I haven't actually started this, but my next wife wants to replace her families wood dock with a rollaway aluminum one and i got volunteered to do it. Never having done anything submerged, i need to know if my material selection is okay. The lake is fresh water and the dock will be in it for about 5 months out of the year. I will mig everything.
6061 aluminum for the frame, deck, railings etc. ?
What wire would be best, 4043 or 5356, or something else?
What would be the best thing for tires? The dock needs to move in and out fairly easily with 2 people at the least. I'd like to use a nice pneumatic tire, but will they hold up under water for that length of time?
if I've neglected anything, don't be afraid to add it in.
Thanks!!!
Other Steve
What welding projects are you working on? Are you proud of something you built?
How about posting some pics so other welders can get some ideas?
How about posting some pics so other welders can get some ideas?
delraydella
- delraydella
-
Weldmonger
-
Posts:
-
Joined:Mon Apr 25, 2011 7:35 pm
-
Location:Detroit, MI
Welding☞Syncrowave 250,Millermatic 252,30a Spoolgun Cutting☞12" Hi-speed Cutoff Saw, 9x 12 Horizontal Bandsaw Milling☞Gorton 8d Vertical Mill Turning☞Monarch EE Precision Lathe Grinding ☞Brown & Sharpe #5 Surface Grinder
- Otto Nobedder
-
Weldmonger
-
Posts:
-
Joined:Thu Jan 06, 2011 11:40 pm
-
Location:Near New Orleans
It sounds like you're describing a fairly simple floating pier, a single structure with no roof. Aluminum and fresh water poses no challenge for alloy choice. Frankly 6061 maybe a bit of overkill. I assuming you're looking at a T1 hardness, so it can roll with the punches, so to speak? 4043 is a fine choice for filler, as the ductility at the joints is important when the wake of a passing boat, or the simple lapping of wind-driven "waves" will flex it regularly.
Pneumatic tires are not an issue in fresh water, beyond considering the extra bouyancy they provide where they're installed. A more important issue is the bearings they roll on. For five months of submersion, I'd recommend a "pressurized" bearing system, where grease is injected through a zerk fitting into a bearing cap with a reservoir and spring, so the grease is always under positive pressure. (This assumes using a typical boat-trailer axle to support the dock on wheels during roll-out.)
Cabela's, Bass Pro Shop, and Tracker Marine will have these in their catalogs.
I strongly suggest either closed-cell polyurethane or sealed-cell flotation... Most locations have outlawed exposed styrofoam, which always sucked as flotation, anyway!
I spent a couple years building floating docks on a huge artificial impoundment, where "cigar boats" were not uncommon. If I can offer further suggestions....
Steve S
Pneumatic tires are not an issue in fresh water, beyond considering the extra bouyancy they provide where they're installed. A more important issue is the bearings they roll on. For five months of submersion, I'd recommend a "pressurized" bearing system, where grease is injected through a zerk fitting into a bearing cap with a reservoir and spring, so the grease is always under positive pressure. (This assumes using a typical boat-trailer axle to support the dock on wheels during roll-out.)
Cabela's, Bass Pro Shop, and Tracker Marine will have these in their catalogs.
I strongly suggest either closed-cell polyurethane or sealed-cell flotation... Most locations have outlawed exposed styrofoam, which always sucked as flotation, anyway!
I spent a couple years building floating docks on a huge artificial impoundment, where "cigar boats" were not uncommon. If I can offer further suggestions....
Steve S
delraydella
- delraydella
-
Weldmonger
-
Posts:
-
Joined:Mon Apr 25, 2011 7:35 pm
-
Location:Detroit, MI
That's exactly what she wants, a simple floating pier. I'll steal some ideas from the web and come up with some drawings and post them here first before i do anything. If you wouldn't mind looking them over, I'd appreciate it.
Thanks!
Other Steve
Thanks!
Other Steve
Welding☞Syncrowave 250,Millermatic 252,30a Spoolgun Cutting☞12" Hi-speed Cutoff Saw, 9x 12 Horizontal Bandsaw Milling☞Gorton 8d Vertical Mill Turning☞Monarch EE Precision Lathe Grinding ☞Brown & Sharpe #5 Surface Grinder
delraydella
- delraydella
-
Weldmonger
-
Posts:
-
Joined:Mon Apr 25, 2011 7:35 pm
-
Location:Detroit, MI
For the framing, I would truss out some tube, but would it be better to use round tube or square tube? Or does it matter? Round tube would seem to offer less resistance to the water movement, but I'm just guessing here.
