How about you at home guys? Can you afford extra parts/materials for test runs? Or for us shop guys who work for places that will not keep extra inventory for one-offs. So, what do we do? Well. . .I am here to admit that I cheat like a emm-effr. It's unorthodox, undocumented and likely unacceptable. At least to the armchair rocket scientists on the internet. Do we care? Most of us don't, and would probably bet our reputations on what we do, when it comes right down to it.
I needed to get NPT threads onto some quirky part. What I do have is a, 1/2" NPT bung. Thing is, I don't want to change out the torch guts or mess with the flow meter or any voltage/peak/freq or pulse settings. I want to clamp this thing to my table and get it right the first time. I want it to look I knew what I was doing, instead of someone knowing I struggled through it. Most of us know you will get good at these on the last one of a half a dozen of them otherwise.
Anyway, I made my own female adapter. I didn't stand any special way, brace myself, hover, or compensate for too much caffiene. This is what we have. It's 1" sched 40 anodized. Scraps of this galore. But I am not going to try to weld this short piece.
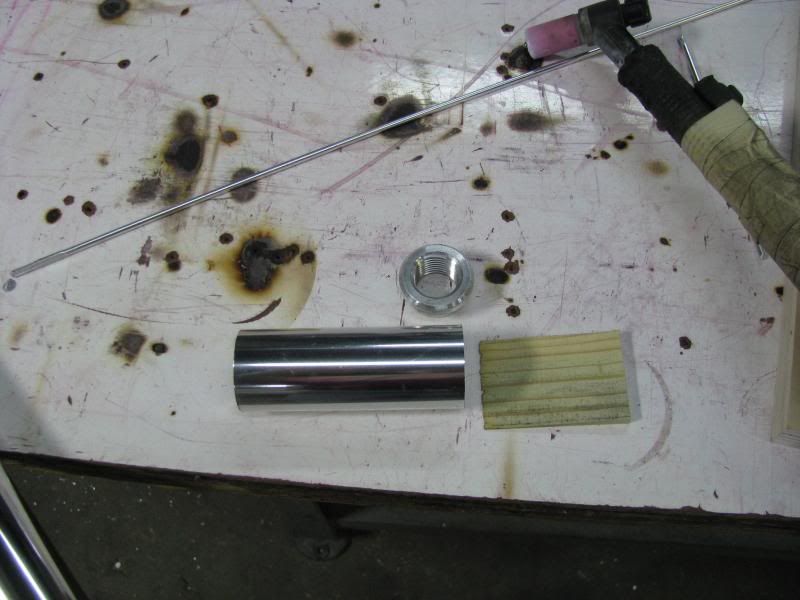
We'll end up with something like this, or this is where it will go eventually.
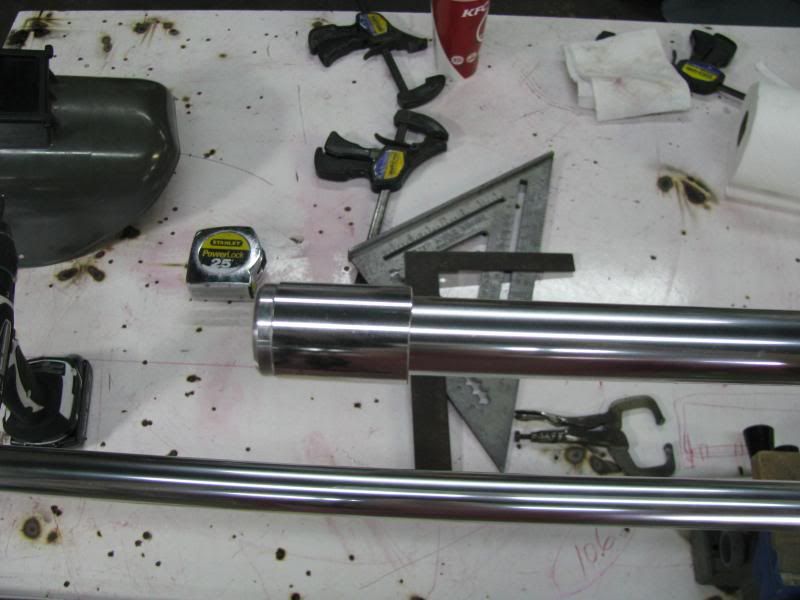
The bung is too small for the I.D. of the 1", so I use a little wedge to set the gap I want and hold the bung somewhat evenly. I didn't change tungsten so it needs to kind of fit the 1/8 pure I am using. No hovering, no stress. Just lay the torch right on the table, aim it where you want it, flip your hood down, or scratch your nose or whatever, and it will stay right where you put it. If your boss is yammerin at you from across the shop, you can even look like you are paying attention to him. For some of us older guys, a standing nap, perhaps, and at 200 amps AC, penetration is assured. Get the first tack and then tweak the parts straighter, or overcompensate the opposite side to allow for shrinkage of the tack to pull it dead nuts perfect. Look at the torch just sitting there. All I have to do is push the button. ZZZZZZZZZZZZT. Done.
