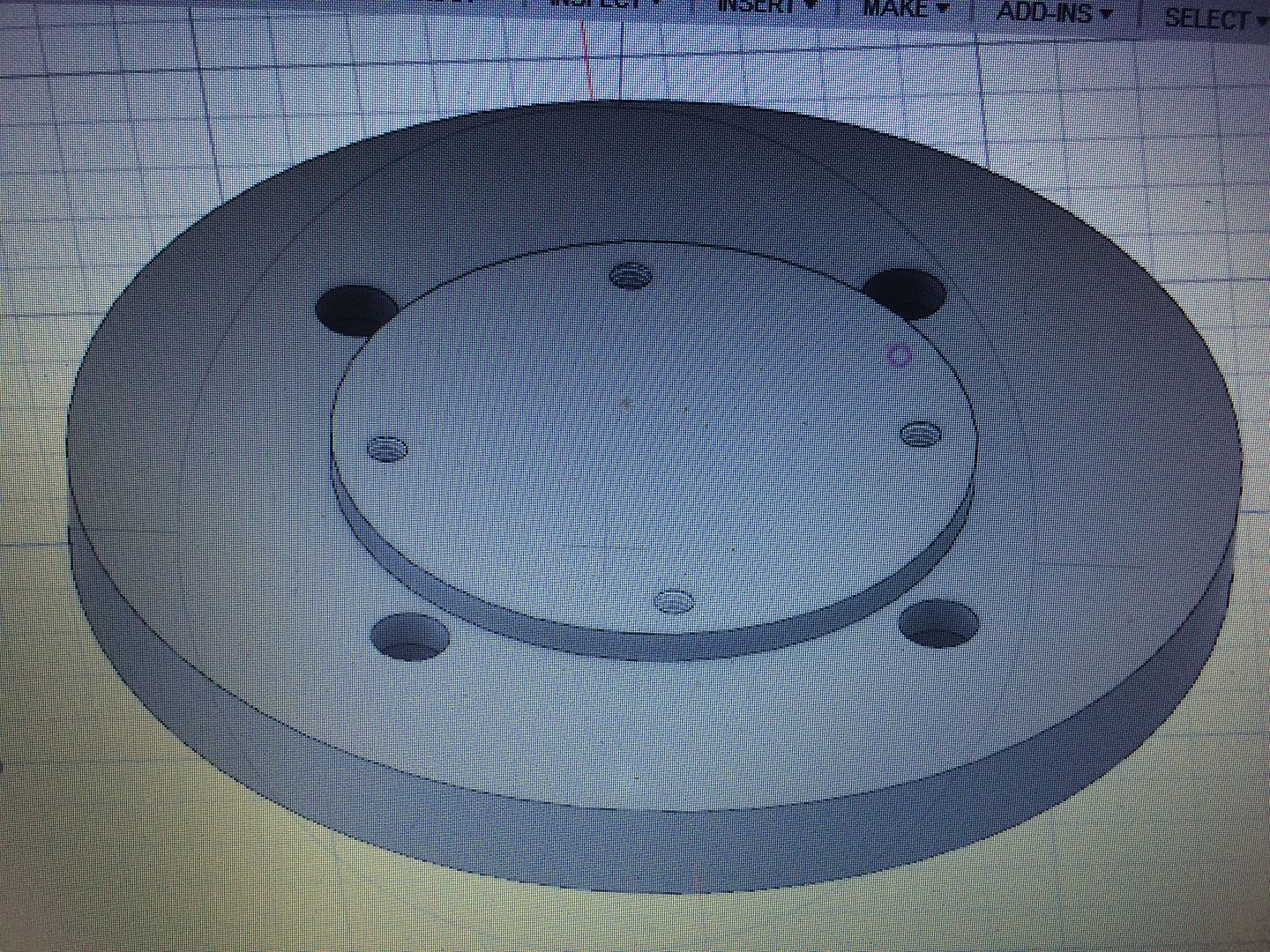
existing chuck and plate
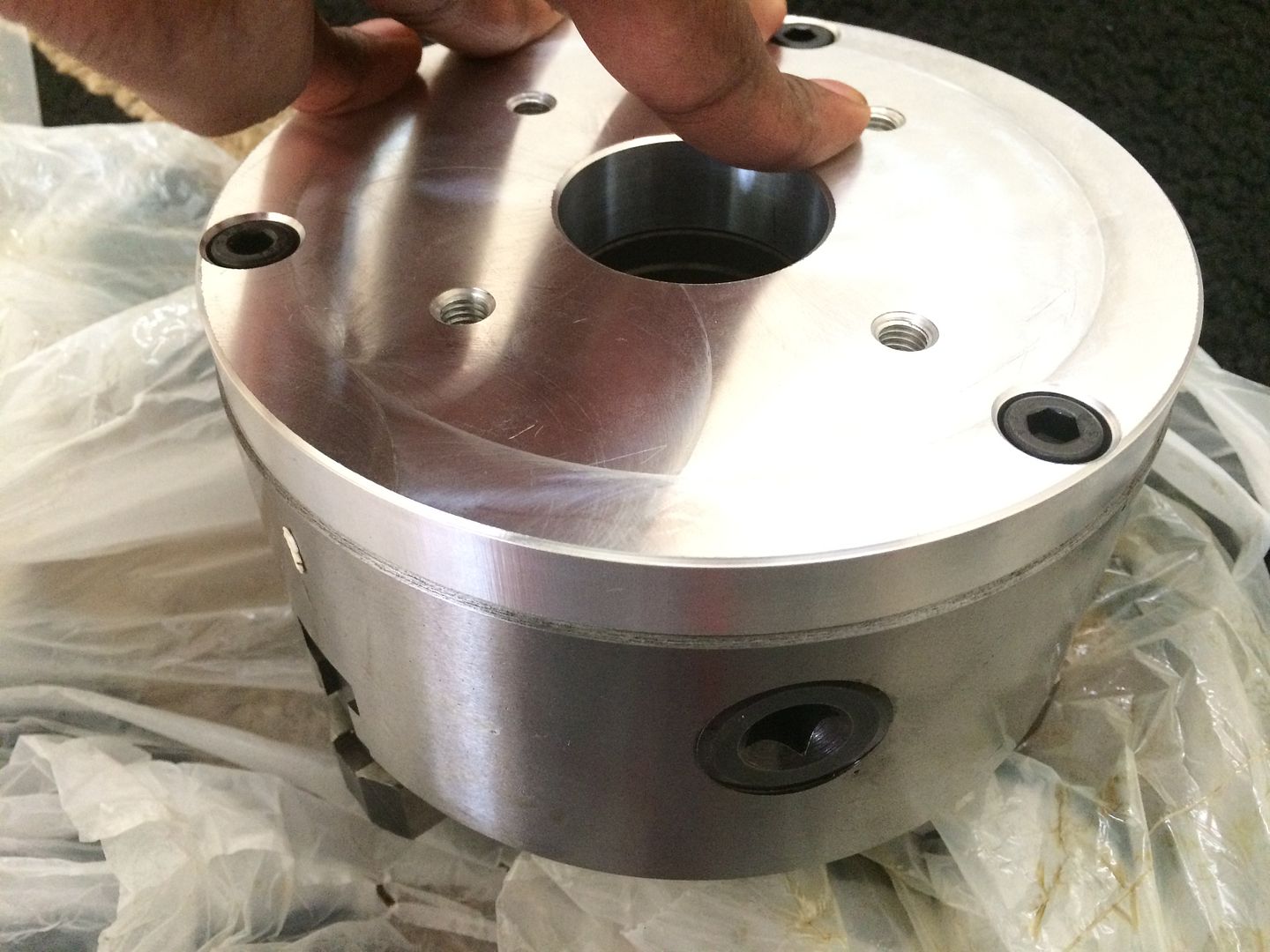
but this would bolt on the same as the other adapter I made...
back
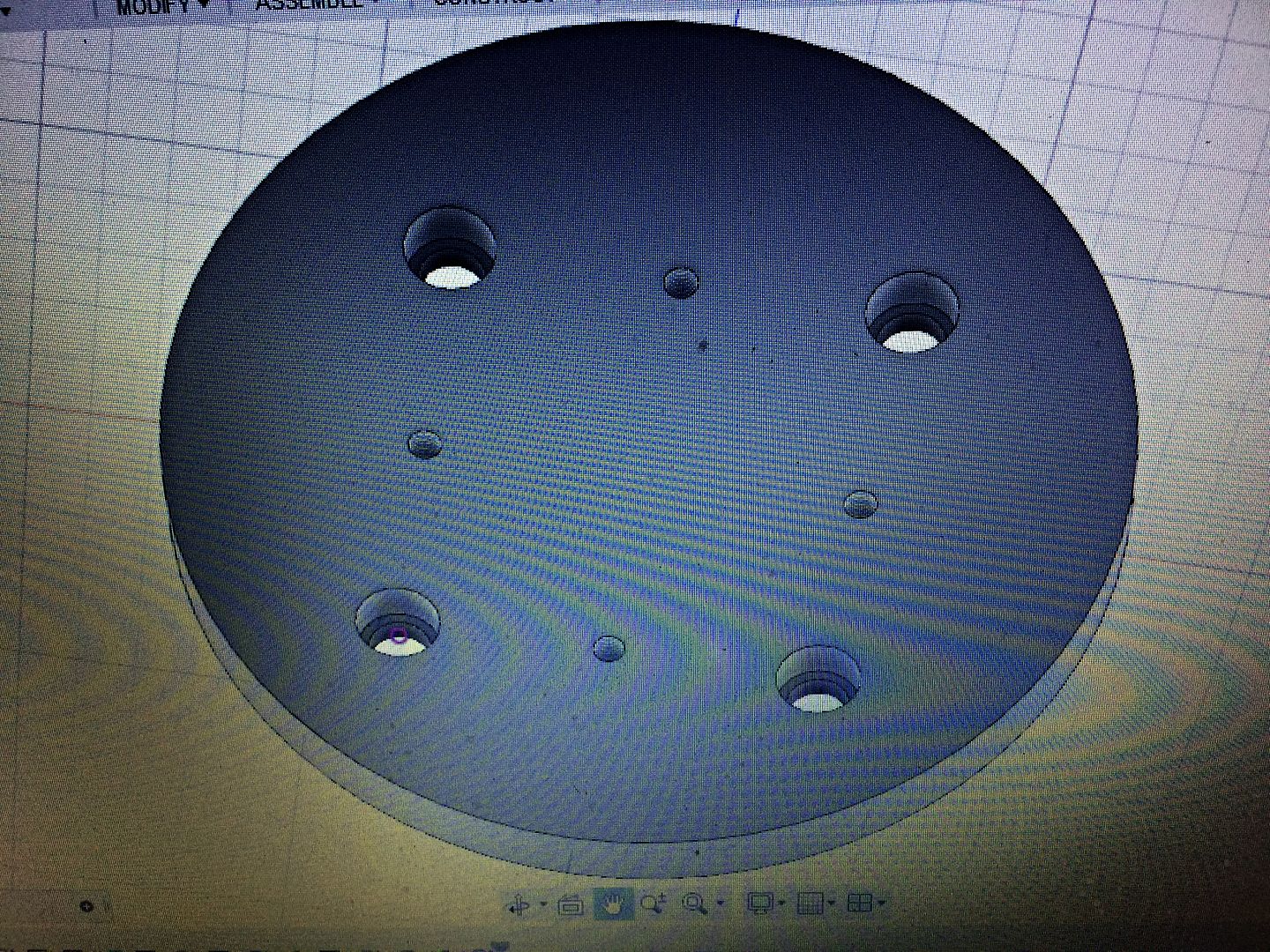
front
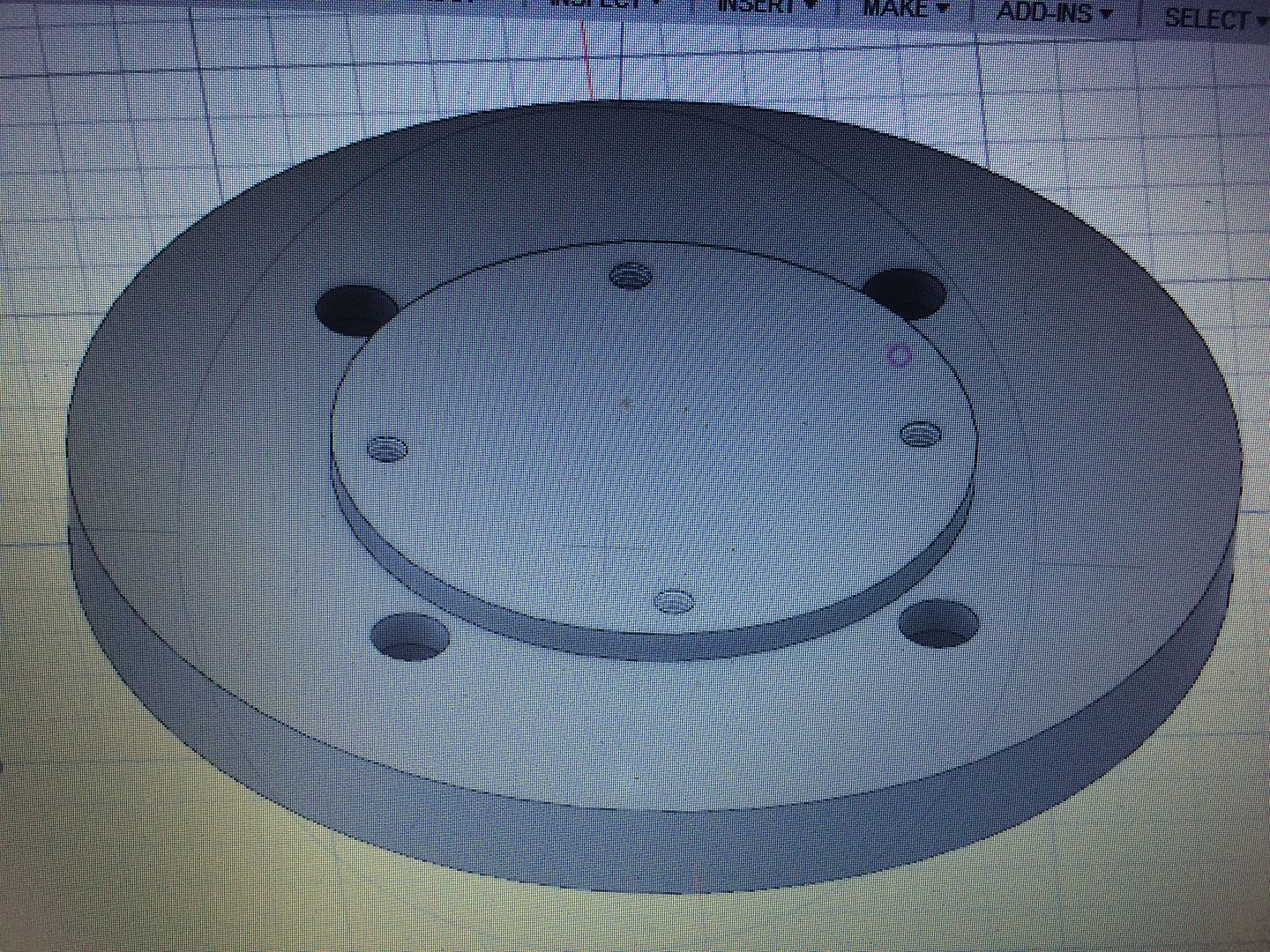
existing chuck and plate
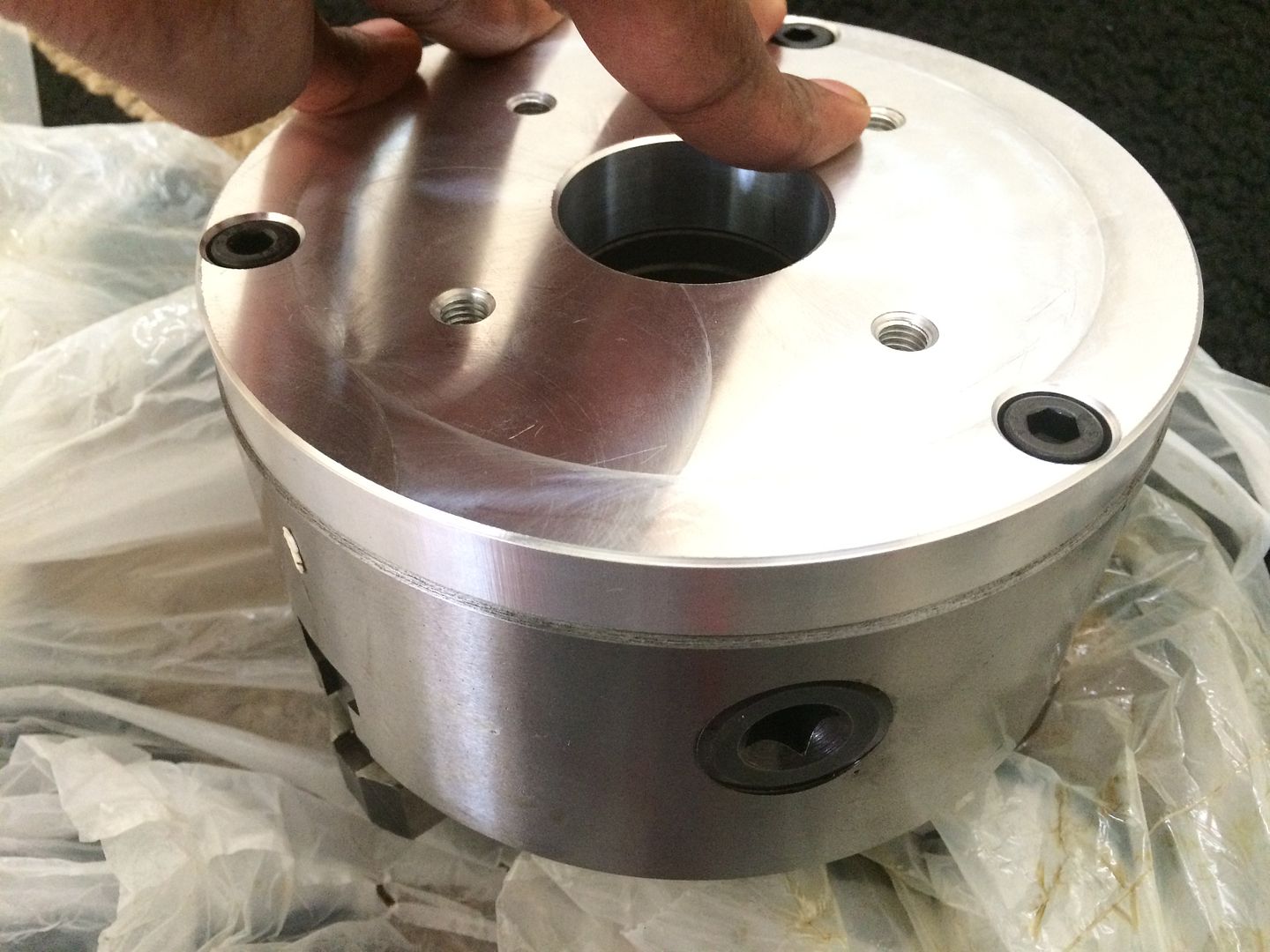
LS Customs
- LS Customs
-
Ace
-
Posts:
-
Joined:Tue Feb 23, 2016 11:56 pm
as I have previously stated the jaws that came with this size chuck, when opened all the way, do not open up quite enough for the size of tubing I typically clamp in it... and though they are reversible, when revised, they are not tall enough, if the profile of an end cap isnt flat....