1/8th inch wall tube for framing?
For the decking, i'd like to use aluminum floor bleacher planks. They are strong, lightweight and are skid-proof.
1/8th inch wall tube for framing?
For the decking, i'd like to use aluminum floor bleacher planks. They are strong, lightweight and are skid-proof.
Welding☞Syncrowave 250,Millermatic 252,30a Spoolgun Cutting☞12" Hi-speed Cutoff Saw, 9x 12 Horizontal Bandsaw Milling☞Gorton 8d Vertical Mill Turning☞Monarch EE Precision Lathe Grinding ☞Brown & Sharpe #5 Surface Grinder
- Otto Nobedder
-
Weldmonger
-
Posts:
-
Joined:Thu Jan 06, 2011 11:40 pm
-
Location:Near New Orleans
How rough is the water? Is this a large lake with powerboats throwing wakes, or a smaller lake with mostly fishing boats and the occasional squall?
There is benefit to round tube in a higher-stress environment; There is benefit to square tube for construction simplicity. The simplest trusses are all 1 1/2" angle with round-bar racking welded between. Weigh the material cost against the abuse it will see.
Steve S
There is benefit to round tube in a higher-stress environment; There is benefit to square tube for construction simplicity. The simplest trusses are all 1 1/2" angle with round-bar racking welded between. Weigh the material cost against the abuse it will see.
Steve S
delraydella
- delraydella
-
Weldmonger
-
Posts:
-
Joined:Mon Apr 25, 2011 7:35 pm
-
Location:Detroit, MI
It won't see much rough water at all, so I'll go with the square tube. I already have some on the shelf anyway. For the truss, i was planning on using 1 1/2" for the top and bottom rails and 1" for the inner truss diagonals and uprights. This way i can get a good solid weld on all 4 sides.
Other Steve
Other Steve
Welding☞Syncrowave 250,Millermatic 252,30a Spoolgun Cutting☞12" Hi-speed Cutoff Saw, 9x 12 Horizontal Bandsaw Milling☞Gorton 8d Vertical Mill Turning☞Monarch EE Precision Lathe Grinding ☞Brown & Sharpe #5 Surface Grinder
- Otto Nobedder
-
Weldmonger
-
Posts:
-
Joined:Thu Jan 06, 2011 11:40 pm
-
Location:Near New Orleans
delraydella
- delraydella
-
Weldmonger
-
Posts:
-
Joined:Mon Apr 25, 2011 7:35 pm
-
Location:Detroit, MI
Definitely!
Thanks!!
Other Steve
Thanks!!
Other Steve
Welding☞Syncrowave 250,Millermatic 252,30a Spoolgun Cutting☞12" Hi-speed Cutoff Saw, 9x 12 Horizontal Bandsaw Milling☞Gorton 8d Vertical Mill Turning☞Monarch EE Precision Lathe Grinding ☞Brown & Sharpe #5 Surface Grinder
delraydella
- delraydella
-
Weldmonger
-
Posts:
-
Joined:Mon Apr 25, 2011 7:35 pm
-
Location:Detroit, MI
I made up a test piece of the truss framework today, this is 1 1/4" square tube on the top and bottom and 1" for the inner pieces and it all has an 1/8th inch wall. It's 12 inches high and 4 feet long and weighs 10 pounds, which i think is too heavy.That would put a 4 x 16 deck at over 200 pounds, not practical if one person has to move it in and out. And that one person will most likely be me!
I'll do one more tomorrow with1/16th inch or 10 gauge wall. That should cut the weight by at least half. The truss gives it a lot of strength, but i don't want to go less than 1/16" wall for fear of blowing through it.
I'll do one more tomorrow with1/16th inch or 10 gauge wall. That should cut the weight by at least half. The truss gives it a lot of strength, but i don't want to go less than 1/16" wall for fear of blowing through it.
