This is what I want to build, I want to mount ball bearings around this arch so I can lift and be able to use a cant hook or peavy to turn a log on my sawmill. I can space the ball bearings out, but don't want them any farther than 3-4 inches, and there will be one on each side with an axle welded into the 1"x1" to hold the ball bearings. I have a bunch of ball bearings with 20mm on the inside that I plan to use. My sawmill has a 32" max cut which translates to a 36" diameter log (you have to cut the sides off first). I want to be able to lift each end of a log and be able to spin it in these arches, which would be welded to the top of floor jacks.
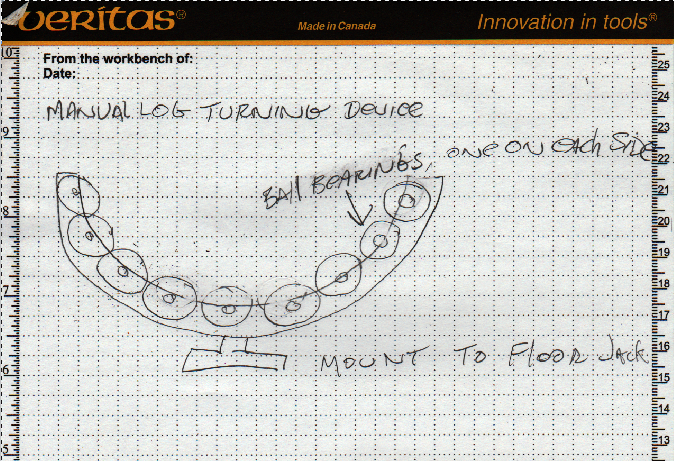
Short of buying the material I may need to build a square bender, I've seen some DIY projects on YT, but before I do that I was curious if there is any place I could buy pre-bent stock?
Maybe a local shop could do that, not sure. I haven't checked yet. Anyone know of a place online? Not sure if shipping would prohibit such a purchase. I've seen some small stuff at King Architecture Metals, but nothing in the size I need.
I could also use round thick wall pipe probably. Would that be stronger than 1" square stock?