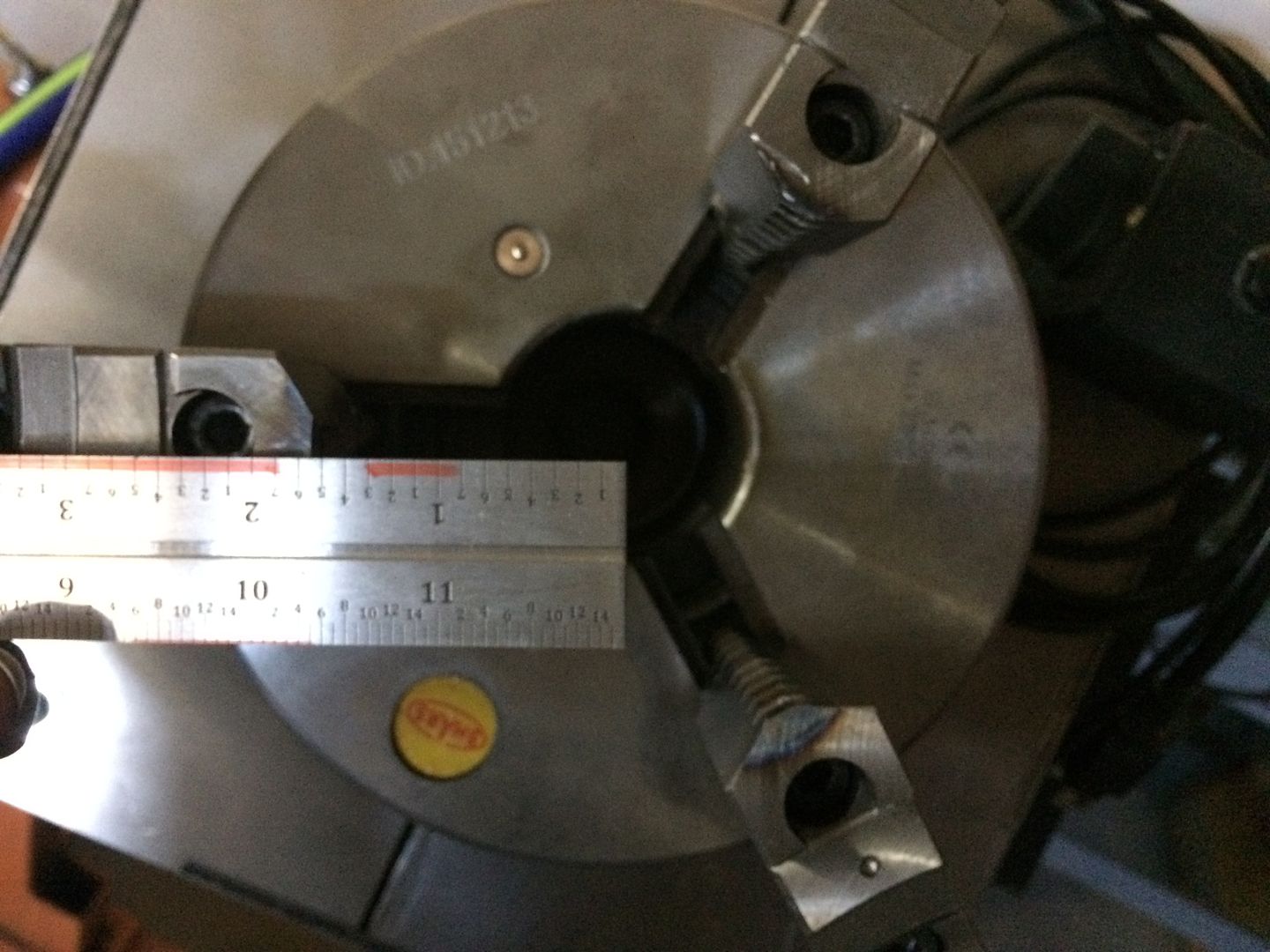
i drew up a program in cad to modify the soft jaws to fit a wide range of things i will be clamping in the 3 jaw... i modified it to open up another two inches in diameter and shaped the other side where when reversed would still clamp very small diameter...
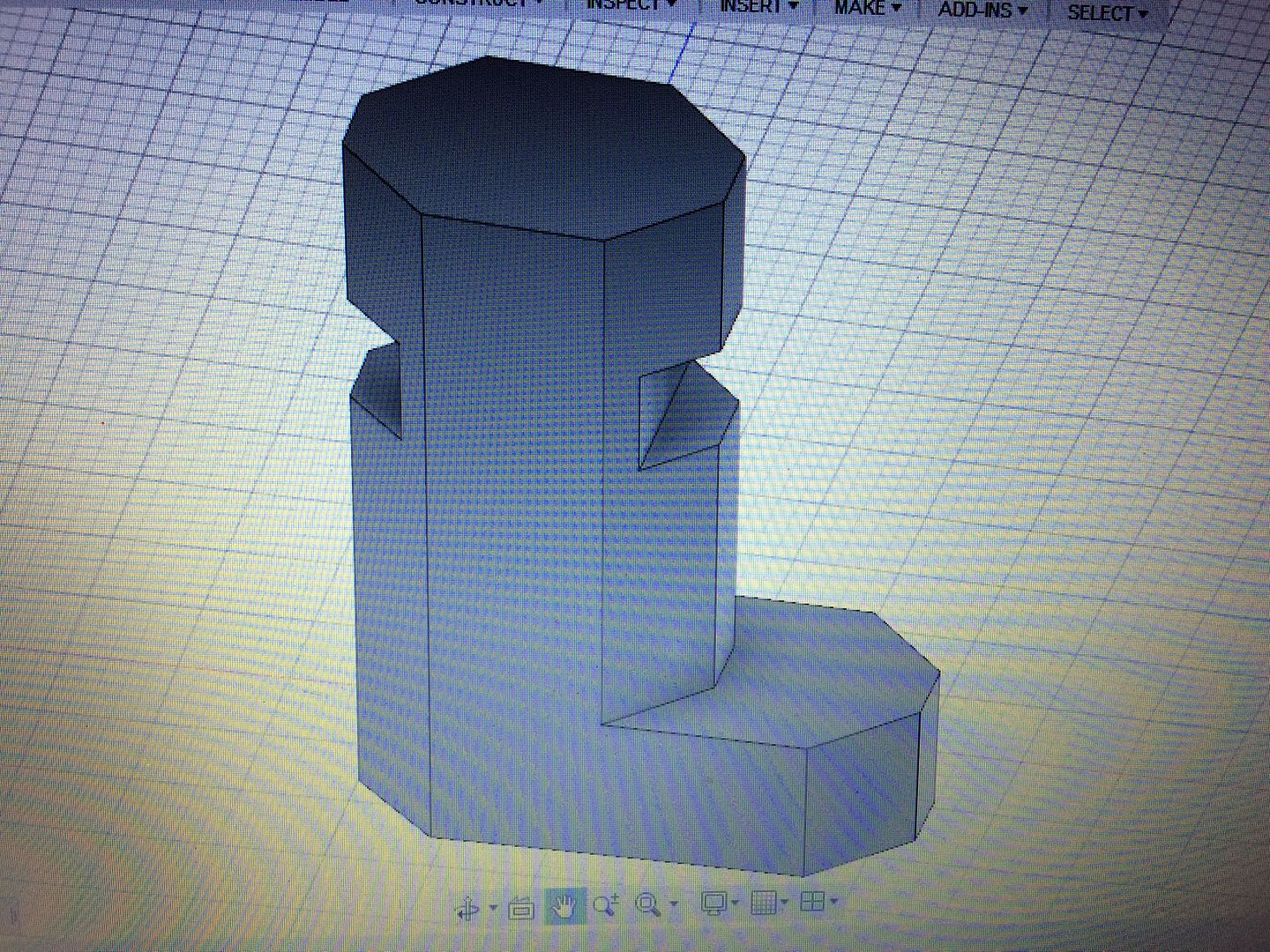
i did not leave the notches in the program, and will be notching it, if i need to, after i clamp a few parts in the chuck and mark exactly where i want the notch...
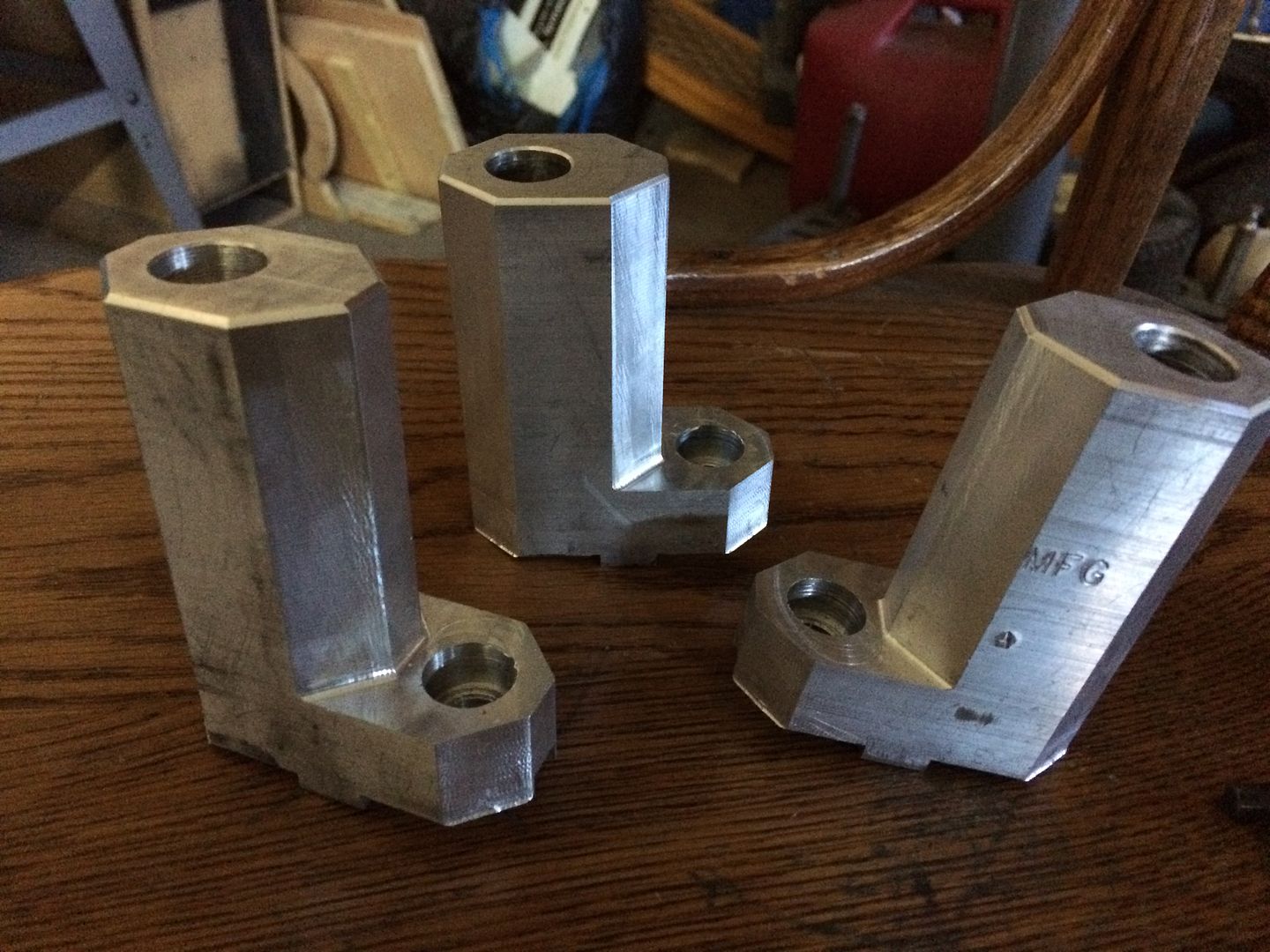
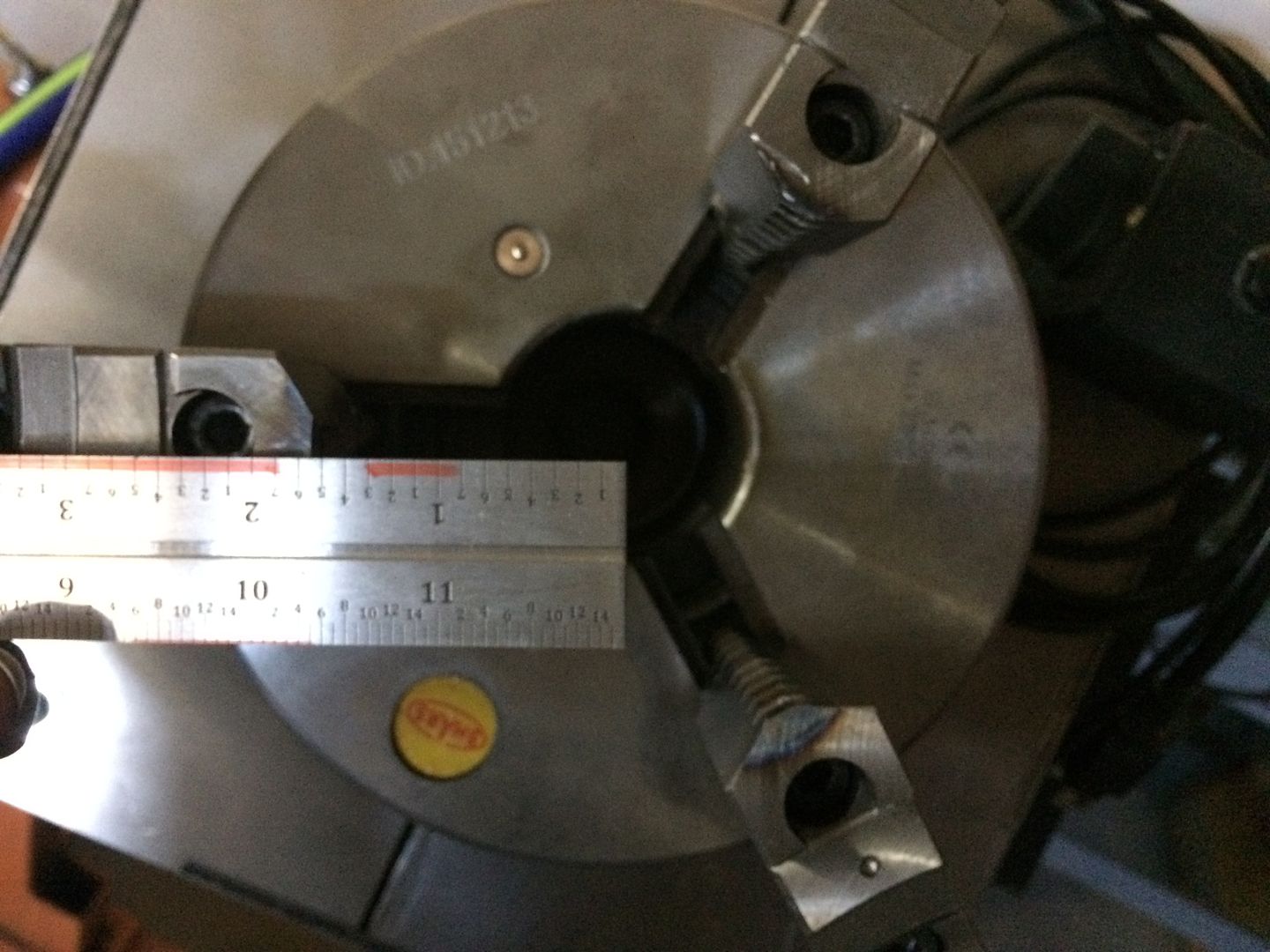
i drew up a program in cad to modify the soft jaws to fit a wide range of things i will be clamping in the 3 jaw... i modified it to open up another two inches in diameter and shaped the other side where when reversed would still clamp very small diameter...
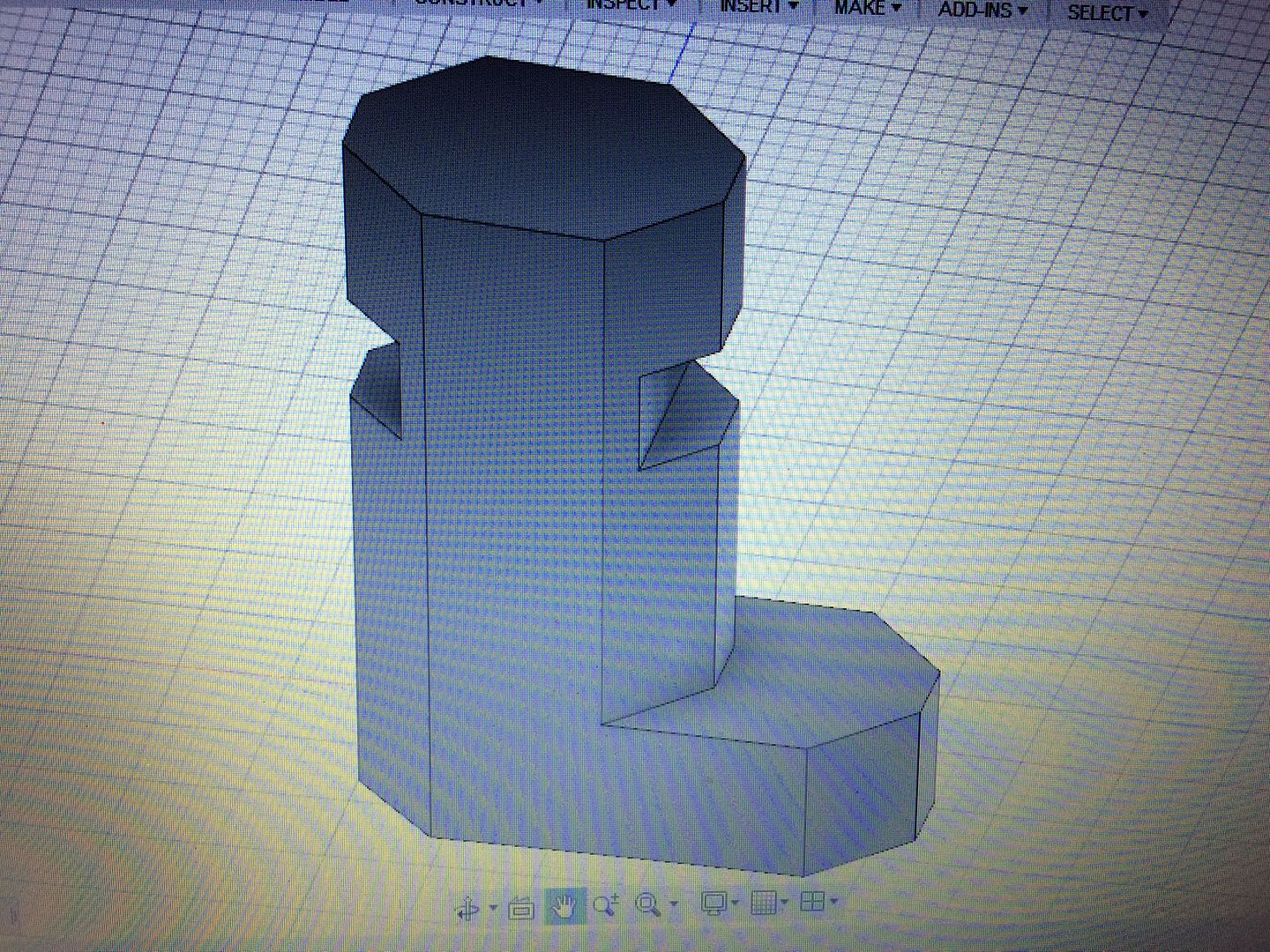
i did not leave the notches in the program, and will be notching it, if i need to, after i clamp a few parts in the chuck and mark exactly where i want the notch...