- Attachments
-
- IMG_8057.JPG (128.2 KiB) Viewed 4306 times
Welding☞Syncrowave 250,Millermatic 252,30a Spoolgun Cutting☞12" Hi-speed Cutoff Saw, 9x 12 Horizontal Bandsaw Milling☞Gorton 8d Vertical Mill Turning☞Monarch EE Precision Lathe Grinding ☞Brown & Sharpe #5 Surface Grinder
- Otto Nobedder
-
Weldmonger
-
Posts:
-
Joined:Thu Jan 06, 2011 11:40 pm
-
Location:Near New Orleans
You'll find an 8" truss more than adequate for that material and service. Also, the rack bracing can be 60*, rather then the 45* on your sample, reducing material and weight.
delraydella
- delraydella
-
Weldmonger
-
Posts:
-
Joined:Mon Apr 25, 2011 7:35 pm
-
Location:Detroit, MI
Sounds good to me!
Welding☞Syncrowave 250,Millermatic 252,30a Spoolgun Cutting☞12" Hi-speed Cutoff Saw, 9x 12 Horizontal Bandsaw Milling☞Gorton 8d Vertical Mill Turning☞Monarch EE Precision Lathe Grinding ☞Brown & Sharpe #5 Surface Grinder
delraydella
- delraydella
-
Weldmonger
-
Posts:
-
Joined:Mon Apr 25, 2011 7:35 pm
-
Location:Detroit, MI
That does work pretty good, it will cut out at least a quarter of the weight.
but, this whole project may be scuttled due to family squabbles. If there's one thing i learned from my first 2 ex-wives, it's......
...Don't get involved in family squabbles!
Other Steve
but, this whole project may be scuttled due to family squabbles. If there's one thing i learned from my first 2 ex-wives, it's......
...Don't get involved in family squabbles!
Other Steve
- Attachments
-
- IMG_8064.JPG (127.86 KiB) Viewed 3150 times
Welding☞Syncrowave 250,Millermatic 252,30a Spoolgun Cutting☞12" Hi-speed Cutoff Saw, 9x 12 Horizontal Bandsaw Milling☞Gorton 8d Vertical Mill Turning☞Monarch EE Precision Lathe Grinding ☞Brown & Sharpe #5 Surface Grinder
delraydella
- delraydella
-
Weldmonger
-
Posts:
-
Joined:Mon Apr 25, 2011 7:35 pm
-
Location:Detroit, MI
Thank you Alexa, that's good advice!
Welding☞Syncrowave 250,Millermatic 252,30a Spoolgun Cutting☞12" Hi-speed Cutoff Saw, 9x 12 Horizontal Bandsaw Milling☞Gorton 8d Vertical Mill Turning☞Monarch EE Precision Lathe Grinding ☞Brown & Sharpe #5 Surface Grinder
I dont mean to get my nose in this,but; there is a man here that built a system for his boat. He must have worked for the rail road, he used a boat trailer, mounted 4 rail car wheels (small about 8"-10" ) on it and used rails into the water. He has a wench mounted to concrete anchor to bring it in and let it out. The boat stays on land when not in use.
Pretty slick set up.
My point is as you build and it gets heavy you may, if possible; think about a wench or trailer hitch and 4 wheeler.
Save your back.
Just a thought,
Richard
Pretty slick set up.
My point is as you build and it gets heavy you may, if possible; think about a wench or trailer hitch and 4 wheeler.
Save your back.
Just a thought,
Richard

When seconds count, the police are only minutes away...
Lincoln Squarewave 335, water cooled WP20 torch with pedal control
Millermatic 200 mig
Thermodynamics Cutmaster 52 Plasma
Old stick welder
Cutting torch, saws and grinders
Very little talent.
Lincoln Squarewave 335, water cooled WP20 torch with pedal control
Millermatic 200 mig
Thermodynamics Cutmaster 52 Plasma
Old stick welder
Cutting torch, saws and grinders
Very little talent.
- Otto Nobedder
-
Weldmonger
-
Posts:
-
Joined:Thu Jan 06, 2011 11:40 pm
-
Location:Near New Orleans
- Otto Nobedder
-
Weldmonger
-
Posts:
-
Joined:Thu Jan 06, 2011 11:40 pm
-
Location:Near New Orleans
hehehee did not catch that to start with, oh well , i need a good wench i guess, 

When seconds count, the police are only minutes away...
Lincoln Squarewave 335, water cooled WP20 torch with pedal control
Millermatic 200 mig
Thermodynamics Cutmaster 52 Plasma
Old stick welder
Cutting torch, saws and grinders
Very little talent.
