It's not just forward travel. It's forward, and then back a half puddle keeping the weld large enough and pushed up without any sag in the puddle, or unequal legs or concavity. It's like forward and an up roll back, without being a weave. It also helps control the heat when running full bore with only a momentary switch. Torch is nearly straight up. This way you can fly, without leaving runny looking welds or divots. Ripples roughly 3/32" apart. The nearly straight up torch will give the ripples some definition without rough edges, with the heat, keeping them from being too "dime-ish."
They cut the parts. Flat stock was cut in a shear by eye it seemed. Welds wrap around to a bead or three behind the crotches of the gussets. Typically, they would just have likely a MIG, piss stitch of sorts on the edges only. There was no written instructions so, full weld they get.
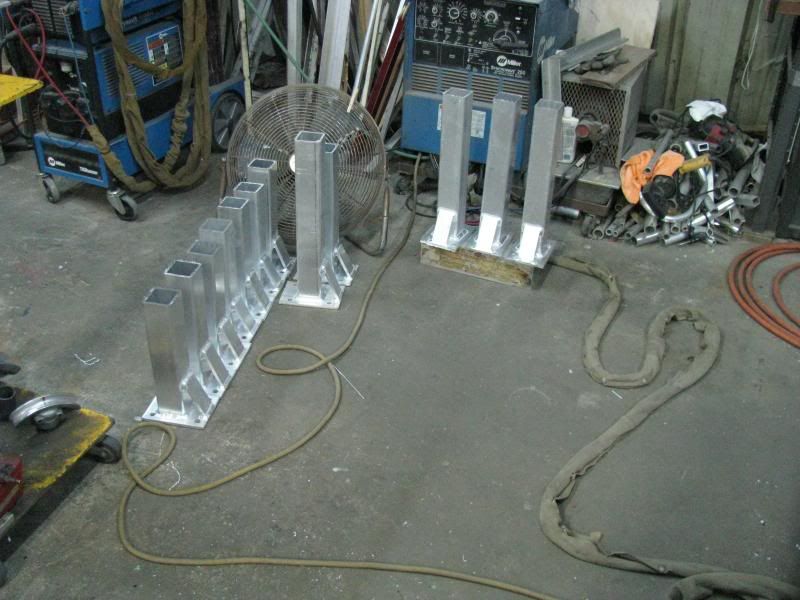
Even after stopping to turn the camera on for this photo with post flow at 15-20.
That's money.

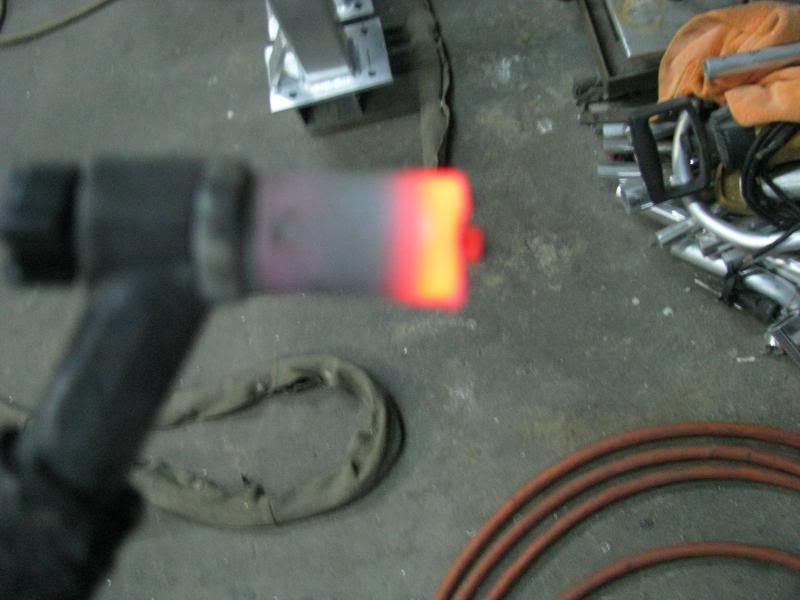
Not that big a deal as far as level of difficulty, but I was pumped. It feels great to weld like this and then look behind you at the end of the day and see a bunch of finished work allover the place. During the piecework days, you just knew you made way more than you thought. Then do it again the next day. Would take until Sunday afternoon to de-amp your own self if you weren't by chance, working it. It's an adrenaline thing, driven almost entirely by the kids, mrtg payment and the electric bill.

Crusty little critter. Amazing that something in that shape can make all those welds as nicely as it does. Not one "poof" on the entire set. I should probably treat myself to a new cup and collet body. Had this one on there about 4 months. If I had at least dusted the plates and such off or knocked the burr off the square stock, this would probably only be half as dirty.
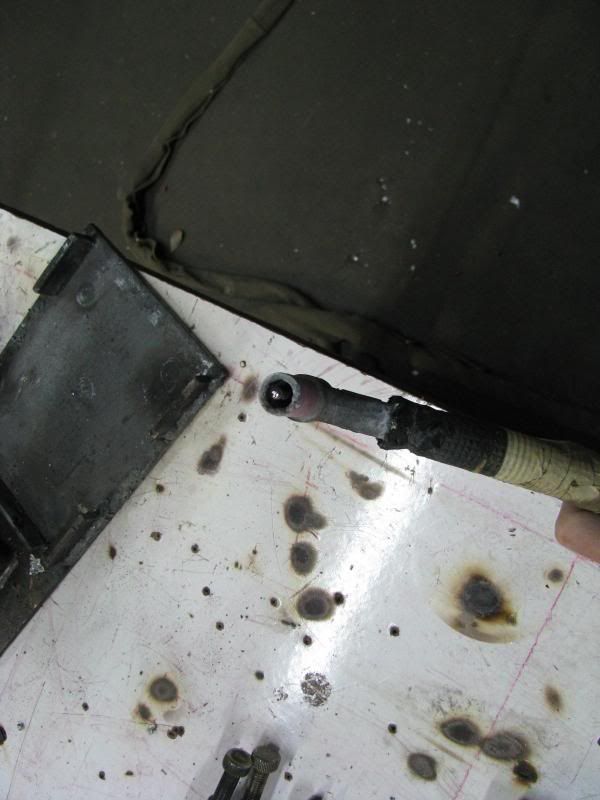
May get upwards of 200 of these to do in a year.