Situation:
- 1 1/2" square aluminum, WITH rounded corners - 1/8" wall thickness
- when doing a 90 degree joint, 2 of 4 edges fit flush, the other 2 edges have a super wide gap, 1/4" gap or so. (due to the rounded corners)
- how does one bridge such a wide gap ?
Options I've considered:
- don't weld all 4 sides. aka don't over weld it. Just weld the 2 x flush fit sides & call it a day
- start with 2 or 3 edge welds (at the RED arrow) and build up that edge, until a bridge is formed
- get out the grinder & free hand a cut into the vertical leg so all 4 edges line up tighter (I'm not real comfortable I can pull this off & do a decent job. But you do what you have to:))
Is there a best practice for dealing with this gap? Thanks for your insight.
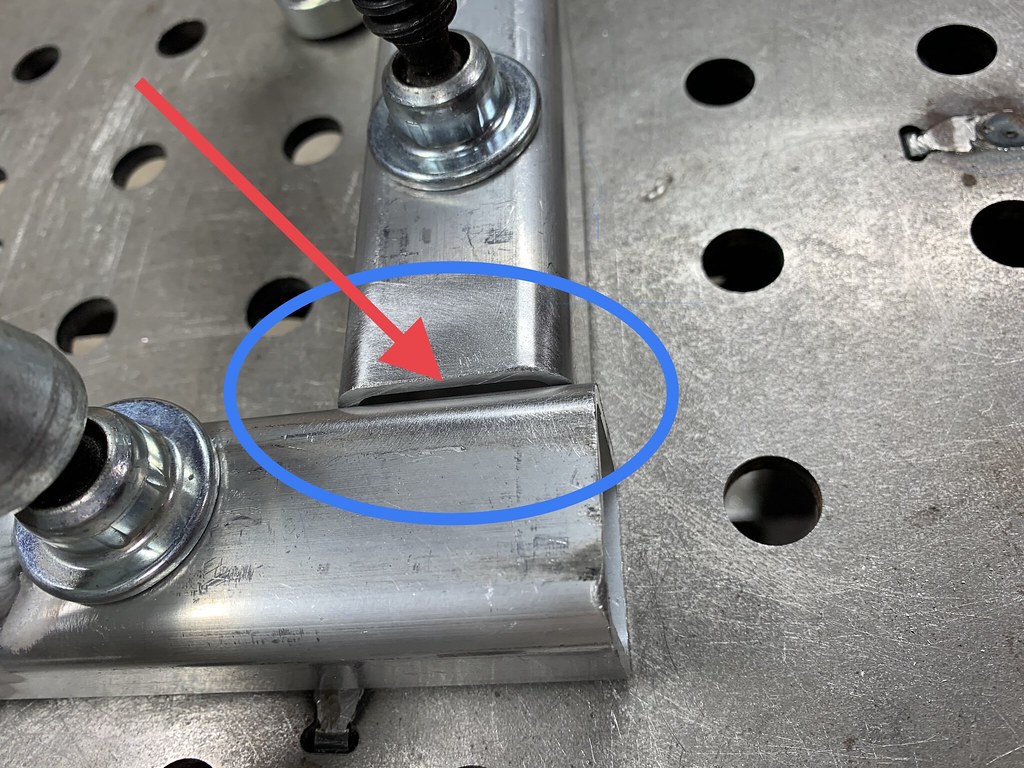
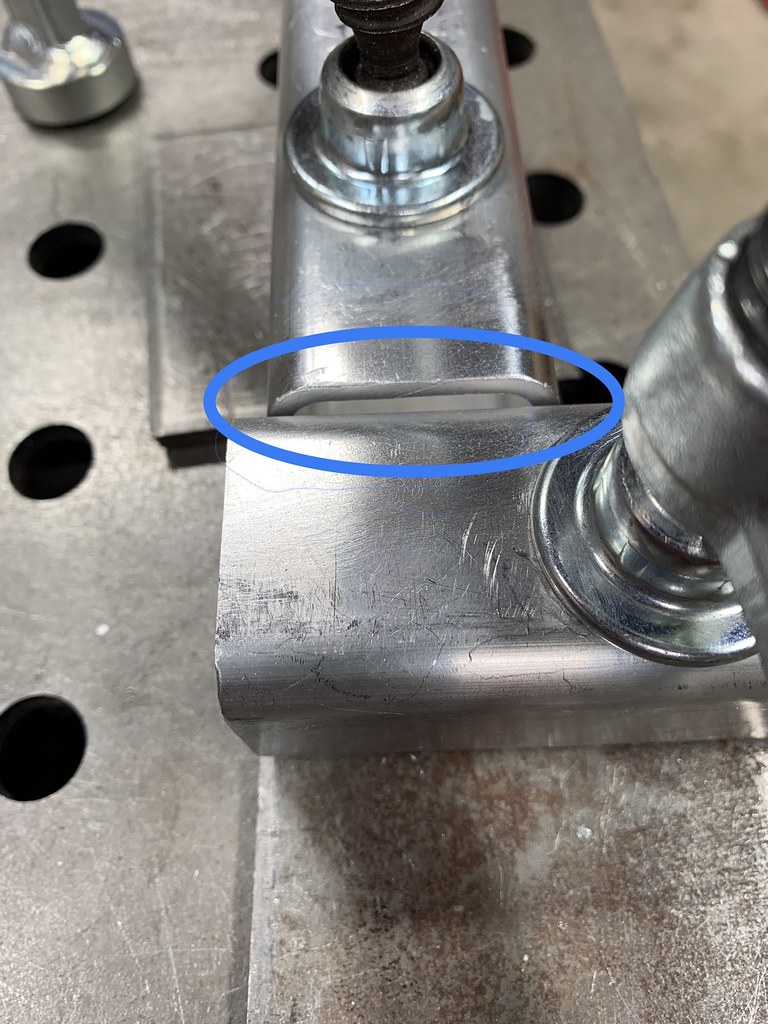