I am working on replacing an intercooler's (broken) plastic end tanks with custom fabricated aluminum ones.
Here is about where I am at currently; I am starting with the inlet manifold. I haven't done any welding yet, just measuring and laying out the sheetmetal pieces, taking time so that they'll fit right.
This is for a racing application, with about 25+ psi boost pressure.
I am not totally sure how to weld to the header of this type of intercooler, which was originally designed to be crimped over a plastic flange with a rubber seal in between. The header is a piece of formed aluminum .050" sheet metal. Should I be concerned about not getting heat too close to the tubes? How should I clean it to prepare it for welding?
I am using .065" (16-ga) 5052 for the end tanks. So far, I like working with this material a lot. I mocked it up in cardboard (manilla file folder material) before cutting and forming the pieces out of sheet stock. I haven't done any welding yet (except for a little practice to dial in my setup and technique).
What welding projects are you working on? Are you proud of something you built?
How about posting some pics so other welders can get some ideas?
How about posting some pics so other welders can get some ideas?
Here are some other interesting examples of intercooler end tanks I came across...
This looks like a very smooth flowing design. It looks like sections were cut out of large diameter mandrel bent tubing. (Notice they are formed into rectangular shapes near the intercooler core)
This provides a nice round opening for the tubing.
Here is a "bent "pyramid" like end tank, fabricated with four pieces of sheet metal and some simple bends. (Note this example has an abrupt transition to round tubing, which I hope to avoid in my design)

Another "bent pyramid like" example (Four flat sheet pieces with simple bends):

This looks like a very smooth flowing design. It looks like sections were cut out of large diameter mandrel bent tubing. (Notice they are formed into rectangular shapes near the intercooler core)
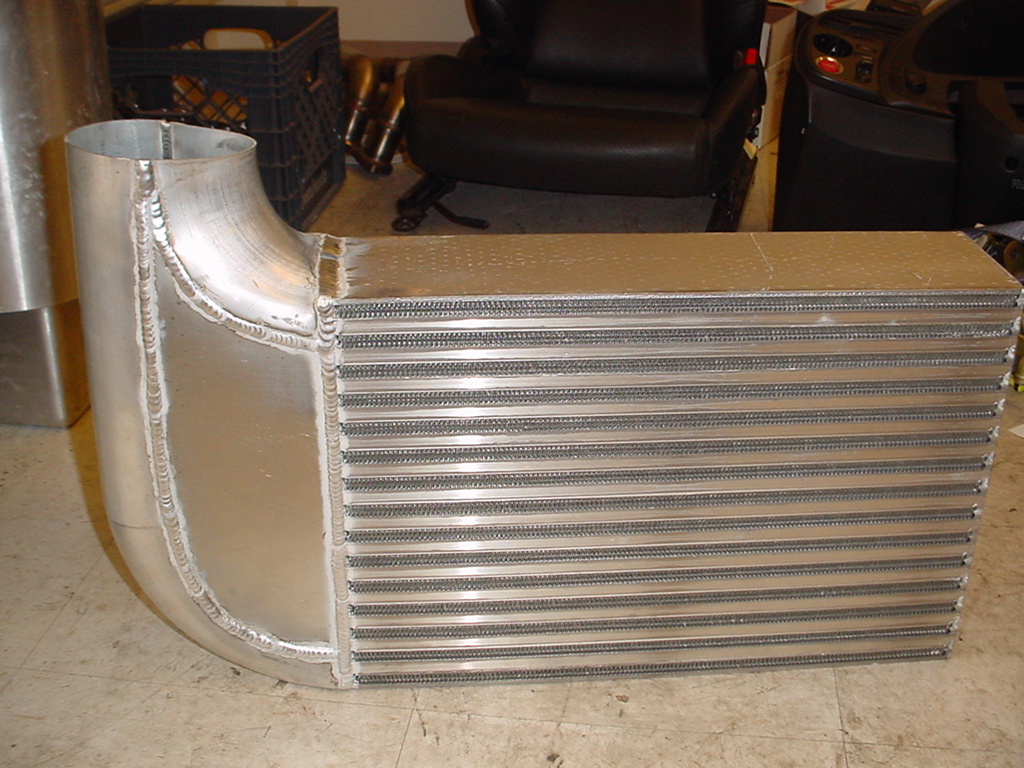
Here is a "bent "pyramid" like end tank, fabricated with four pieces of sheet metal and some simple bends. (Note this example has an abrupt transition to round tubing, which I hope to avoid in my design)

Another "bent pyramid like" example (Four flat sheet pieces with simple bends):

Update - I took a first pass at solvent cleaning the intercooler core. I used gasoline to dissolve and remove the old engine oil out of the insides. It initially turned the gasoline black, while a subsequent gasoline wash stayed mostly clear. I used a nylon bristle brush with the gasoline to scrub the header plates (which I'll weld to) especially clean. The gasoline turned a top layer of black paint on the outside of the 'cooler soft and wrinkley, kind of softening and delaminating it in some places. It peeled off by itself in some places and where I scrubbed it in others. I focused on the sides and back of the header plates, where I'll be welding. There was another layer of black paint/primer in some spots that the gasoline didn't dissolve or soften, but I found that a brass brush wetted in gasoline took that down to bare aluminum, at least in spots where I could reach with the bristles.
The sides and front face (where I'll be welding) of the header plates are all scrubbed down to bare aluminum now. A lot of the back sides of the header plates are scrubbed down to bare metal. The top and bottom of the header plate are inaccessible on the back side, so I'll probably get some smoking when I weld near there. I'll just have to be careful not to melt through right there or there is going to be some nasty contamination I will probably not be able to recover from. I'll probably try cleaning it some more first though.