Lincoln Squarewave 335, water cooled WP20 torch with pedal control
Millermatic 200 mig
Thermodynamics Cutmaster 52 Plasma
Old stick welder
Cutting torch, saws and grinders
Very little talent.
It is rumored that I may have 200 of these to build, being that since you brought up docks, and that I followed your thread and suddenly ended up with dock parts to build, figured to post it here. This one was needing to be shortened and narrowed in two days before this holiday weekend. Got it in on Tuesday, Got the material on Wednesday, And had it completed by Thursday evening. All done with a circular saw and my SW 250. It also needed wheel housings built in. I didn't have time to clean anything. Was 4' x 24', and is now 3' x 16'. We wouldn't have been able to source the hinge extrusion or the side rail extrusion in time, so this was the only option. A hinged ramp for a floating dock.

Here's half of what's left, being it at to be shortened equally from each end and each side.

I capped the ends, even though they didn't require it. Just the thought of some kid getting his toes up under here, even though the frame is to be faced with wood, and for the fact that it just looked gnarly.


Here's half of what's left, being it at to be shortened equally from each end and each side.

I capped the ends, even though they didn't require it. Just the thought of some kid getting his toes up under here, even though the frame is to be faced with wood, and for the fact that it just looked gnarly.

Miller ABP 330, Syncrowave 250, Dynasty 300 DX.
Honorary member of the Fraternity of Faded Tee Shirts.
Honorary member of the Fraternity of Faded Tee Shirts.
- Otto Nobedder
-
Weldmonger
-
Posts:
-
Joined:Thu Jan 06, 2011 11:40 pm
-
Location:Near New Orleans
Jeff, while the docks I built were in steel, that is almost exactly the way we hinged the gangway.
Ours were much beefier trusses, because this was Lake of the Ozarks, with Cigar boats and such tearing it up, with docks often right on the main channel. Cables and cross-cables would hold the dock to shore, with a single gangway usually the only thing holding a three-slip covered dock out from shore.
Four-slip docks and bigger were easier to brace, as they usually had two gangways, and X-cables between the gangways added a lot of rigidity.
Reminiscing... That was one of the most fun jobs I ever had, despite the crappy pay.
Steve S
Ours were much beefier trusses, because this was Lake of the Ozarks, with Cigar boats and such tearing it up, with docks often right on the main channel. Cables and cross-cables would hold the dock to shore, with a single gangway usually the only thing holding a three-slip covered dock out from shore.
Four-slip docks and bigger were easier to brace, as they usually had two gangways, and X-cables between the gangways added a lot of rigidity.
Reminiscing... That was one of the most fun jobs I ever had, despite the crappy pay.
Steve S
By the end of it, I was throwing weld beads at it. I have some on there that could pass for fast Alu MIG welds. The clincher was he got one size material, which was 3/8" x 5", because the two piling stay hoops I had to make after the fact were on 5" material, so I had to rip it to size for the end rails with the circular saw and then finish the cut edge. All that nit-picky, time consuming stuff that drags a job on, then you have to weld it all too. There wasn't enough material, so I re-purposed a section of the old side rail for the wheel plates to attach to. It still had some wood on it when they brought it.
On the doodle, they had the end caps dimensioned at 2", but the hinges were 2.5". Now add second guess work into the procedure and more time gets added on. It came out dead-nuts square and parallel though, and my hurried welds are nicer than the pre-existing ones, just for being complete.
I was hustling like the old underpaid piecework days. I felt it Friday. Was like having a work hangover. lol
On the doodle, they had the end caps dimensioned at 2", but the hinges were 2.5". Now add second guess work into the procedure and more time gets added on. It came out dead-nuts square and parallel though, and my hurried welds are nicer than the pre-existing ones, just for being complete.
I was hustling like the old underpaid piecework days. I felt it Friday. Was like having a work hangover. lol
Miller ABP 330, Syncrowave 250, Dynasty 300 DX.
Honorary member of the Fraternity of Faded Tee Shirts.