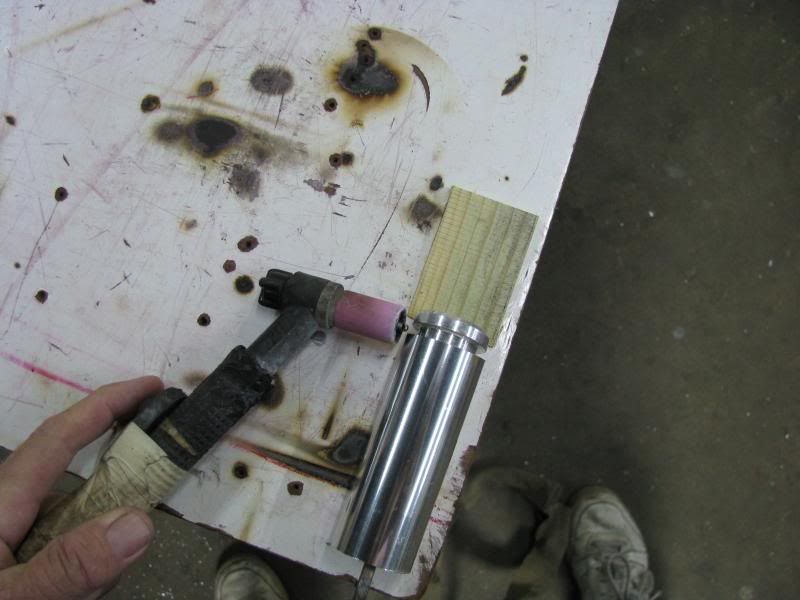
The cheating part? I have gotten so relaxed with the torch just laying there, I decided to let lay on every part of the joint. I bump welded it with manual pulse in reverse travel. I could see the tungsten and the penetration just like this, 3/4 of the way around, both right handed, and left handed. I could see the spaces of my ripples without the torch in the way and there is all the room in the world to add filler, exactly how and where I wanted it. Resting the torch on each pulse, takes away at least 75% of left handed error and almost all of the caffiene effect. Better yet is, I can stop instantly if it starts to get away and I also have the residual flashlight that in inclusive with balled, pure tungsten. I can make my corrections while it is still glowing and redirect my arc again before it goes out. No cable over the shoulder, no overhand torch holding, which alone adds about an additional 60 degrees or so of articulation at the torch head, comparatively, and I can flame dress my puddles as I go with just a bit of a back step.
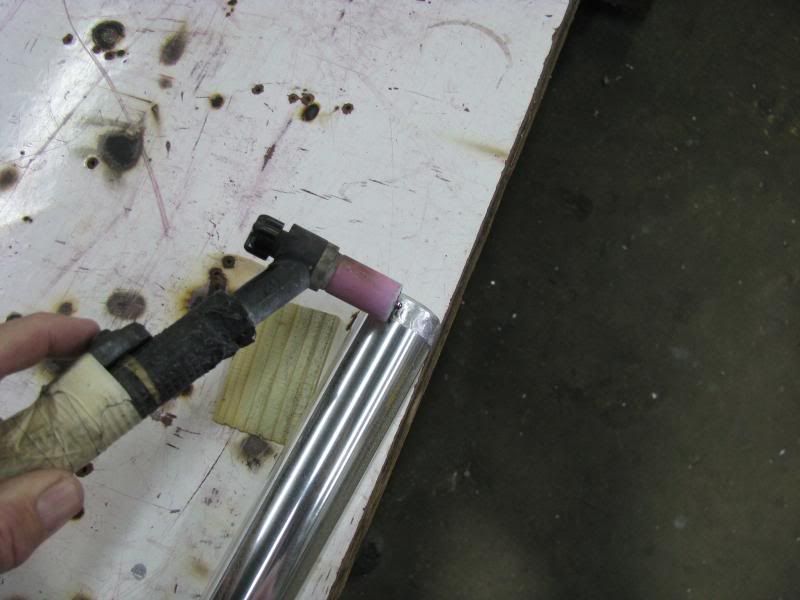
The part comes out like you weld them every day. The weld is clean and it's edges straight and crisp.The gap that was set in the parts initially, aligns the cup and tungsten perfectly, so all you have to do is rock the ball of the tungsten down in, and then out as you add filler. Bump the torch back another puddle and let it rest on the joint again and hit the button. zzzzzzzt zzzzzzzt zzzzzzzzt zzzzzzzzt zzzzzzzzzt and then zzt,zzt,zt to kill the crater, and timed at intervals just about how it reads in text. 200 amps sinks it home perfectly every time without burn thru or warping the threads.
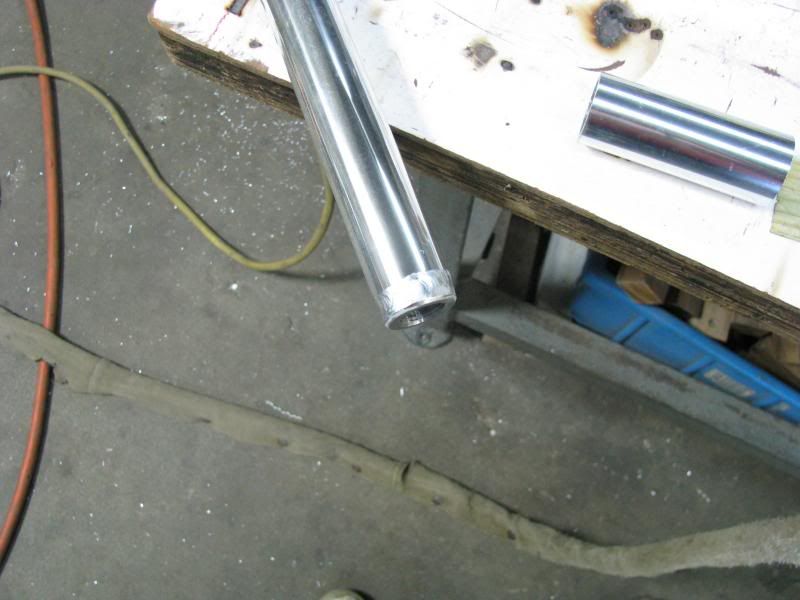
I welded it to the longer scrap as I found it. No sense cutting it twice and it gives you something to be able to hold onto to reposition it without burning gloves or monkeying with pliers.
No, it's no great project but I think a lot of people could find the tactic useful for small and odd parts.