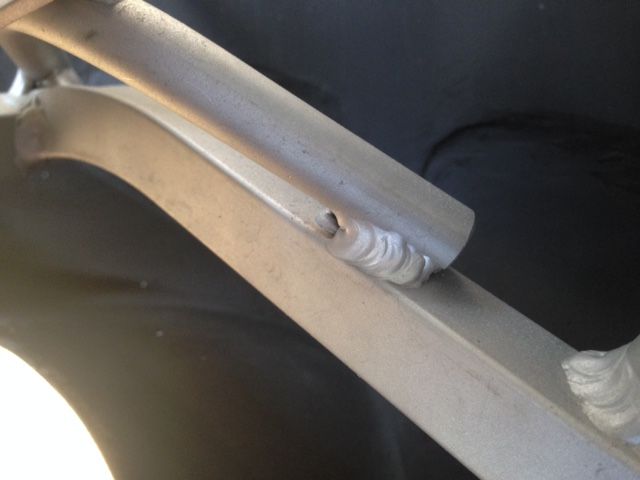
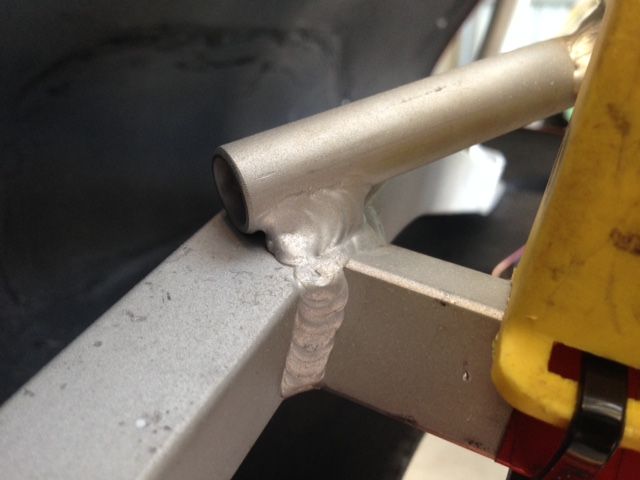
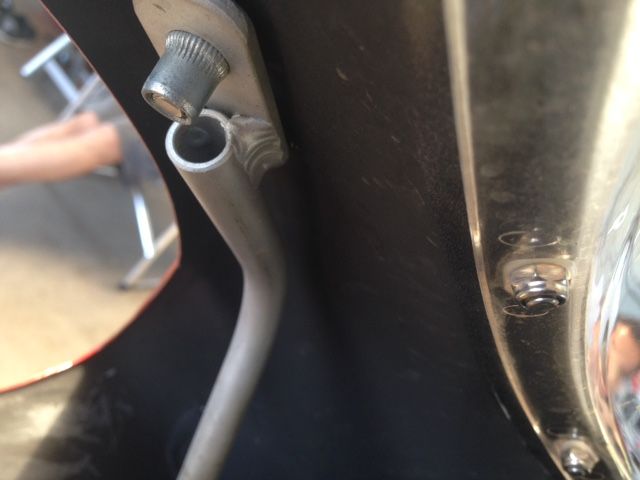
A quick update on this conversation.
Was out at the race track yesterday helping out some friends and took some shots while there of these welds on a friend's (purchased) front subframe. The round tube you see is only a little bigger in OD than a pencil. I didn't have a vernier calipers, but I'd say it's 1mm wall thickness, max.
This thin, light tube is part of a front subframe that has held up to a lot of racing on one of Australia's roughest road circuits - Mallala Raceway.
It inspires me to see that this can be done. In my normal stubborn way, I shall take all of your tips on board and keep practising until I get this. These tubes are considerably lighter than what I've been attempting...I just need to step up and build my skills.
Kym