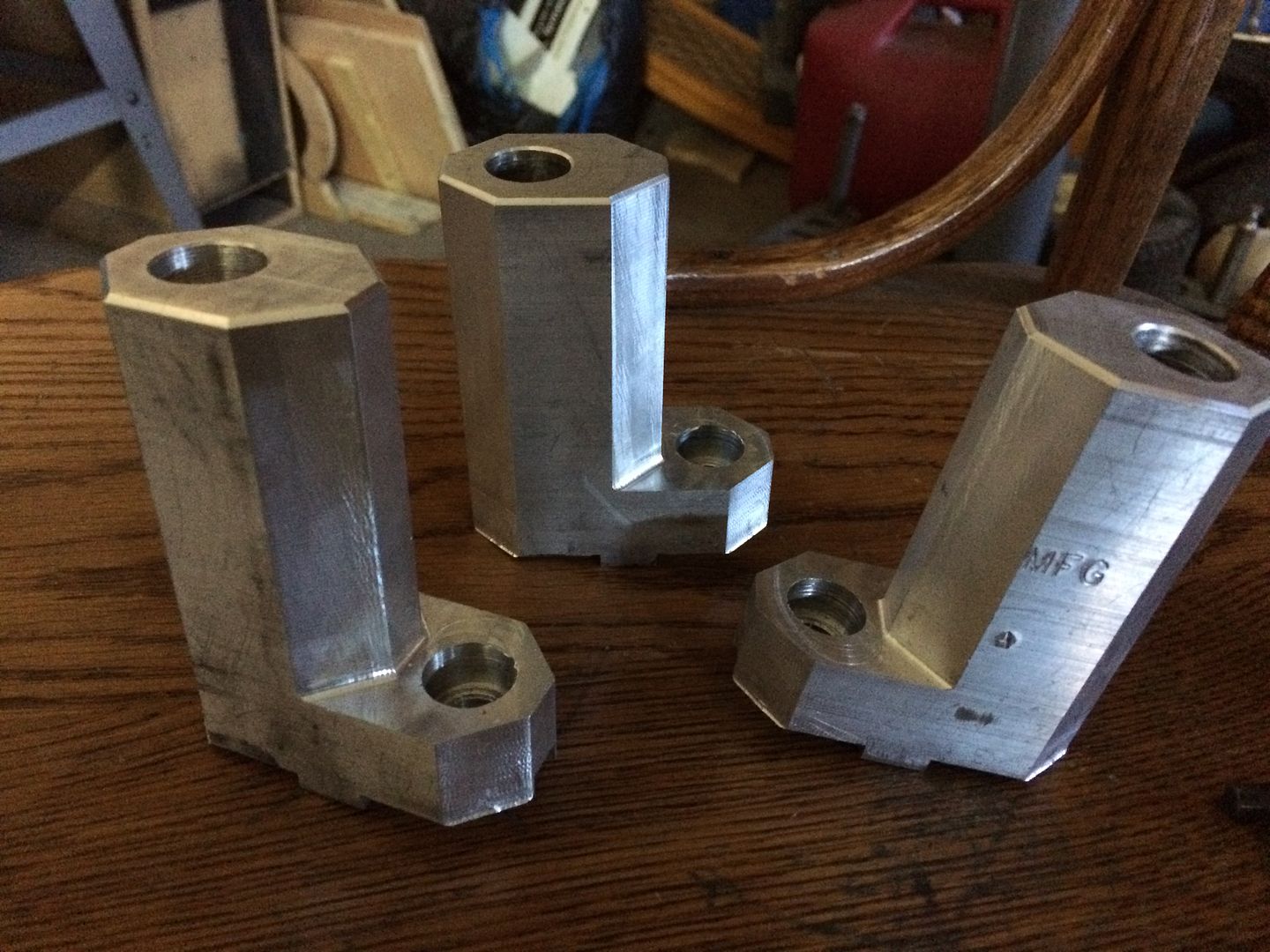
Last edited by LS Customs on Wed Oct 19, 2016 9:43 pm, edited 1 time in total.
LS Customs
- LS Customs
-
Ace
-
Posts:
-
Joined:Tue Feb 23, 2016 11:56 pm
the total cost of the soft jaws, plus machining (with my programming) was approx. $75. but to have something specific to what i am doing and made my way, it was a relatively inexpensive mod...
made a significant difference though... \
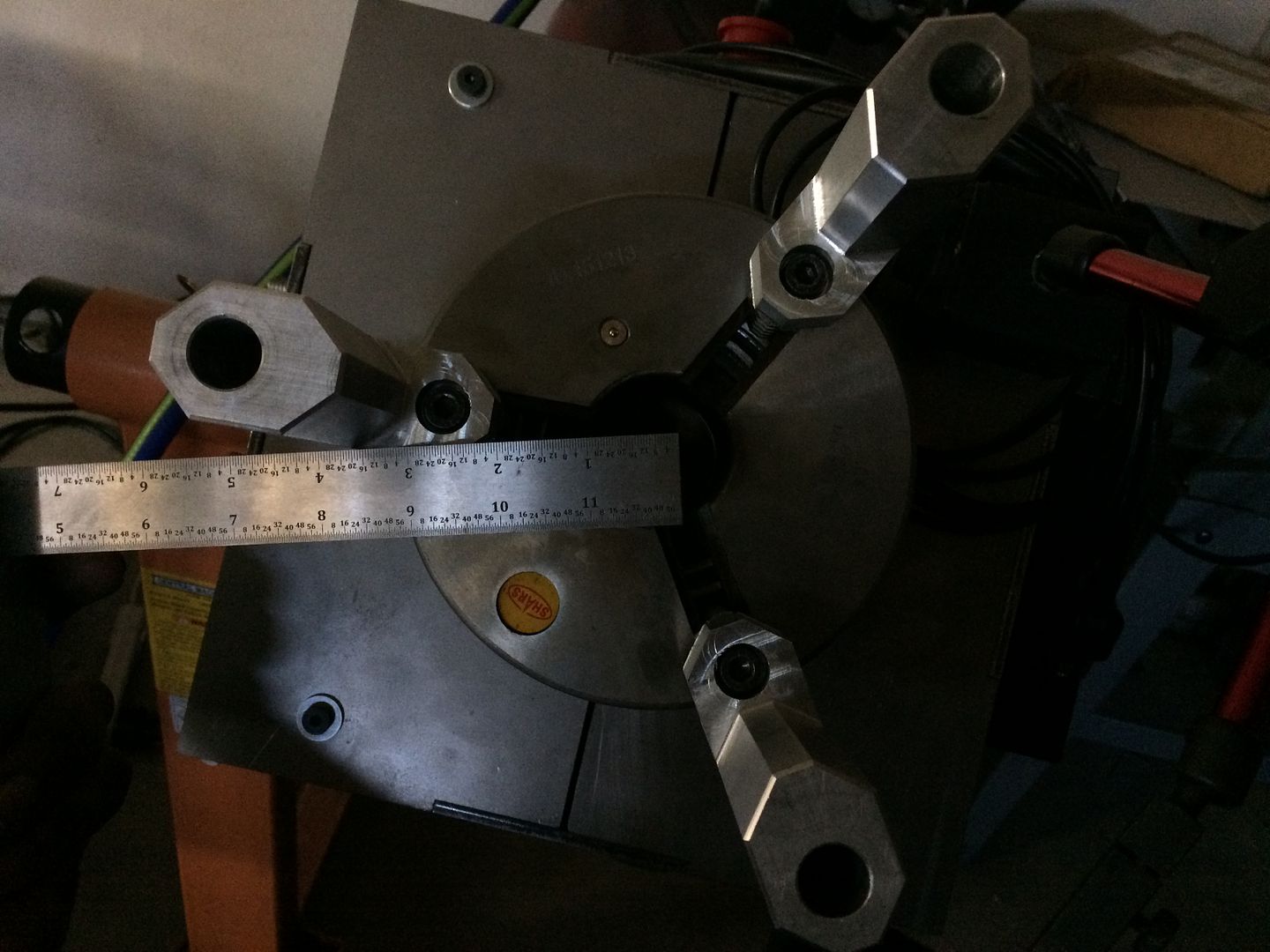
made a significant difference though... \
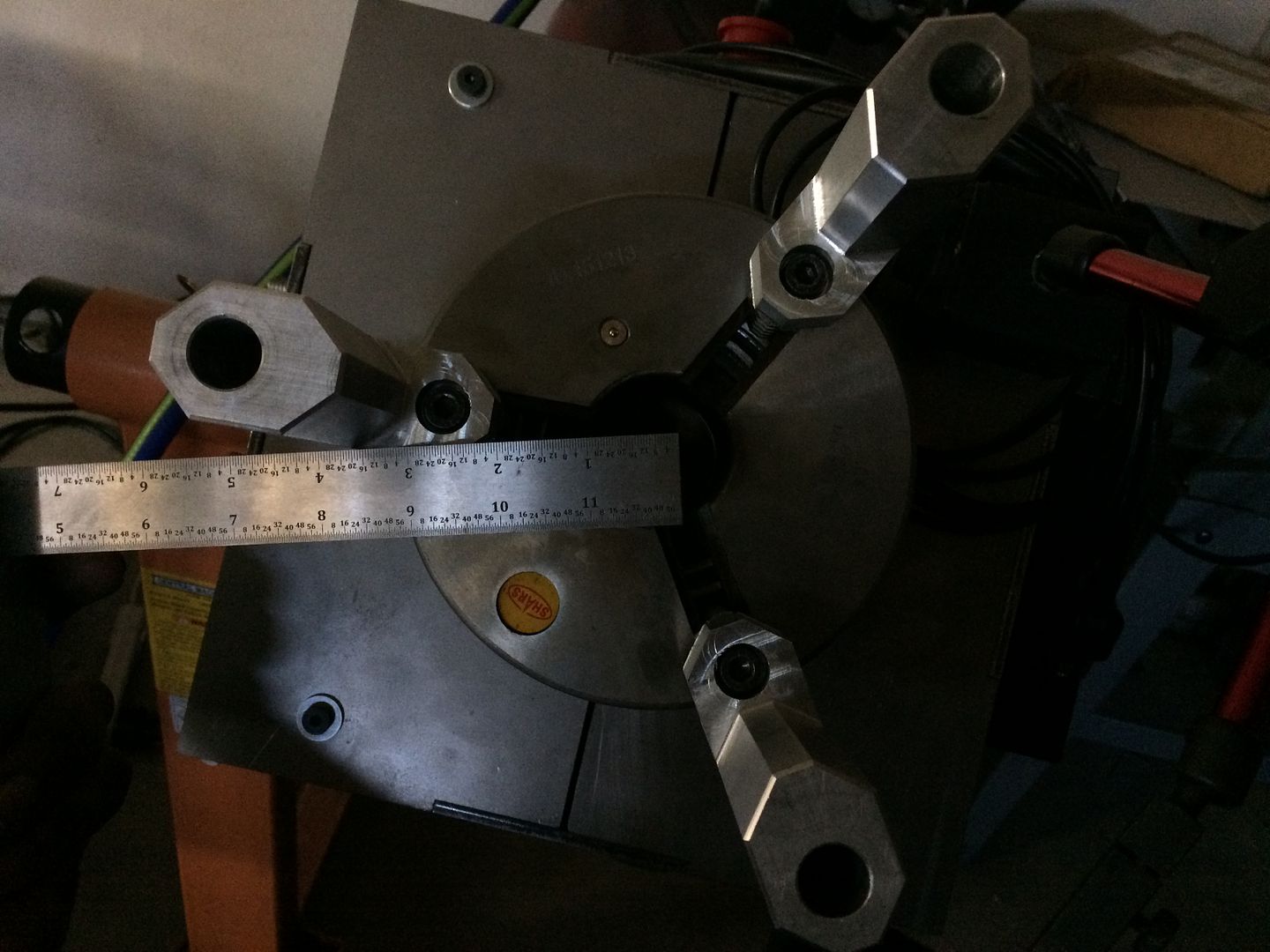
LS Customs
- LS Customs
-
Ace
-
Posts:
-
Joined:Tue Feb 23, 2016 11:56 pm
and this is what i am notching them for... if i am clamping something where the weld isnt completely flat, there will be a small notch so that the part fits in the chuck and runs pretty true, without the extra time it takes to set it up straight without the notches..
