After drilling the top plates and beam, I was able to weld the plates and braces to the main posts.
Alignment of these components was crucial!
I wanted to add a little color to my shop, this being a fairly large machine, I choose blue to match my welders and other pieces of equipment. Rattle can spray paint did the trick!
All the parts finished and ready for final assembly!
With a friends help and a forklift (Yes it's good to have both!) we were able to put it all together. It's just the right size to move around the shop and do all the heavy lifting in the future.
I made a little collector box for the lift chain on my hoist to clean everything up a little.
The tacked together box was made a little long to figure out how much space would be needed for the chain with the hook all the way up. It's easy to cut it back as needed.
Here it is mounted to the hoist housing.
Cut to finished length and painted.
First lift test was my welding table, approx 1,500 lb total. Lifted it with ease and moved it a little more into the shop space.
Parked in the corner ready for the next lift.
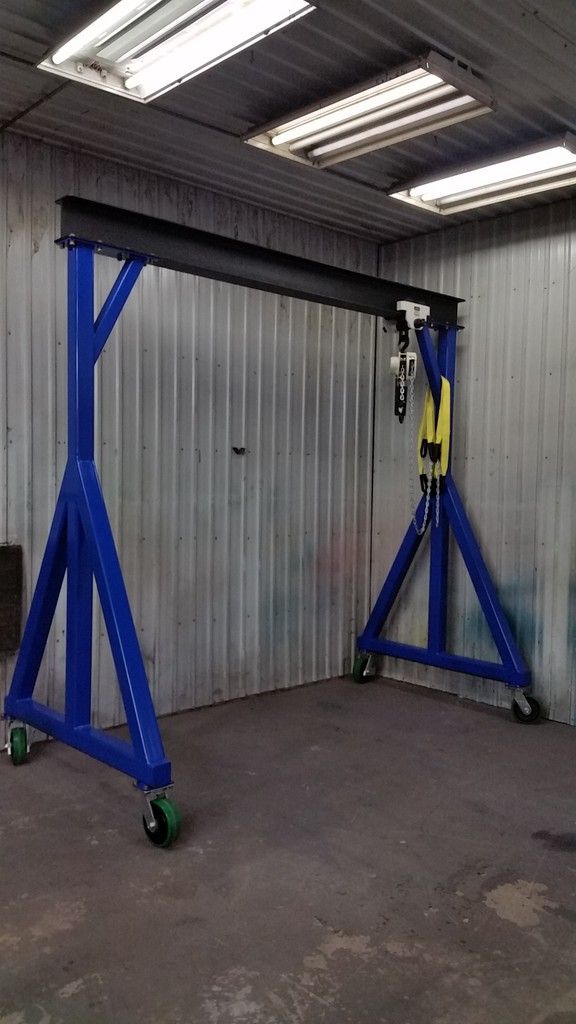