Honorary member of the Fraternity of Faded Tee Shirts.
delraydella
- delraydella
-
Weldmonger
-
Posts:
-
Joined:Mon Apr 25, 2011 7:35 pm
-
Location:Detroit, MI
I like the trailer hitch idea, since it will most likely be me that has to put this thing in the water and take it our every year. I also have a bunch of 10" triangle truss that I might use for framing, it all depends on how much they want to spend and how much time I have to do this. I also thought this would be a good project to show her son how to weld, he's a great kid to have around the shop, but so far he doesn't seem too enthused about welding. I guess it's not for everybody.
What would be the best way to anchor this thing into place once it's in the water? I don't want it to float away in a storm. If you haven't guessed, this dock stuff is pretty new to me, I'm a city boy.
Other Steve
What would be the best way to anchor this thing into place once it's in the water? I don't want it to float away in a storm. If you haven't guessed, this dock stuff is pretty new to me, I'm a city boy.
Other Steve
Welding☞Syncrowave 250,Millermatic 252,30a Spoolgun Cutting☞12" Hi-speed Cutoff Saw, 9x 12 Horizontal Bandsaw Milling☞Gorton 8d Vertical Mill Turning☞Monarch EE Precision Lathe Grinding ☞Brown & Sharpe #5 Surface Grinder
around here the way most secure a dock is to drive 2'' - 3" pipe into the ground several feet ( until very solid ) at the end of the dock that is in the water. then put a larger loop of some type around the pipe attached to the dock. this allows the dock to be anchored and be free to rise and fall with the waves. the pipes would be at the sides of the dock,
some cut the pipes a couple feet higher than the dock deck, some don't and use them for lights, tie-up points, sign posts, if they are high enough.
I have seen everything from small front tires off a lawn mower (no rim) , canvas fire hose , metal rings, you name it , to create the loops to secure dock to pipes ( pilings ). I would suggest a thick wall pipe and sharpen the ends that are driven into the ground or weld a point on them to ease driving in. One thing about using metal loops is the noise it will make all the time scraping up and down metal on metal.
Hope this helps
Richard
some cut the pipes a couple feet higher than the dock deck, some don't and use them for lights, tie-up points, sign posts, if they are high enough.
I have seen everything from small front tires off a lawn mower (no rim) , canvas fire hose , metal rings, you name it , to create the loops to secure dock to pipes ( pilings ). I would suggest a thick wall pipe and sharpen the ends that are driven into the ground or weld a point on them to ease driving in. One thing about using metal loops is the noise it will make all the time scraping up and down metal on metal.
Hope this helps
Richard
When seconds count, the police are only minutes away...
Lincoln Squarewave 335, water cooled WP20 torch with pedal control
Millermatic 200 mig
Thermodynamics Cutmaster 52 Plasma
Old stick welder
Cutting torch, saws and grinders
Very little talent.
Lincoln Squarewave 335, water cooled WP20 torch with pedal control
Millermatic 200 mig
Thermodynamics Cutmaster 52 Plasma
Old stick welder
Cutting torch, saws and grinders
Very little talent.
I made hoops as an aside but they never gave a post size or whether it was pipe or beam. I don't have a bending die that will do 180's, nor did I have the right radius die to make a smooth U on such short notice. Tried calling the guy on his contact # and he never returned my call so he got what he got. He had given me an older galvanized one and only generalized one dimension change without the other. I could have bent the pipe incrementing the bend centers and altered the radius to make it smooth but didn't have enough 1.5" to make two unless he wanted anodized, which is more $.
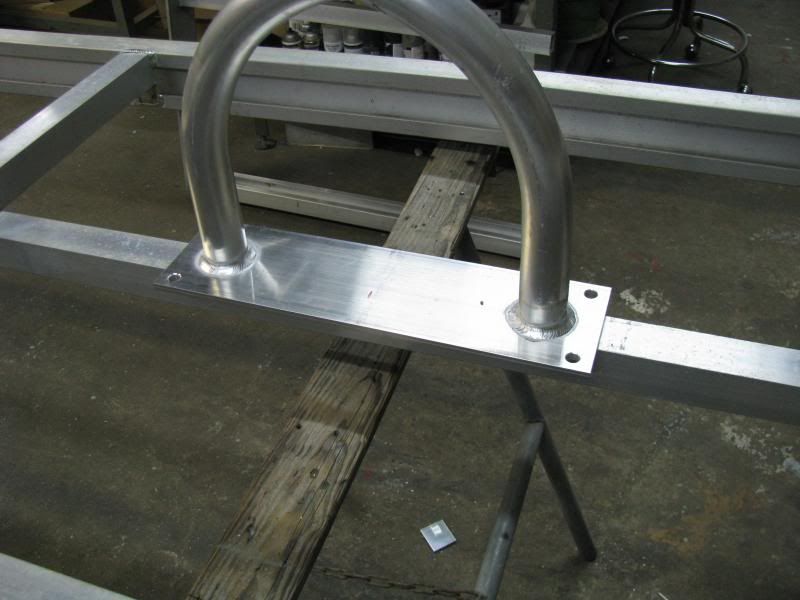
As it was, I was 10 pm on a Friday night getting thru with these after attacking the ramp project on Memorial Day weekend, while everyone else got a day head start on the festivities. Figured if nothing else, it will get them thru in this pinch until they get the ones they want.