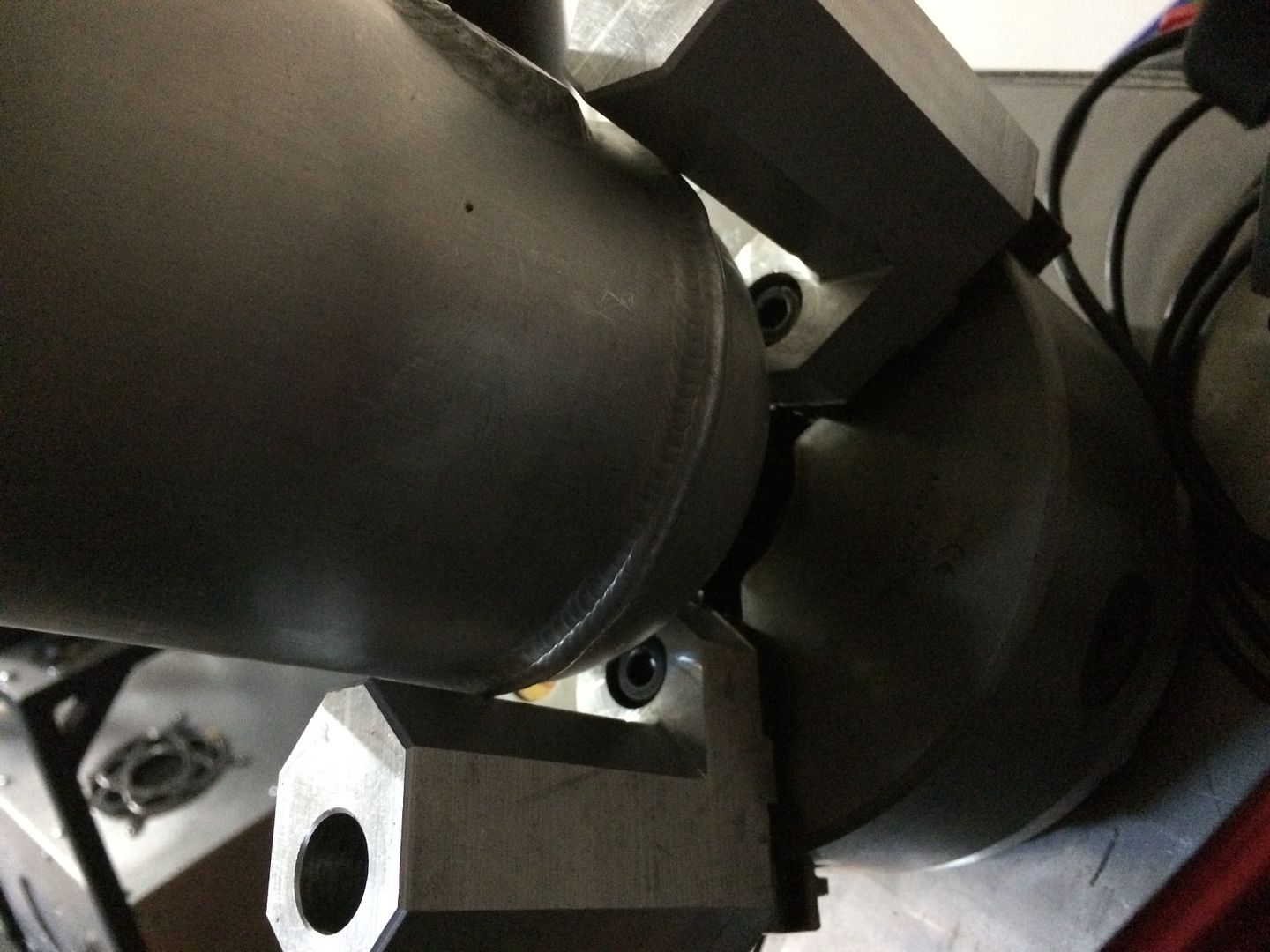
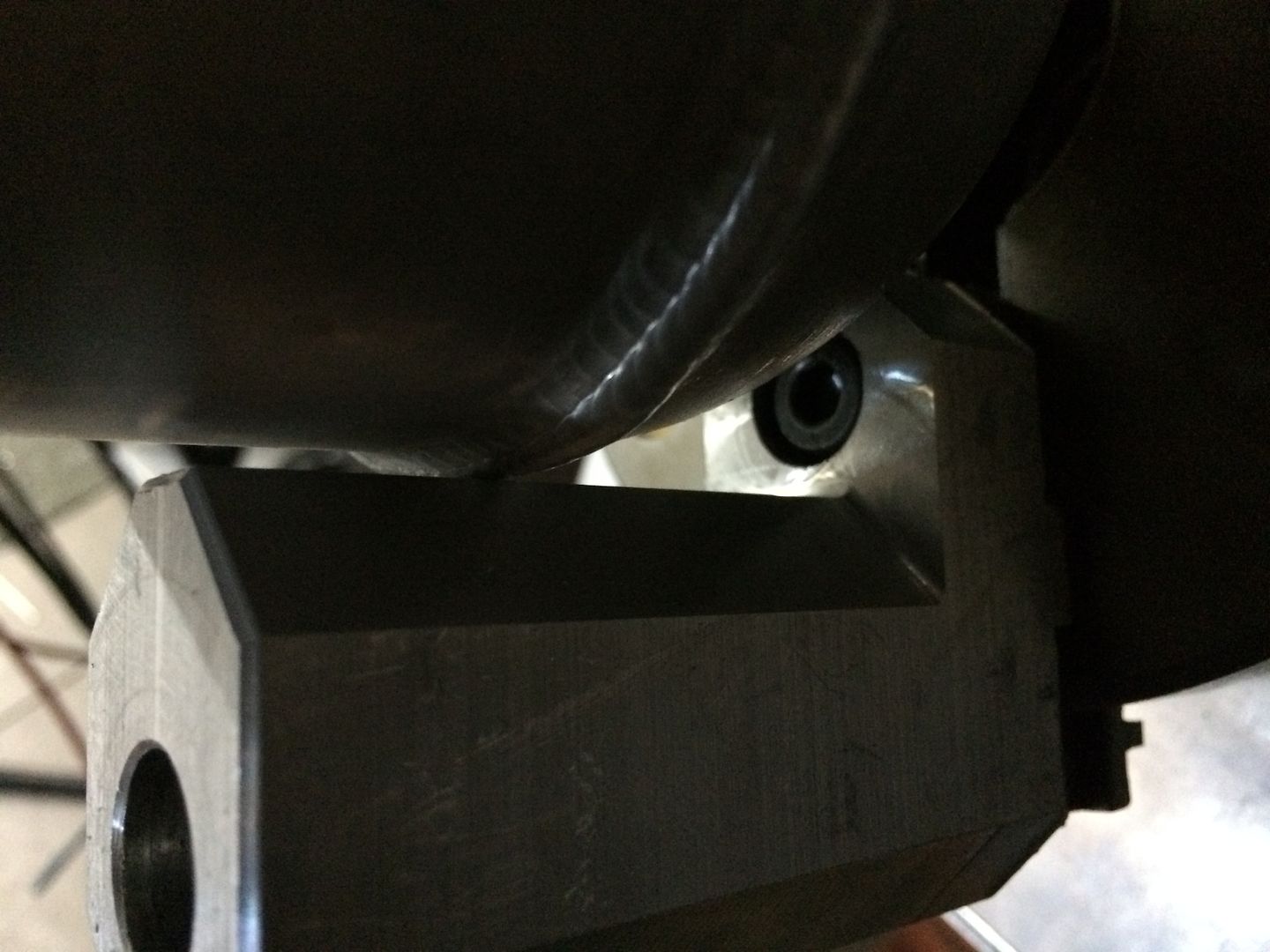
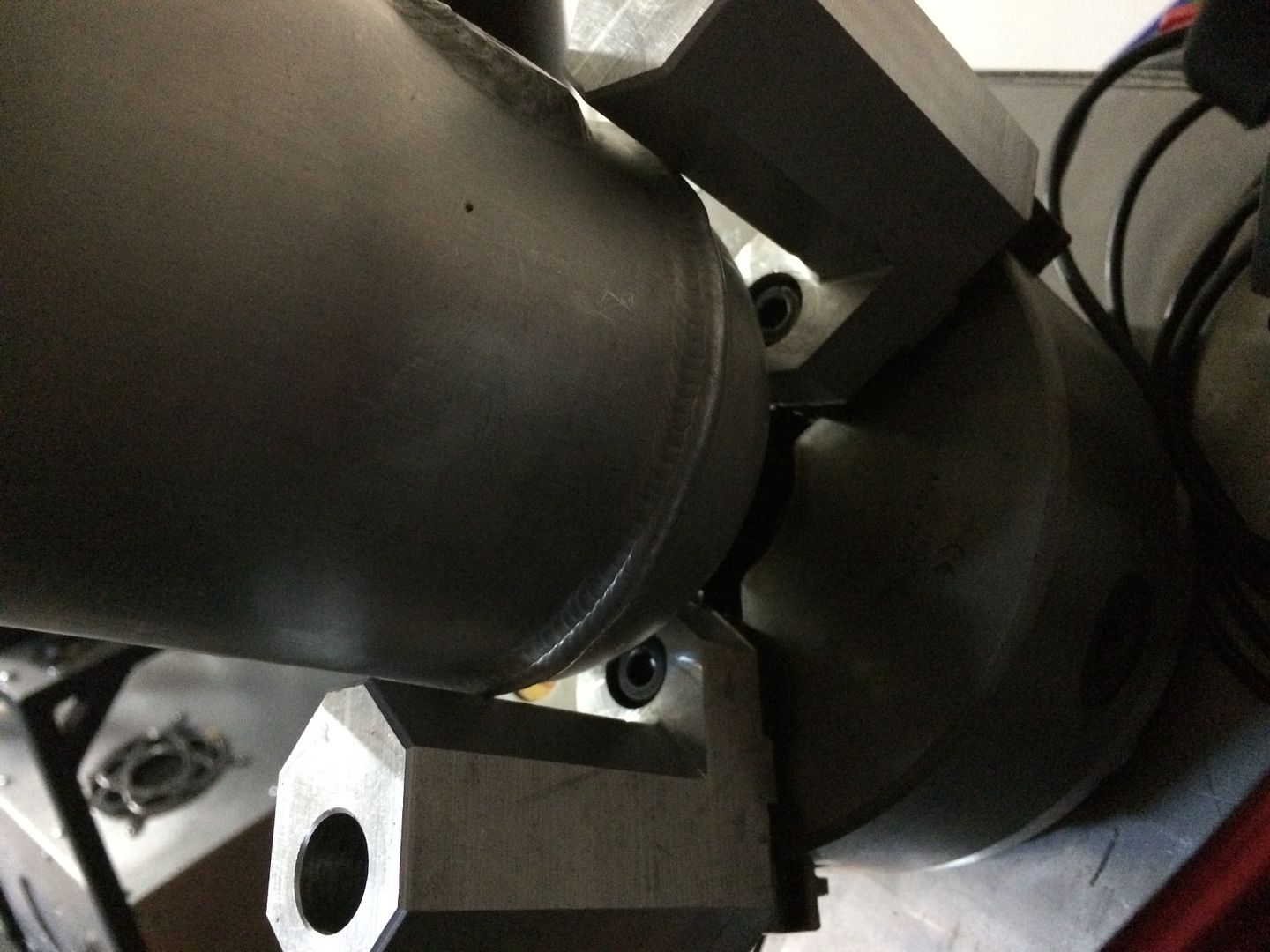
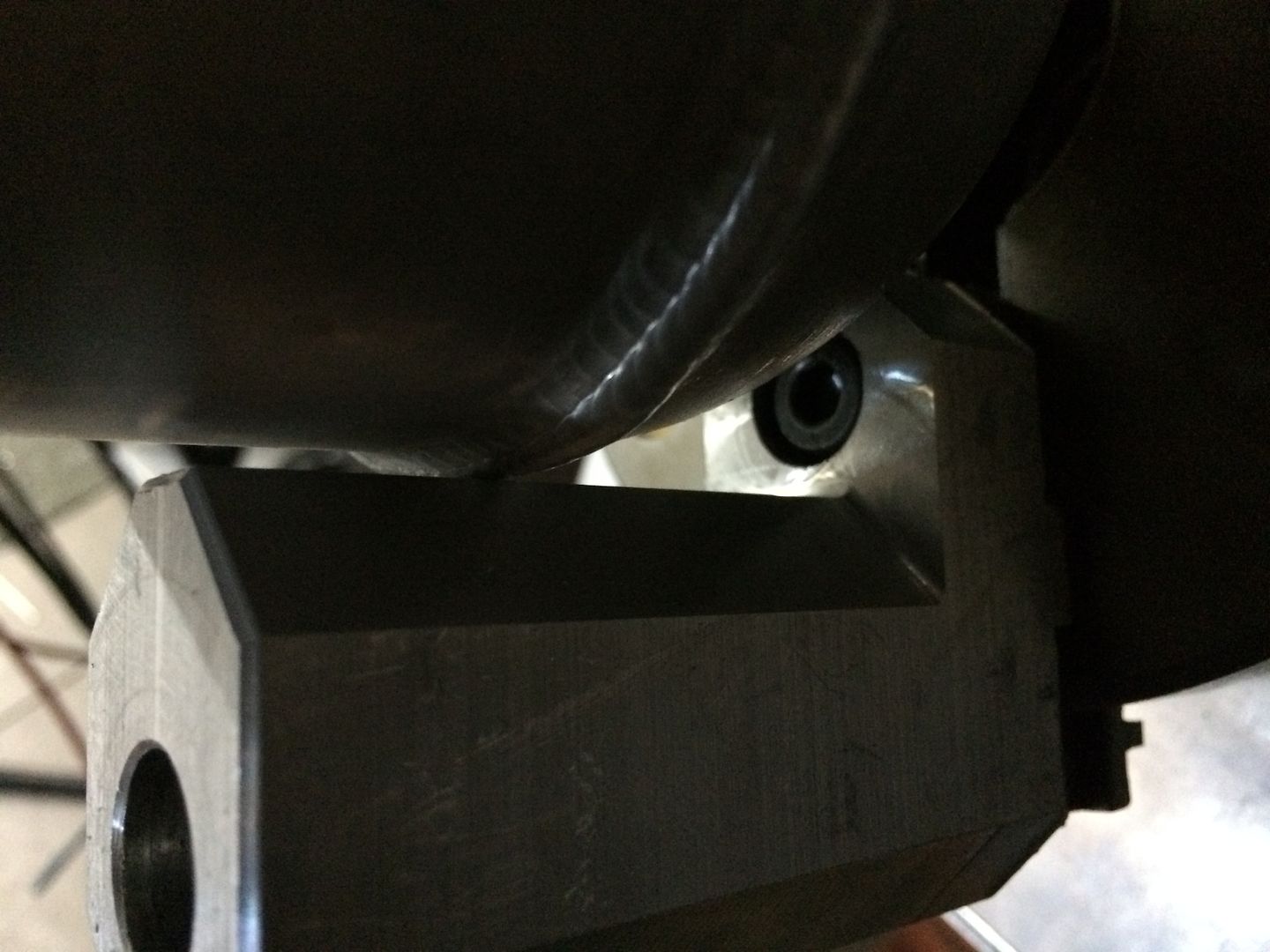
LS Customs
- LS Customs
-
Ace
-
Posts:
-
Joined:Tue Feb 23, 2016 11:56 pm
I designed, programmed in cad, some end caps, and filler cap and bungs, (and had my machinist run the programs on his cnc) to give the setup a good consistent run and i hope i can sell some of these tanks, on ebay and facebook, and help to pay for some materials to keep the practice going...
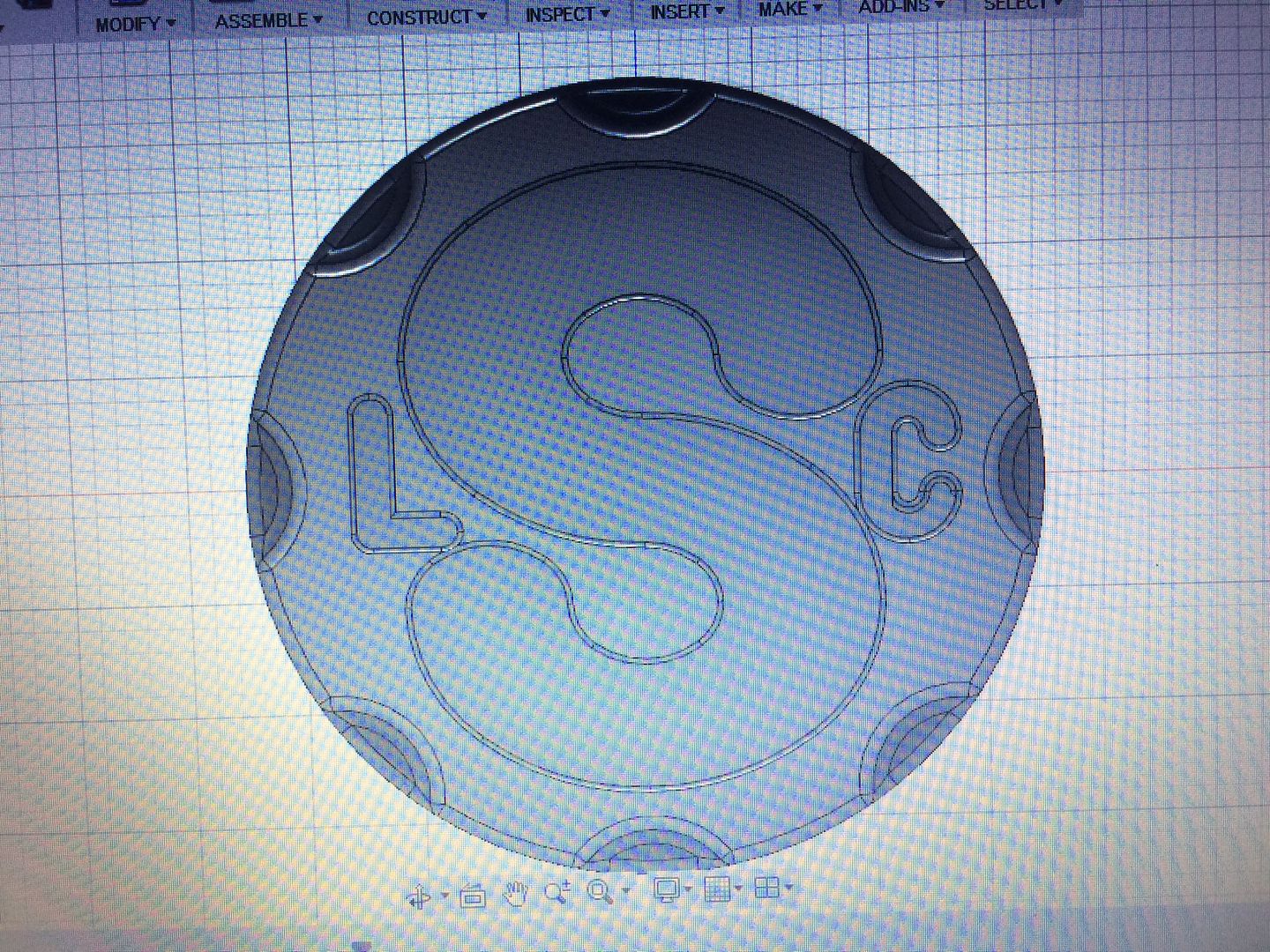
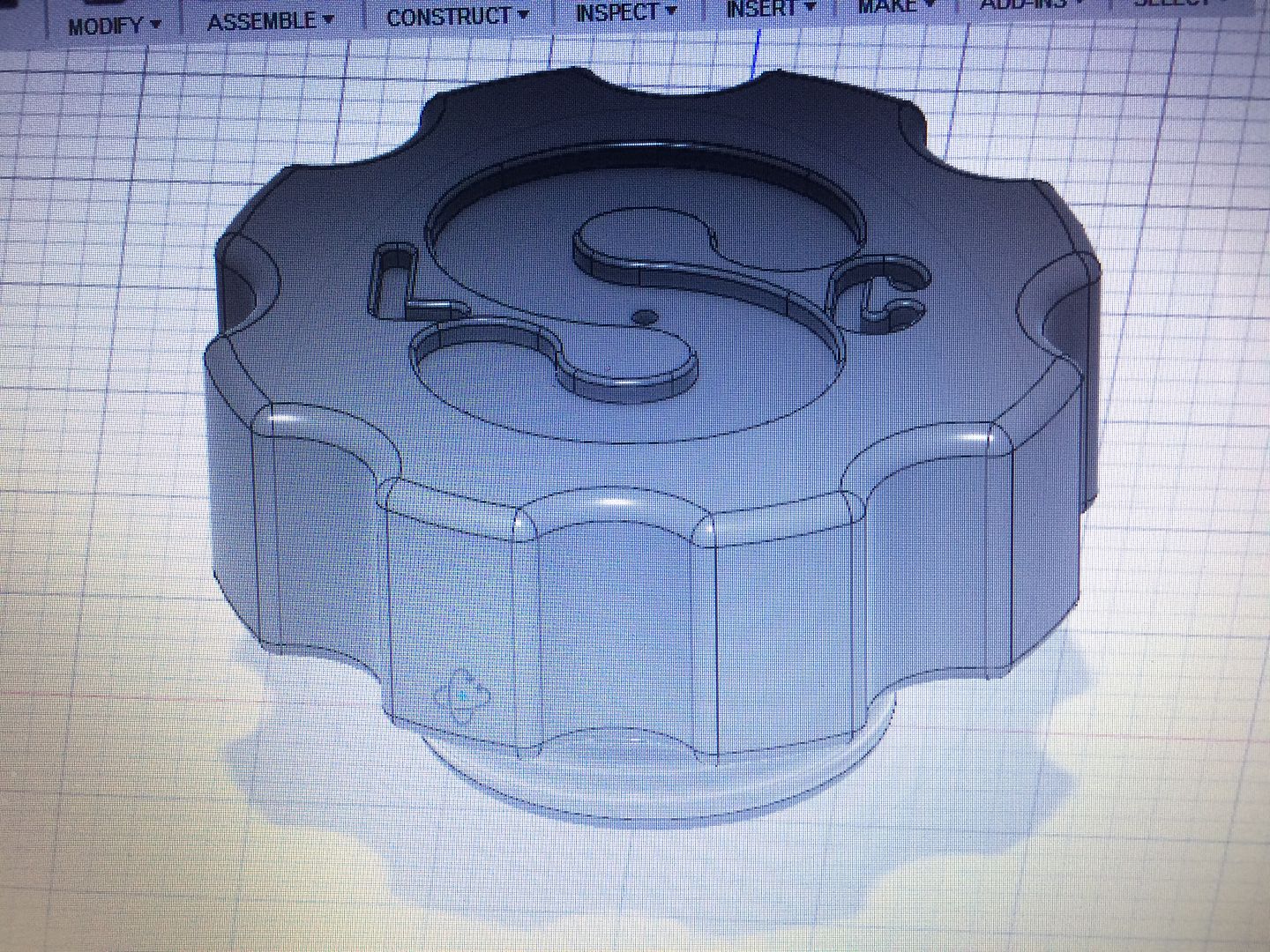
i programmed the cap to be a small vent through the top... but fit a filter (1/8' npt) on the bottom to help prevent any vacuum issues with gas coming out the vent... grabbed the small vents from mcmaster car
[/quote]
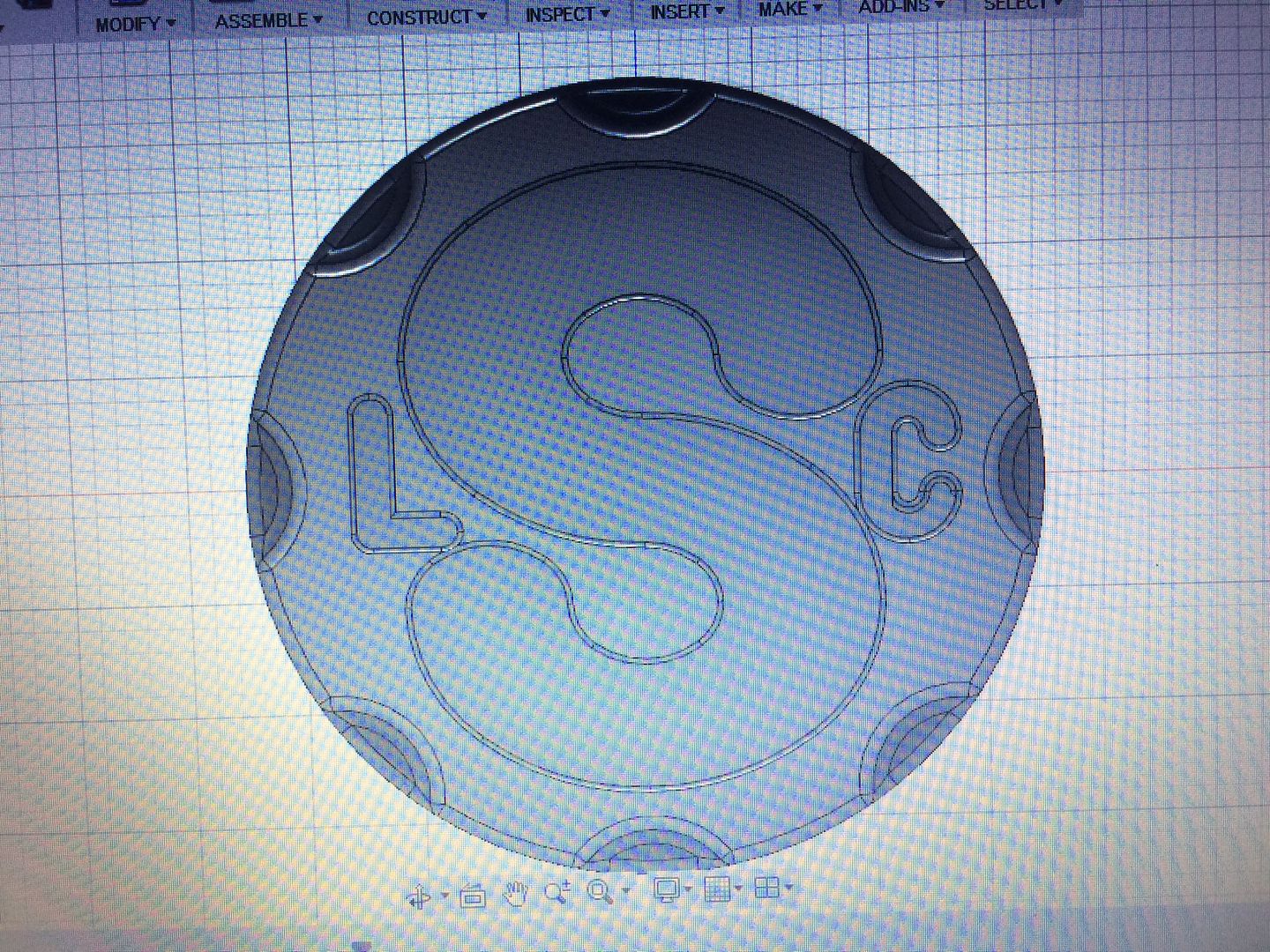
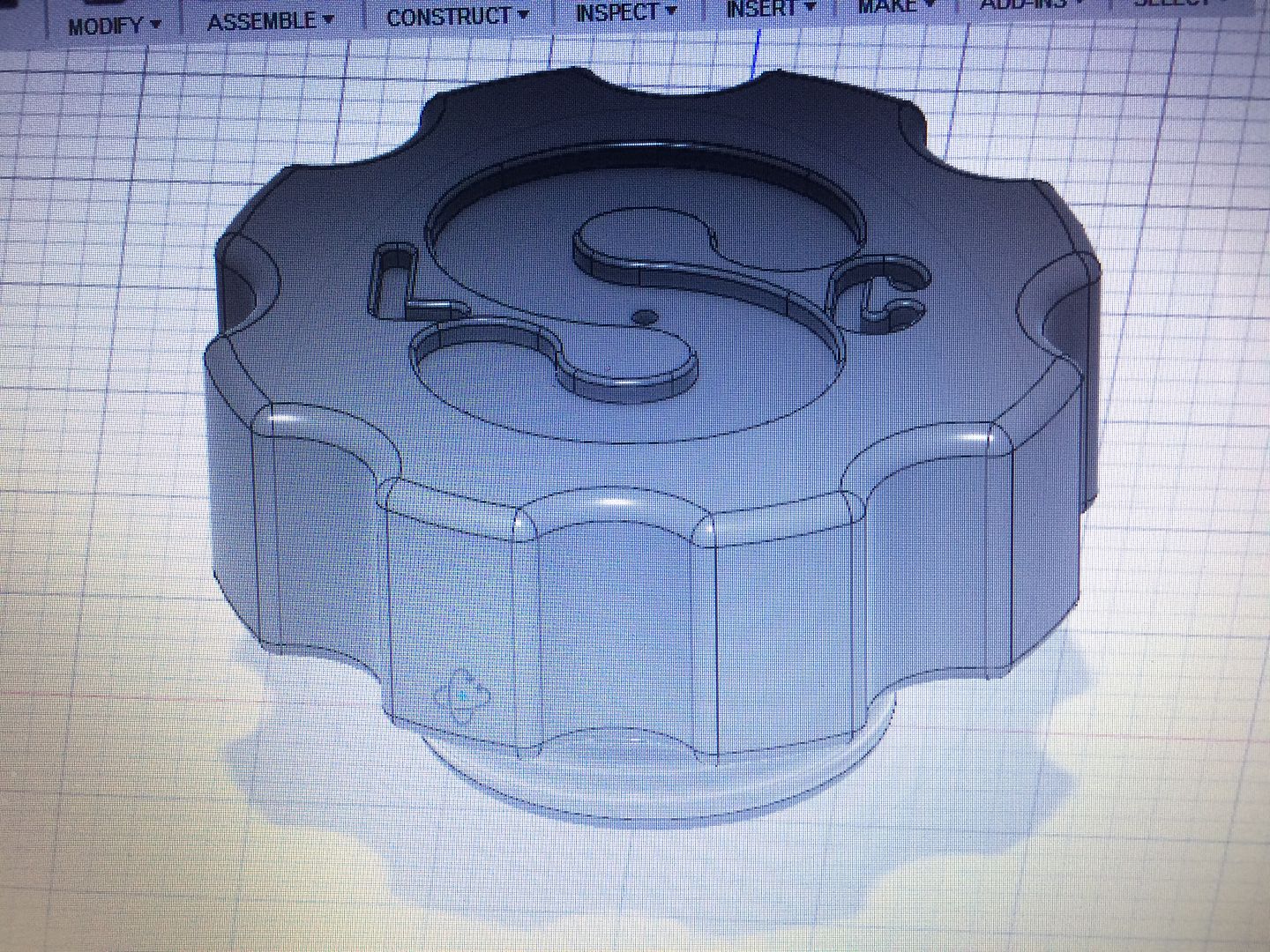
i programmed the cap to be a small vent through the top... but fit a filter (1/8' npt) on the bottom to help prevent any vacuum issues with gas coming out the vent... grabbed the small vents from mcmaster car