Edit: probably won't bother posting any more updates unless other folks are interested in hearing them, and say so.
The sides and front face (where I'll be welding) of the header plates are all scrubbed down to bare aluminum now. A lot of the back sides of the header plates are scrubbed down to bare metal. The top and bottom of the header plate are inaccessible on the back side, so I'll probably get some smoking when I weld near there. I'll just have to be careful not to melt through right there or there is going to be some nasty contamination I will probably not be able to recover from. I'll probably try cleaning it some more first though.
Edit: probably won't bother posting any more updates unless other folks are interested in hearing them, and say so.
looks good so far, man. I'dve said something earlier, but I've been busy and just not checking the forums. your dice look good in that other thread, but I would advise welding .050" to .063" a few times before you go ahead and weld these puppies on. .050" is REAL easy to blow holes in, much more so than you'd .013" would make a difference.
also, have you test fit this in the vehicle? you might want to look at how you can optimize your hose layout by putting the inlet/outlet in a better location (and hell, stock might be perfect, but it certainly doesn't hurt to check)
as far as your smooth transition from square "pyramid" to round tubing, I'd calculate the circumference of the tubing size you want to end up at, then divide that by 4 and make the end of your pyramid have sides of that length. then take the sides and form the ends into quarter-circles before you weld it all up. there's a number of ways to do that, wood mallet and a T-dolly would probably be the quickest. then just clean up the circle after its welding together so it's nice and round and weld your tubing to it. you might want to make the end of the pyramid either smaller or larger than the ID or OD(respectively) of the tubing so you can slip the tubing inside or over top of the collar.
good luck! let us know how it turns out. even if no one is posting, we're interested and likely just too busy to check the forums regularly. when things slow down, it's nice to see what everyone else was up to.
also, have you test fit this in the vehicle? you might want to look at how you can optimize your hose layout by putting the inlet/outlet in a better location (and hell, stock might be perfect, but it certainly doesn't hurt to check)
as far as your smooth transition from square "pyramid" to round tubing, I'd calculate the circumference of the tubing size you want to end up at, then divide that by 4 and make the end of your pyramid have sides of that length. then take the sides and form the ends into quarter-circles before you weld it all up. there's a number of ways to do that, wood mallet and a T-dolly would probably be the quickest. then just clean up the circle after its welding together so it's nice and round and weld your tubing to it. you might want to make the end of the pyramid either smaller or larger than the ID or OD(respectively) of the tubing so you can slip the tubing inside or over top of the collar.
good luck! let us know how it turns out. even if no one is posting, we're interested and likely just too busy to check the forums regularly. when things slow down, it's nice to see what everyone else was up to.