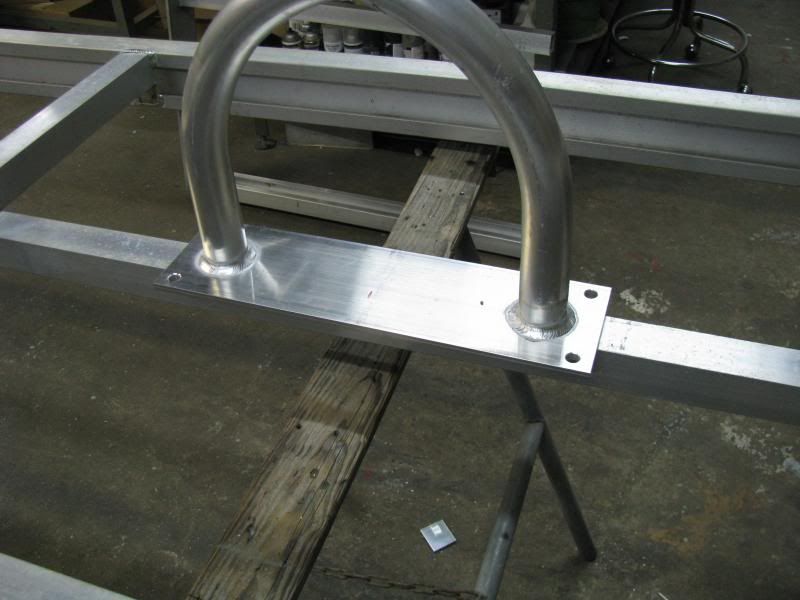
As it was, I was 10 pm on a Friday night getting thru with these after attacking the ramp project on Memorial Day weekend, while everyone else got a day head start on the festivities. Figured if nothing else, it will get them thru in this pinch until they get the ones they want.
Miller ABP 330, Syncrowave 250, Dynasty 300 DX.
Honorary member of the Fraternity of Faded Tee Shirts.
Honorary member of the Fraternity of Faded Tee Shirts.
Return to “Welding Projects - Welding project Ideas - Welding project plans”
Jump to
- Introductions & How to Use the Forum
- ↳ Welcome!
- ↳ Member Introductions
- ↳ How to Use the Forum
- ↳ Moderator Applications
- Welding Discussion
- ↳ Metal Cutting
- ↳ Tig Welding - Tig Welding Aluminum - Tig Welding Techniques - Aluminum Tig Welding
- ↳ Mig and Flux Core - gas metal arc welding & flux cored arc welding
- ↳ Stick Welding/Arc Welding - Shielded Metal Arc Welding
- ↳ Welding Forum General Shop Talk
- ↳ Welding Certification - Stick/Arc Welding, Tig Welding, Mig Welding Certification tests - Welding Tests of all kinds
- ↳ Welding Projects - Welding project Ideas - Welding project plans
- ↳ Product Reviews
- ↳ Fuel Gas Heating
- Welding Tips & Tricks
- ↳ Video Discussion
- ↳ Wish List
- Announcements & Feedback
- ↳ Forum News
- ↳ Suggestions, Feedback and Support
- Welding Marketplace
- ↳ Welding Jobs - Industrial Welding Jobs - Pipe Welding Jobs - Tig Welding Jobs
- ↳ Classifieds - Buy, Sell, Trade Used Welding Equipment
- Welding Resources
- ↳ Tradeshows, Seminars and Events
- ↳ The Welding Library
- ↳ Education Opportunities