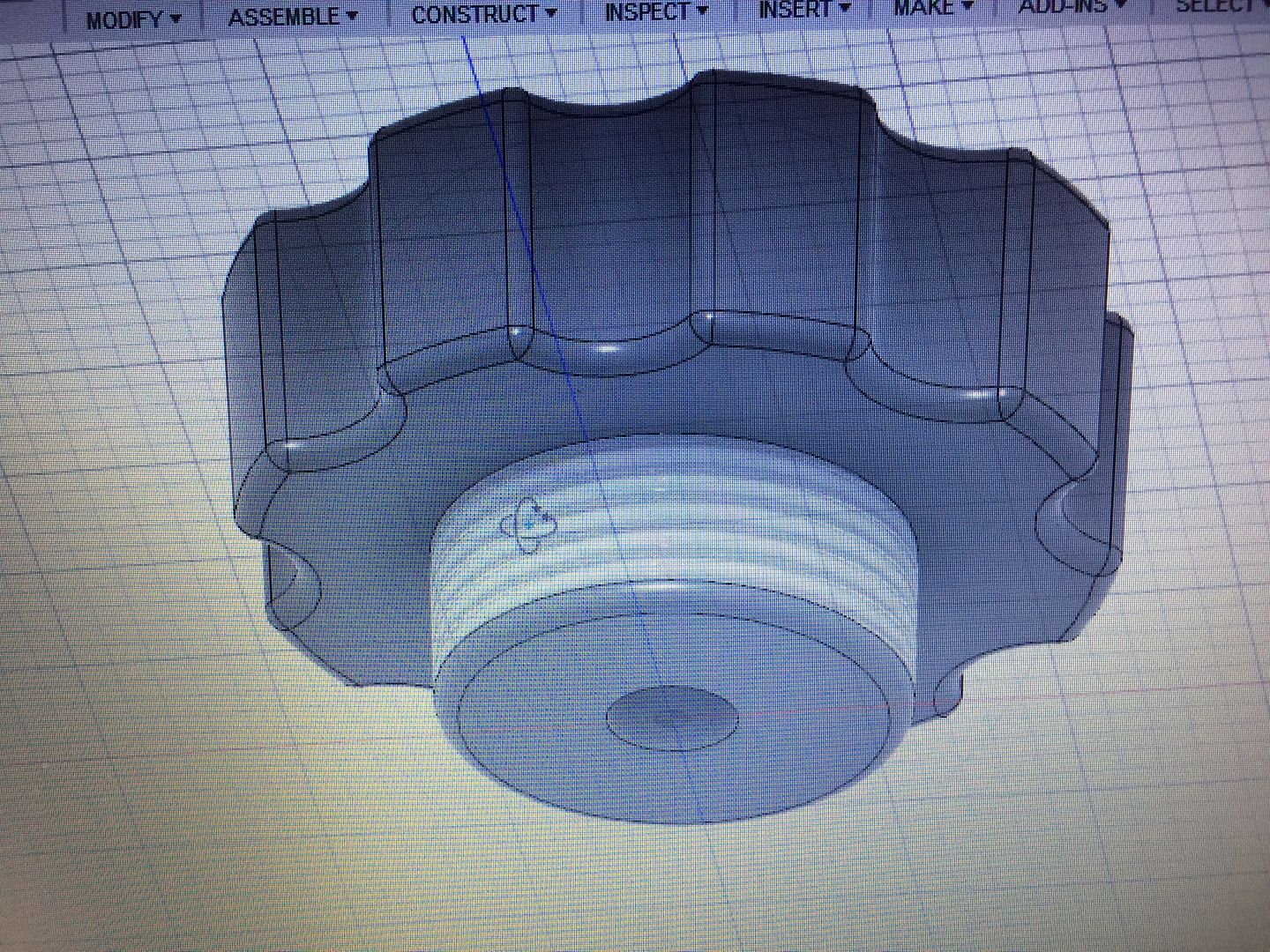
LS Customs
- LS Customs
-
Ace
-
Posts:
-
Joined:Tue Feb 23, 2016 11:56 pm
I welded up the first one... I do not use the pulse feature, which may make rhythm a little easier to get down initially, but the point for me is to keep getting better feeding the wire and controlling the welder without any of the extra features of a welder in a sense... each time it sit down, i do seem to get more comfy with it... the better i get, i will play with the functions of the positioner's controller and play with pulse and maybe try to make a cold wire feeder, to be used with the positioner, when im using it.. but for now, i want to practice tig welding and dipping the rod, etc by hand... i am not using the tig pen either.. havent sense after the first day it arrived... for me its easier to just feed by hand...
my modified soft jaws work perfect... was ann affordable way to make this chuck more versatile...
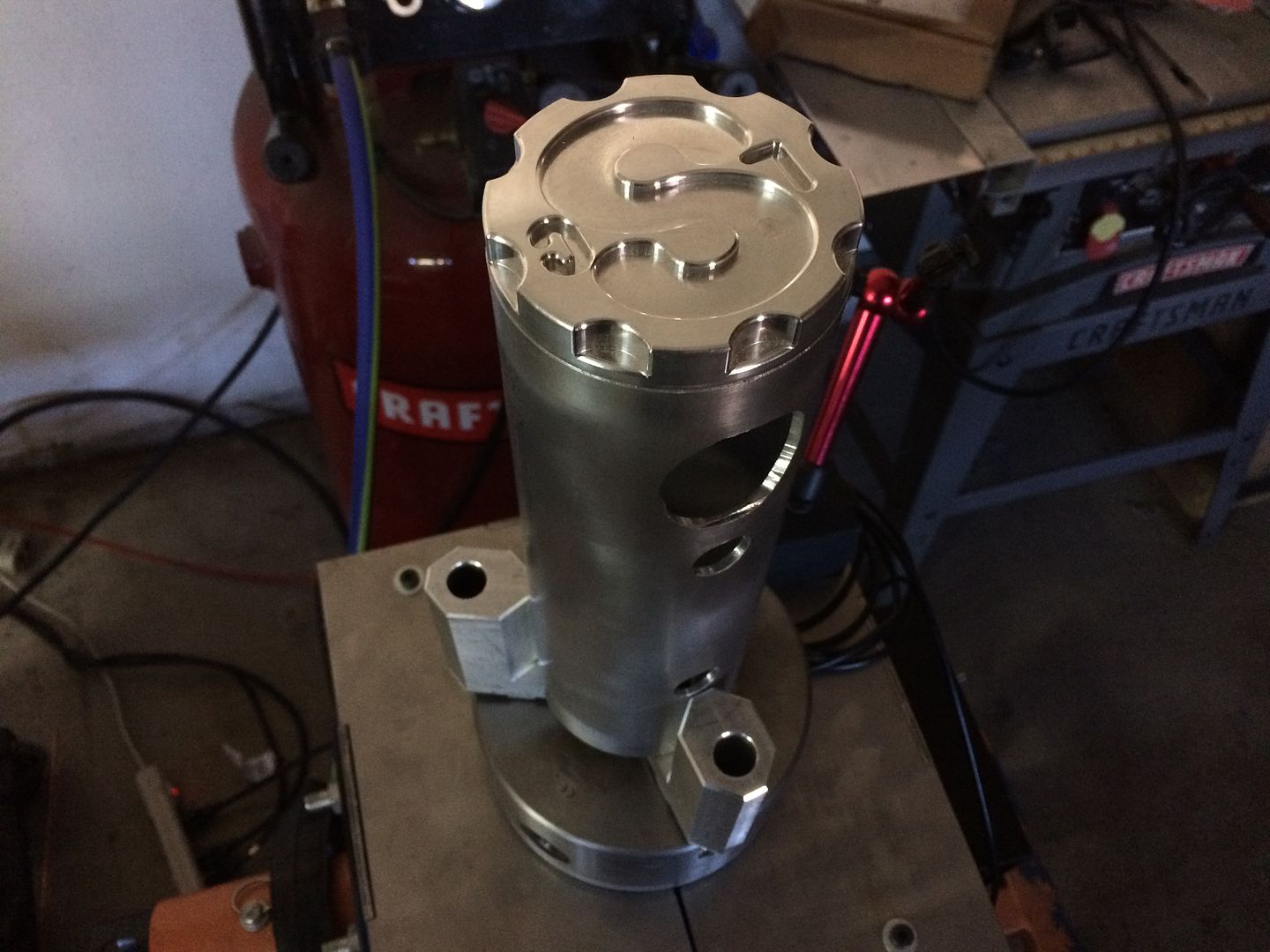
first end cap down...
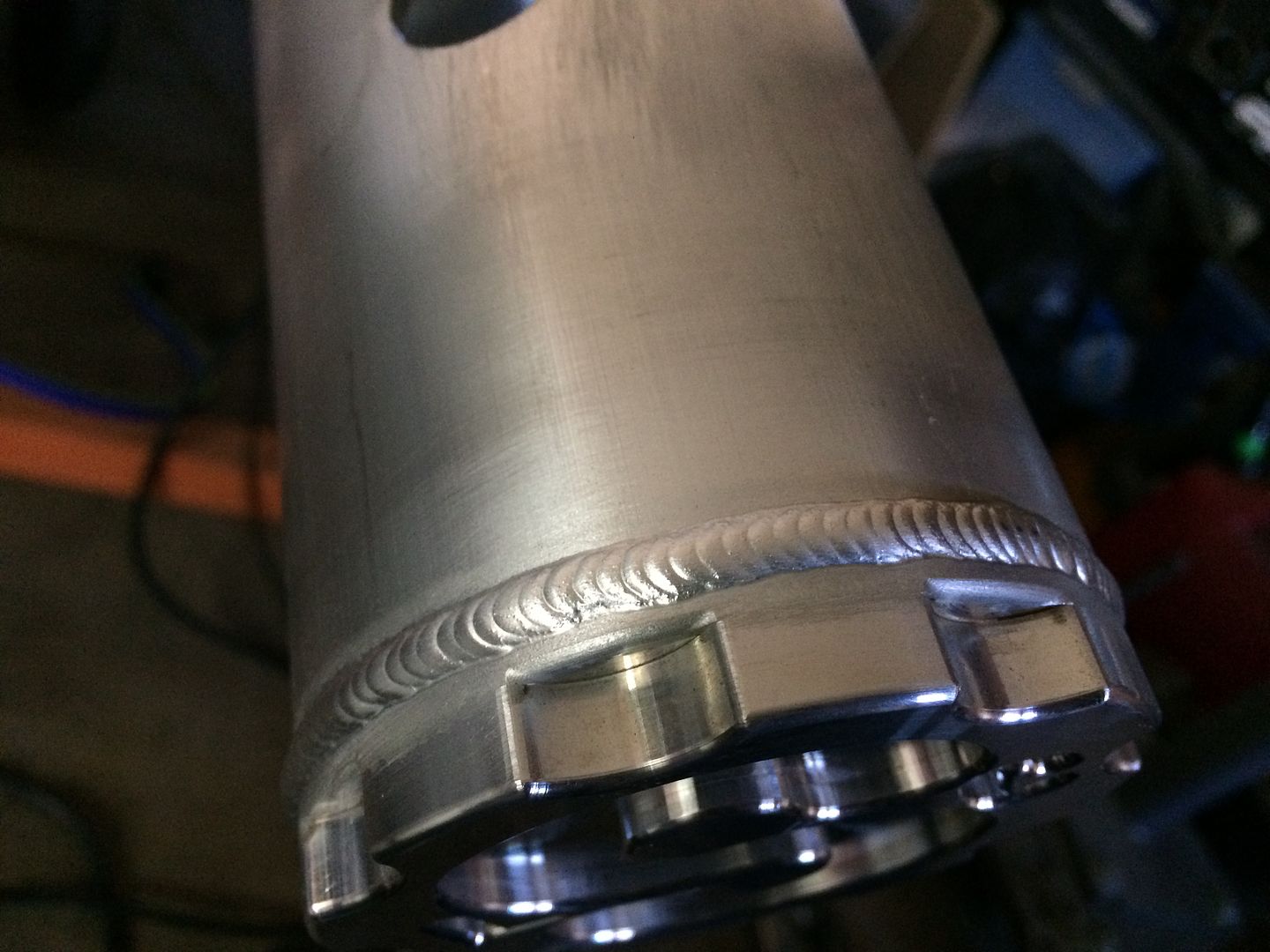
my modified soft jaws work perfect... was ann affordable way to make this chuck more versatile...