Thanks guys. Good to know others are reading this forum who are interested.
ogorir - yes I am test fitting in the vehicle as I go, and I'm making use of the opportunity to redesign the position of the tubing connections. I am even reversing the inlet and outlet to make the routing of the boost tubes a bit more streamlined (shorter.)
Update:
I've got the inlet manifold on the intercooler all done now, including adapting the square shape to round tubing (complete with a beaded edge.) To adapt the round to square, I flared a piece of tubing out (with a tubing expander tool, just not inserted fully, makes it flare the end, and I did calculate a diameter from a desired circimference to determine how much to flare) then I "squished" the flared out portion into a square shape carefully using a vice. It actually worked quite well. The tubing I used was one I found from some mandrel bent piece that seemed very malleable (and quite soft also.) compared to other grades of aluminum I have worked with.
Oh by the way to weld the sheet together, I decided to weld inside and outside as I found that was strongest method with some test coupons. I was originally going to weld outside only with stronger filler rod (5356), but I changed to a weaker 4043 which should hold up better at high temperatures (which this intercooler will definitely be seeing), so I put some focus on making sure the weld joints were strong. Some test coupons I made showed inside+outside welded was significantly stronger than just outside welded only. The downside (besides more work) is it doesn't look quite as pretty from the outside (as where I fully penetrate from the inside, it causes a "sag" in the outside finish), but function is more important than form.
Oh by the way about 2-3 cans of brake parts cleaner (non-chlorinated for safety) worked wonders for stripping *all* the old finish off the intercooler core.
ogorir - yes I am test fitting in the vehicle as I go, and I'm making use of the opportunity to redesign the position of the tubing connections. I am even reversing the inlet and outlet to make the routing of the boost tubes a bit more streamlined (shorter.)
Update:
I've got the inlet manifold on the intercooler all done now, including adapting the square shape to round tubing (complete with a beaded edge.) To adapt the round to square, I flared a piece of tubing out (with a tubing expander tool, just not inserted fully, makes it flare the end, and I did calculate a diameter from a desired circimference to determine how much to flare) then I "squished" the flared out portion into a square shape carefully using a vice. It actually worked quite well. The tubing I used was one I found from some mandrel bent piece that seemed very malleable (and quite soft also.) compared to other grades of aluminum I have worked with.
Oh by the way to weld the sheet together, I decided to weld inside and outside as I found that was strongest method with some test coupons. I was originally going to weld outside only with stronger filler rod (5356), but I changed to a weaker 4043 which should hold up better at high temperatures (which this intercooler will definitely be seeing), so I put some focus on making sure the weld joints were strong. Some test coupons I made showed inside+outside welded was significantly stronger than just outside welded only. The downside (besides more work) is it doesn't look quite as pretty from the outside (as where I fully penetrate from the inside, it causes a "sag" in the outside finish), but function is more important than form.
Oh by the way about 2-3 cans of brake parts cleaner (non-chlorinated for safety) worked wonders for stripping *all* the old finish off the intercooler core.
- Attachments
-
- beaded and welded tube connection
- IMG_0014_small.JPG (44.7 KiB) Viewed 10873 times
-
- preparing header for welding
- IMG_0018_small.JPG (77.7 KiB) Viewed 10873 times
-
- completed inlet manifold
- IMG_0032_small.JPG (84.2 KiB) Viewed 10873 times
Here is the inside of the manifold (showing the inside welds) before I welded it to the core. And also, a picture of the tubing end after forming it into a square transition.
