I have some heavy duty extension cord and decided to use it to wire the project up... I had one male end of a cord left over from another project and decide to use that end, along with the female end of the cord still intact... to create a quick disconnect for the motor... since i made the side of the enclosure that the controller mounts to remove-able, I wanted to be able to unplug the motor, etc, as needed... I dont like the wing nut or twist type of electrical connectors, so I use wago connectors i have laying around... i can also very easily add wiring for lighting and additional electrical outlet on the box, , etc. if i want to...
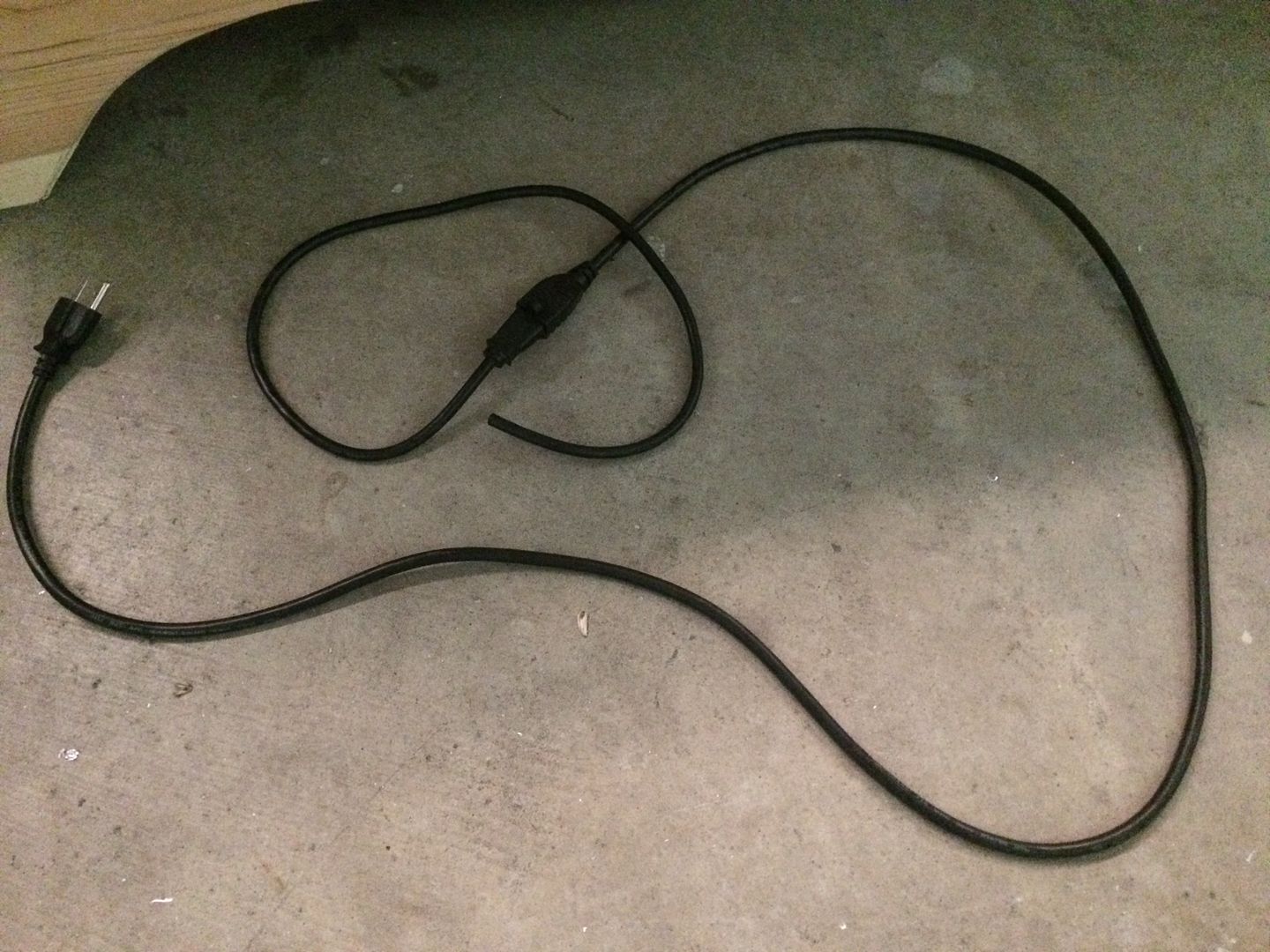
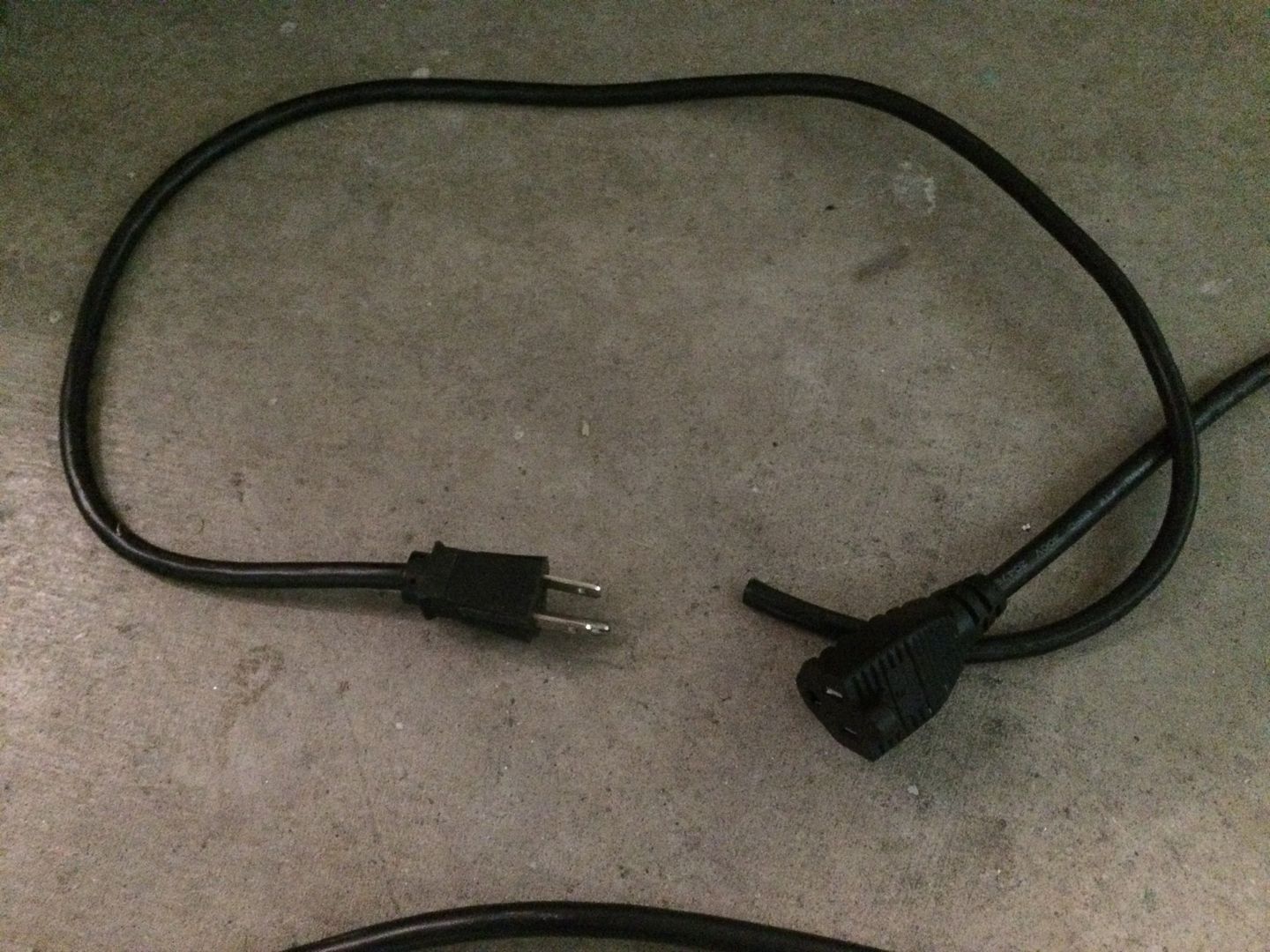
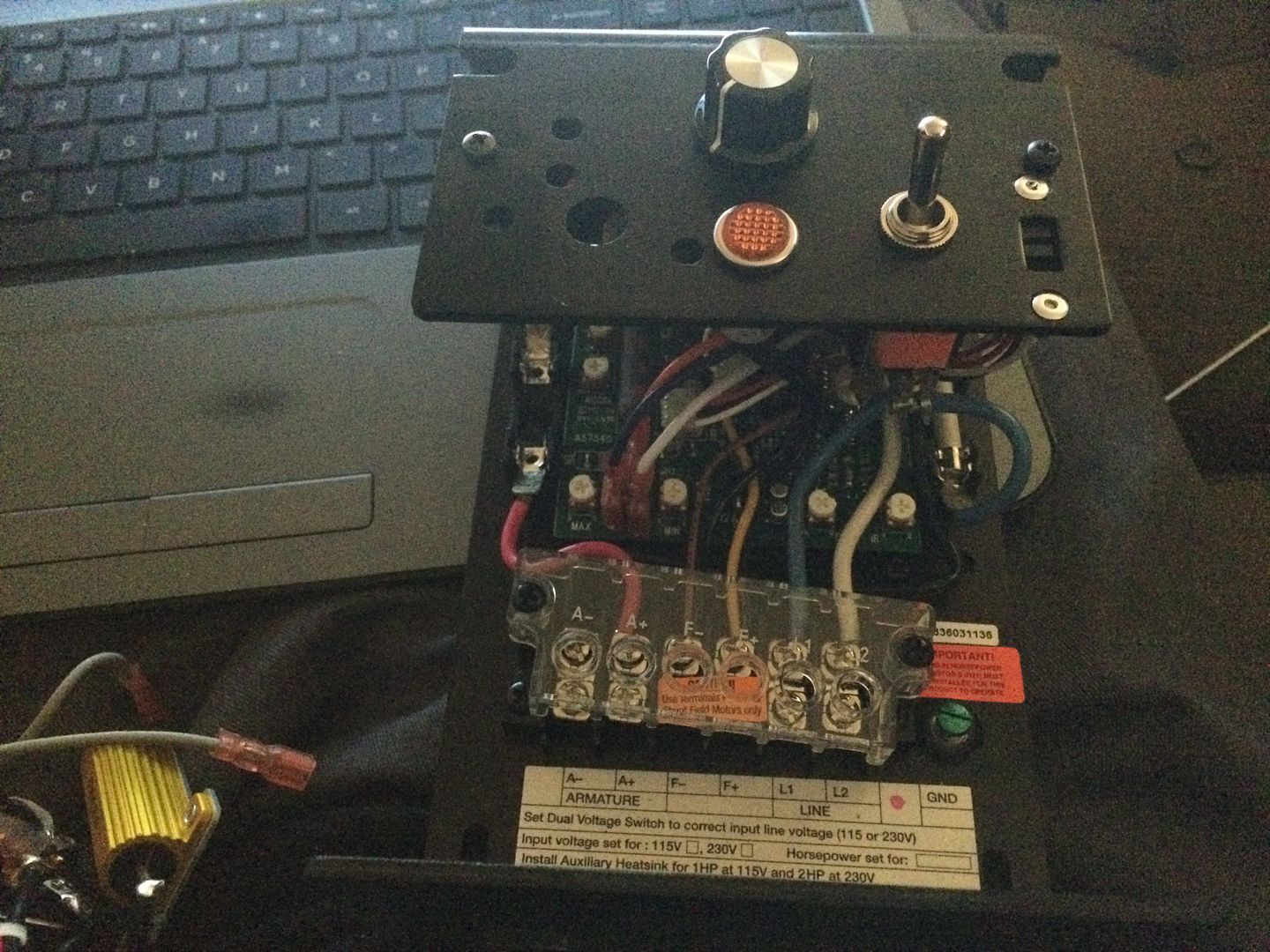