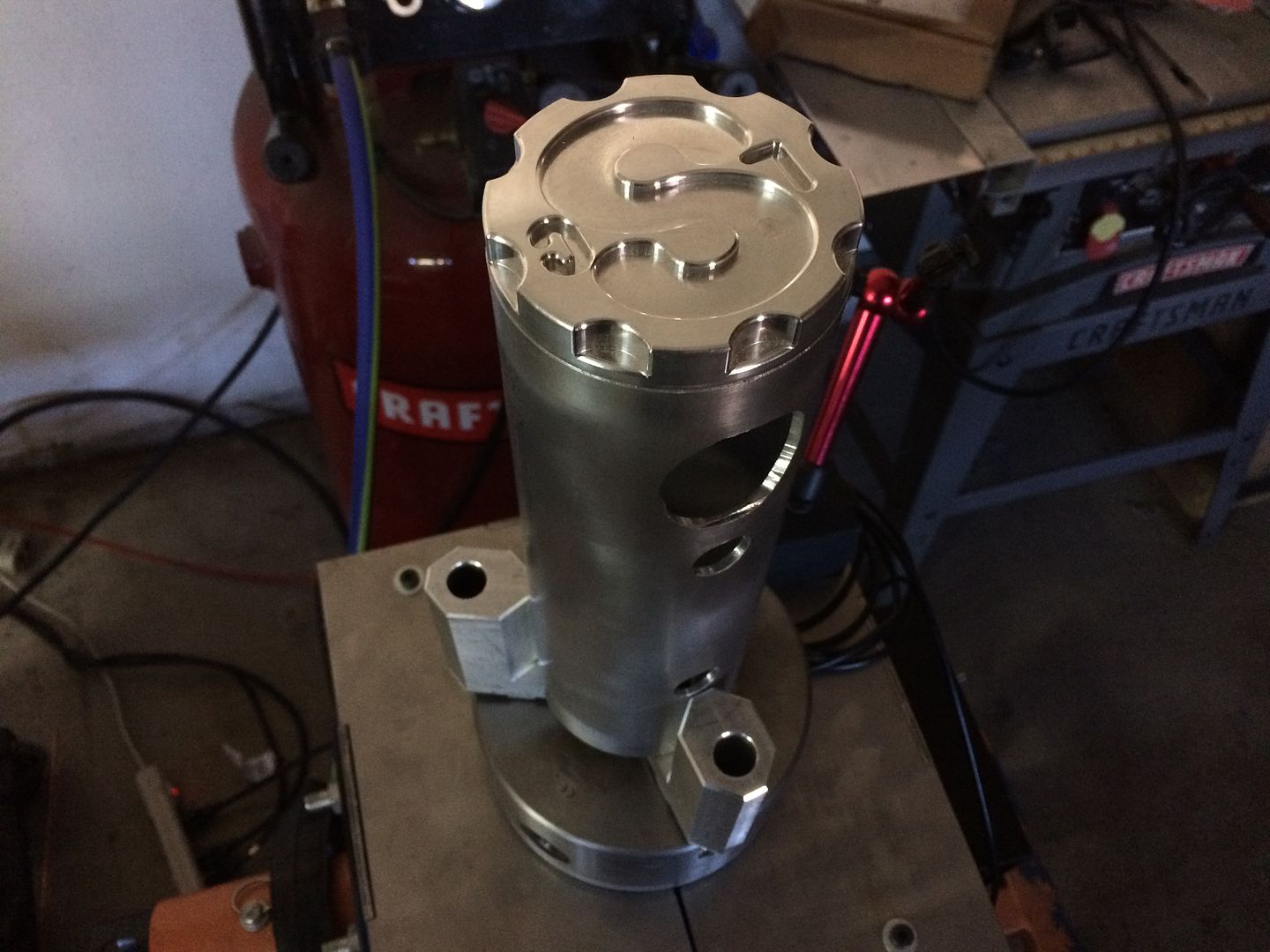
first end cap down...
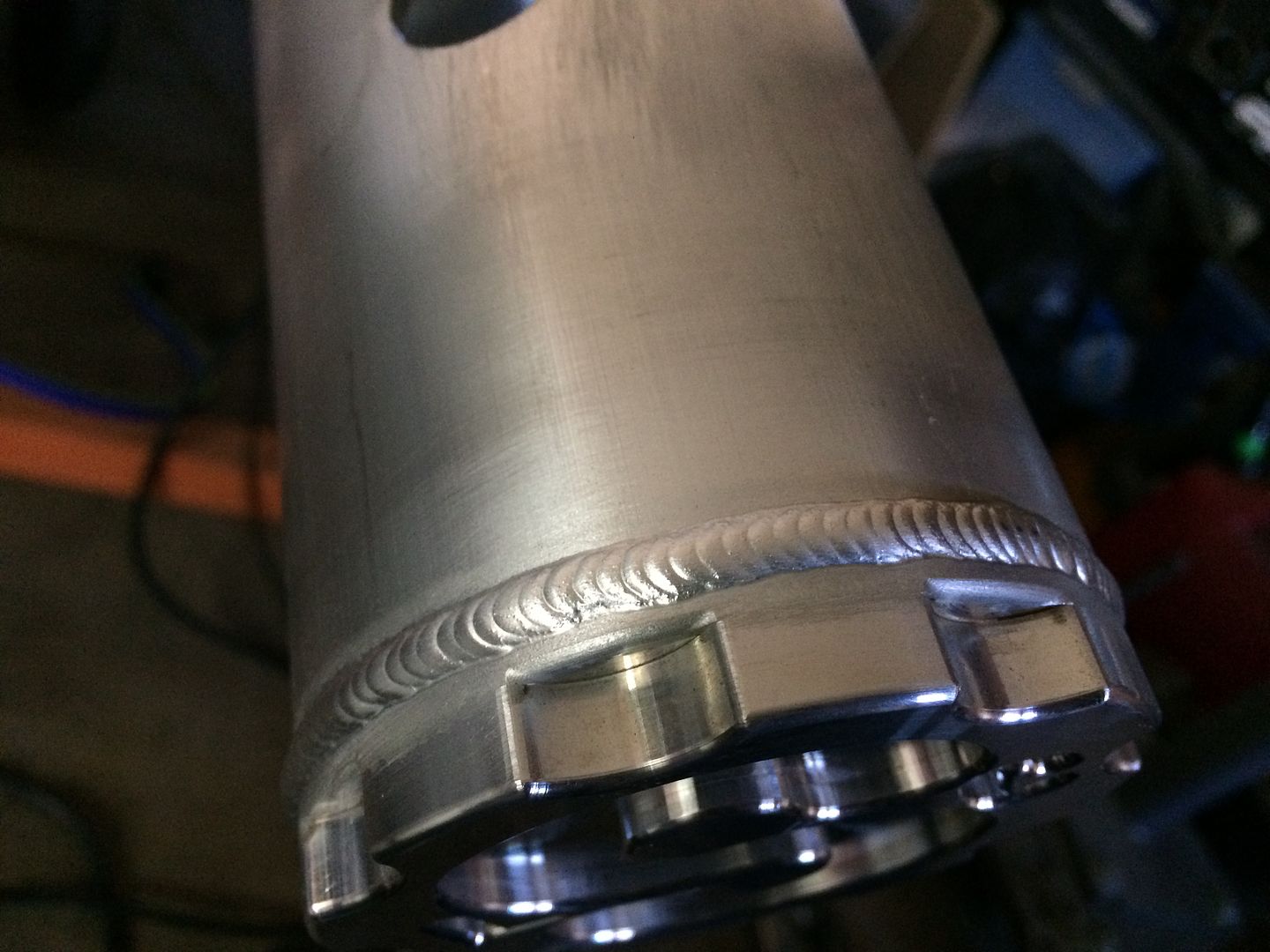
LS Customs
- LS Customs
-
Ace
-
Posts:
-
Joined:Tue Feb 23, 2016 11:56 pm
i wanted to weld something smaller diameter on the positioner, so as opposed to welding the bung for the cap directly to the cylinder, i added a short filler neck... this is all 1/8" thick 6061 tubing...
i unbolted the jaw and reversed it... and this is the third weld, after welding the two end caps, i was even more comfortable with the coordination between the rotation of the positioner, pedal control and dipping the rod... I also paid close attention to the puddle and watched the puddle start to sink/little eye open up and dipped the rod, as this would happen to help ensure correct fusion...
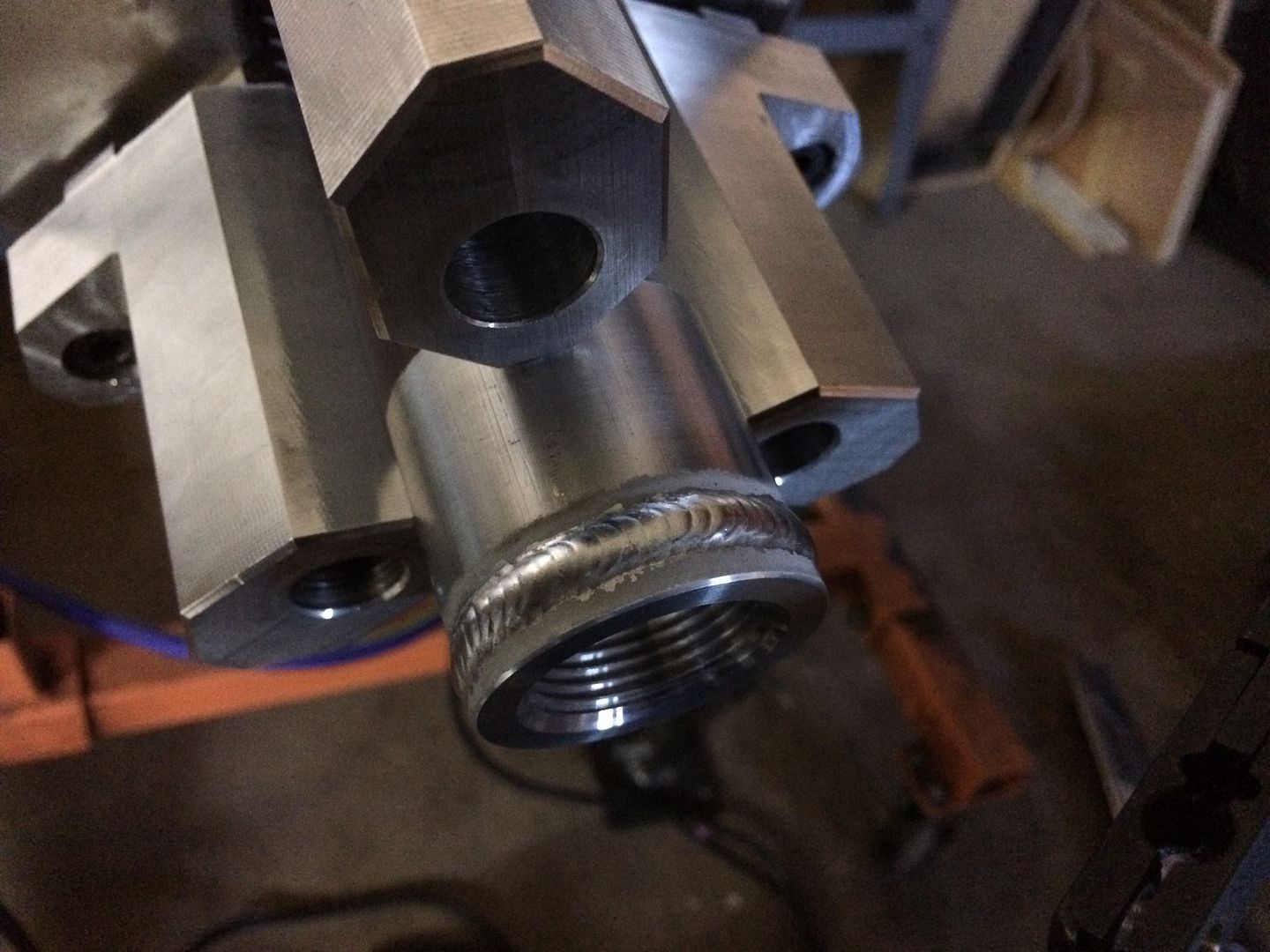
i unbolted the jaw and reversed it... and this is the third weld, after welding the two end caps, i was even more comfortable with the coordination between the rotation of the positioner, pedal