- Attachments
-
- tube ends before and after "bellmouthing" (for less airflow resistance)
- IMG_0022_small.JPG (65.64 KiB) Viewed 10873 times
-
- square transition formed in round tubing
- IMG_0012_small.JPG (32.08 KiB) Viewed 10873 times
-
- inside of manifold
- IMG_0004_small.JPG (62.46 KiB) Viewed 10873 times
that square to round adapter came out really nice.
we use the inside+outside welding technique on almost everything. it really helps if you can weld the inside first, then weld the outside. it's more difficult, but you don't have the sagging issue on the visible side. you can also go back and 'smear' the outside after you've welded the inside. I wouldn't recommend doing that with 4043 filler, though. I've had problems with it cracking, but 1100 rod is awesome for that. it's not super strong tensile-wise compared to 4043 but for sheet metal, the added ductility is way more important. it doesn't create as stiff a 'hinge' where the weld is so vibration doesn't crack the aluminum as easily. it certainly welds a hell of a lot better, though.
we use the inside+outside welding technique on almost everything. it really helps if you can weld the inside first, then weld the outside. it's more difficult, but you don't have the sagging issue on the visible side. you can also go back and 'smear' the outside after you've welded the inside. I wouldn't recommend doing that with 4043 filler, though. I've had problems with it cracking, but 1100 rod is awesome for that. it's not super strong tensile-wise compared to 4043 but for sheet metal, the added ductility is way more important. it doesn't create as stiff a 'hinge' where the weld is so vibration doesn't crack the aluminum as easily. it certainly welds a hell of a lot better, though.
I'd like to experiment with 1100 filler rod sometime. I decided against it for this project though, because I didn't see it in the Alcoa filler rod selection chart for the materials I'm welding, which (IIRC) means that a butt weld with it is weaker than the parent metals. It sure made it seem like Alcoa didn't recommend using it in this application, anyway, but maybe that was my misinterpretation. Anyhow, I am probably over-engineering all this anyway, as I bet that the mostly bent pieces will impart a good deal of strength and rigidity to the structure (there are not many flat surfaces to "oil can" from pressure). Come to think of it, the taped paper mock-up of these manifolds seemed pretty strong & rigid. 
I think I understand what you are saying about the 1100 being very ductile, despite it being low in tensile strength. So, I'm imagining that with it, perhaps you could probably start folding a test coupon welded with the 1100 with less force than other higher strength filler materials, however it would probably allow completely folding over without tearing apart due to its extremely high ductility. I was pretty satisfied being able to completely fold flat a test coupon corner weld made with inside+outside welds with the 4043 filler, however with my outside only test coupon corner welds with 4043, the weld did tear apart before I got it to fold completely flat. And I noticed I was getting as little as about 60-70% penetration in some spots (from looking at the fractured surfaces.)
I am getting down to my last piece formed out of flat sheet on the second manifold, and since the rest of it is already all welded together (including welded to the intercooler core), I'm not going to be able to access the inside corners on these final welds. I guess I will try and do the best I can with the outside only weld. I did take my time and got the piece formed so that the fitup is quite good.

I think I understand what you are saying about the 1100 being very ductile, despite it being low in tensile strength. So, I'm imagining that with it, perhaps you could probably start folding a test coupon welded with the 1100 with less force than other higher strength filler materials, however it would probably allow completely folding over without tearing apart due to its extremely high ductility. I was pretty satisfied being able to completely fold flat a test coupon corner weld made with inside+outside welds with the 4043 filler, however with my outside only test coupon corner welds with 4043, the weld did tear apart before I got it to fold completely flat. And I noticed I was getting as little as about 60-70% penetration in some spots (from looking at the fractured surfaces.)
I am getting down to my last piece formed out of flat sheet on the second manifold, and since the rest of it is already all welded together (including welded to the intercooler core), I'm not going to be able to access the inside corners on these final welds. I guess I will try and do the best I can with the outside only weld. I did take my time and got the piece formed so that the fitup is quite good.
- Attachments
-
- IMG_0051_small.JPG (82.29 KiB) Viewed 10865 times
when you weld up the spots you can't get at the back of, keyhole the front of the puddle a bit before you push rod in. it will get you near complete penetration on the backside (it still looks ugly though). you have to watch it closely, though, so you don't sag the aluminum.
