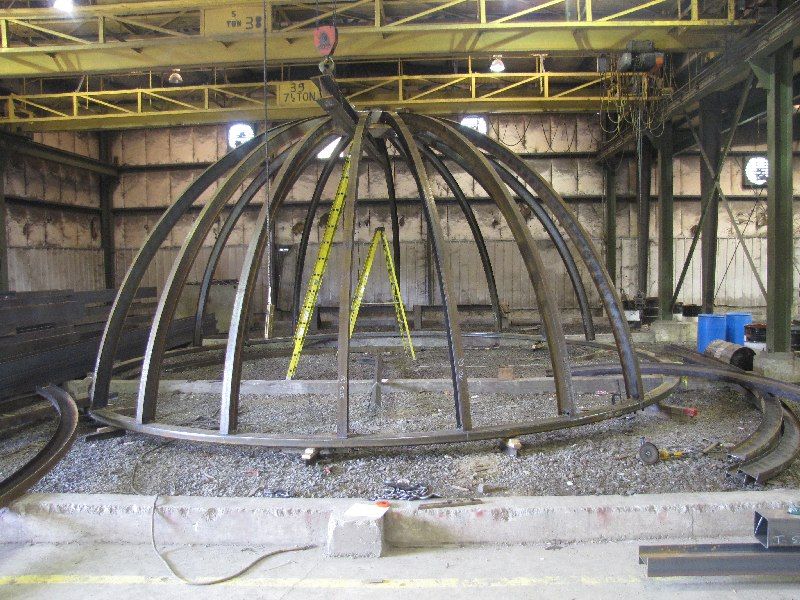
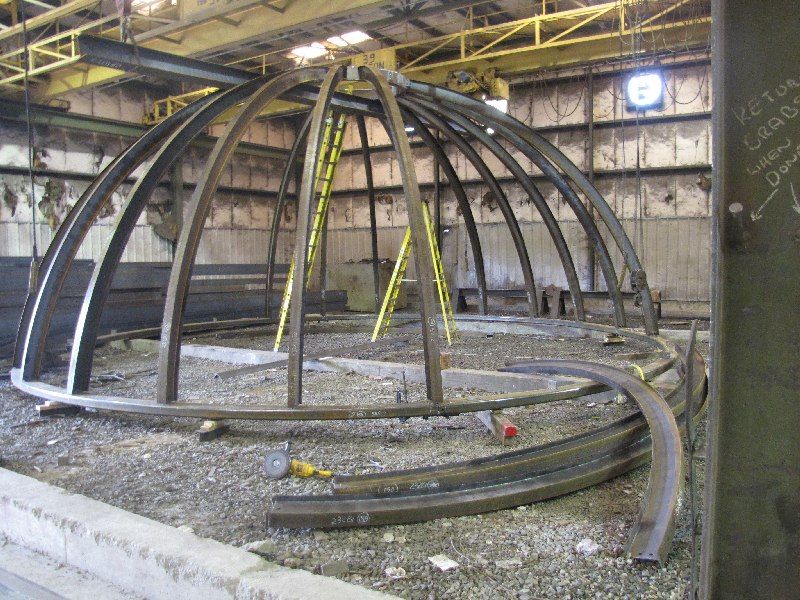
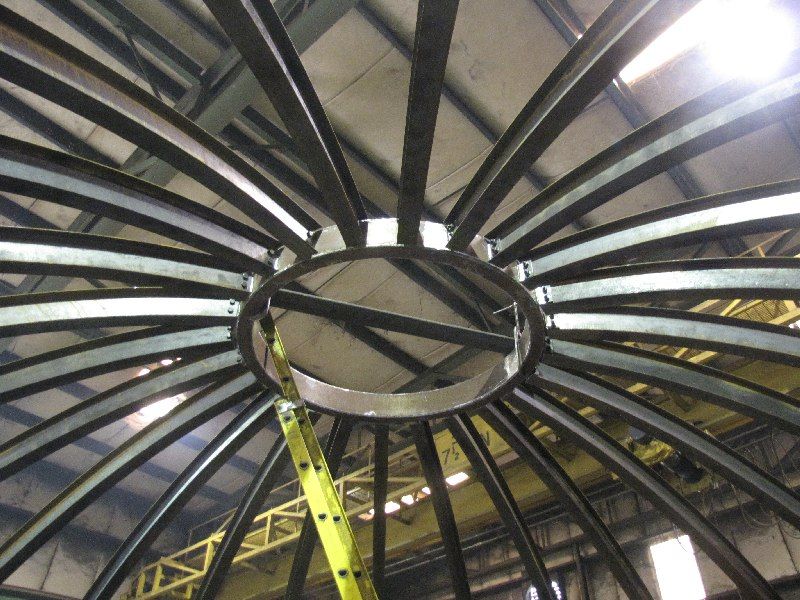
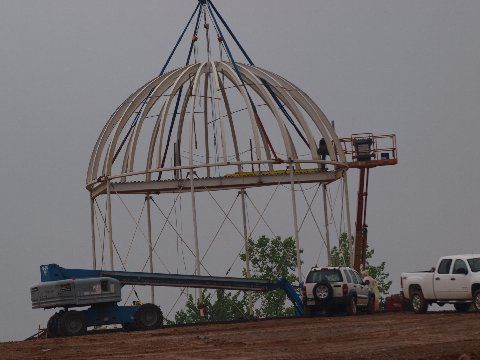
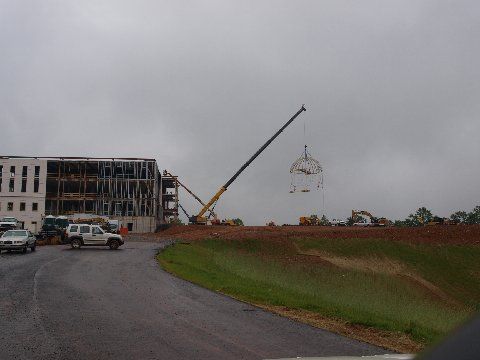
That sounds neat!WerkSpace wrote:I have a similar project
Is this question for me? If so, that pic was taken in the material receiving department, it was the only place that I could lay it all out and put it together without disrupting the entire shop(due to the over head cranes). The concrete piers with gravel floor are to hold the beams up off the floor and still are able to throw chains underneath and wrap the stacks of steel to move them down into the main shop for further processing(sawing, punching, cambering, fabrication, etc....weldin mike 27 wrote:Did they ever bother to concrete the floor for you? That looks abit 3rd world.
Yup, the painting/shipping/loading department is setup the same way on the opposite end of the plant. The main fabrication plant has solid floors with steel saw horses for work tables.weldin mike 27 wrote:Right. The flooring set up is exactly what it needs to be. Got ya.
Return to “Welding Projects - Welding project Ideas - Welding project plans”