control and dipping the rod... I also paid close attention to the puddle and watched the puddle start to sink/little eye open up and dipped the rod, as this would happen to help ensure correct fusion...
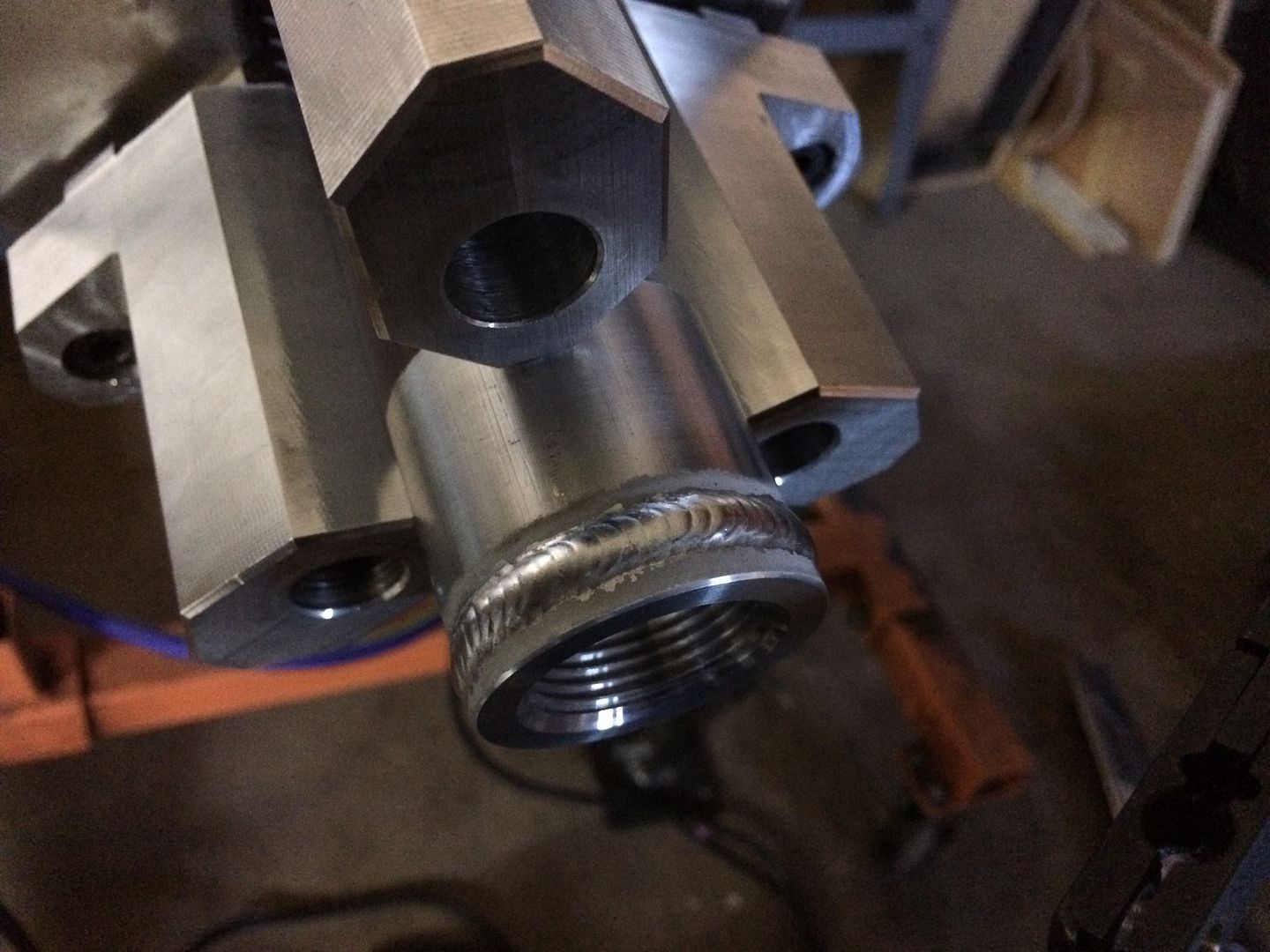
LS Customs
- LS Customs
-
Ace
-
Posts:
-
Joined:Tue Feb 23, 2016 11:56 pm
while on the positioner, it also helped to weld all the other bungs onto the tank, in this case. 1/4" NPT on bottom, and two blind bungs on the top... was able to positioner them and hold them nicely at certain angles to help get around those little fittings
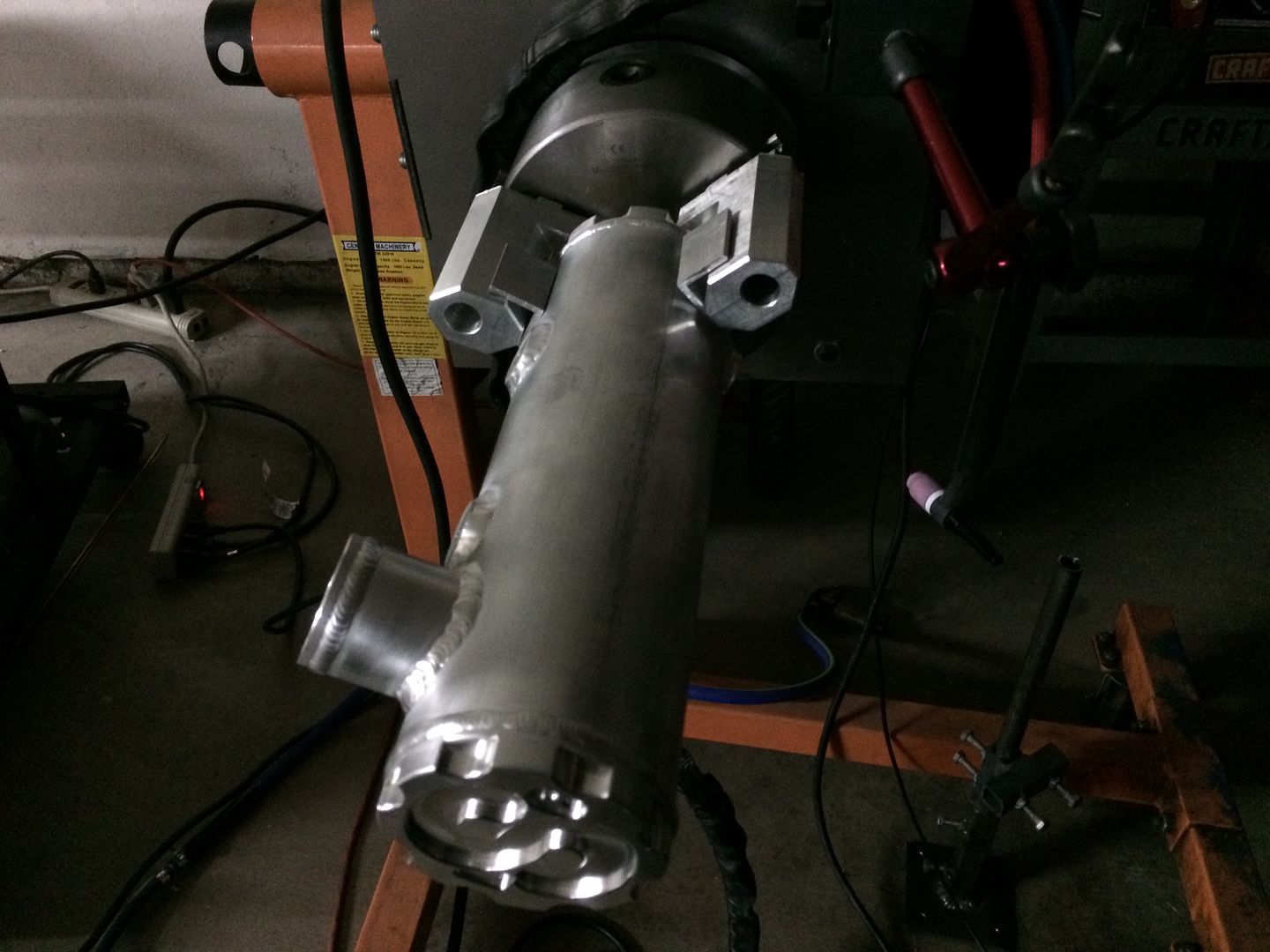
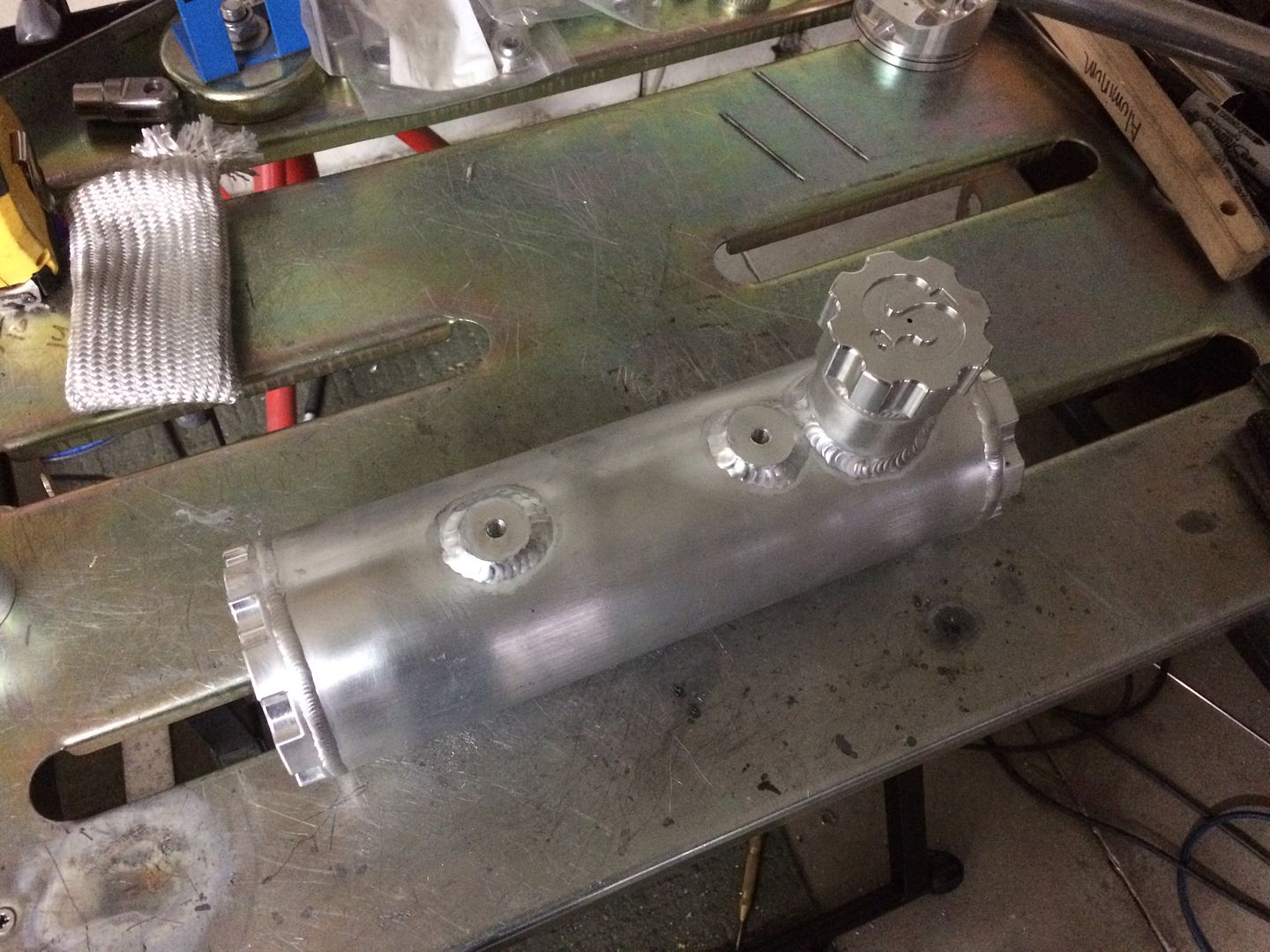
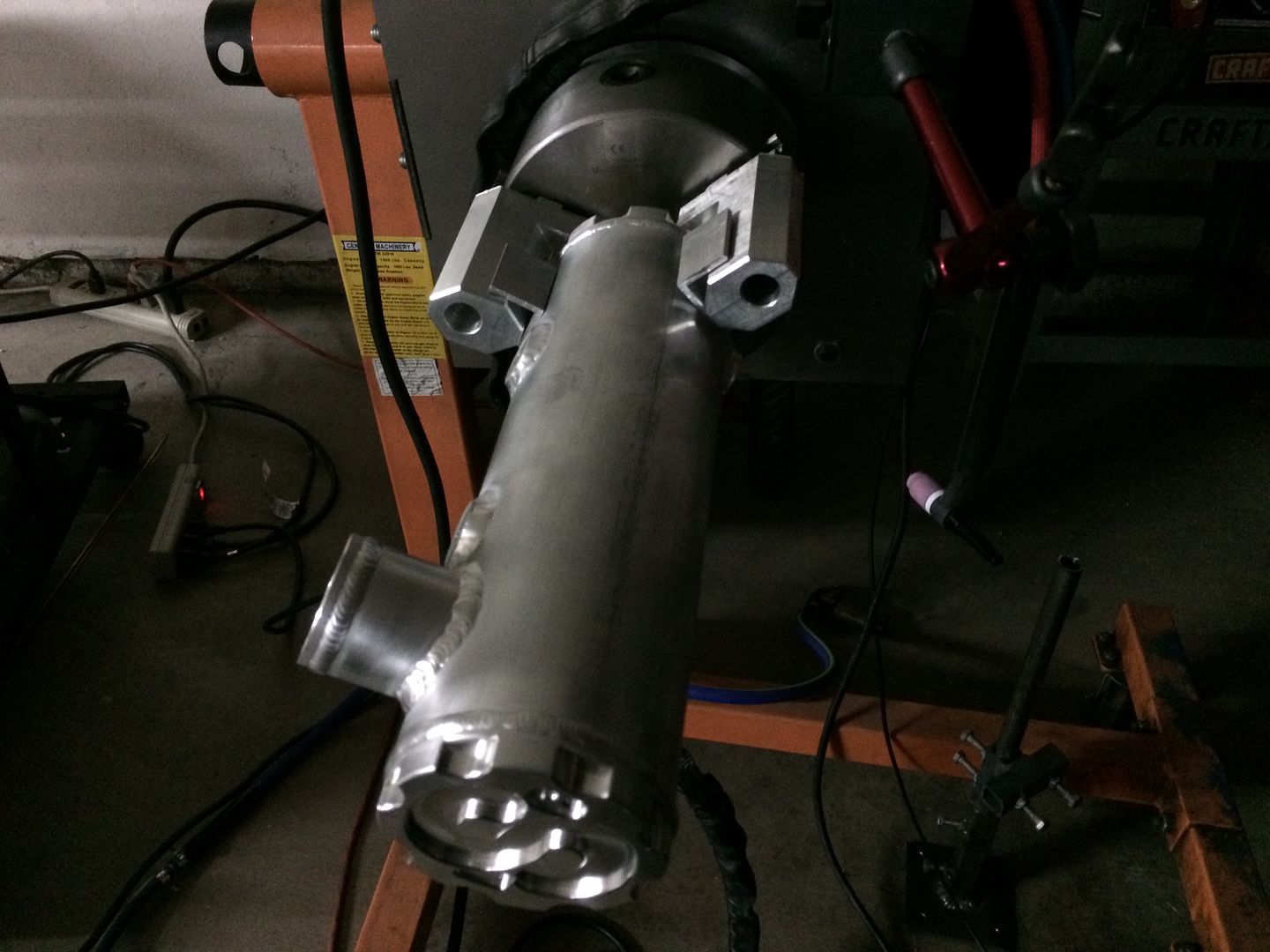
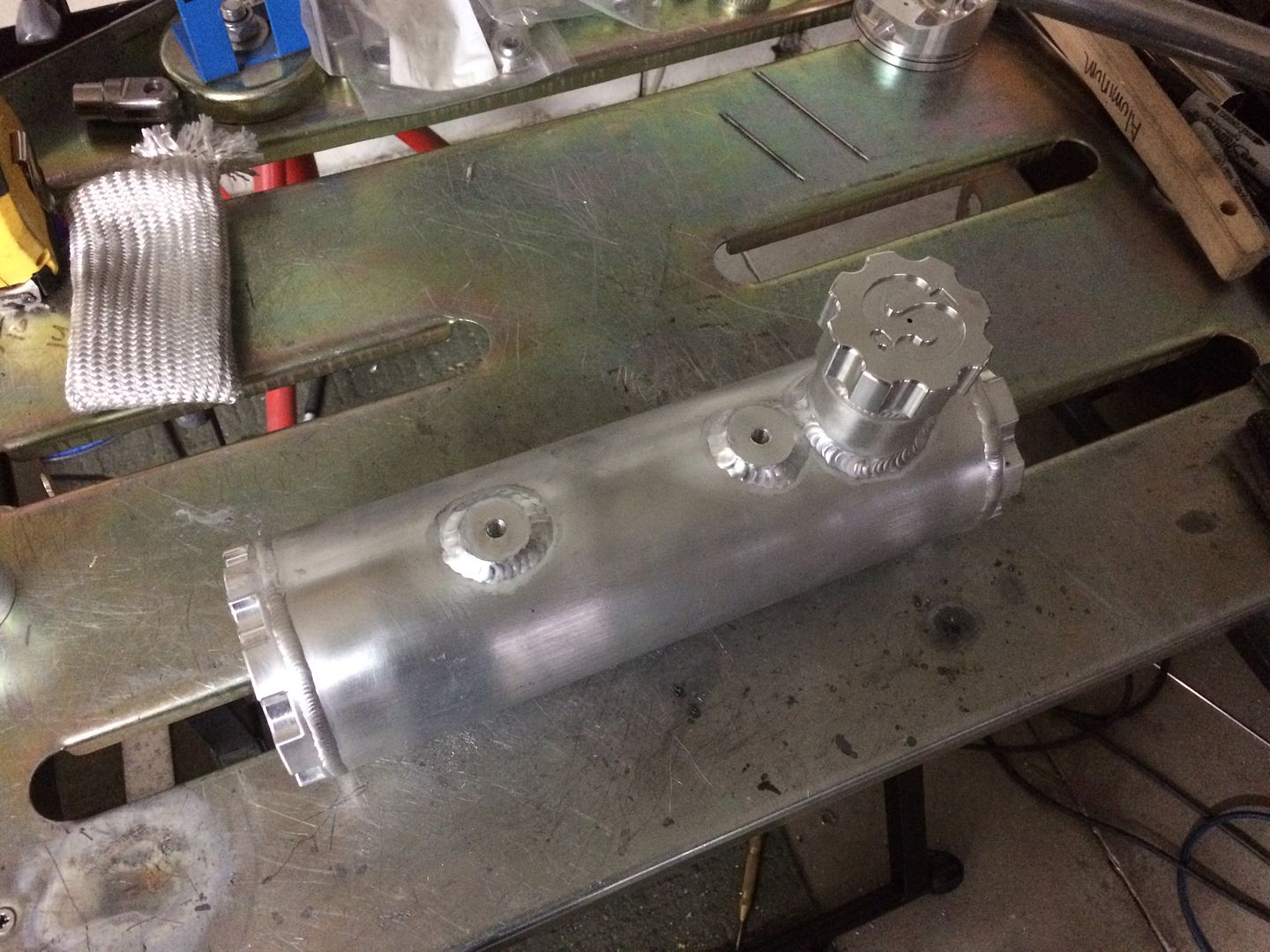
LS Customs
- LS Customs
-
Ace
-
Posts:
-
Joined:Tue Feb 23, 2016 11:56 pm
still working nicely... i dont use pulse... after welding with this for a little bit i am very comfy welding with both hands and feeding rod at a fast consistent pace... gotta keep at it..