I've never used 1100 on 5052, so I don't know how well it works. I usually use 3003 for most everything and that welds nice with 1100 rod. it welds ok with 4043, but the bead isn't shiny. the 4043 flows a bit better, but tacking is still a pain.
I've never used 1100 on 5052, so I don't know how well it works. I usually use 3003 for most everything and that welds nice with 1100 rod. it welds ok with 4043, but the bead isn't shiny. the 4043 flows a bit better, but tacking is still a pain.
Thanks for the tips, I think I will do just that (practice & attempt the "keyhole" filling method, for more complete penetration). The other idea I had was, experimenting with some heat sink compound I've got (clay / putty like like stuff) - I was thinking I might try forming it into a rope, and "smooshing" that into the backside of the weld joint before welding, to see if it might aid with more complete penetration.
Oh yeah, I also thought about using cut strips of the parent metal for filler rod; I think that would be quite strong and ductile, but I have a feeling it would be overkill.
Oh yeah, I also thought about using cut strips of the parent metal for filler rod; I think that would be quite strong and ductile, but I have a feeling it would be overkill.

- Attachments
-
- IMG_0050_small.JPG (60.53 KiB) Viewed 6157 times
Update: The last piece of sheet metal on this end tank welded on nicely. I'll be ready to weld the round tubing piece on as soon as I get the bead formed for the rubber hose connection.
- Attachments
-
- IMG_0004_small.JPG (80.17 KiB) Viewed 6156 times
I've completed the first end tank now. Got the bead formed on the second round tube, and welded that to the rest of the intercooler.
I have been able to fuse weld (no filler) the back side of many welds that are tricky to access, but possible, with the TIG torch; such as pictured below, through the round opening. I can do this without necessarily having full vision of the puddle; I just do a little bit of metal melting (or attempted melting) at a time, pulling the torch out so I can check my work in between torch blasts. The angle-ground TIG cup is proving handy for allowing me to reach narrow angle surfaces I would otherwise not be able to get adequate inert gas shielding.
I have been able to fuse weld (no filler) the back side of many welds that are tricky to access, but possible, with the TIG torch; such as pictured below, through the round opening. I can do this without necessarily having full vision of the puddle; I just do a little bit of metal melting (or attempted melting) at a time, pulling the torch out so I can check my work in between torch blasts. The angle-ground TIG cup is proving handy for allowing me to reach narrow angle surfaces I would otherwise not be able to get adequate inert gas shielding.
- Attachments
-
- IMG_0001_small.JPG (86.71 KiB) Viewed 6154 times
-
- IMG_0004_small.JPG (79.26 KiB) Viewed 6154 times
-
- IMG_0003_small.JPG (61.5 KiB) Viewed 6154 times
It's a dual pass intercooler, with the inlet and outlet both sharing the same end tank. At the other end tank, the air makes a "U-turn". Here's a photo of what it looked like before I pulled the plastic off. (epoxied on aluminum tubing connection is where the failure occurred.)
- Attachments
-
- IMG_0004_small.JPG (106.18 KiB) Viewed 6152 times
I got the second end tank done! While the design of this one was a simple three pieces of sheet, I challenged myself by trying smoothly rounding over the edges where the sheets mate together. (I made a homemade "T-dolly" for this, by grinding a hemispherical shape into the end of a steel rod and chucking that into a vice.)
I welded this end tank inside&out and also "smeared" the inside weld beads (to make it easier for air to flow), before welding it to the core.
I welded this end tank inside&out and also "smeared" the inside weld beads (to make it easier for air to flow), before welding it to the core.
- Attachments
-
- IMG_0003_small.JPG (67.39 KiB) Viewed 6144 times
-
- IMG_0013_small.JPG (72.6 KiB) Viewed 6144 times
What machine are you using?
Millermatic 251
Spectrum 300 Plasma
Everlast PowerTig 250EX
Everlast PowerCool W300
Harris/Victor OA
Craftsman 13 Speed Drill Press
ProTools Air/Hydraulic Bender
48" Brake
Compressor, Notchers, Grinders, etc.
