I have this in my shop:
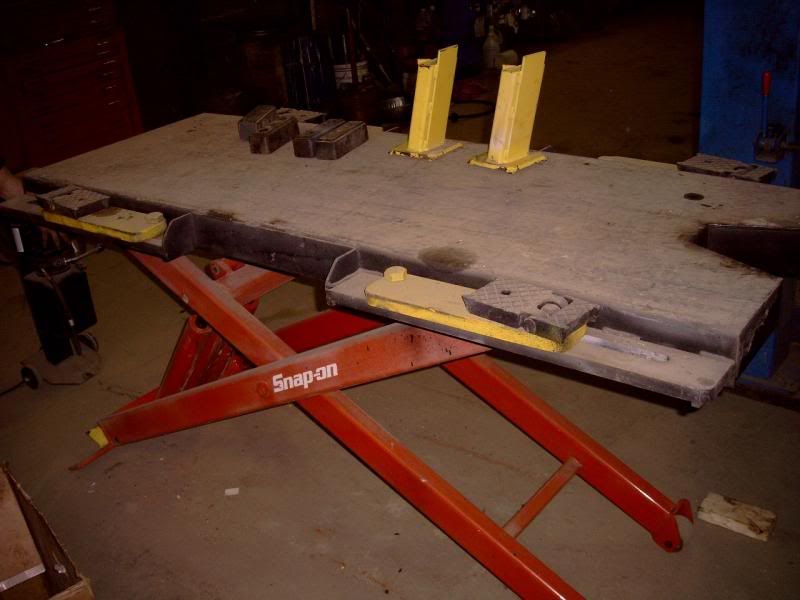
It's a mid-rise lift that goes from 6" to 48" high. Adjustable... I likey. It's about 3'x6'... good size. Bad thoughts, it's hard to clamp anything on and those arms are just going to be in the way. It's mobile and paid for.
Does anyone see any issues with sanding off the powdercoat on the top and grounding through the table? I am not sure if the hydraulics/electric pump will get hurt by doing that. The top is 1/4" thick. I wonder if I should/could cut an X in it for clamping like Miller's table or slots like the Nomad has? I don't see how it could hurt the lifting capacity because it has a sub-structure under it.
And maybe instead of the X or slots, for <$300.00 I could get this and just throw it on top of the lift:
http://www.industrial-toolcrib.com/prod ... MgodenEAFQ
What do you guys think??