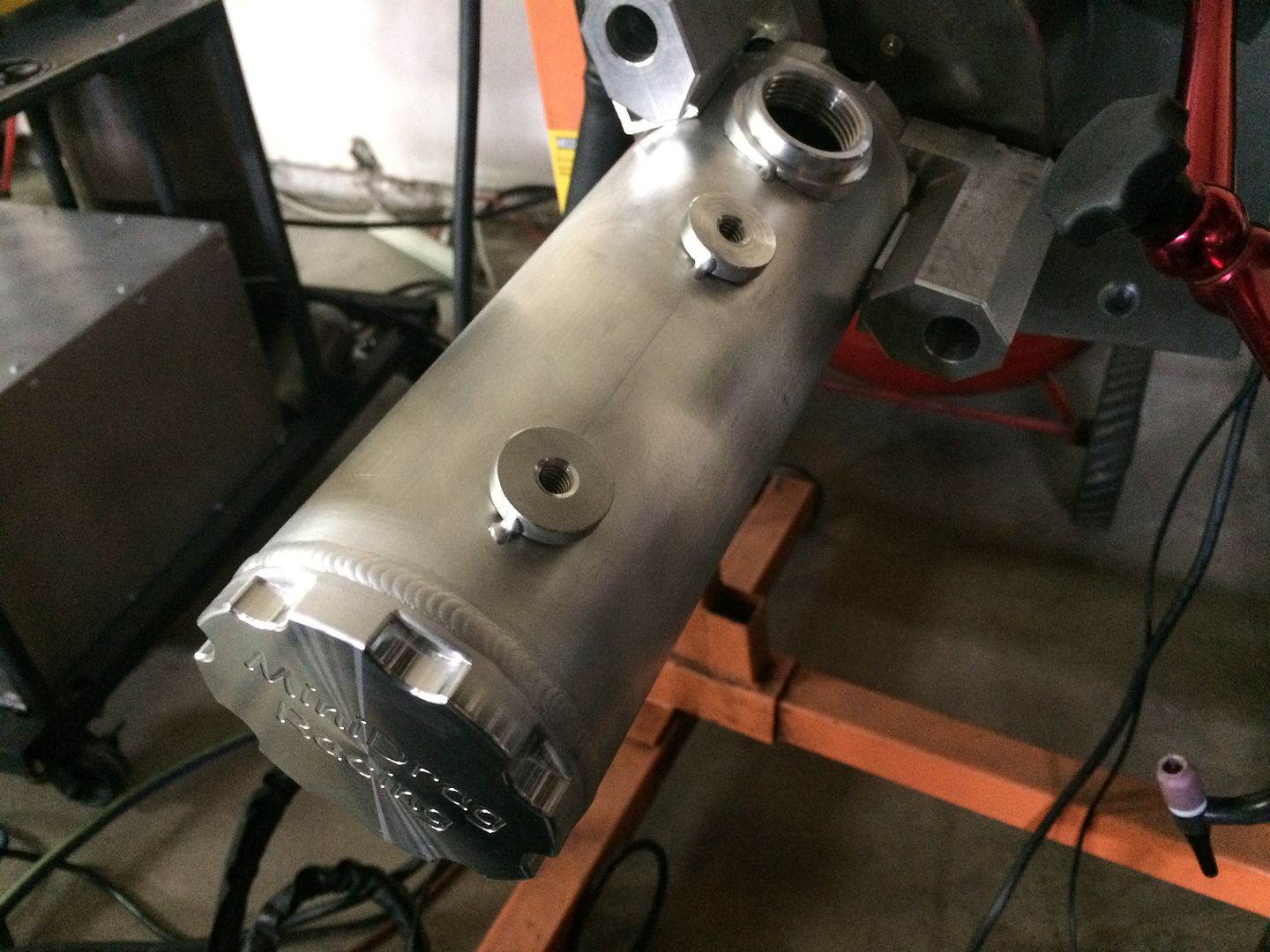
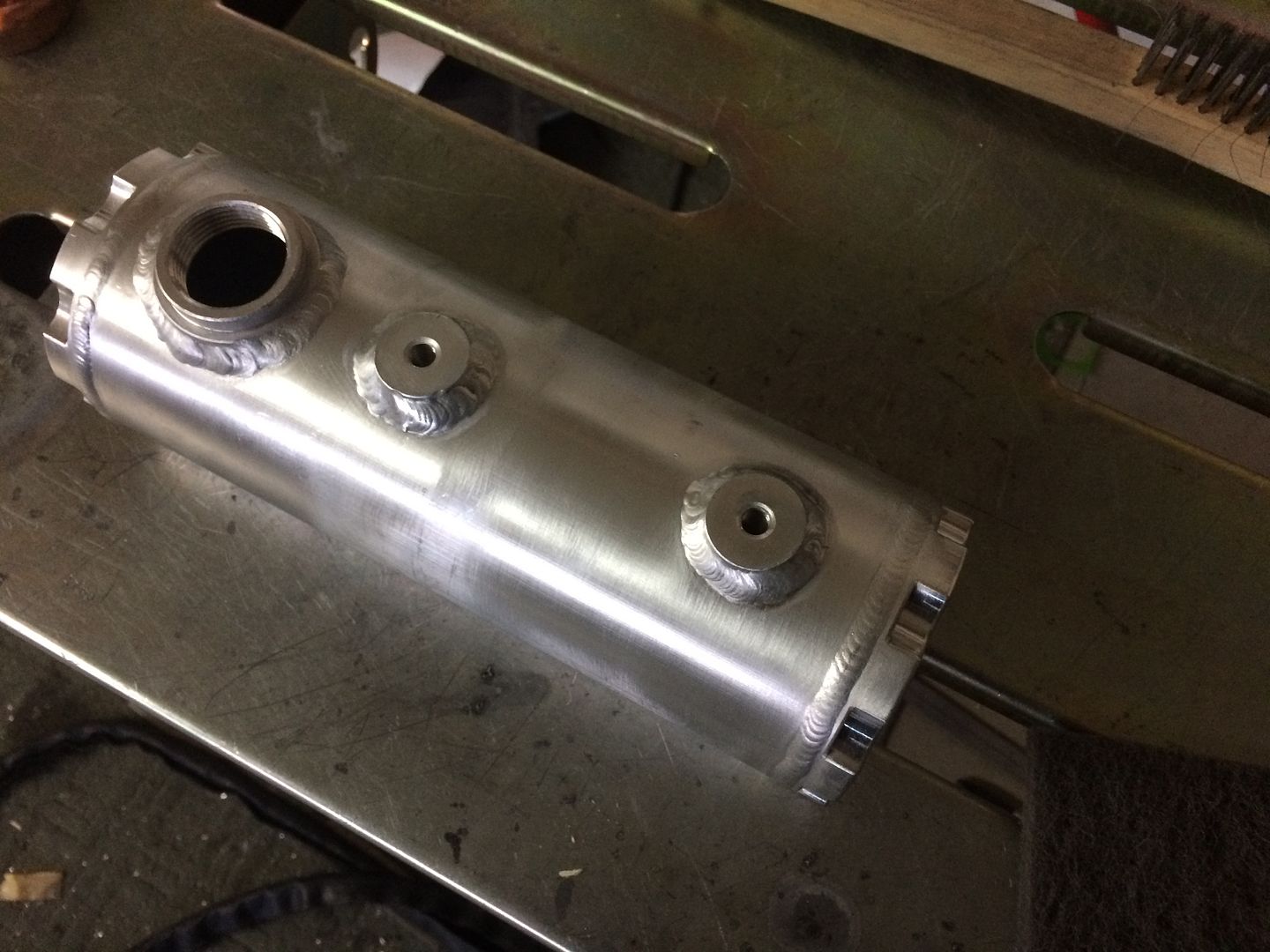
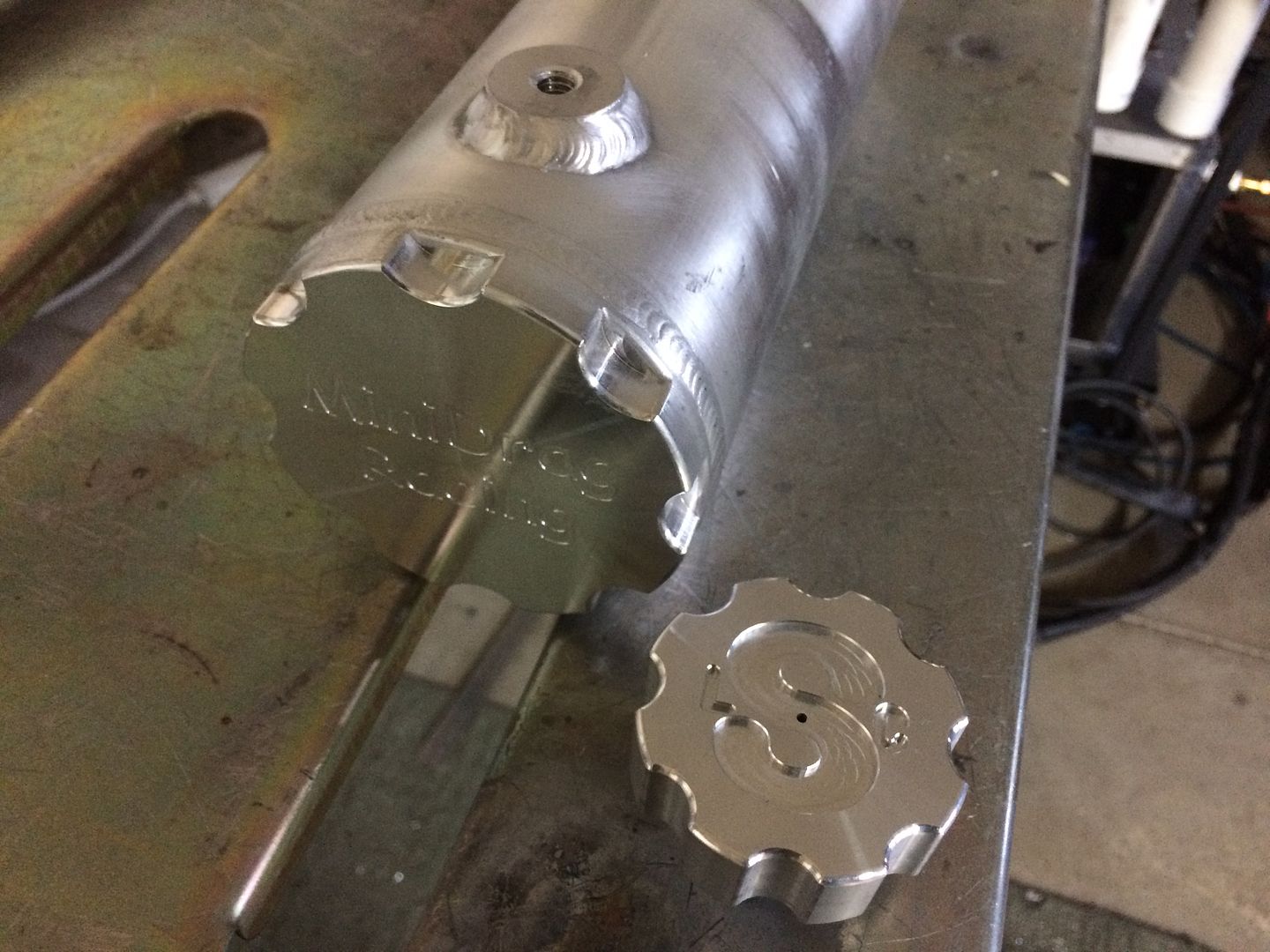
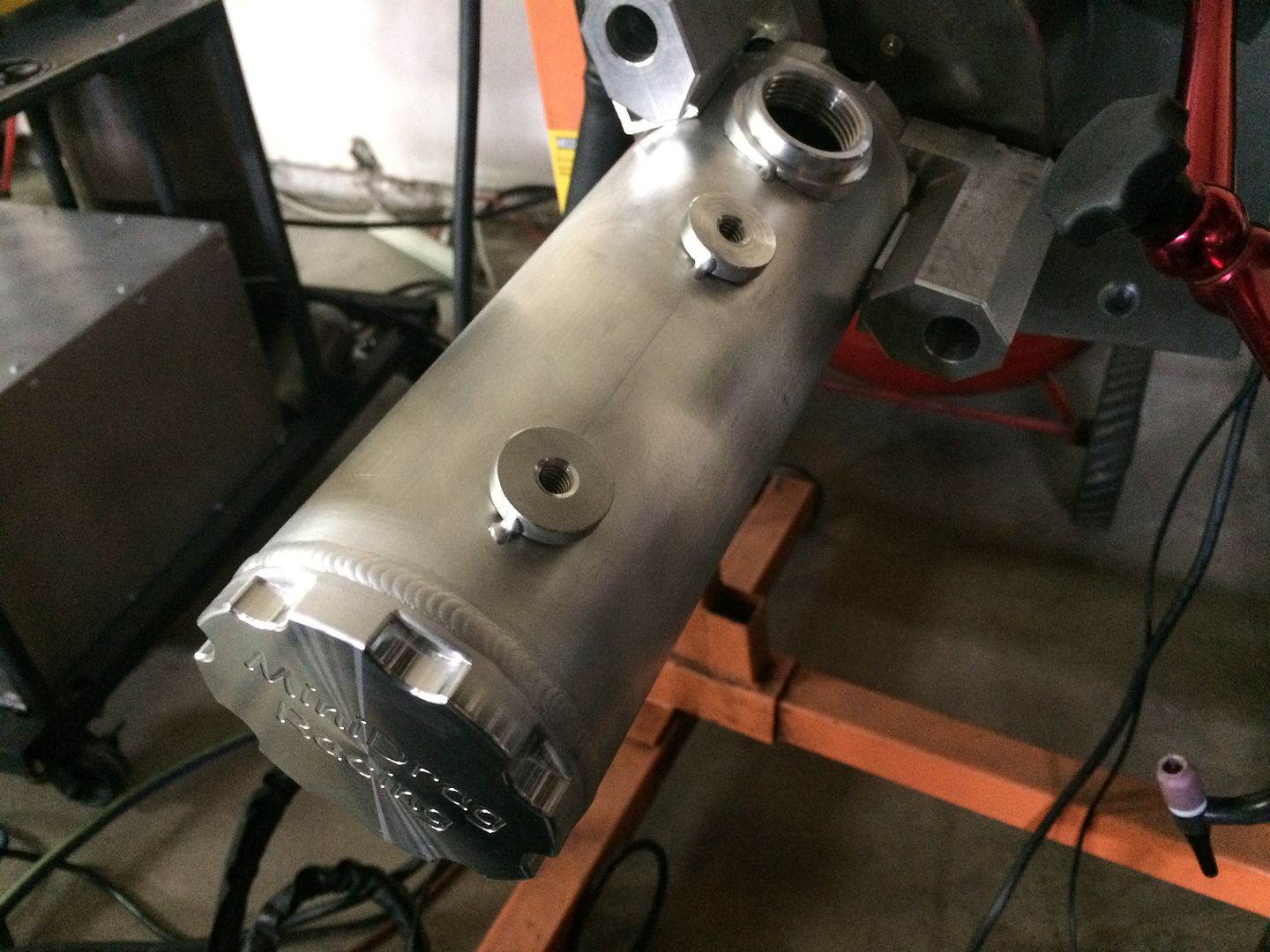
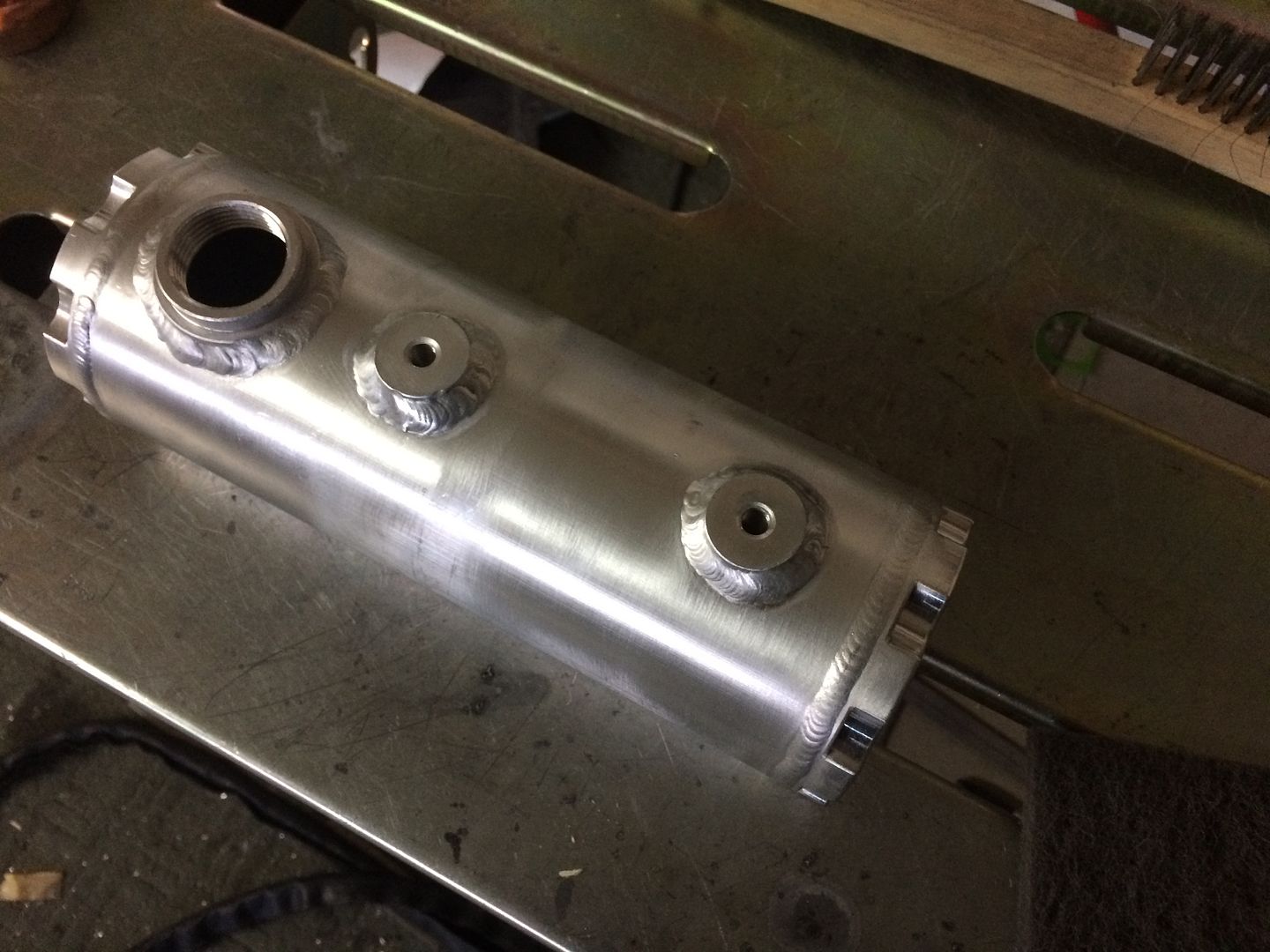
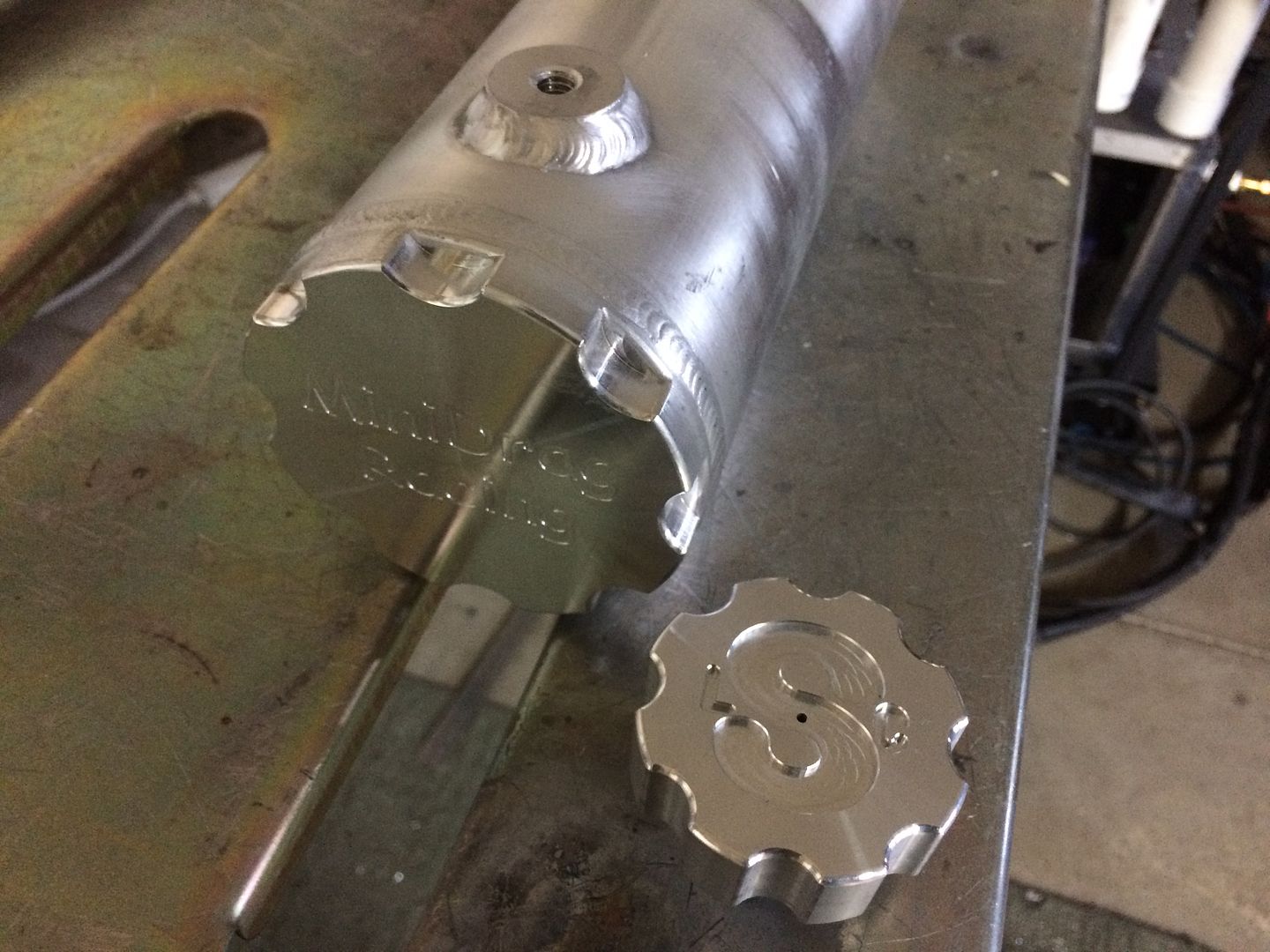
Return to “Welding Projects - Welding project Ideas - Welding project plans”
Jump to
- Introductions & How to Use the Forum
- ↳ Welcome!
- ↳ Member Introductions
- ↳ How to Use the Forum
- ↳ Moderator Applications
- Welding Discussion
- ↳ Metal Cutting
- ↳ Tig Welding - Tig Welding Aluminum - Tig Welding Techniques - Aluminum Tig Welding
- ↳ Mig and Flux Core - gas metal arc welding & flux cored arc welding
- ↳ Stick Welding/Arc Welding - Shielded Metal Arc Welding
- ↳ Welding Forum General Shop Talk
- ↳ Welding Certification - Stick/Arc Welding, Tig Welding, Mig Welding Certification tests - Welding Tests of all kinds
- ↳ Welding Projects - Welding project Ideas - Welding project plans
- ↳ Product Reviews
- ↳ Fuel Gas Heating
- Welding Tips & Tricks
- ↳ Video Discussion
- ↳ Wish List
- Announcements & Feedback
- ↳ Forum News
- ↳ Suggestions, Feedback and Support
- Welding Marketplace
- ↳ Welding Jobs - Industrial Welding Jobs - Pipe Welding Jobs - Tig Welding Jobs
- ↳ Classifieds - Buy, Sell, Trade Used Welding Equipment
- Welding Resources
- ↳ Tradeshows, Seminars and Events
- ↳ The Welding Library
- ↳ Education Opportunities