Spectrum 300 Plasma
Everlast PowerTig 250EX
Everlast PowerCool W300
Harris/Victor OA
Craftsman 13 Speed Drill Press
ProTools Air/Hydraulic Bender
48" Brake
Compressor, Notchers, Grinders, etc.
Thanks ogorir!
I feel like I've definitely gotten better at "TIG sheet aluminum" since I started this project, and I really appreciate your helpful advice on the techniques also.
I welded on the first two of three mounting flanges to the intercooler today. Its looking like a totally perfect fit in the car (as it should, given this level of customization.) I went until my argon tank blew its last breath, with just one more mounting bracket to go. I can almost hear the car running again.

I welded on the first two of three mounting flanges to the intercooler today. Its looking like a totally perfect fit in the car (as it should, given this level of customization.) I went until my argon tank blew its last breath, with just one more mounting bracket to go. I can almost hear the car running again.

The intercooler is all done now. I was really proud of a couple of beads I put down today welding on that last mounting bracket. I made them all in one shot, with no stops. I've finally got my filler rod feeding hand working. 

- Attachments
-
- IMG_0004_small.JPG (59.36 KiB) Viewed 7475 times
-
- IMG_0012_small.JPG (78.38 KiB) Viewed 7475 times
Sure -
First I used a tubing expander tool (see picture below) patially inserted into the tubing, to flare out the end. These can be had for cheap (I recall spending about $8) from harbor freight. They come in three different sizes.
http://www.harborfreight.com/catalogsea ... q=expander
I've learned from experience playing around with this tool that if you don't insert it all the way, it will flare the tubing out into a cone shape, rather than evenly expanding it. So I used that behavior to my advantage as I wanted to flare out the tubing as a first step of making it adapt evenly from round to square.
Before you make the flare, you should plan how much to flare the tubing to (the diameter of the flare) and also how long the taper should be (how long the round to square transition will take.) To calculate the diameter of the flare, I figured the circumference of the flared out end I wanted, by adding up all the edges of the square or rectangle you want to adapt to. So in my case, a square with edges having 2"x2"x2"x2" lengths gave me a target circumference of 8", which implies that it could be formed (without any shrinking or stretching) from a circle having exactly 2.55" diameter (Using the ol' trigonometry formula: Circumference = PIE * Diameter). When you are making the flare, periodically check the flare diameter and stop the flaring operation when you reach it.
After you have made the round flare, I just pinched the square shape into it with a vice. It will help to mark the center of the four faces on the tubing, or the edges (where the faces are going to meet) so you can work it evenly on the vice. You can also reset the expander tool into a cylindrical shape of the minimum dimension and leave that inserted in tubing if you want, to keep the vice from pinching the tubing smaller than that diameter. You can also use pliers to make small adjustments, although I found I was able to accomplish it pretty much all on the vice. And don't try and form the flats all in one vice pinch, but instead make them a little bit at a time and work them in different spots and also doing all four edges about evenly on the vice. Take your time. I managed to get a good result on my first attempt. The malleable grade of aluminum I used for these pieces (I don't know the grade for sure, but if I had to guess I'd say it was 3003) probably helped.
Finally, I made the bead with the tool shown pictured below, which I made out of a pair of vice grips. No need for an expensive bead rolling tool. I just go a little bit at a time around the tubing and progressively make the bead deeper until I am satisfied with it. However for this project I also decided to try adding a weld bead around the inside of the formed bead part, for smoother airflow. I cleaned it up with a cartridge roll on a die grinder afterwards to smooth out the welded bead (you can barely see it.) To idea was to make minimal turbulence for airflow. A nice unexpected beneift of the weld bead inside the rolled bead was that it helped stiffen the open end of the tubing.
First I used a tubing expander tool (see picture below) patially inserted into the tubing, to flare out the end. These can be had for cheap (I recall spending about $8) from harbor freight. They come in three different sizes.
http://www.harborfreight.com/catalogsea ... q=expander
I've learned from experience playing around with this tool that if you don't insert it all the way, it will flare the tubing out into a cone shape, rather than evenly expanding it. So I used that behavior to my advantage as I wanted to flare out the tubing as a first step of making it adapt evenly from round to square.
Before you make the flare, you should plan how much to flare the tubing to (the diameter of the flare) and also how long the taper should be (how long the round to square transition will take.) To calculate the diameter of the flare, I figured the circumference of the flared out end I wanted, by adding up all the edges of the square or rectangle you want to adapt to. So in my case, a square with edges having 2"x2"x2"x2" lengths gave me a target circumference of 8", which implies that it could be formed (without any shrinking or stretching) from a circle having exactly 2.55" diameter (Using the ol' trigonometry formula: Circumference = PIE * Diameter). When you are making the flare, periodically check the flare diameter and stop the flaring operation when you reach it.
After you have made the round flare, I just pinched the square shape into it with a vice. It will help to mark the center of the four faces on the tubing, or the edges (where the faces are going to meet) so you can work it evenly on the vice. You can also reset the expander tool into a cylindrical shape of the minimum dimension and leave that inserted in tubing if you want, to keep the vice from pinching the tubing smaller than that diameter. You can also use pliers to make small adjustments, although I found I was able to accomplish it pretty much all on the vice. And don't try and form the flats all in one vice pinch, but instead make them a little bit at a time and work them in different spots and also doing all four edges about evenly on the vice. Take your time. I managed to get a good result on my first attempt. The malleable grade of aluminum I used for these pieces (I don't know the grade for sure, but if I had to guess I'd say it was 3003) probably helped.
Finally, I made the bead with the tool shown pictured below, which I made out of a pair of vice grips. No need for an expensive bead rolling tool. I just go a little bit at a time around the tubing and progressively make the bead deeper until I am satisfied with it. However for this project I also decided to try adding a weld bead around the inside of the formed bead part, for smoother airflow. I cleaned it up with a cartridge roll on a die grinder afterwards to smooth out the welded bead (you can barely see it.) To idea was to make minimal turbulence for airflow. A nice unexpected beneift of the weld bead inside the rolled bead was that it helped stiffen the open end of the tubing.
- Attachments
-
- IMG_0012_small.JPG (32.08 KiB) Viewed 7463 times
-
- IMG_0001_small.JPG (42.13 KiB) Viewed 7463 times
-
- IMG_0001_2_small.JPG (87.04 KiB) Viewed 7463 times
Last edited by jakeru on Mon Aug 02, 2010 9:25 pm, edited 2 times in total.
Return to “Welding Projects - Welding project Ideas - Welding project plans”
Jump to
- Introductions & How to Use the Forum
- ↳ Welcome!
- ↳ Member Introductions
- ↳ How to Use the Forum
- ↳ Moderator Applications
- Welding Discussion
- ↳ Metal Cutting
- ↳ Tig Welding - Tig Welding Aluminum - Tig Welding Techniques - Aluminum Tig Welding
- ↳ Mig and Flux Core - gas metal arc welding & flux cored arc welding
- ↳ Stick Welding/Arc Welding - Shielded Metal Arc Welding
- ↳ Welding Forum General Shop Talk
- ↳ Welding Certification - Stick/Arc Welding, Tig Welding, Mig Welding Certification tests - Welding Tests of all kinds
- ↳ Welding Projects - Welding project Ideas - Welding project plans
- ↳ Product Reviews
- ↳ Fuel Gas Heating
- Welding Tips & Tricks
- ↳ Video Discussion
- ↳ Wish List
- Announcements & Feedback
- ↳ Forum News
- ↳ Suggestions, Feedback and Support
- Welding Marketplace
- ↳ Welding Jobs - Industrial Welding Jobs - Pipe Welding Jobs - Tig Welding Jobs
- ↳ Classifieds - Buy, Sell, Trade Used Welding Equipment
- Welding Resources
- ↳ Tradeshows, Seminars and Events
- ↳ The Welding Library
- ↳ Education Opportunities